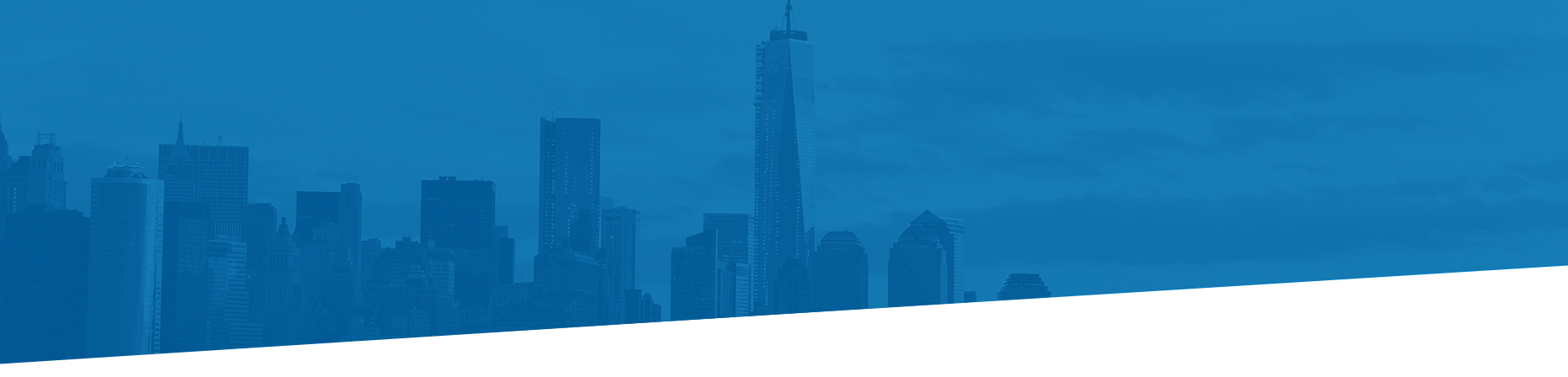
СПЕЦТЕХНОЛОГІЯ ГР. 37
Тема: Антикорозійний захист кузовів
Тема уроку. Матеріали для консервації транспортних засобів
Учбові питання
1.Види матеріалів для консервації ТЗ
2. Характеристика матеріалів для консервації
1.Для зовнішньої консервації елементів ТЗ використовують такі захисні матеріали:
а) пластичні мастила
б)мастики та пасти
в)консерваційні оливи
г)змивні інгібовані покриття
д)плівкоутворювальні інгібовані нафтові суміші
ж) плівкові полімерні й воскові покриття
2. Найчастіше використовують вуглеводні мастила , які мають низьку температуру плавлення ( до 70 градусів). Пластичні мастила наносять на поверхню шаром до 5 мм, що забезпечує високу водостійкість і консерваційні властивості . Для тимчасової консервації ТЗ і їх вузлів застосовують солідол, технічний вазелін, літол.
Для антикорозійного захисту металевих частин ТЗ використовують мастики і пасти на основі бітуму. Для захисту від корозії внутрішніх металевих частин застосовують рідкі консерваційні оливи. Для захисту лакофарбових покрить застосовують напіврідке мастило. Змивні інгібовані покриття легко наносяться будь - яким способом, мають високі захисні властивості, здатні проникати в мікротріщини.
Для додаткового захисту від корозії шасі і днищ ТЗ застосовують плівкоутворювальні нафтові суміші, які здатні утворювати на металі тверді або напівтверді плівки товщиною 0,6 мм. Для консервації прихованих і важкодоступних поверхонь ТЗ ( пороги, лонжерони, стояки, двері) застосовують спеціальні плівкоутворювальні інгібовані нафтові суміші, які мають високу проникну здатність. Для захисту металевих виробів від корозії можуть застосовуватися покриття на основі воску, які легко видаляються з допомогою пари або мякої ганчірки змоченої розчинником.
Тема: Нанесення захисних матеріалів
Учбові питання:
1. Операції технологічного процесу
2.Основні способи нанесення захисних матеріалів
1.Процес антикорозійної обробки складається з таких технологічних операцій:
а)підготовка автомобіля до антикорозійної обробки( 1. промити місця нанесення захисного матеріалу 2. зняти гумові заглушки 3. підняти ТЗ на підйомник 4. очистити дефектні ділянки днища від корозії 5.висушити воду 5. зняти колеса 6. закрити гальмові механізми і місця, які не обробляються цупким папером або плівкою)
б) нанесення захисного матеріалу
в) зняття технологічних кожухів і паперу
г) встановлення раніше знятих деталей та гумових заглушок
д) очищення лакофарбового покриття від забруднень
2.Способи нанесення захисних матеріалів : ручний з допомогою пензля і шляхом розпилення. На СТО можуть використовуватися установки безповітряного розпилення, які дають змогу розпилювати захисний матеріал під тиском 7,2 - 18 МПа. В приховані порожнини захисний матеріал наносять за допомогою змінних насадок різних конфігурацій та довжини. Для доступу до всіх прихованих порожнин додатково просвердлюють отвори діаметром до 8 мм. В умовах індивідуальних гаражів захисну суміш наносять пневморозпиленням з використанням пульверизатора і компресора. Суміш до потрібної концентрації розводять з допомогою розчинника.
Тема: Матеріали необхідні для фарбування автомобіля
Ви зібралися перетворити вашого «залізного друга»? Тоді вам необхідно гарненько підготуватися. У цій статті від avtoservis.lutsk.ua, ви дізнаєтеся які матеріали для фарбування автомобіля вам будуть потрібні. Адже тільки фарбою і лаком не обійтися, тим більше що фарбування та полірування кузова - це вже заключний етап. А йому передує ще велика і серйозна підготовча робота. Від якості проведення підготовки залежить успіх всього процесу.
Змивка фарби
Якщо ви вирішили кардинально поміняти колір автомобіля або стара фарба має сильні пошкодження, відшаровується від металу або спучується, то найкращим рішенням буде позбутися від шару старої фарби. При цьому потрібно не пошкодити метал кузова.
Сучасні технології дозволили винайти дуже ефективний і швидкодіючий спосіб видаляти фарби і лаки з поверхні металу. Такий ефект дає змивка для автомобільної фарби. Наприклад, такі змивки як ABRO або BODY відмінно розм'якшують і відшаровують старі лакофарбові покриття практично з будь-яких поверхонь, за винятком пластмас.
Шпаклівка
Якщо фарбування автомобіля носить відновлювальний характер після будь-яких пошкоджень або ДТП, то часто вдаються до рихтування кузова. Ця процедура досить груба і з її допомогою не завжди вдається отримати ідеально рівну поверхню. Тому всі нерівності і шорсткості що залишилися, вирівнюються нанесенням шпаклівки.
Їх поділяють на два основних види: однокомпонентні і двокомпонентні. Останніми, що містять саму шпаклювальну суміш і затверджувач, вирівнюють глибокі вм'ятини. Добре перемішуючи шпаклівку з затверджувачем перед застосуванням, ви отримуєте густий і в'язкий продукт, який можна наносити товстим шаром.
Фінішні шпаклівки більш рідкі і наносити їх потрібно тонким шаром, тому що вони дають велику ступінь усадки. Залежно від основи, на якій виготовлена шпаклівка, їх ділять на такі види:
- акрилові - ці шпаклівки виробляють на водній основі. Вони ідеальні для обробки великих поверхонь (акрилова рідка шпаклівка) з використанням розпилювача. Акрилова однокомпонентна шпаклівка добре вирівнює дрібні недоліки після грунтовки. Після неї можна відразу наносити емаль або фарбу-металік;
- нітроцелюлозні - шпаклівки, які усувають дефекти на кузовах, покритих нітроемалями і синтетичними емалями. Наносяться тонким шаром і висихають протягом години;
- поліефірні - дрібнозернисті, двокомпонентні шпаклівки на основі поліефірних смол, які добре заповнюють пори і дуже швидко сохнуть (20-30 хвилин). Наприклад, шпаклівка з алюмінієм добре підходить для деталей, що піддаються сильній вібрації (капот), шпаклівки BODY;
- для глибоких вм'ятин і поверхонь, пошкоджених корозією, добре підходить шпаклівка зі скловолокном. Це ідеальний, дуже еластичне засіб здатний закласти найглибші нерівності завдяки армуючим властивостям його скловолоконних ниток;
- шпаклівка для роботи з пластиком - нею можна відреставрувати бампера, а також різні елементи в салоні автомобіля. Вона досить м'яка й еластична. Також має відмінну адгезію з пластиковими виробами.
Грунт автомобільний
Що ще потрібно для фарбування авто? Це, безумовно, грунтовки. Вони потрібні для того, щоб підсилити зчеплення лакофарбових матеріалів з металом, захистити кузов від корозії, а також приховати дефекти шпаклівки:
Епоксидні грунти. Відмінно захищають метал кузова від корозії і усувають незначні нерівності шпаклівки.
Грунти адгезійні для пластику міцно зчіплюють емалі і пластик. Ними можна користуватися для фарбування будь-яких деталей авто з пластика.
Акриловими грунтовками виконують остаточне вирівнювання поверхні перед фарбуванням. Акриловий грунт виготовляється на водній основі, тому він універсальний стосовно до всіх видів фарб.
Шліфувальний папір
Матеріали для фарбування автомобіля передбачають наявність великої кількості шліфувального паперу різної зернистості. Папір використовують для зачистки поверхні від дрібних нерівностей після шпаклювання та грунтування.
Так, рухаючись по технологічному ланцюжку, ми підійшли до основного процесу - покриттю поверхні кузова лакофарбовими матеріалами.
Види автомобільних фарб
Переймаючись питанням, що потрібно для фарбування авто, ми в першу чергу маємо на увазі фарбу і лаки.
Всю фарбу, призначену для автомобілів, можна розділити на три основні групи:
акрилові фарби. Їх виготовляють на водній основі. Вони дають глибокий, яскравий колір, легко наносяться і швидко сохнуть. Стійкі до впливу зовнішніх факторів. Завдяки цим чудовим якостям, акрилові фарби стали найпопулярнішими серед автолюбителів і професіоналів.
фарба-металік наноситься в два шари: спочатку синтетична нітроемаль обраного відтінку з ефектом металу, потім наносять другий захисний шар акрилового лаку.
фарба спеціального призначення - призначена для тюнінгу автомобіля або виконання аерографії (малюнків на поверхні кузова).
Обрана фарба може виявитися досить густою і, як правило, потребує розведення. Тому у вашому арсеналі повинен бути присутнім розчинник для автомобільної фарби. Він повинен відповідати типу фарби, яку ви обрали.
Полірувальні пасти
Щоб надати зовнішній блиск новому лакофарбовому покриттю, використовують полірувальні пасти. Вони стануть швидким помічником при усуненні недоліків фарбування, а також випадкових дрібних подряпин.
За допомогою полірування такою пастою можна домогтися різного ефекту. Це може бути привабливий дзеркальний блиск, який виходить при застосуванні рідкої дрібноабразивної пасти. Або ж навпаки - матової поверхні, яка виходить за допомогою грубої полірувальної пасти. Також для дрібного ремонту, полірування та захисту металу й пластику застосовують неабразивні полірувальні пасти.
Тема: Підготовка автомобіля до фарбування
Мийка та огляд кузова
Підготовка до фарбування автомобіля починається з попереднього ретельного огляду кузова. Добре вимийте машину і досконально огляньте її. Особливу увагу приділіть так званим зонам ризику: днище, крила, пороги, стійки, місця стиків деталей. Якщо виявите гнилі місця, то тут не обійтися без радикальних заходів. Проблемні місця краще вирізати болгаркою і накласти латки, застосувавши зварювальний апарат. Виявивши бульбашки іржі, натисніть на них твердим предметом. Швидше за все, в цих місцях іржа йде зсередини і доведеться теж скористатися зварюванням.
Зачистка кузова автомобіля
Після обстеження з автомобіля потрібно зняти всі деталі, які не повинні потрапити під струмінь фарби: скло, фари, ручки, тюнінг, бампера. Дещо можна заклеїти газетами і малярним скотчем. Якщо при огляді було виявлено глибокі вм'ятини й тріщини, то доведеться ці місця рихтувати (читайте тут). Для цієї роботи потрібен певний досвід. За його відсутності краще звернутися до нас. Для рихтовки застосовують різні витяжні пристосування, рихтувальні молотки і опори.
Після зварювальних робіт і рихтування можна приступати до зачистки. Її мета - згладити зварні шви, відколи, тріщини і прибрати верхній блискучий шар старої фарби. Для цього можна скористатися спеціальним рубанком або шліфувальною машинкою і наждачним папером. У місцях, де є бульбашки іржі, знімаємо, не шкодуючи, все до металу. Можна використовувати перетворювач іржі. Якщо стара шпаклівка і фарба тримаються міцно, то не слід дуже старатися. Ці місця просто «затуманьте», знявши шкіркою верхній шар. Після цього поверхню потрібно знежирити бензином.
Великі поверхні потрісканої фарби можна протруїти 30% розчином каустичної соди і залишити на ніч. Вранці фарба легко зніметься струменем гарячої води. Каустик наносити пензлем щоб уникнути травмування рук - це агресивна рідина.
Зварні шви можна шліфувати болгаркою. Вм'ятини, тріщини і подряпини обробляють вручну шкіркою Р60-Р120, остаточне шліфування виконують більш дрібною наждачкою Р220-Р260.Шпаклівка кузова
Підготовка авто під фарбування передбачає ще один етап. Для усунення всіх нерівностей поверхню потрібно зашпаклювати. Шпаклівки автомобільні бувають різні, і тому способи нанесення теж відрізняються. Кожен виробник дає свої рекомендації, яких і потрібно дотримуватися. Але є основне правило: не накладайте шпаклівку товстим шаром - вона обов'язково потріскається. Але якщо все ж така необхідність з'явиться, то шпаклювання потрібно робити шарами, ретельно просушуючи кожен з них. Для великих вм'ятин і тріщин краще застосовувати крупнозернисту шпаклівку зі скловолокном або нітрошпаклівку. Для деталей з пластику застосовують спеціальну шпаклівку, призначену для пластиків.
Шпаклювання капота
Наносити шпаклівку найкраще прямокутним шматком листової гуми. Після висихання її теж потрібно зашкурити, щоб поверхня була гладкою. Шпаклівку зі скловолокном, яку ви наклали товстим шаром, потрібно залишити на добу для кращого висихання. Інакше вона може просісти і доведеться виправляти ситуацію. Незначні дефекти можна зашпаклювати двохкомпонентною шпаклівкою, яка є універсальною. Для мікротріщин підійде однокомпонентна акрилова шпаклівка, яку наносять зазвичай після грунтовки. Всю роботу виконують водостійким наждаковим папером з рясним додаванням води.
Грунтовка
Ми розглянули самі основні і важливі моменти, і тепер знаємо, як підготувати авто до фарбування. Але є ще один крок, який деякі автолюбителі пропускають.
Це грунтування кузова. Для того щоб фарба трималася довго і міцно, краще цією процедурою не нехтувати. Для неї потрібен компресор з робочим тиском 3 атмосфери, краскопульт для фарбування і безпосередньо грунт. На сьогоднішній день самий популярний - акриловий. Він чудово захищає метал від корозії. Починати потрібно з тих місць, які шпаклювали, і наносити в декілька шарів. Після грунтовки потрібно знову зачистити поверхню шкіркою.
Після закінчення грунтування необхідно нанести «проявляючий» шар - розбавлену розчинником емаль. Вона покаже ваші недоробки, до яких доведеться повернутися і знову зашпатлювати проблемні місця. Потім ретельно відшліфувати і довести кузов до ідеальної гладкості .
На цьому підготовку до фарбування можна вважати завершеною.
Тема: Фарбування кузовів
Кількість шарів фарби, яку наносять на поверхню грунтованого і шпакльованого виробу визначається властивостями лакофарбового матеріалу (в'язкість, покривність), способом його нанесення та експлуатаційними вимогами до цього виду покриття. Кожний наступний шар, як правило, наноситься на добре висушений попередній шар. Хоча в деяких випадках використовується принцип мокрий по мокрому".
Фарбування пневматичним розпилюванням полягає в розпилюванні лакофарбового матеріалу стиснутим повітрям і нанесенні його у вигляді дисперсії на поверхню виробу. Позитивними якостями методу є висока продуктивність, можливість фарбування виробів різної конфігурації і габаритів, використання всіх видів лакофарбових матеріалів і отримання покрить високого класу. До недоліків цього методу належать великі втрати лакофарбового матеріалу (15-55%), значні витрати розчинників, вогненебезпечність і погані санітарно-гігієнічні умови праці. Лакофарбові матеріали можна наносити в холодному стані або нагріванням. В останньому випадку знижується в'язкість матеріалів, зменшуються витрати розчинників на 30 - 40 %, кількість покривних шарів фарби, втрати матеріалів і покращується декоративний вигляд виробів.
Фарбування безповітряним розпилюванням здійснюється під високим тиском з нагріванням або без нагрівання. При фарбуванні з нагріванням лакофарбові матеріали при температурі 40- 100 °С подаються до сопла розпилювача під тиском 4-6 МПа, а при фарбуванні без нагрівання при температурі 18-25 °С під тиском 10-25 МПа. Розпилювання матеріалу досягається за рахунок перепаду тиску при виході з сопла розпилювача і миттєвого випаровування розчинників
Переваги цього методу фарбування порівняно з попереднім полягають у тому, що зменшуються втрати лакофарбових матеріалів і розчинників, отримуються щільні покриття. Недоліками с те, що важко фарбувати вироби складної форми, значна вартість обладнання, погіршення зовнішнього вигляду виробів.
При фарбуванні в електричному полі високої напруги диспергований лакофарбовий матеріал набуває від'ємного потенціалу, під дією електричного поля переміщується до позитивно зарядженого виробу і осаджується на його поверхню. Якість покриття залежить від параметрів електричного поля, електричних властивостей лакофарбового матеріалу і методу його розпилювання. Перевагами цього методу фарбування є те, що значно знижуються витрати матеріалу, поліпшуються умови праці, є можливість отримання покрить високого класу.
При фарбуванні методом занурювання виріб після занурення в фарбу потрібно встановити над ванною для стікання надмірної кількості фарби. Метод використовується для фарбування виробів простої конфігурації.
Фарбування методом струменевого поливання реалізується в спеціальній установці. Після поливання виріб витримується в парах розчинника. Такий метод використовується для фарбування виробів складної конфігурації. Метод забезпечує високу якість покриття, дозволяє механізувати фарбування.
Фарбування методом електроосаджування здійснюється в водяному середовищі при протіканні постійного струму. Метод дає можливість отримати щільні покриття рівномірної товщини, забезпечує одержання покрить високого класу, піддається повній механізації, пожежо- і вибухобезпечний, значно покращуються санітарно-гігієнічні умови праці. Недоліками методу є великі капітальні вкладення, велика витрата води, можливість отримання покрить тільки на струмопровідних матеріалах.
Тема: Сушіння лакофарбових покритть кузовів
Для сушіння лакофарбових матеріалів при ремонті кузова автомобілів використовують два основних способи - конвективний (теплової НА - Hot Air) і терморадіационной (інфрачервоний IR - Infra Red). Конвективная сушка проводиться в спеціальній камері, де теплоносієм є гаряче повітря - він нагріває весь виріб, включаючи деталі, які не потрібно сушити. До цього способу в основному вдаються при повного фарбування кузова або ремонті його великих ділянок.
Головний недолік конвективного способу сушки полягає в тому, що нагрів лакофарбового покриття (ЛКП) починається з його зовнішнього шару. При цьому залишився у внутрішніх шарах фарби розчинник, випаровуючись під дією температури, «пробивається» назовні через вже підсохлий верхній шар покриття. В результаті утворюються мікропори, що негативно позначається на властивостях ЛКП - знижуються його міцність і герметичність, а отже, погіршується антикорозійний захист металу. Вирішують цю проблему застосуванням фінішного лаку.
Вищезазначені недоліки не виявляються при сушінні за допомогою інфрачервоних ламп. За принципом дії такі установки частково схожі з мікрохвильовою піччю, тільки в даному випадку виріб нагрівається не СВЧ, а інфрачервоним випромінюванням. Залежно від довжини хвилі промені можуть вільно проникати крізь всі шари лакофарбового матеріалу до поверхні виробу (металу, пластмаси) або відбиватися від кордону розділу шарів ЛКП (наприклад, між шарами фарби і шпаклівки). У першому випадку спочатку нагрівається метал, а від нього - сам лакофарбовий матеріал. Розчинник і летючі речовини при цьому переходять з внутрішнього висихає шару будь-якого матеріалу в ще в'язкий (рідкий) зовнішній, а потім в атмосферу. У другому - відбувається нагрів тільки зовнішнього (свіжонанесенного) шару. При використанні IR-випромінювання ремонтуються деталі кузова нагріваються до необхідної температури вже через кілька хвилин після включення нагрівачів. Обумовлено це тим, що енергія випромінювання практично повністю передається на поверхню виробу і ЛКП, які не витрачаючись на нагрів проміжного теплоносія - повітря, який знаходиться в зазорі між лампою і поверхнею. Інфрачервоні сушки дозволяють нагрівати пофарбовану поверхню до 240 ° С, але на практиці використовується нагрів від 60 - 80 до 120-140 ° С. Це дає можливість при ремонті використовувати практично всю гаму випускаються лакофарбових матеріалів, грунтів і шпаклівок, а також створювати умови для полімеризації порошкових матеріалів.
Залежно від використовуваної довжини хвилі все IR-сушки діляться на два класи - середньохвильові (СВ) і короткохвильові (КВ). Вони відрізняються за глибиною проникнення інфрачервоних променів в шар лакофарбового матеріалу і температурою його нагрівання. При використанні СВ-сушок час повного затвердіння покриття становить від 12 до 30 хвилин.
Застосування КВ-сушок, промені яких глибше проникають в висушуваний шар, сприяє кращій полімеризації лакофарбових матеріалів і скорочує час їх затвердіння вдвічі (до 5-13 хв). Відразу після охолодження висушений за допомогою IR-нагрівачів шар ЛКП можна шліфувати і (або) полірувати.
Інфрачервоні сушки класифікуються і за іншими ознаками. Наприклад, за габаритами і способу установки: вони можуть бути портативними (ручними), переносними, вбудованими в стаціонарні пости (рейкові), а також встановлюються на колісні або на спеціальні штативи. Така різноманітність способів розміщення дає можливість проводити частковий ремонт або підфарбовування кузова на місці, не переміщаючи машину і не займаючи малярську камеру.
IR-установки обладнані електронним блоком управління, що дозволяє задавати режим сушки для самих різних матеріалів: шпаклівки (грубої і тонкої), грунту-вирівнювача, акрилової і алкідної емалей, а також лаку. Можливе застосування східчастих режимів сушки, при яких забезпечується оптимальний процес висихання (наприклад, на останніх етапах потужність випромінювання зменшується автоматично).
Час сушіння лакофарбових матеріалів (шпаклівки, фарби, лаку) при IR-нагріванні як правило, не перевищує 30 хвилин. Слід зазначити, що періоди, необхідні для затвердіння однотипних лакофарбових матеріалів різних виробників різні. Тому точні параметри режиму сушіння визначаються в кожному конкретному випадку, згідно з даними, наведеними в інструкціях до IR-обладнання.
Інфрачервона лампа вмонтована в корпус (софіт, випромінювач) і забезпечена рефлектором. У деяких моделях для кращого відображення хвиль внутрішню поверхню рефлектора роблять позолоченою. IR-сушіння комплектуються декількома (зазвичай - від одного до чотирьох) блок-випромінювачами, що збільшує максимальну площу нагріву. Це дозволяє виробляти сушку виробів різних розмірів - від кришки люка бензобака до даху машини.
Ультрафіолетові технології сушіння лакофарбових матеріалів
З 1999 р для ремонту ЛКП автомобіля були розроблені і стали застосовуватися лакофарбові матеріали ультрафіолетового (UV - UltraViolet) затвердіння. В першу чергу вони були призначені для так званого точкового ремонту ЛКП кузова при незначних його пошкодженнях - наприклад, подряпинах, відколах малих розмірів, а також для економії часу, що витрачається на сушку і обробку використовуваних матеріалів.
UV-шпаклівки, грунти і лаки при опроміненні ультрафіолетовим світлом тверднуть за 2 - 5 хвилин. Слід зазначити, що при даній технології використовуються звичайні двокомпонентні акрилові фарби (час їх висихання при опроміненні короткохвильовим IR-нагрівачем не перевищує 5 - 12 хвилин).
Переваги UV-матеріалів і технологій в порівнянні з традиційними видами шпаклювальних матеріалів:
Основний недолік UV-матеріалів - висока вартість - окупається малими термінами тужавіння, які дозволяють скоротити час ремонтної фарбування машини до 1,5 години.
Слід зазначити, що час висихання UV-матеріалів різних виробників різна. Так, італійські шпаклівки і грунти при опроміненні тверднуть за 2-3 хвилини, а німецькі ще швидше - всього за 3 - 5 секунд (!). Правда, останні в кілька разів дорожче. Для мінімізації витрат дорогі UV-матеріали наносять дуже економно - за допомогою спеціальних шприців-дозаторів.
Тема: Контроль якості фарбування кузовів
Якість лакофарбових покрить визначають за такими показниками:
а) колір
б) чистота
в) блиск
г) твердість
д) міцність на згин і удар
ж) товщина плівки
з) стійкість до дії різних речовин
к) адгезія
Колір плівки визначають за картотекою колірних еталонів або за допомогою фотоколориметра. Чистоту лакофарбового покриття визначають візуально. Блиск лакофарбового покриття оцінюють за допомогою фотоелектричного блискоміра, порівнюючи з гянцем спеціального скла , взятого за еталон. Твердість плівки лакофарбового покриття визначають за часом загасання коливань маятника встановленого на поверхні плівки відносно часу загасання коливань на пластинці з фотоскла. Вона повинна становити 0.5 - 0.8 твердості скла. Міцність плівки на згин визначають за допомогою шкали гнучкості яка являє собою набір стержнів різного діаметру навколо яких згинають пластику із жесті на яку нанесене лакофарбове покриття. Міцність плівки на удар оцінюють за допомогою спеціального приладу при падінні вантажу масою 1 кг з певної висоти. Товщину лакофарбової плівки визначають за допомогою спеціальних приладів ( товщиномірів) не порушуючи цілісності плівки. Вологостійкість плівки визначають з допомогою гідростата при вологості 100% і температурі 40 градусів. Стійкість до сольового туману визначають у спеціальній камері розпиленням 3% розчину хлористого натрію. Атмосферостійкість визначають в апараті штучної погоди обладнаного різними типами ламп при підвищеній вологості. Адгезію лакофарбового покриття оцінюють методом надрізу.
Тема: Діагностика технічного стану автомобілів
Учбові питання
1.Призначення і види діагностики
2. Методи та способи діагностики
3.Методи організації діагностики
4. Діагностика двигуна
5. Діагностика системи живлення
6. Діагностика трансмісії
7. Діагностика ходової частини
8. Діагностика механізмів керування автомобілем
Література: Б.І. Костів " Експлуатація автомобільного транспорту" стр.277 - 291 ,А. Ф. Антоненко, Р. М. Недашківський " Комплексна система технічного обслуговування тракторів і автомобілів" стр. 161 - 208
1.Діагностика - визначення технічного стану автомобіля, його вузлів, механізмів, агрегатів без їх розбирання і прогнозування ресурсу їх безвідмовної роботи. Види діагностики: загальна і поглиблена. Загальну діагностику проводять перед першим ТО , а поглиблену - перед другим.
2. Методи діагностики; субєктивні і обєктивні.Субєктивні методи діагностики здійснюються без застосування технічних засобів (віброакустичний,зоровий, з допомогою нюху або дотику).Обєктивні методи діагностики здійснюються з допомогою технічних засобів (віброакустичний, електричний , хімічний). Способи діагностики: стаціонарна і ходова.Стаціонарна діагностика проводиться на спеціально обладнаних постах, а ходова - під час руху автомобіля.
3.Методи організації діагностики: на поточних лініях, на тупикових постах. Поточний метод діагностики передбачає проведення операцій у певній послідовності. Діагностування на тупикових постах застосовують переважно для проведення загальної діагностики.
4. При діагностиці двигуна звертають увагу на такі показники: а) наявність стуків і шумів б) наявність вібрації в) тиск масла в масляній магістралі г) перевірка натягу пасів приводу вентилятора ,генератора, компресора д) охолоджувана здатність радіаторів ж) забруднення центрифуги з) придатність масла до подальшої роботи.
5.При діагностиці системи живлення визначають : а) герметичність форсунок б) тиск початку розпилювання палива форсункою в) момент подачі палива плунжерною парою г) забруднення повітреочисника д)забруднення паливних фільтрів.
6 При діагностиці трансмісії звертають увагу на такі показники: а) вільний хід педалі муфти зчеплення б) наявність стуків і шуиів в) тепловий стан вузлів і агрегатів трансмісії .
7. Під час діагностики ходової частини перевіряють: а)сходження коліс б) розвал коліс в) тиск повітря в шинах г) стан підшипників коліс д) ступінь спрацювання протектора шин.
8. При діагностиці механізмів керування визначають : а) люфт рульового колеса б) зусилля на ободі рульового колеса в) люфт у рульових тягах г) гальмівний шлях д) відхилення від напряму руху при гальмуванні ж) герметичність гальмівної системи і системи рульового керування з) вільний і повний хід гальмівної системи.
Тема : Система керування інжекторним двигуном.
Учбові питання:
1. Призначення системи
2.Датчики і виконавчі пристрої
3. Обробка сигналів
4. Фунція самодіагностики
5. Скорочений режим роботи
6. Система адаптації
Тема: РЕМОНТ РУЛЬОВОГО УПРАВЛІННЯ І ГАЛЬМІВНОЇ СИСТЕМИ
Основні
дефекти рульового управління. Характерні дефекти рульового управління колісних
машин - це спрацювання втулок і ролика вала сошки, черв'яка, підшипників і
місць їх посадки, різьбових отворів картера, деталей кульових з'єднань рульових
тяг; погнутість тяг і ослаблення кріплення рульового колеса на валу; тріщини і
злами на фланці кріплення картера рульового механізму; знос деталей
гідропідсилювача і масляного насоса.
В результаті зносу деталей рульового управління порушується його регулювання,
не може управління і втрачається стійкість на ходу, особливо у
колісних тракторів і екскаваторів.
Відновлення деталей рульового управління колісних машин. Малоспрацьовані
черв'як і ролик зачищають або проточують до виведення слідів зносу. При
великому зносі, який не можна компенсувати регулюванням, ці деталі замінюють.
Посадочні місця вала сошки під втулки шліфують під ремонтний розмір, а при
необхідності хромують під номінальний розмір. Пошкоджену на валу різьблення
проточують, наварюють і нарізають нову номінального розміру. Втулки
замінюють і розгортають під розмір опорних шийок вала сошки або рульового вала.
Зсув осей розгорнутих втулок допускається не більше 003 мм, а овальність - не
більше 005 мм
Кермові вали і вали сошки з тріщинами, скручуванням або зі зношеними шліцами
замінюють новими.
Місця посадки підшипників в картері рульового механізму відновлюють постановкою
втулки. Картер рульового механізму з тріщинами або обломами замінюють
новим.
Зношені кульові пальці зазвичай заміняють, але при необхідності їх відновлюють
наплавленням або осадкою. Перед осадкою головку нагрівають до температури 850 °
С (червоний колір гартування), ставлять на спеціальну оправку і роздають
конічним пуансоном. Обробляють кульові головки на токарному верстаті
спеціальними різцями і пристосуваннями.
Ослаблені або зламані пружини і зношені вкладиші кульових пальців замінюють
новими. Погнуті кермові тяги і важелі правлять в холодному стані або з місцевим
нагріванням до температури 800 ° С. Перед правкою пустотілі тяги заповнюють
дрібним піском.
Складання і регулювання механізмів рульового управління колісних машин.
Збирають рульовий механізм на спеціальних стендах або підставках. Рульовий
механізм без гідропідсилювача збирають приблизно в такій послідовності.
Запресовують черв'як на вал рульового управління так, щоб він сидів щільно, без
гойдання (черв'як не повинен мати раковин і ступеневої зносу на зубах і
конусах). Вал рульового управління встановлюють в колонку і кріплять до картера
рульового механізму. Підшипники регулюють прокладками, встановленими під
фланцем рульової колонки.
Правильно змонтований вал черв'яка рульового управління колісних тракторів
не повинен мати осьового зазору. Він повинен повертатися в підшипниках від
зусилля 3-8 Н на плечі, рівному радіусу рульового колеса. Зусилля вимірюють
динамометром. Встановлюють сошку з роликом і регулюють її зачеплення з
черв'яком. Ролик повинен знаходитися посередині черв'яка (визначають по
половині числа обертів рульового колеса, необхідних для повороту ролика з
одного крайнього положення в інше). Зазор в зачепленні зубів ролика сошки з
черв'яком регулюють переміщенням сошки керма регулювальним гвинтом або
прокладками.
Зачеплення ролика з черв'яком відрегульовано правильно, якщо вал рульового
управління обертається вільно, без заїдань, від зусилля не більше 15-25 Н,
прикладеного до обода рульового колеса, а нижній кінець рульової сошки
переміщається не більше ніж на 015 мм.
При складанні рульового механізму необхідно особливу увагу звертати на
справність прокладок ущільнювачів, сальників та інших ущільнювачів пристроїв.Несправності гальмівної системи. До цих несправностей відносяться дефекти
вузлів гідроприводу гальм: гальмівних дисків, гальмівних барабанів, накладок,
колодок і т. П. Характерними для гальмівної системи з гідравлічним приводом є
несправності колісних і головних циліндрів під поршень. Можуть мати місце
тріщини і обломи деталей, Надір, ризики або знос дзеркала циліндрів під
поршень.Ремонт деталей гальмівної системи. Обов'язковими операціями при капітальному
ремонті є розточування гальмівних барабанів і заміна накладок гальмівних
колодок. Накладки приклеюють до гальмівних колодок на пристосуванні (рис. 114)
клеєм ВС-10ТМал. 114. Пристосування для приклеювання накладок до гальмівних колодок:1 - штурвал, 2 - обтискове кільце, 3 гвинт, 4 - фіксатор, 5 - гальмівні
колодки, 6 - плитаПриклеєні накладки перевіряють на зрушення під пресом. Якщо при свідченні
манометра преса 75-80 МПа накладка не зрушується, то якість склеювання хороше.Зношені гумові манжети гідравлічних гальмівних циліндрів замінюють новими.
Отвори гальмівних циліндрів відновлюють розточуванням з подальшим хонінгуванням
під ремонтний розмір поршнів. Деякі ремонтні підприємства відновлюють ці отвори
спеціальними протяжками на протяжні верстати або прошивають на гідравлічному
пресі.При зносі отворів гальмівних циліндрів більше 03 мм циліндри розточують і
запресовують в них сталеву або чавунну гільзу з натягом 002 мм і закріплюють її
клеєм. Потім розточують або розгортають і хонінгують під нормальний розмір.
Овальність і конусність робочої поверхні циліндра допускається не більше 001
мм.
У разі постановки гільзи в головний гальмівний циліндр перед обробкою гільзи в
ній свердлять отвори під перепускний і компенсаційний клапани.
Зношені алюмінієві поршні відновлюють під збільшений розмір роздачею конічними
пуансонами і подальшої обточуванням на токарному верстаті до ремонтного або
нормального розміру.Після складання гальмівні циліндри випробовують на герметичність повітрям під
тиском 05-06 МПа з зануренням в гальмівну рідину.Зношені поверхні гальмівних барабанів розточують до виведення слідів зносу.
Сильно зношені або вже розточеніі барабани відновлюють постановкою чавунного
або сталевого кільця, яке потім розточують під креслярський розмір. Встановлене
кільце кріплять гвинтами з потаємною головкою або приварюють з торців.
Розточують гальмівні барабани з маточиноюЗруйновані діафрагми і зношені клапани пневматичних гальм замінюють новими.
Складання і регулювання гальм. Фрикційні накладки встановлених гальмівних
стрічок і колодок повинні щільно прилягати до гальмівного барабану всієї
робочої поверхнею. Допускається зачищати нерівності, задираки і ризики на
робочій поверхні накладок. Колодки встановлюють на диск гальма так, щоб всі шарнірні
з'єднання були рухомі.
Гальмівні гідравлічні циліндри перед установкою перевіряють на підтікання та
щільність з'єднання. Для цього в циліндрі натисканням на шток створюють тиск
згідно з технічними умовами. Протягом 3 хв не повинно бути підтікання рідини ні
в одній точці.При установці трубопроводів і шлангів стежать, щоб вони не стикалися з рухомими
Тема: Ремонт деталей механізму газорозподілу
Основними несправностями газорозподільного механізму є: порушення теплових зазорів клапанів; витягування зубчастого ременя, знос зубчастих шківів; знос ланцюга і зірочок приводу; ослаблення кріплень кришок підшипників розподільного вала, нещільне закриття клапанів через зношування їх головок і сідел; зниження пружності клапанних пружин, знос підшипників, шийок і кулачків розподільного валу, штовхачів, поршнів і їх осей, втулок і сідел клапанів. В результаті порушення регулювань і зносу деталей газорозподільного механізму прослуховуються стуки і шум при роботі двигуна. він втрачає потужність, йде підвищена витрата масла і т. д. Після перевірки технічного стану визначають необхідність ремонту або регулювання механізму газорозподілу.
РОЗПОДІЛЬЧИЙ ВАЛ І ЙОГО ПРИВІД.
Основними несправностями є знос опорних шийок вала, знос і задираки кулачків і вигин вала. Ці ушкодження викликають стуки в клапанному механізмі, а збільшення зазорів в підшипниках призводить до падіння тиску масла в системі змащування.
Для відновлення зазорів в підшипниках розподільчого вала відновлюють, перешліфовувати його опорні шийки, канавки для подачі масла поглиблюють, щоб після повторного шліфування масло надходило до деталей двигуна. Шийки вала шліфують під найближчий ремонтний розмір. Після шліфування їх полірують пастою ГОІ.
При невеликому зносі кулачків розподільного вала їх зачищають шліфувальною шкуркою, спочатку крупнозернистою, потім дрібнозернистою. Місця викришування металу на торцях вершин кулачків обпилюють шліфувальним бруском або наждачним шкіркою до усунення гострих кромок. При викрашування понад 3 мм по довжині кулачка вал підлягає заміні. Якщо кулачки розподільного вала зношені по висоті, їх шліфують на спеціальному копіювально-шліфувальному верстаті для розподільних валів. Кулачки вала, що мають значний знос, можна відновити наплавленням з подальшим шліфуванням.
Після ремонту вал промивають і перевіряють висоту кулачків. При зносі кулачків по висоті більш ніж на 0,5 мм в порівнянні з номінальною висотою вал замінюють, так як при такому зносі погіршується наповнення циліндрів, в результаті чого потужність двигуна падає.
Якщо опорні шийки розподільного вала зношені понад допустимих меж, їх відновлюють наплавленням, осталюванням або хромуванням, а потім шліфують.
Вигин розподільного вала вимірюють спеціальним індикатором і перевіряють по середньої шийки. Допустимий вигин (биття) може бути не більше 0,10 мм. Якщо він більше, потрібно вал правити.
На опорних поверхнях під шийки вала не повинно бути подряпин і зазорів, а на корпусах підшипників не повинно бути тріщин. Після очищення і промивання розподільного вала перевіряють зазор між його шийками і отворами опор на голівці циліндра. Для того щоб визначити зазор потрібно виміряти діаметр шийки розподільного вала, встановити відповідний їй підшипник, закріпити його корпус і виміряти внутрішній діаметр підшипника, потім відняти друге значення з першого. Різниця значень і є величина зазору. Вимірюють зазор і каліброваного пластмасовою дротом. Допустимий зазор може бути не більше 0,2 мм.
РЕГУЛЮВАННЯ ЛАНЦЮГА ПРИВОДУ РОЗПОДІЛЬНОГО ВАЛУ.
Ланцюг не повинна мати відколів і тріщин. Вона вважається працездатною при витягуванні не більше ніж на 4 мм. Для регулювання натягу ланцюга слід відвернути стопорний болт натягача на 0,5 обороту. Провернути колінчастий вал за годинниковою стрілкою на два оберти з відпущеним стопорним болтом натягача для усунення всіх зазорів в приводі розподільного вала, потім стопорний болт загорнути до упору.
Перевірка пружності пружин клапанів проводиться як без зняття їх з двигуна, так і після розбирання клапанного механізму. Для контролю пружин на двигуні необхідно зняти клапанну кришку, встановити поршень відповідного циліндра у верхню мертву точку такту стиснення приладом КИ-723 виміряти зусилля, необхідне для стиснення пружин. Якщо воно виявиться менше гранично допустимого, пружину заміняють або підкладають під нижню опорну тарілку додаткову шайбу.
Ремонт клапанів. Перед розбиранням клапани розмічають по циліндрах. Газопроводи, камери згоряння, клапани та інші деталі очищають від нагару і промивають. Якщо робоча фаска клапана підгоріла або піддалася корозії то її шліфують. Але при цьому циліндрична поверхня головки клапана повинна мати висоту не менше 0,3 мм. Гострий край головки клапана може перегрітися і викликатиме краплинне запалювання. Якщо немає шліфувального верстата, то клапан закріплюють в патроні токарного верстата і робочу фаску обробляють напилком, зберігаючи при цьому початковий кут фаски. Малий знос можна відшліфувати вручну. Для цього в клапанне гніздо кладуть наждачний папір і по її шорсткою стороні обертають клапан, поки фаска його очиститься. Знос торця стержня клапана відшліфовують наждачним кругом.
Знос між стрижнем клапана і його направляючою втулкою вимірюють індикатором. Допускається зазор до 0,15 мм. Зношені втулки перепресовують і нові втулки розгортають під стрижні клапана. Клапан повинен під дією своєї ваги вільно опускатися під втулку, але в той же час рукою не повинен відчуватися зазор у втулці. Хоча клапанне гніздо виготовляють з дуже твердого матеріалу, але і воно зношується, підгорає і кородує. Робочу фаску гнізда шліфують конічними абразивними дисками), але якщо пошкодження фаски незначні, то вони усуваються в ході притирання.
Притирають клапан, поки на фасках клапана і гнізда не утворюються пояса шириною 1,5. 2,0 мм, що знаходяться иа середині фаски. У разі потреби гніздо шліфують диском під кутом 15 °. Якщо клапан провалюється глибоко, то зношене гніздо замінюють. Це треба зробити і тоді, коли ослаб натяг гнізда в голівці блоку. Для цього випускають гнізда ремонтного розміру.
Для заміни гнізда головку нагрівають до температури 170. 200 ° С, Після запресовування зачеканюють
Перевіряють жорсткість клапанних пружин. На вагах стискають пружину до певної довжини і визначають при цьому виникає силу за показаннями ваг. Порівнюють з даними таблиці. Якщо жорсткість зменшилася більш 10%, пружину заміняють.
Так як через шліфування клапана і його гнізда натяг пружини зменшиться, то під пружину треба встановити додаткову сталеву шайбу. Пружину зі змінним кроком витків встановлюють так, щоб витки з меншим кроком були в сторону головки блоку.
Після притирання клапанів замінюють зношені масловідбивні ковпачки стрижнів клапанів. При неможливості придбання нових заводських ковпачків для двигуна ВАЗ в журналі «За кермом» № 8, 1986 р пропонується надійна і проста у виготовленні конструкція ущільнення (152). Масловідбивним елементом служить кільце з фторопласту - пластмаси, стійкої до нафтопродуктів і володіє низьким коефіцієнтом тертя через що незабаром заповнюється порожнину між денцем ковпачка і шайбою , забезпечуючи надійне і довговічне ущільнення вузла.
Потреба в заміні масловідбивних ковпачків може виникнути і раніше, до поточного ремонту двигуна. На це вказують підвищена витрата масла, димний вихлоп і замаслення свічок. Якщо при цьому компресія в циліндрах нормальна, то, очевидно, що зносилися ковпачки.
Для заміни ковпачків надходять у такий спосіб. Вивертають свічку того циліндра, де ковпачки замінюються, ставлять поршень в ньому в ВМТ і знімають розподільний вал, важелі і пружини, підтримуючи клапан викруткою, вставленої в отвір свічки. Ковпачки зазвичай знімають двома викрутками або плоскогубцями, але так можна легко зламати верхню частину напрямної втулки клапана, виготовленої з тендітною металокераміки. У журналі «За кермом» № 10, 1989 г. для цієї мети пропонується знімач (153) ударного типу. Захоплення виточують на токарному верстаті і розпилюють уздовж. У розпил вставляють пластину 4, що сполучає захоплення зі стрижнем 5: Захоплення надягають на ковпачок і його половинки стягують хомутом /. Б'ючи вантажем 6 по наконечнику 7, знімають ковпачок. Новий ковпачок встановлюють за допомогою пристосування, зображеного на 154.
Якщо для заміни немає нових ковпачків, то можна скористатися способом, запропонованим журналом «За кермом» № 3, 1986 р продовження працездатності зношених ковпачків (155).
При роботі гума втрачає еластичність і недостатньо стискається пружиною навколо стрижня клапана. Для усунення цього недоліку під пружину накладають нитковий бандаж, як показано на малюнку. На шийку ковпачка намотують три витка капронової нитки № 10 або 20. Якщо є тільки тонкі нитки № 50 або 60, то попередньо їх скручують втричі. Нитки повинні знаходитися в пазу між гумою і пружиною і кінці їх пов'язують вузлами. Сильно нитки не натягують. Стрижень клапана повинен слабо захоплюватися ковпачком так, щоб клапан не падав під власною вагою.
Головки блоку відливають з алюмінієвого сплаву. Тріщини сорочки охолодження закладають епоксидним клеєм. Герметичність сорочки перевіряють опресуванням під тиском 0,4 МПа (4 кгс / см2).
Деформовану площину роз'єму головки фрезерують або шабрують. Допустима неплощинність в залежності від довжини головки складає 0,05. 0,15 мм. При ремонті знімається можливо тонка стружка, так як через зменшення висоти камери згоряння підвищується ступінь стиснення двигуна. Найменш допустима висота камери згоряння наводиться в технічних умовах.
При пригоранні прокладки головки блоку на поверхні головки виникає поглиблення, яке треба заварити і потім зарівняти. Тимчасово туди можна покласти листовий азбест відповідної товщини.
Різьблення свічкових отворів зношуються з різних причин. На холодному двигуні свічку можна затягнути моментом 37 ± 2 Н м (3,7 ± 0,2кгс- м). Якщо таким же моментом затягнути свічку і на гарячому двигуні, то при охолодженні натяг збільшується і при відверненні свічки різьблення швидко зношується. У гарячу головку або зношену різьблення свічку загортають слабкіше, моментом 26. 30 Н м (2,6. 3 кгс- м). Шайба під свічку повинна бути м'якою. Затверділу шайбу нагрівають до червоного і потім охолоджують у холодній воді. Якщо товщина шайби менше 1 мм або її зовсім немає, то різьблення свічки виходить в камеру згоряння, де покривається нагаром. При вивертанні свічки така різьблення псує різьблення в свічковий отворі головки блоку.
Зірвану різьбу свічкового отвори відновлюють різьбовим ввертиш (156). Для цього отвір свічки розгортають до діаметра 18,3 мм. Торець баньки на глибину 5,5 мм, його поверхня повинна бути не нижче 5-го класу шорсткості. В отворі нарізають різьбу М20Х 1,5, і туди вкручують різьбову вставку, попередньо підклавши під його буртик мідну шайбу товщиною 1 мм. Виступаючий в камеру згоряння кінець різьбової вставки розвальцьовують і обробляють за формою камери. Свічковий отвір калібрують мітчиком М14х1,25.
У розподільних валів зношуються опорні шайби і кулачки. Через зношеність кулачка зменшується підйом клапана і порушуються фази газорозподілу. Внаслідок цього зменшується потужність двигуна.
Кулачки повинні бути дзеркально гладкими. Невеликі риски і задири усувають поліруванням. Сильно зношені або з задирами кулачки перешліфовувати на копіювальному верстаті, наявному на ремонтному підприємстві.
У двигунів ВАЗ робочі поверхні важелів механізму газорозподілу повинні бути дзеркально чистими. При надирі або зносі у вигляді дрібних граней, а в місці первинного контакту з кулачком освіти поглиблення не більше 0,3 мм важіль треба ремонтувати. Якщо знос глибше 0,3 мм, важіль замінюють. За тильній стороні кулачка розподільного вала можна судити про якість регулювання клапанів. Якщо ця поверхня вся темна, то тепловий зазор між кулачком і важелем існував. Якщо є кільцеві смуги на краю кулачка, то, ймовірно, важіль стояв з перекосом. Причиною може бути зміщення притискної пружини, важеля або її деформація. Якщо ж тильна сторона кулачка блищить по всій поверхні, то це вказує на малий тепловий зазор. Перевіряють пружини важелем. Їх відігнуті кінці повинні бути на одній осі, перпендикулярної поздовжньої площини, а відстань між ними і крайньою точкою петлі має становити 35 мм. У разі потреби подгинають спіральну частину пружини, так як неспіввісність її кінців є зазвичай причиною перекосу важеля і появи стуку клапана.
Робочі поверхні важелів і кулачків захищають наждаковими колами різної зернистості з наступним поліруванням. Знімають можливо мінімальний шар металу, не спотворюючи форму поверхні і зберігаючи верхній твердий шар. Можна скористатися і алмазним надфілем, алмазними брусками і шкіркою. Обробку закінчують поліруванням.
Зношені кулачки чавунного розподільного вала двигуна ВАЗ наплавляють високолегованим електродом Т-590 або T-62Q. Застосовуючи електрод діаметром 4 мм, встановлюють силу струму 200. 220 А. Так як чавунний розподільний вал через його крихкості майже не можна правити, то при наплавленні застосовують такий спосіб, щоб вал деформувався можливо менше. Наплавлену поверхню з твердістю HRC 55. 62 обробляють на копіювальному верстаті. При наплавленні покриття електрода не повинно містити вологу, тому електроди попередньо витримують при температурі 180. 200 ° С протягом 2 3 год.
Якщо розподільний вал знаходиться в блоці і обертається в біметалевих втулках, то в ремонтних підприємствах його опорні шийки можуть бути перешліфувати під ремонтні розміри. Биття розподільного вала, встановленого крайніми шийками на призми, допускається в межах 0,02. 0,03 мм.
Тема: Ремонт деталей систем мащення і охолодження
· Ремонт деталей системи охолодження
2.Ремонт деталей системи мащення
1.Характерними дефектами радіаторів водяної системи охолодження є: відкладення накипу на внутрішніх стінках і засмічення резервуарів і трубок, відпаювання трубок від опорних пластин; ушкодження трубок і охолодних пластин; тріщини на нижніх і верхніх резервуарах. Зазначені несправності приводять до порушення теплового режиму двигуна і його перегріву.
Більшість ушкоджень виявляють зовнішнім оглядом та випробуванням радіатора під тиском, попередньо очистивши його від бруду і накипу. Зовні радіатора бруд видаляють струменем води, а потім продувають його стисненим повітрям. Ушкоджені охолодні пластини вирівнюють правкою. Накип усередині радіатора видаляють промиванням 5% розчином соляної кислоти з додаванням 2...3 г/л інгібітору ПБ-5 або И-1М (2М), а також 5% розчином фосфорної кислоти з додаванням 1...2% хромового ангідриду. Температура розчину 60...80°С, час промивання 5...15 хв у залежності від товщини і хімічного складу накипу і застосовуваних реагентів.
Потім радіатор промивають у лужному розчині марки СМС. Серцевини радіаторів, що мають товсті і щільні відкладення, кип'ятять у 5...6% водному розчині каустичної соди протягом 25...30 хв, потім шомполом прочищають трубки, промивають їхньою гарячою водою і продувають стисненим повітрям.
Потім радіатори перевіряють на герметичність водою або повітрям під тиском 0,10...0,15 МПа протягом 2...3 хв. Теча і просочування води (повітря) не допускаються.
Для перевірки стану радіаторів до і після ремонту застосовують стенди типу КП-2002. Стан кожної трубки серцевини визначають у ванні з водою, подаючи стиснене повітря до трубки. По появі пухирців повітря знаходять місця ушкодження трубки. Серцевини радіаторів вибраковують при наявності більш 25% ушкоджених трубок, а також при ушкодженні опорних і охолодних пластин.
Ушкодження в трубках зовнішніх рядів запоюють припоєм ПОС-3. Ушкоджені внутрішні рядки трубок запаюють з обох кінців, попередньо зжавши плоскогубцями. Запаювати допускається не більш 5% трубок радіатора. Якщо ушкоджені більш 5% трубок заміняють новими. Для цього ушкоджені трубки нагрівають до температури 300...400 °С и відпаюють їх від опорних охолодних пластин. Нагрівання роблять гарячим повітрям або нагрітим шомполом. Замість ушкоджених трубок впаюють нові або відновлені.
Пайку радіатора роблять за допомогою спеціальних паяльників, використовуючи для цього припой ПОС-30 і флюс - хлористий цинк. Тріщини і розриви в сталевих і латунних резервуарах усувають пайкою або припаюванням латок м'яким припоєм. Після ремонту серцевину, а потім радіатор у зборі випробують на герметичність.
Накип з термостатів видаляють так, як із серцевин водяних радіаторів. Тріщини в гофрованому елементі термостата запаюють олов'янисто-свинцевим припоєм. Перед пайкою порожнину елемента заповнюють 15% розчином етилового спирту.
Після відновлення термостат випробують у ванні з підігрітою водою. Початок відкриття клапана повинний бути при 70 °С, а повне відкриття при 85 °С. Повний підйом клапана повинний бути в межах 9,0...9,5 мм. Його регулюють довжиною ходу штока.
Основними дефектами деталей водяного насоса є: ушкодження деталей ущільнення і підшипників; знос посадкових місць під підшипники і сальники у корпусі і на валику; бічних поверхонь лопаток; ушкодження різьблення і шпонкових пазів; тріщини в корпусі.
Ушкоджені (зношені) ущільнення і підшипники заміняють новими. Тріщини в корпусі насоса заварюють біметалічними електродами газовим зварюванням або латунними прутками припоями ЛОК (ЛОМНА), дротом ПАНЧ-11 і т.п. Ушкоджене різьблення розсвердлюють і нарізають нову збільшеного розміру або ставлять різьбові вставки.
На зношені посадкові місця під підшипники наносять шар металу насталюванням або склад на базі епоксидної смоли, потім їх розточують до нормального розміру. Ушкоджені поверхні під втулки рове до виведення слідів зносу, потім запресовують ремонтні з натягом 0,015...0,045 мм. Після запресовування втулки розвертають (розточують) у розмір. Нерівності торцевых поверхонь корпусів усувають проточуванням або шліфуванням. Торцеве биття не повинно бути більш 0,1 мм у крайніх точок.
Зношені посадкові місця валика водяного насоса під підшипники і сальники, а також ушкоджену різьбову поверхню наплавляють у середовищі вуглекислого газу (пари і т.п.). Після наплавлення різьбову поверхню обточують і нарізають нову різьбу, а посадкові місця після обточування шліфують до нормального розміру. Шпонкові пази, при зазорі більш 0,05 мм, фрезерують під збільшений розмір або фрезерують у новому місці паз нормального розміру.
При зборці насоса звертають увагу на напресовку підшипників, установку ущільнень. У зібраному насосі валик повинний легко обертатися від руки. Зібраний насос обкатують протягом 3 хв при температурі води 85...95 °С. Після ремонту насос перевіряють на герметичність під тиском 0,07...0,12 МПа протягом 1 хв при обертовому і не обертовому валику. Підтікання води не допускається.
У вентиляторів зношуються посадкові місця під підшипники в шківах і конічні поверхні струмка під пас; буває ослаблення заклепок, вигин лопат і хрестовини.
Зношені посадкові місця шківа розточують і на епоксидному клею установлюють втулку, що потім розточують до нормального розміру. Можна відновлювати посадкове місце осталюванням з наступним розточуванням.
Контроль зносу струмків у шківах виробляється калібром і щупом. Допускається просвіт між калібром і стінками струмка до 0,4 мм. При зносі до 1 мм струмки проточують до виведення зносу.
При ослабленні кріплення лопатей заклепки підтягують, а якщо отвори під заклепки мають овальну форму, їхній розсвердлюють і ставлять заклепки збільшеного діаметра. При заміні лопатей, різниця в їхній масі не повинна перевищувати 3... .5грамів. Кромки лопатей повинні лежати в одній площині, відхилення допускається не більш 1 мм, при більшому - хрестовину і лопатей правлять. При виправленні хрестовини повинна бути збережені форма і кут нахилу лопатей щодо площини обертання. Кут нахилу лопатей для двигунів різних марок складає 30...35. ° Після ремонту вентилятор статично балансують на спеціальному пристосуванні. Дисбаланс допускається не більш 20 м. Якщо він більше, тоді свердлять отвори в торці чавунного шківа або з опуклої сторони лопатей приварюють або приклепують пластини.
2.Радіатор системи мащення може мати такі дефекти: тріщини в бачках, пошкодження трубок серцевини. Дані дефекти усувають паянням. Масляний насос може мати такі дефекти: спрацювання посадочних поверхонь, спрацювання валів шестерень, спрацювання або викришування зубів шестерень, руйнування пружини редукційного клапана. Спрацьовані посадочні поверхні відновлюють насталюванням. Аналогічним способом відновлюють спрацювання валів. При спрацюванні або викришуванні зубів шестерень їх замінюють на нові Поломану пружину замінюють. У розбірних масляних фільтрів замінюють фільтрувальні елементи. У центрифугах очищають ковпак ротора від бруду.
Тема; Ремонт деталей системи живлення
Паливну апаратуру дизелів ремонтують після її перевірки на спеціальних стендах. Паливні фільтри випробовують на герметичність і гідравлічний опір фільтрувальних елементів. Паливопроводи низького тиску візуально перевіряють на герметичність, наявність вмятин, перегинів. Стисненим повітрям опресовують. Паливопроводи високого тиску перевіряють зовнішнім оглядом, а також контролюють форму і довжину по шаблонах. Помятість і спрацювання зовнішньої конічної поверхні допускається не більше 0,08 мм, Каліброваним дротом діаметром 1,5 мм перевіряють діаметр каналу.. Паливопроводи продувають стисненим повітрям. При спрацюванні конічного наконечника його обрізують і утворюють новий конус з допомогою спеціального пристрою. Деталі паливопідкачувального насосу , які мають тріщини і відколи на ремонтують. Деталі насосу які працюють у парі не розкомплектовують. Спрацьовані деталі форсунок замінюють на нові або відремонтовані. Перевірку та регулювання форсунок проводять на спеціальному стенді. Деталі паливного насосу високого тиску ремонтують слідуючим чином: спрацьовані кулачки розподільного валу наплавляють і обробляють на спеціальному стенді, зовнішню поверхню плунжера хромують, нікелюють а потім шліфують. Паливні насоси високого тиску після складання перевіряють і регулюють на спеціальних стендах. Паливні баки можуть мати тріщини і вмятини. Вмятини усувають шляхом витягування деформованого місця. Тріщини заварюють попередньо видаливши з баку залишки палива. Після ремонту бак перевіряють під тиском 0.,3 - 0,5 атм.
Тема: Ремонт деталей ходової частини
Характерні дефекти ресор - зменшення стріли прогину, тріщини та поломка окремих листів, спрацювання втулок, пальців, пошкодження центрувальних болтів ресор. Зменшений прогин ресор відновлюють правкою в холодному стані на спеціальному стенді. Тріснуті та поломані листи замінюють. Спрацьовані втулки, пальці, центрувальні болти , хомути кріплення замінюють на нові. Перед складанням листи ресори змащують графітною змазкою. Спрацьовані ущільнення амортизаторів і втулки замінюють на нові. Клапани і гнізда притирають. Колеса ТЗ можуть мати такі дефекти : тріщини, вмятини,спрацювання отворів під шпильки у ступиці, спрацювання посадочних місць під підшипники.. Тріщини , які не проходять через отвори - заварюють. Вмятини на диску випрямляють вручну з нагріванням або на спеціальному стенді.Спрацьовані отвори заварюють, а потім розвердлюють. Послаблені посадочні місця під підшипники відновлюють запресуванням проміжних кілець і розточують до номінального розміру. Ступиці з тріщинами і пошкодженими шпильками - бракують. При спрацюванні протектора пневматичної шини його відновлюють шляхом наварювання . Камери шин, які мають проколи, ремонтують накладанням латок, що кріпляться з допомогою спеціального клею. Відремонтовані камери випробовують на герметичність у ванні з водою під тиском 0,3 - 0,5 атм.
Тема: Ремонт кузовів
Учбові питання:
1.Основні пошкодження кузовів
2. Дефектація кузова
3. Розбирально -складальні роботи
4. Обладнання для виправляння кузовів
5. Методи ремонту кузовів
Література: Б. С. Бабіч , В.В. Лущик « Технічне обслуговування й ремонт металевих кузовів автомобілів» стр 289 - 340
1. Пошкодження металевих кузовів колісних ТЗ діляться на дві групи: аварійні і експлуатаційні. Аварійні пошкодження виникають внаслідок ДТП. Найбільші пошкодження кузовів виникають внаслідок лобового зіткнення ТЗ. Невидимі деформації можна виявити за наявністю перекосів у лицьових деталях. До експлуатаційних пошкоджень кузовів відносяться: умятини, тріщини, розриви ,пробоїни, обриви, прогини , перекоси, скручування , порушення заклепкових зєднань, корозія (суцільна і місцева).
2. Дефектація кузовів ТЗ проводиться такими методами: візуальний контроль, контроль геометрії кузова шляхом вимірювання. Для виявлення перекосу кузова вимірюють діагональні розміри його основи, дверних прорізів, прорізів капота , кришки багажника , вітрового і заднього скла.
3.Розбирання кузовів ТЗ може бути частковим і повним. Часткове розбирання кузова проводять під час поточного ремонту або ремонту за потребою. Повне розбирання кузова проводять під час капітального ремонту. Вузли кузова можуть бути правильно розібрані за умови дотримання певної технологічної послідовності. Тому порядок розбирання кузова ТЗ визначається технологічним процесом , який розробляють на кожний тип кузова. Складання кузова проводять у зворотньому порядку до розбирання.
4. При ремонті кузовів застосовують такі види обладнання: гідравлічні розтяжки, гідравлічні косинці , ремонтні підйомники. Гідравлічні розтяжки використовують для виправляння аварійних пошкоджень кузова. Гідравлічна розтяжка складається з насосу, масляного баку , зворотнього клапана, гідроциліндра , зєднувального шлангу ,набору додаткового обладнання. Основними елементами гідравлічного косинця є рама, розпірний косинець , гідравлічна розтяжка. Ремонтні підйомники дають можливість виконувати весь комплекс робіт, повязаних із виправлянням пошкодженого кузова. Основними елементами ремонтного підйомника є рама, гідроциліндр, електродвигун , насос , рихтувальне обладнання .
5. Є такі методи ремонту кузовів : стаціонарний і потоковий . При стаціонарному методі кузов встановлюють на стенді а при потоковому - переміщують між спеціалізованими робочими постами. Потоковий метод підвищує точність і якість виконання кузовних робіт а також продуктивність праці. Потокові лінії можуть бути двох видів : з нерухомими і пересувними кузовами.
Тема: Обкатка нових або відремонтованих транспортних засобів
Загальні рекомендації по виконанню обкатки
1. Навантаження на транспортний засіб не повинно перевищувати 0,7- 0,8 номінального
2.Швидкість руху ТЗ - 35_40км/год
3. Постійний контроль за показами контрольно - вимірювальних приладів
4 Контроль температури нагрівання підшипникових вузлів, картерів вузлів трансмісії
5 Після закінчення обкатки ( через 1000 км пробігу) злити масло з всіх картерів , промити їх і залити нове
6 Зняти пломби, які обмежують подачу палива
Тема: Слюсарно - механічні методи ремонту деталей
Під час виконання ремонтних робіт можуть використовуватися такі методи ремонту деталей:
1. Відновлення пошкодженої різьби в отворах і на стержнях
2. Притирання
3. Паяння
4. Фрезерування
5. Розточування
6 Шліфування
7. Обточування
Відновлення різьби в отворах можна здійснювати двома методами:: а) заварювання отвору і нарізання різьби б) видалення пошкодженої різьби шляхом розточування отвору і нарізання різьби більшого діаметру або постановка різьбових вставок. Притирання застосовують при підгонці клапанів до своїх гнізд. Паяння виконують при ремонті деталей вузлів електрообладнання. Розточування застосовують при ремонті блок - картерів (розточування гільз циліндрів). Шліфування виконують при ремонті колінвалів,розподільних валів. Обточування застосовують при ремонті валів ( наварювання спрацьованих ділянок і обточування під номінальний розмір).
Тема: Ремонт деталей зварюванням і наплавленням
РЕМОНТ ДЕТАЛЕЙ ЗВАРЮВАННЯМ І НАПЛАВЛЕННЯМ
Зварювання та наплавлення є найбільш прогресивними і широко поширеними способами ремонту деталей. Вони займають близько 70% всього обсягу робіт з відновлення деталей. Зварюванням і наплавленням рекомендують ремонтувати деталі, виготовлені зі сталі, чавуну і кольорових металів, наприклад, блоки циліндрів, головки блоків циліндрів, колінчаті вали, картери, опорні катки, напрямні колеса, ланки гусениць, ковші, вали, осі. Ремонт деталей цими способами найбільш економічний, не вимагає складного обладнання та простий при виконанні технологічного процесу.
Зварюванням називається процес отримання нероз'ємних з'єднань за допомогою встановлення міжатомних зв'язків між зварюються частинами при їх місцевому або загальному нагріванні, пластичній деформації, або спільною дією того й іншого. Зварювання застосовують для з'єднання і закріплення відламаних і додаткових деталей (втулок, пластин, зубчастих вінців), закладення тріщин, розривів, пробоїн.
Наплавленням називається процес нанесення за допомогою зварювання шару металу на поверхню виробу. Наплавлення застосовують для відновлення зношених поверхонь деталей, а також підвищення зносостійкості поверхонь тертя.
В даний час при ремонті застосовуються такі основні види зварювання і наплавлення деталей: ручна дугове зварювання та наплавлення; автоматична дугова наплавлення під флюсом; автоматична вибродуговая наплавлення; дугова зварка і наплавлення в захисному газі.
Ручна дугова зварка і наплавлення. Ручна дугова зварка застосовується для заварки тріщин в блоках і головках циліндрів, картерах, для відновлення зварних швів в рамах і корпусах, заварки отворів, приварювання відламаних частин і додаткових деталей. Ручна дугова наплавлення застосовується для наплавлення зношених поверхонь отворів, валів, осей, ножів відвалів, щік дробарок, зірочок і т. д. Ручна дугова зварка і наплавлення здійснюється не плавляться вугільними, графітовими або вольфрамовими і плавкими металевими електродами. Зварювання та наплавлення плавляться мають обмежене застосування, використовуються тільки при зварюванні кольорових металів і наплавленні зношених поверхонь твердими сплавами. У ремонтному виробництві широко застосовується дугове зварювання та наплавлення плавкими металевими електродами.
Для підвищення продуктивності праці і зниження витрат електроенергії в ремонтному виробництві застосовуються високопродуктивні методи ручного дугового зварювання і наплавлення пучком електродів і трифазної дугою.
Зварювання та наплавлення пучком електродів застосовується тоді, коли потрібно наплавляти велику кількість металу. Сутність цього методу полягає в наступному. кілька звичайних покритих обмазкой електродів складають разом і скріплюють дротом. Контактні кінці зварюють і вставляють в електротримач. У цьому випадку виходить блукаюча дуга, так як горить вона поперемінно між окремими електродами і поверхнею деталі ( При зварюванні і наплавленні пучком, що складається з п'яти і більше електродів, частина стрижнів не включається в ланцюг зварювального струму, і вони плавляться за рахунок тепла зварювальної ванни. Зварювання та наплавлення пучком електродів може виконуватися на підвищеному струмі і збільшує продуктивність в 15-2 рази.
Застосування цього методу на 20-30% знижує витрату електроенергії за рахунок кращого використання тепла дуги. Крім того, значно зменшується місцевий нагрів деталі, внаслідок чого деталь менше піддається викривленню.
Зварювання та наплавлення трифазною дугою застосовується там, де потрібно наплавляти великий обсяг металу. Цим методом зварюють деталі з низьколегованих і легованих сталей великої і середньої товщини, а також ведуть наплавку твердих сплавів. Для зварювання і наплавлення трифазною дугою застосовують спеціальні електроди, що складаються з двох стержнів ( що мають загальне покриття, але ізольованих один від іншого. Зачищені кінці стрижнів з'єднують з електротримач особливої конструкції що дозволяє підводити струм до кожного стрижня окремо. При зварюванні (наплавленні) дві фази приєднують до електротримачі і третю - до виробу. У процесі зварювання (наплавлення) горять одночасно три дуги, дві - між кожним стрижнем і деталлю і одна - між двома стрижнями. Внаслідок виділення великої кількості тепла продуктивність зварювання (наплавлення) в порівнянні з однофазної збільшується в 2-3 рази. При діаметрі стрижнів електрода 6 мм і трифазної дузі можна наплавить до 8 кг металу на годину, при цьому за рахунок кращого використання тепла витрата електроенергії знижується на 20-30%. Живлення дуги проводиться від спеціальних трансформаторів типу 3-СТ та ТТС-400.
Процес зварювання і наплавлення металу складається з трьох етапів: підготовки деталей, зварювання (наплавлення), зачистки.
Підготовка деталей. Якщо поверхні, що підлягають зварюванню або наплавленні, забруднені або покриті іржею, в наплавленого металу будуть утворюватися шлакові включення, непровари, тріщини. Газові пори з'являються в наплавленого металу, якщо поверхня покрита маслом або вологою. Ці дефекти значно погіршують якість зварювання (наплавлення) або призводять до шлюбу. Тому всі деталі, що надходять на зварювання або наплавлення, ретельно очищають від бруду, іржі та інших забруднень.
Потім деталі знежирюють в гарячих розчинах, миють в гарячій воді і сушать. Наплавляєму або зварюєму поверхню бажано очистити до металевого блиску піскоструминної обробкою, сталевими щітками, абразивним кругом або різцем. якщо поверхні отворів або валів мають нерівномірний знос, що перевищує 05 мм на сторону, то такі поверхні проточують різцем. Це пов'язано з тим, що робоча поверхня деталі з невеликим зносом, якщо її попередньо механічно не оброблені, після наплавлення може виявитися в перехідному шарі, який має знижені механічні властивості. Зношені або пошкоджені різьблення (внутрішні та зовнішні) перед наплавленням необхідно зрізати для того, щоб в поглиблення старої різьби не потрапляв шлак, так як забруднення між гребенями різьби важко очистити. В іншому випадку при наплавленні можуть утворюватися шлакові включення або пори, що знижують якість наплавленого металу.
Наявні на наплавленої поверхні отвори, шпонкові пази і канавки закладають мідними графітовими вставками, які після наплавлення видаляють. Тріщини готують до зварювання шляхом оброблення крайок за допомогою шліфувального круга на гнучкому валу. Для цього може бути використано зубило. При товщині стінок деталі до 5 мм оброблення можна не робити, а обмежитися зачисткою, прилеглої до тріщини поверхні шириною 15-20 мм з кожного боку. При великій товщині стінок (до 12 мм) тріщини обробляють V-образно. Якщо товщина стінок деталі, що зварюється більше 12 мм, тріщину обробляють з двох сторін Х-образно. Кінці тріщин рекомендується засвердлюють, щоб при зварюванні вони не поширювалися далі.
. Для отримання доброякісного зварного з'єднання або заданої якості наплавленого шару при відновленні деталей першорядне значення мають правильний вибір типу і марки електрода, а також режимів зварювання (наплавлення). Вибір електрода залежить від характеру видаляється дефекту, марки матеріалу (сталь, чавун, алюміній), з якого виготовлена деталь, і вимог до наплавляти шару.
При заварці тріщин зазвичай застосовують зварювальні електроди. Вони поділяються на декілька типів від Е-34 до Е-145. Основною характеристикою кожного типу є тимчасовий опір розриву зварного з'єднання. Воно вказується в найменуванні типу електрода. Наприклад, електроди типу Е-42 дають зварне з'єднання, що має тимчасовий опір розриву, рівне 42 МПа. До кожного типу може ставитися кілька марок електродів. Наприклад, до типу Е-42 відносяться електроди марок ОЗЦ-10мм-5; до типу Е-42А - електроди ЦМ-8 УОНИ-13 /45П, ОЗС-3; до Е-46 -ОЗС-4 АНО-3 АНО-4; до типу Е-50А -електрод УОНИ-13/55 та ін.
Перераховані типи електродів застосовуються для зварювання мало-і середньовуглецевих сталей. Стрижні всіх електродів виготовлені з дроту Св-08 діаметром від 16 до 12 мм. Типи і марки електродів відрізняються один від одного покриттям (обмазкою). Електроди з крейдяний обмазкою, що складається з 70-80% меленої крейди і 20-30% рідкого скла, відносяться до типу Е-34. крейдяна обмазка є тільки стабілізуючою, т. е. сприяє стійкому горінню дуги. Решта типів і марки електродів мають якісну глину. Ця обмазка, крім стабілізуючих, містить захисні, шлакообразующие і газообразующие, а іноді раскисляющие і легуючі елементи. Умовне позначення типів складів покриттів: Руднокислі - Р, рутилове - Т, фтористо-кальциевое-Ф, органічне - О. Повний умовне позначення електрода по ГОСТу містить послідовно марку і тип електрода, його діаметр, вид складу покриття і номер ГОСТу. Наприклад, електрод ЦМ-7 діаметром 5 мм, що відноситься до типу Е-42 і має покриття Руднокислі типу, матиме позначення ЦМ-7-Е-42-5-Р-ГОСТ 9467-75.
Зварювання маловуглецевих (з вмістом вуглецю до 020%), а також низьколегованих сталей, наприклад, марок 15Х, 20ХНА, 20Х, ЗОХ не зустрічається труднощів.
Вуглецеві і леговані стали з середнім і високим вмістом вуглецю зварюються важче і схильні до утворення пір і тріщин, тому при зварюванні і наплавленні середньо- і високовуглецевих і легованих сталей потрібно попередній підігрів деталей. При змісті вуглецю від 02 до 03% деталі рекомендується підігрівати до температури 100-150 ° С, від 03 до 045% -до 150-250 ° С, від 045 до 080% - до 250-400 ° С. При відновленні зношених деталей дугового наплавленням вибір електродів залежить від марки стали наплавлюваної деталі, необхідної твердості і зносостійкості наплавленого шару.
Наплавлення зношених поверхонь деталей, виготовлених з маловуглецевої стали і не піддаються термічній або хи-мікотерміческой обробці, можна проводити зварювальними електродами.
При наплавленні деталей із середньовуглецевих і легованих сталей (наприклад, сталей марок 303545 ЗОХ, 40Х), загартованих, а також з маловуглецевої сталі, але з цементованої поверхнею, повинні застосовуватися спеціальні наплавочні електроди або тверді сплави.
ГОСТ 10051-75 встановлює ряд типів наплавочних електродів, що розрізняються за хімічним складом наплавленого шару. Позначення типу електрода розшифровується так: букви «ЕН» означають «електрод наплавочні», потім вказуються основні хімічні елементи, що входять до складу наплавленого шару, і їх середній вміст у відсотках. Позначення хімічних елементів загальноприйняте: У - вуглець, С - кремній, Г - марганець, Н - нікель, X - хром, Т -тітан і т. Д. Спочатку вказується вміст вуглецю. При цьому, якщо в позначенні типу електрода є буква «У», то вміст вуглецю дано в десятих частках відсотка, а якщо вона відсутня - в сотих частках.
Останні цифри вказують твердість шару ( HRC ). Наприклад, позначення типу електрода ЕН-14Г2Х-30 означає: електрод наплавочні, в наплавленном шарі міститься 014% вуглецю, 2% марганцю, 1% хрому, твердість шару - 30 HRC .
Вказівки на твердість наплавленого шару (НВ) містяться іноді і в позначеннях марки електрода, наприклад, електрод ОЗН-300 Т-590 і ін. Типами електродів відповідають певні марки електродів. Повне умовне позначення наплавочного електрода містить його марку, тип, діаметр і ГОСТ. Наприклад, електрод марки ОЗН-300 типу ЕН-15ГЗ-25 діаметром 5 мм буде мати позначення: ОЗН-300-ЕН-15ГЗ-2550 -ГОСТ 10051-75 і ГОСТ 9466-75.
Стрижні наплавлювальних електродів виготовляють як з вуглецевої, так і з легованої зварювального дроту. Легуючі елементи вводять в наплавлений шар як і & покриття і матеріалу стрижня, так і тільки з матеріалу покриття.
найбільш широке застосування для наплавлення деталей дорожніх машин знайшли електроди марок ОЗН-300 (тип ЕН-15ГЗ-25), ОЗН-400 (тип ЕН-20Г4-40); для наплавлення деталей з високомарганцовістой стали ПЗ - електроди ОМГ-Н (тип ЕН-70ХН-25); для наплавлення швидкозношуваних деталей, які працюють в умовах абразивного зношування, - електроди марок Т-590 Т-620 ЦС-1 ЦС-2 та ін. В останні роки для отримання наплавлених шарів високої твердості застосовують трубчасті наплавочні електроди ЕТН-1 ЕТН-2 етно-3 ЕТН-4. В якості наповнювача використовують тверді сплави, найчастіше сормайт, феросплави, карбід вольфраму. Для холодного зварювання (наплавлення) деталей з чавуну застосовують електроди марок ОМЧ-1 МСТ, МНЧ-1 ЦНІІВТ, ЦЧ-ЗА, Анч-1 і ін. Для зварювання чистого алюмінію застосовують електроди марки ОЗА-1 а для зварювання сплавів алюмінію - ОЗА-2.
Основними параметрами режимів зварювання і наплавлення є: рід струму і полярність, діаметр електродного дроту, величина зварювального струму і напруга дуги. Дугове зварювання та наплавлення металу може проводитися постійним або змінним струмом. На постійному струмі дуга горить більш стійко. Зварювання (наплавлення) на постійному струмі можна вести на прямій і зворотній полярності. При зварюванні (наплавленні) на прямій полярності до деталі приєднують «плюс» джерела струму, а до електроду- «мінус». На зворотній полярності навпаки. Тепло електричної дуги розподіляється (приблизно) наступним чином: позитивний полюс - 43%, негативний полюс - 36% і електрична дуга - 21%. Це необхідно враховувати при виборі полярності. Зазвичай до деталі підключають позитивний полюс в тих випадках, коли вона має велику масу і вимагає значної кількості тепла для нагріву. Деталі, що мають невелику масу або товщину (<3 мм), сваривают при обратной полярности.
Величина струму встановлюється в залежності від діаметра електрода. Для зварювання стали в нижньому положенні необхідну величину струму можна вибрати за даними табл. 5. При зварюванні вертикальних і стельових швів величина зварювального струму приймається на 10-20% менше, ніж при зварюванні в нижньому положенні.
Діаметр електрода при наплавленні підбирають в залежності від товщини наплавного шару. Величину струму приймають в залежності від обраного діаметра електрода приблизно таку ж, як і при зварюванні, ближче до нижнього значення. Наплавлення слід вести короткою дугою з перекриттям сусідніх валиків на 30-50%, причому електрод повинен бути нахилений під кутом 15-20 ° до вертикалі в напрямку руху. Наплавлення рекомендується проводити, поєднуючи переміщення електрода в напрямку наплавлення з поперечним коливанням його таким чином, щоб ширина валика дорівнювала приблизно 25 діаметруелектрода. Товщина наплавленого шару виходить рівною приблизно 07 йв. Сталий горіння дуги при зварюванні (наплавленні) металевим електродом відбувається при напрузі 18-28 В, а вугільним або графітовим - при 30- 35 В.
Зачистка зварних швів і наплавлених поверхонь проводиться металевими щітками з метою видалення з їх поверхонь шлаку і металевої бризки.
Обладнання для зварювання і наплавлення. Як джерела живлення електроенергією при веденні дугового зварювання й наплавлення застосовують зварювальні трансформатори змінного струму, перетворювачі і випрямлячі постійного струму. Найбільшого поширення набули зварювальні трансформатори типів ТС-120 МС-300 МС-500 ТСК-300 ТСК-500 (число позначає величину номінального зварювального струму).
Зварювальний перетворювач являє собою агрегат, що складається з зварювального генератора постійного струму і двигуна, що обертає генератор. Найбільшого поширення мають перетворювачі типів ПСО-120 ПСО-300 ПСО-500 ПСО-800.
Для ручного дугового зварювання (наплавлення) останнім часом застосовують випрямлячі ВСС-120-4 ВСС-300-3 (селенові), ВКС-120 ВКС-300 ВКС-500 (кремнієві).
Автоматичне дугове наплавлення під флюсом - це дугова наплавлення, при якій дуга горить під шаром зварювального флюсу, а подача плавиться електрода і переміщення дуги вздовж наплавлюваної поверхні деталі
Автоматичне дугове наплавлення під шаром флюсу вперше створена в інституті електрозварювання імені Є. О. Патона. Вона застосовується для відновлення поверхні деталей діаметром понад 50 мм і плоских деталей з величиною зносу від 1 до 15 мм. Деталі з великою величиною зносу наплавляют в кілька шарів. Для наплавлення використовують переобладнані токарно-вин-торезние верстати з частотою обертання шпинделя від 025 до 4 об /хв, на супорті яких встановлені наплавочні головки або установки. Джерелом струму є зварювальні перетворювачі або подовжувачі.
Сутність наплавлення під шаром флюсу (рис. 48) полягає в тому, що в зону горіння дуги 6 автоматично подається сипучий флюс в гранулах розміром від 1 до 4 мм і електродний дріт 5. Під дією високих температур частина флюсу плавиться, утворюючи навколо дуги еластичну оболонку 3 з рідкого флюсу, яка захищає розплавлений метал від окислення, поглинання азоту та інших елементів. Внаслідок цього наплавлений метал 8 набуває високу пластичність, так як в ньому виявляється приблизно в 20 разів менше кисню і в 3 рази менше азоту, ніж при ручному наплавленні. Втрати металу на розбризкування, угар, недогарки не перевищують при цьому 2-4%, в той час як при ручному наплавленні вони в 10 разів більше.
Наплавлення ведеться постійним струмом напругою 25-40 В при прямій полярності. Для запобігання стікання рідкого металу і флюсу при наплавленні круглих деталей електрод зміщують з зеніту в сторону, протилежну напрямку обертання, на величину е
Переваги автоматичної наплавки перед ручної: висока продуктивність (більше в 5-10 разів), менша вартість (в 5-8 разів), висока якість наплавленого шару.
Для поліпшення якості наплавленого металу, збереження початкової твердості і структури загартованих деталей, зменшення викривлення наплавлюваного деталі і підвищення зносостійкості Ташкентським інститутом залізничного транспорту запропонований прогресивний спосіб наплавлення деталей під шаром флюсу з примусовим охолодженням водою і розроблена установка
На поздовжньому супорті токарно-гвинторізного верстата змонтована автоматична наплавочная головка з бункером для флюсу, з флюсоудержівающім пристроєм, підйомником флюсо-утримуючого пристрою і мундштуком наплавочной головки. На поперечному супорті змонтовані розподільник охолодження, душовий пристрій і різець. У центрах верстата закріплюється наплавляюча деталь. при наплавленні одночасно проводиться охолодження наплавного шару металу і видалення різцем шлакової кірки.
Собівартість відновлення деталей цим способом знижується за рахунок того, що не потрібно робити роботу по усуненню викривлення і термообробки. При автоматичної дугового наплавленні під флюсом твердість і зносостійкість наплавленого шару в основному залежить від застосовуваної електродного дроту і марки флюсу.
Електродний дріт. Для наплавлення маловуглецевих і низьколегованих сталей застосовують дріт з маловуглецевих (Св-08 Св-08А, Св-15), марганцевистих (Св-08г, Св-08ГА, Св-15Г) і кремніймарганцевистих (Св-ЮГС) сталей. Для наплавлення вуглецевих і високовуглецевих сталей застосовують дріт Нп-65Г, Нп-ЗОХГСА і Нп-ЗХ13.
Флюси. Залежно від марки стали, яка піддається наплавленні, марки електродного дроту, необхідної твердості і зносостійкості наплавленого шару флюси діляться на плавлені, керамічні та флюси-суміші. Плавлені флюси містять стабілізуючі і шлакообразующие елементи, але в них не входять легуючі добавки, тому вони не можуть надавати шару, наплавленого малоуглеродистой, марганцовистой і кремнемарганцові-стій дротами, високу твердість і зносостійкість. З плавлених флюсів найбільшого поширення набули флюси марок АН-348А, АН-60 ОСЦ-45 АН-20 АН-28. керамічні флюси марок АНК-18 АНК-19 ЖСН-1 і інші, крім стабілізуючих і шлакообразующих елементів, містять легуючі добавки, головним чином у вигляді феросплавів (ферохрому, Ферроті-тана і ін.), що дають шару, наплавленого малоуглеродистой дротом, високу твердість без термообробки і зносостійкість.
Флюси-суміші (АНЛ-1) являють собою механічну суміш, що складається з 93% плавленого флюсу марки АН-10 і 7% лігатури алюмінію з залізом (15% заліза + 85% алюмінію). Твердість покриття деталей, наплавлених цим флюсом, досягає 380-400 НВ.
Іноді під флюси-суміші додають магнітний залізний порошок. У процесі наплавлення деталі під дією магнітного поля залізний порошок притягається до зони наплавлення, що сприяє підвищенню продуктивності процесу.
Режим наплавлення має суттєвий вплив на стабільність процесу, товщину наплавленого металу і його фізико-механічні властивості.
Технологія наплавлення. Для підготовки наплавочной установки (до наплавленні циліндричних деталей виконують такі операції. У центрах верстата закріплюють деталь, ставлять касету, заправлену електродної дротом, на вісь зварювальної головки і простягають дріт через ролики в мундштук.
Встановлюють необхідну швидкість подачі електродного дроту за допомогою змінних шестерень, що подає. Коректором нахиляють мундштук на необхідний кут (приблизно 6-8 ° в бік обертання деталі). Обертаючи рукоятку механізму підйому, підводять зварювальну головку до наплавлюваного деталі. Встановлюють зміщення і виліт електрода.
Наплавлення ведуть в такому порядку: встановлюють реостатом генератора розраховану величину зварювального струму; пускають флюс з бункера 5 по патрубку 11 відкривши шиберні засувки 8; пускають зварювальний перетворювач, натискають кнопку «Пуск», розташовану на пульті управління 6. Наплавлення проводиться по гвинтовий лінії. Наплавляемие валики накладають так, щоб кожний наступний валик приблизно на 1/3 перекривав попередній. Під час наплавлення молотком видаляють шлакову кірку, стежать за показаннями контрольних приладів і рівномірністю подачі флюсу в зону наплавлення. Перший і останній кільцеві валики наплавляют при вимкненому поздовжньої подачі наплавочной головки. Припиняють процес наплавлення шляхом натискання кнопок «Вниз - стоп 1» і «Вгору - стоп 2 », після чого закривають шиберні засувки і вимикають зварювальний перетворювач.
Устаткування. На підприємствах по ремонту дорожніх машин широке поширення для наплавлення деталей отримали: автоматичні апарати типів А-384МК, А-409 А-508М, А-874Н, АБС, А-929 А-1030 ОКС, А-1031Б в поєднанні зі зварювальними перетворювачами (ПС-300 ПСУ-300 ПСГ-500 ПСУ-500) і випрямлячами (ВСУ-300 ВСУ-500 ВСС-300 ІПП-300 ВДГ-1001 ВДУ-1001 та ін.), а також токарно-гвинторізні верстати типів 1А62 1А64 1Д62Г, 1К62 1А616 1А665 1А680 та ін.
Автоматичне дугове наплавлення зношених деталей трубчастими електродами, порошковим дротом і порошкової стрічкою.
Все більше застосування в ремонтному виробництві знаходить автоматична дугова наплавлення зношених деталей трубчастими електродами марок ЧЕРЕЗ 1 З-2 ТЗ-3 етно-1 етно-2 етно-3 етно-4 етно-5 порошковим дротом марок ПП-АН-124 ПП-АН-105 ПП-АН-170 і порошковими стрічками марок ПЛ-У40Х38ГЗТЮ, ПЛ-628 ПЛ-634. Трубчасті електроди, порошкові дроти і стрічки застосовують для наплавлення зубів екскаваторів, щік камнедробілок, козирків ковшів, ножів бульдозерів і скреперів, опорних ковзанок і гусеничних ланок екскаваторів.
Трубчастий електрод являє собою трубку, згорнуту з сталевої стрічки товщиною 068-080 мм і наповнену порошкоподібної сумішшю з сталініта, феромарганцю або інших матеріалів. Суміш захищена від впливу повітря як самої трубкою, так і її зовнішньої обмазкой. Наплавлений шар має велику зносостійкість і має твердість HRC 55-58.
Порошковий дріт являє собою металеву оболонку, щільно наповнену порошкоподібними легирующими елементами-шихтою. Шихту застосовують різну. Найпростішою і найбільш дешевою є дрібна чавунна стружка з додаванням до 20% доменного феромарганцю. Наплавлений шар має гарну зносостійкість і має твердість HRC 40-60 в залежності від застосованої шихти.
Порошкові стрічки (рис. 51 а) складаються з двох стрічок (виготовлених зі смугової сталі 08 товщиною 06 мм і шириною 50 мм) і порошкової легирующей суміші, розташованої в осередках одній зі стрічок. Як легирующей суміші застосовують різні компоненти, що складаються з феросплавів. Фізико-механічні властивості наплавленого металу визначаються складом легуючих сумішей і режимами наплавлення. Наплавлений шар має гарну зносостійкість і має твердість HRC 48-54.
Розроблено установку, в якій поєднані процеси виготовлення порошкової стрічки і наплавлення (рис. 51 б). Процес виготовлення порошкової стрічки зводиться до пропускання стрічок між формують роликами, які надають стрічок П-образну і гофровану ячейкообразную форму, наповненню осередку нижньої стрічки легирующей сумішшю і обтисненню стрічки роликами. При наплавленні дуга горить під шаром флюсу.
Автоматична вибродуговая наплавка - це дугова наплавлення плавиться, який вібрує, внаслідок чого дугові розряди чергуються з короткими замиканнями. Подача і переміщення електрода уздовж наплавлюваного поверхні деталі механізовані.
Цей вид наплавлення простий, не вимагає дефіцитних матеріалів, дозволяє наплавляти на деталі діаметром від 8 мм і вище шар металу товщиною 05-35 мм. При цьому деталь не відчуває деформацій, а твердість шару може бути доведена до HRC 50-58 без подальшої термічної обробки. Вибродуговая наплавлення може проводитися в рідкому середовищі, середовищі захисних газів (аргон, вуглекислий газ і ін.) І під флюсом. більша поширення набула наплавка в рідкому середовищі.
наплавляти деталь закріплюють у центрах або трикулачні патроні токарного верстата. На супорті верстата встановлюють ізольовано від маси вибродуговой головку. До деталі і голівці підводять струм низької напруги. До наплавлюваного поверхні обертової деталі роликами 5 з касети 6 автоматично через вібруючий мундштук подається електродний дріт, яка весь час вібрує. Стикаючись з поверхнею деталі, дріт оплавляется під дією імпульсних електричних розрядів і розплавлений метал електрода приварюється до поверхні. Для охолодження і загартування наплавленого шару до нього через спеціальний канал в мундштуці насосом з системи охолодження подається рідина, що складається з 4-6% -ного розчину кальцинованої соди у воді. Вібрація мундштука здійснюється за допомогою електромагнітного вібратора.
Діаметр електродного дроту вибирають в залежності від товщини наплавляемого шару і сили струму. Чим товщі наплавляється шар, тим беруть більший діаметр дроту.
Наприклад, для наплавлення шару завтовшки до 1 мм застосовують дріт діаметром 1-16 мм, для шару 2 мм - діаметром до 25 мм і для шару товщиною більше 2 мм - діаметром - 2-3 мм.
Режими наплавлення. Наплавлення ведуть постійним струмом при зворотній полярності. Сила струму визначається діаметром електродного дроту і швидкістю її подачі при наплавленні. Для дроту діаметром 13-18 мм рекомендується сила струму 100200 А. На практиці силу струму вибирають за величиною його щільності. Наприклад, при діаметрі електродного дроту до 2 мм щільність струму беруть 6075 А /мм2 для дроту більшого діаметра - 50-70 А /мм 2. Найбільш раціональне напруга при наплавленні шару завтовшки до 1 мм 12-15 В, при більшій товщині 15-28 В.
Витрата охолоджуючої рідини становить для середньо- і високовуглецевих, а також легованих сталей 03-05 л /хв, для малоуглеродістих- 1 л /хв. При наплавленні тонких деталей з низьковуглецевих сталей зазвичай витрачається 3-5 л /хв.
Наплавлення ведеться по гвинтовий лінії. Після, наплавлення поверхню обробляють шліфуванням, спочатку грубим (обдирні), а потім чистовим під необхідний розмір. При наплавленні дротом Св-08 поверхня легко обробляється різцями.
Устаткування. Широке поширення отримали автоматичні наплавочні головки типів УАНЖ-5 УАНЖ-6 ГМВК-2 ВГ-4 ВГ-8М і інші в поєднанні зі зварювальними перетворювачами (ПСО-300 ПСУ-300 ПСУ-500) і випрямлячами (ВС-400 ІПП-500 вагга-15-600), а також токарно-гвинторізні верстати типів 1А62 1А64 1Д63А і ін..
Для подачі охолоджуючої рідини використовують систему охолодження токарного верстата або встановлюють насос з подачею 6-10 л /хв і бачок місткістю до 100 м. Токарні верстати переобладнують для того, щоб отримати частоту обертання деталі в межах від 05 до 20 об /хв.
Дугове зварювання та наплавлення в середовищі захисних газів. У зону горіння дуги під невеликим тиском подається газ, який витісняє повітря з цієї зони і захищає розплавлений метал від впливу кисню та азоту повітря. Зварювання і наплавлення в середовищі захисних газів можна вести як плавиться (рис. 53 а), так і не плавиться (рис. 53 б) електродом (зазвичай вольфрамовим), а присадний матеріал вводиться в зону дуги окремо.
Плавляться електроди широко застосовуються при зварюванні (наплавленні) деталей з алюмінію і його сплавів.
Як захисні газів застосовують аргон, гелій (для зварювання та наплавлення всіх металів), азот (для зварювання і наплавлення міді і її сплавів), вуглекислий газ (для зварювання та наплавлення стали і чавуну).
Напівавтоматична наплавка в захисній средеуглекіслого газу. Наплавлення ведуть постійним струмом на зворотній полярності плавиться. Подача електродного дроту механізована.
Газоелектричного пальник переміщають при наплавленні вручну, застосовуючи ті ж прийоми, що і при ручного дугового наплавленні металевим електродом. Робоча напруга при наплавленні тонколистових конструкцій і деталей невеликого діаметра знаходиться в межах 17-22 В при діаметрі дроту 05-12 мм, і в межах 28-32 В при діаметрі дроту 20-25 мм для більш товстих листових конструкцій і деталей більшого діаметра. Найбільшого поширення при зварюванні отримали електродні дроту марок Св-08ГС, Св-10ГС, Св-10ХГ2С, Св-ЮХГСА, а для наплавлення - Нп-ЗОХГСА.
Сила зварювального струму залежить від діаметра і швидкості подачі електродного дроту. Для найбільш поширених діаметрів дроту 08-2 мм при зварюванні стикових з'єднань товщиною до 3 мм сила струму знаходиться в межах 70-180 А, а швидкість подачі дроту 170-260 м /ч. меншому значенню діаметра дроту відповідають менші значення сили струму і швидкості подачі. При наплавленні режим дещо інший, ніж при зварюванні. Так, при діаметрі наплавлюваного деталі від 10 до 40 мм і діаметрі дроту 08-12 мм сила струму знаходиться в межах 75-95 А, а швидкість подачі дроту 175-250 м /ч. Перші значення відповідають меншим діаметрами дроту і деталі, а останні - великим. Робочий тиск вуглекислого газу в пальнику знаходиться в межах 003-015 МПа (03-15 кгс /см2).
Установка для наплавлення в середовищі вуглекислого газу складається з газової апаратури, полуавтомата для наплавлення і джерела живлення струмом.
Газова апаратура складається з балона з газом, осушувача, підігрівача, газового редуктора, витратоміра, шлангів та ін. Напівавтомати для наплавлення застосовують наступних марок: А-547Р, А-547У, А-537 А-929 і ін..
Джерелами струму можуть бути зварювальні перетворювачі ПСГ-900 і ПСГ-500 а також випрямлячі ВСС-300 ТСК-300 і ін. Напівавтоматичне наплавку (зварювання) в середовищі вуглекислого газу застосовують для з'єднання деталей кабін, оперення, усунення тріщин і отворів на сталевих деталях, заварки тріщин в картерах коробок передач і інших деталях із сірого чавуну.
Напівавтоматична аргонодуговая наплавка. Наплавлення ведуть постійним струмом на прямій полярності або змінним струмом так само, як і при наплавленні в середовищі вуглекислого газу.
Аргонодуговая наплавка не плавиться є одним з кращих способів наплавлення алюмінію і його сплавів. Як не плавиться переважно застосовують вольфрамові стрижні діаметром від 08 до 6 мм. Дріт для наплавлення (зварювання) алюмінію і його сплавів застосовується діаметром 08-6 мм з чистого алюмінію (Св-АВ00 Св-А1), з алюмінієво-магнієвого сплаву (Св-Амг-3 Амг-5 та ін.) , з алю-мініевих-марганцевого сплаву (Св-АМц) і з алюмінієво-крем-ніевого сплаву (Св-АК-3 Св-АК-5 і ін.). Дуга горить між вольфрамовим електродом і деталлю. Подача дроту для наплавлення (зварювання) в зону горіння дуги механізована.
Сила струму приймається в Залежно від діаметра вольфрамового електрода і товщини деталі, що зварюється. При товщині зварюваної деталі від 1 до 8 мм силу струму можна прийняти рівною 40-50 діаметрам електрода, а при товщині від 6 до 12 мм - 50- 60 діаметрам. Робоча напруга становить 22-26 В.
Установка для наплавлення (зварювання) в середовищі аргону складається з зварювального перетворювача постійного струму (ПСУ-300 ПСУ-500), реостата, газоелектричним пальника (АР-9 АР-10 ГРАД-200 ГРАД-400 і ін.), механізму подачі дроту, редуктора з витратоміром газу і балона з газом. Пальник для аргонодугового наплавлення (зварювання) неплавким вольфрамовим електродом складається з головки (рис. 54) і корпусу. До корпусу приєднується кабель, в якому розміщені шланг для аргону і токопровод. Вольфрамовий електрод, розміщений в голівці пальника, кріпиться за допомогою цангового втулки і закривається ковпаком 5. Потік аргону формується навколо електрода і зони зварювання (наплавлення) соплом. Зварювальний дріт подається в зону горіння дуги в гнучкий шланг, який кріпиться до корпусу пальника. Витрата аргону становить від 2 до 12 дм3 /хв.
Переваги зварювання і наплавлення в захисних газах: вартість наплавлення (зварювання) на 20% нижче, ніж наплавлення під шаром флюсу; майже повний захист металу шва від навколишнього повітря; хороша видимість відкритої дуги забезпечує точність накладення шва; менше витрата електродів, ніж при ручному зварюванні (наплавленні). Останнім часом при ремонті деталей дорожніх машин застосовується плазмова, лазерна і високочастотне зварювання і наплавка. Плазмова наплавка заснована на тому, що тугоплавкі жароміцні і зносостійкі покриття різної товщини наносяться на деталь за допомогою низькотемпературної плазми. Лазерне зварювання - це зварювання плавленням, при якій для місцевого розплавлення з'єднуються частин деталей використовується енергія світлового променя, одержаного від оптичного квантового генератора. Високочастотну зварювання або наплавлення ведуть в індукторі струмами високої частоти на спеціальних високочастотних установках. При зварюванні і наплавленні можуть виникати такі дефекти: підрізи, прожогом, непровари, пористість, тріщини і шлакові включення.
Контроль зварювання і наплавлення здійснюється зовнішнім оглядом, виміром швів, механічними випробуваннями, хімічним аналізом, рентгенівським просвічуванням, а також ультразвукової, люмінесцентної, електромагнітної дефектоскопії та ін. Виявлені дефекти підлягають виправленню.
Тема: Напилення металу
Газотермі́чне напи́лення (англ. Thermal Spraying) - одержання покриття із нагрітих та прискорених частинок напилюваного матеріалу із застосуванням високотемпературного газового струменя, в результаті зіткнення яких з основою або напиленим матеріалом відбувається їх з'єднання за рахунок зварювання, адгезії та механічного зчеплення[1].
Винахідником даного методу нанесення покриттів вважається швейцарський винахідник доктор Макс Ульріх Шооп (нім. Max Ulrich Schoop, 1870-1956). Розпилюючи свинець за допомогою стаціонарної тигельної установки він отримував покриття на різних матеріалах. Варто відзначити, що на відміну від сучасних методів, де для переносу використовуються в основному гази, перша установка Шоопа переносила рідкий свинець за допомогою водяної пари. На основі його технології в Цюриху в 1909 році був відкритий завод по металізації. У цьому ж році У. Шооп зареєстрував перший «метод отримання щільних металевих шарів» (патент DE № 258505[2] і патент СН № 49278[3]). Він описує спосіб перенесення «дрібнодисперсного металу під тиском на підкладку» для отримання шару з міді, срібла, олова, цинку, алюмінію та інших сплавів практично на будь-яких підкладках, наприклад, з металу, дерева, скла, паперу, текстильної тканини, глини або гіпсу. У 1913 році Ульріх Шооп удосконалив і запатентував[4] конструкцію газополуменевого розпилювача, де матеріал для розпилення подавався в полум'я газового пальника у вигляді дроту. У 1918 році він із співробітниками розробив конструкцію електродугового розпилювача, що дозволяв ефективно наносити покриття з різних металів. Основні матеріали - цинк та алюміній як покриття використовувались ним для захисту від корозії переносного моста на каналі Дортмунд-Емс, воріт шлюзів тощо. Завдяки значному внеску в початковий розвиток технологій, методи нанесення газотермічних покриттів шляхом розпилення стали назвали шоопуванням, по імені винахідника технології. У 1921 році Ульріх Шооп запатентував технологію металопорошкового газополуменевого напилення.
В Україні розробленням та запровадженням технологій газотермічного напилення займається Інститут електрозварювання імені Євгена Патона НАН України (вчені Борисов Б.С., Коржик В.М.)
Під загальною назвою «газотермічне напилювання» (ГТН) об'єднують такі методи[5]:
- газополуменеве напилювання - газотермічне напилювання, під час якого використовується струмінь продуктів згорання суміші газів, які спалюються за допомогою пальника[1];
- високошвидкісне (надзвукове) газополуменеве напилювання (HVOF - англ. High velocity oxygen fuel - високошвидкісний киснево-паливний метод) - одна з технологій газотермічного напилювання захисних покриттів, при якій порошковий матеріал наноситься на підкладку на високій (зазвичай до 3 швидкостей звуку);
- детонаційне напилювання - газотермічне напилювання, під час якого використовується струмінь продуктів детонації[1];
- плазмове напилювання - газотермічне напилювання, під час якого використовується струмінь електронів, іонів та нейтральних атомів газу, з якого утворюється плазма[1], різновидами якого можна вважати:
- плазмово-дугове напилювання - плазмове напилювання, під час якого плазмовий струмінь створюється за допомогою електричної дуги[1];
- надзвукове плазмове напилювання - плазмово-дугове напилювання, під час якого плазмовий струмінь витікає з надзвуковою швидкістю[1];
- напилювання з оплавленням - метод газотермічного напилювання, що дозволяє отримати щільні зносостійкі корозійностійкі покриття з високою адгезією;
- електродугове напилювання - газотермічне напилювання, під час якого нагрівання та плавлення напилюваного металу у вигляді дроту, стрижня або стрічки здійснюється електричною дугою, а диспергування струменем стисненого газу, звичайно повітря[1];
- активована електродугова металізація - метод електродугового напилювання, що базується на плавленні дротів електричною дугою і розпилюванні розплавленого металу високошвидкісним струменем продуктів згорання пропано-повітряної суміші.
Зазвичай ГТН застосовують для створення на поверхні деталей та обладнання функціональних покриттів - зносостійких, корозійно-стійких, антифрикційних, протизадирних, теплостійких, термобар'єрних, електроізоляційних, електропровідних тощо. Матеріалами для напилення служать порошки, шнури і дроти з металів, металокераміки і кераміки.
Деякі з методів газотермічного напилення є альтернативою методам гальванічної, хіміко-термічної обробки металів, плакування, інші - методам фарбування чи нанесенням полімерних покриттів. Поширеним застосуванням ГТН є ремонт і відновлення деталей та обладнання. За допомогою напилення можна відновити від десятків мікрон до декількох міліметрів за товщиною на поверхні металу.
Особливостями технології є:
- можливість нанесення покриттів з різних матеріалів (практично будь-який плавкий матеріал, що можна подати у вигляді порошку або дроту);
- відсутність перемішування матеріалу основи і матеріалу покриття;
- незначне (не більше 150 °С) нагрівання поверхні при нанесенні покриття;
- можливість нанесення декількох шарів, кожен з яких несе свою функцію.
- Тема; Ремонт деталей тиском
Відновлення деталей за допомогою пластичних деформацій засноване на їх здатності змінювати свою геометричну форму і розміри за рахунок перерозподілу металу без руйнування під дією зовнішніх сил.
Ремонт деталей пластичною деформацією - один з найбільш поширених методів ремонту деталей, заснований на пластичної деформації зношених деталей з наступною механічною обробкою. Метод використовують для виправлення вм'ятин, погнутости, скручування, зміни посадкових розмірів зношених місць деталей (збільшення діаметра зношених шийок осей, валів, зменшення діаметра зношених поверхонь втулок), підвищення міцності деталей (дробоструминний наклеп) і зниження шорсткості механічної обробки (накатка роликами шийок валів замість їх шліфування). Цей спосіб застосовується також для відновлення первісних властивостей деталей, зміцнення їх робочих поверхонь і в якості заключної чистової обробки. Для полегшення пластичного деформування деталь попередньо підігрівають, що різко підвищує пластичність металу. Так, при нагріванні деталей до 900 ° С прикладену навантаження можна знизити до 0,5 ... 0,6 МПа.
Деталі відновлюють як в холодному, так і в гарячому стані. У холодному стані зазвичай відновлюють деталі з низьковуглецевих сталей, кольорових металів і сплавів, а в гарячому - з середньо- і високовуглецевих сталей з температурою нагріву 0,7 ... 0,9 температури плавлення. Після відновлення тиском відповідальні деталі піддають термічній обробці.
При відновленні деталей пластичною деформацією (тиском) використовують пластичні властивості металу, здатність за деяких умов деформуватися під навантаженнями, не втрачаючи цілісності деталі.
Ремонт зношених деталей за допомогою пластичних деформацій вимагає спеціальних пристосувань і штампів, тому є економічно виправданим тільки в тому випадку, коли ремонтується багато однотипних деталей.
Розрізняють такі види обробки пластичним деформуванням: осадку, роздачу, обтиснення, вдавлювання, витяжку, правку, накочення.
Правка застосовується при спотворенні форми деталей, наприклад при вигині і скручуванні валів, осей, шатунів, рам; вм'ятинах і перекоси тонкостінних деталей. Залежно від ступеня деформації і розмірів деталі правлять з нагріванням або без нього. Інструментом при правці можуть служити молотки (сталевий, мідний, дерев'яний), кувалди, спеціальні ключі, скоби, преси, домкрати та ін.
При правці без нагріву у сталевих деталей залишаються значні внутрішні напруження. В результаті цього після правки вони поступово приймають первісну форму. Для зняття внутрішніх напружень після холодної правки деталь необхідно стабілізувати, т. Е. Витримати при температурі 400 ... 450 ° С близько 1ч або при температурі 250 ... 300 ° С протягом кількох годин.
Великі й сильно деформовані деталі правлять в нагрітому стані, оскільки холодна правка не завжди дає стійкий результат, так як в металі в результаті наклепу можуть виникнути внутрішні напруження, що накладаються на залишкові напруги, що зберігаються в деталях. Ці процеси не виникають при гарячої правці, коли місця деформації нагрівають до 600 ... 900 ° С. Наприклад, для правки металоконструкцій нагрівають деформовані елементи за допомогою газових пальників і паяльних ламп до 900 ° С в місцях найбільших вигинів з опуклого боку. Виниклі при нагріванні напруги розтягнення викликають випрямлення деталі.
Осадка застосовується для збільшення зовнішнього діаметра суцільних деталей або для зменшення внутрішнього діаметра порожнистих. При осаді діаметр деталі збільшується за рахунок зменшення її довжини. Цим способом відновлюють різні втулки при зносі по зовнішньому або внутрішньому діаметру, цапфи валів, осі, клапани двигунів внутрішнього згоряння, зубчасті колеса та інші деталі, що мають поверхневий знос не більше 1% їх діаметру. Осадкою збільшують діаметр деталей типу пальців і втулок з кольорових металів за рахунок деякого зменшення їх довжини.
Цим способом можна зменшити довжину деталей до 15%, однак відповідальні деталі не зменшують більше ніж на 8%. Пристосування для опади складається з верхньої та нижньої підставок і циліндричної оправки, діаметр якої повинен бути на 0,2 мм менше остаточного діаметра отвору. Після опади під пресом отвір втулки розгортають до необхідного розміру. Невеликі по ширині циліндричні зубчасті колеса відновлюють в нагрітому стані за допомогою спеціальних штампів, які дозволяють отримати невелике потовщення зубів і зменшення отвору маточини.
Отвір маточини після осідання розточують, а потім обточують зовнішні поверхні і нарізають зуби колеса. Якщо необхідно, проводять термічну обробку зубів на режимах, передбачених для нових зубчастих коліс. Обтиснення проводять при необхідності зменшити, внутрішній діаметр порожнистих деталей за рахунок зміни зовнішнього діаметра. Цим способом відновлюють втулки з кольорових металів, вушка різних важелів при зносі гладких або шліцьових отворів, корпуси гідронасосів та ін. При обтисненні зношену втулку проштовхують за допомогою пуансона через отвір матриці, розмір якої, регульований вкладишем, дорівнює зовнішньому діаметру обтиснень втулки. Після обтиску зовнішній діаметр збільшують, наприклад, за допомогою електролітичного нарощування шару металу, а внутрішній - розгортають до необхідного розміру.
Обтисненням зменшують внутрішні розміри деталей типу втулок, виготовлених з кольорових металів. Втулку проштовхують пуансоном через встановлену в підставці матрицю. Вхідний отвір матриці звужується під кутом 7 ... 8 °, далі йде калібрує частина, яка закінчується вхідним отвором, що розширюється кутом 18 ... 20 °. Після обтиску зовнішню поверхню втулок оміднюють і проточують, а внутрішню розгортають.
Витяжка застосовується для збільшення довжини деталі за рахунок місцевого (на невеликій ділянці) звуження її поперечного перерізу. Цей спосіб використовують при ремонті тяг, штанг та ін.
Роздача застосовується для збільшення зовнішнього діаметра за рахунок збільшення внутрішнього діаметра порожнистих деталей. Цим способом відновлюють бронзові втулки шестерних насосів гідросистем, труби рульової колонки та ін. Роздачу частіше проводять в холодному стані, загартовані деталі попередньо піддають відпустці або відпалу. Найчастіше цей спосіб застосовують при відновленні поршневих пальців двигунів внутрішнього згоряння. Зношений палець встановлюють в спеціальну матрицю і роздають за допомогою пуансона на пресі.
Втискуванням відновлюють тарілки клапанів, шліци, шестірні при зносі за профілем зуба і ін. (Рис. 59). Ролики 2 і 3 виготовляють зі спеціальних твердих сплавів або інструментальної сталі і піддають термообробці. Ролик 2, вдавлюючись, перерозподіляє метал, а ролики 3 формують профіль і розміри шліців. Установка має дві або три подібні головки, т. Е. Одночасно обробляються два або три шліца під кутами відповідно 180 і 120 °. Завдяки такій конструкції вал розвантажується від изгибающих сил. Перед головками закріплені індуктори високочастотної установки для розігріву шліців, ззаду роликів - пристрій для їх охолодження. Накочуванням збільшують розміри термічно не оброблені циліндричних поверхонь, на які встановлюють деталі за допомогою нерухомих посадок. Такі деталі, закріплені в центрах токарного верстата, обкатують роликом з хромонікелевої сталі, які мають на поверхні насічку.
При накоченні діаметр поверхні збільшується за рахунок підняття гребінців металу. Отриману поверхню шліфують або накочують гладким роликом до отримання необхідного розміру. Накатка може бути застосована для відновлення вкладишів, залитих свинцювата бронзою, а також для відновлення зношених поверхонь під нерухому посадку кілець роликових і кулькових підшипників. Накаткою можна збільшити діаметр деталі на 0,3 ... 0,4 мм на сторону.
Накатку застосовують для збереження працездатності тільки деталей, що працюють в легких умовах, так як зносостійкість сполук, відремонтованих таким шляхом, значно нижче зносостійкості нового з'єднання.
Після пластичної деформації деталі обробляють термічно відповідно до технічних умов. При холодній обробці завжди більшою чи меншою мірою виникає наклеп.
Відновлення деталей тиском є відносно простим способом, але зумовлює наявність пристосувань. При цьому метал переміщається на зношені поверхні. Це передбачає наявність запасу металу. Але деталі автомобіля виготовляються з найменшою можливою масою, і тому цей метод не завжди застосуємо.
Зношені шліци вала розширюють накаткою роликом. Зношені конусні отвори рульових важелів можна осадити в пристосуванні. Особливим штампом витягають зношені шестерні. Втулки з кольорових металів зі зношеною внутрішньої або зовнішньої поверхнею обжимают в холодному стані. Отвори сепараторів конічних роликових підшипників зношуються і витягуються. Осадити їх просто пристосуванням Підшипник без зовнішньої обойми встановлюють внутрішньої обоймою на палець. Замість зовнішньої обойми ставлять пуансон, на внутрішній поверхні якого є стільки конічних поглиблень, скільки роликів в підшипнику. До грибку докладають силу ручного преса.
Рифленням відновлюють зношені шийки під підшипники кочення. Розмір шийки можна збільшити на 0,4 мм, але площа зіткнення при цьому значно зменшується і довговічність з'єднання буде малою.
Втомна міцність деталей, що працюють при знакозмінних навантаженнях, може при роботі або ремонті знизитися. Її можна збільшити зміцненням (наклепом) поверхні деталей. Роликом, виготовленим з інструментальної сталі і загартованим до HRC 62 ... 65, накочують поверхню, викликаючи тим стискають напруги, що підвищує втомну міцність деталі. Найпростіше пристосування з одним роликом зображено на 109. Накаткою можна трохи підвищити і жорсткість спіральних пружин. Пружину встановлюють на загартовану оправлення, останній виток фіксується штифтом. На ролику накатки є канавка, діаметр якої дорівнює діаметру дроту пружини. Накатку закріплюють у різцетримачі токарного верстата, а оправлення з пружиною - в патроні верстата. Встановлюють найменші обороти шпинделя верстата. Подача супорта ручна, рівна кроку пружини. Накатку притискають до витка пружини силою до 1000 Н (100 кгс). Жорсткість пружини кілька відновиться при багаторазовому накоченні роликом взад-вперед. Накочують і внутрішні поверхні, але пристосування для цього складніше. Якщо знайдеться відповідний кульку, то його можна проштовхнути через отвір.
Працюючи на пресах, стежать за показаннями манометра, намагаючись не перевищити допустимого тиску. Пристосування для пресування повинні бути надійно закріплені. Коли пуансон дійде до кінцевого положення, прес відразу ж вимикають. При гарячій обробці обличчя і тіло повинні бути захищені від бризок і осколків металу.
Знос, довговічність і надійність з'єднань у великій мірі залежать від шорсткості дотичних поверхонь. У шорсткостях поверхні накопичується масло як в кишенях. Тому на гладких поверхнях масло утримується гірше, що збільшує знос. Шорсткі поверхні мають малу поверхню зіткнення, тому особливо в період підробітки відбувається посилений знос. Через це треба обробляти поверхні до оптимальної шорсткості. При цьому важливо, щоб шорсткості були певної форми і розмірності.
Тема: Ремонт деталей полімерними матеріалами
Полімерні матеріали поділяються на термопластичні і термореактивні. Перші при нагріванні плавляться, а при охолодженні твердіють. І хоч це не супроводжується реакціями і при повторному нагріванні вони повертаються у пластичний стан, їхні фізико-механічні властивості дещо змінюються, частіше погіршуються.
Термореактивні матеріали під дією тепла спочатку пом'якшуються і частково плавляться, а потім в результаті хімічних реакцій переходять у неплавкий (твердий і нерозчинний) стан (процес незворотний).
У ремонтному виробництві полімерні матеріали в основному застосовують для зарівнювання тріщин, пробоїн, раковин, вм'ятин, усунення інших дефектів на поверхні деталі, приклеювання фрикційних накладок і склеювання деталей, відновлення зношеного шару деталей, фіксації циліндричних і різьбових з'єднань, відновлення нерухомих з'єднань підшипників кочення, герметизації та ущільнення з'єднань спряжених деталей, виготовлення полімерних ремонтних деталей.
Відновлення деталей за допомогою полімерних матеріалів передбачає: підготовку поверхні деталі для нанесення полімерного матеріалу (механічну, хімічну, теплову); виготовлення композицій на основі полімерних смол (хімічну, теплову обробку полімерних матеріалів); нанесення полімерного матеріалу на поверхню, що відновлюється; затвердіння (полімеризацію); механічну обробку відновленої деталі.
Тема : Ремонт деталей кривошипно -шатунного механізму
Ремонт деталей кривошипно-шатунного механізму
Блок циліндрів більшості двигунів виконаний з сірого чавуну з мокрими втулками, що підключаються. Основними дефектами блоку циліндрів є: отвори, відколи, тріщини різного розміру і розташування, знос циліндрів або деформація посадкових отворів для гільзи, знос розтрубів вкладишів основних підшипників, розтруби клапанів, обрив шпильки, обрив різьблення в отворах.
Дефекти блоку циліндрів встановлюються ретельним оглядом, виміром циліндрів і опресовуванням. При огляді виявляються отвори, відколи, помітні оку тріщини, поломки різьблення, стан дзеркала циліндра. Опресовування виявляє тріщини, які не помічені при огляді. У сорочці охолодження агрегату при тиску 4-5 кгс/см2 закачується вода. При цьому на блок циліндрів повинна бути встановлена ГБЦ або замість неї чавунна пластина з гумовою прокладкою. Повертаючи раму підставки, огляньте блок і встановіть, чи немає витоку води.
При наявності тріщин, що проходять через дзеркало циліндра, розетки клапанів і площину роз'єму, блок циліндрів відбраковується. У доступних місцях тріщини зварюються. Попередньо просвердлюють кінці тріщин
свердлом діаметром 5 мм і вирізати по всій довжині шліфувальним кругом під кутом 90 ° на глибину, 4/5 товщина стінок. Нагрівати блок циліндрів рекомендується перед зварюванням до температури 600-650 ° С. Тріщина зварюється газовим зварюванням, з використанням нейтрального полум'я, флюсу і чавунно-мідного наповнювача стрижня діаметром 5 мм. Шов повинен бути рівним, суцільним і виступати над поверхнею основного металу не більше ніж на 1,0-1,5 мм. Після зварювання блок циліндрів повільно охолоджується в термокоробці або в томільному ямі, Зварювання тріщин можна проводити без нагрівання блоку. В цьому випадку тріщина зварюється електрозварюванням, з використанням постійного струму зворотної полярності. Хороші результати виходять при зварюванні тріщин між стрічками циліндрів електродами з металу монель, і наступному режимі зварювання: струм - 120 А, напруга 65-75 В.
Зварювальний шов зачищається врівень з площиною основного металу напилком або наждачним кругом. Потім блок циліндрів піддають обтиску на підставці, перевіряючи герметичність зварювального шва. Не допускається протікання води по шву.
Тріщини і отвори в блоці циліндрів можна закрити епоксидними пастами. Процес герметизації полягає в наступному. Поверхня блоку з обох сторін тріщини очищається до блиску металевою щіткою або кам'яною крихтою при установці для очищення деталей. На кінцях тріщини дрилем діаметром 3-4 мм просвердлюють отвори, в них нарізають різьблення і вкручують заглушки з мідного або алюмінієвого дроту. Тріщина обробляється під кутом 60-90 ° стамескою або абразивним кругом на глибину до 3/4 товщина стінок.
На поверхні блоку навколо тріщини на відстані до 30 мм шорсткість створюється надрізом стамески або дробеструйной обробкою. Ацетоном або бензином знежирюють підготовлену поверхню блоку. Лопаткою послідовно наносяться шари епоксидної пасти на підготовлену суху поверхню. Спочатку наноситься перший шар пасти товщиною до 1 мм, різко переміщаючи шпатель по поверхні блоку. Потім нанесіть другий шар пасти товщиною не менше 2 мм, ретельно натираючи її. Загальна товщина шару пасти на всій поверхні повинна становити 3-4 мм.
Після закладення щілин блок циліндрів залишають на 25-28 годин до повного затвердіння пасти. Процес загартовування пасти можна прискорити, нагрівши електровідбиваючу піч до температури 100 ° С або при приготуванні пасти затверджувач (поліетиленполіамін) випарюють нагріванням до температури 105-110 ° С і потім витримують при цій температурі 3 год. Плями зрізаються стамескою.
Отвори, які можна відремонтувати, закладаються шляхом нанесення пасти. Спочатку краю і поверхня навколо отворів очищаються і знежирюються. Потім наноситься паста і наноситься клаптик зі скловолокна товщиною 0,3 мм і розкочується валиком. Відстань від краю латки до краю отвору має бути не менше 15-20 мм. Після цього наноситься другий шар пасти і наноситься другий пластир так, щоб він перекривав перший на 10-15 мм з усіх боків. Пластир згортається валиком. У такій послідовності наноситься до восьми шарів скловолокна. Останній шар пластиру покривають пастою, щоб захистити його від пошкоджень.
Отвори можна закрити зварювальними латками, виготовленими з м'якої сталі тієї ж товщини, що і стінка деталі. Форма пластиру повинна відповідати формі пошкодженої ділянки, а її розміри повинні бути на 1,5-2,0 мм менше розміру отвору. Краї отвору і латки обробляються під кутом. Латка спочатку зварюється в двох місцях, а потім зварюється по периметру. Використовується електрозварювання і мідні електроди, загорнуті в жерсть. Пошкоджену ділянку рекомендується заклеїти епоксидною смолою.
Після ремонту отвору з латками і обробки нанесеного шару пасти блок циліндрів піддається обтиску на підставці. Якщо протягом 5-6 хвилин просочування води не виявлено, то ремонт агрегату виконується якісно.
Тріщини в сорочці охолодження агрегату можуть бути заклеєні штифтами. Порядок роботи наступний. Спочатку на кінцях тріщини свердлом просвердлюють отвори діаметром 4-5 мм. Потім цим же свердлом просвердлюють отвори по всій довжині тріщини на відстані 7-8 мм один від одного. Наріжте різьблення і прикрутіть мідні прути на глибину, рівну товщині стінки блоку.
Прути зрізають ножівкою, залишаючи кінці виступаючими на 1,5-2,0 мм над поверхнею деталі. Між встановленими штифтами просвердлите отвори так, щоб вони перекривали їх на 3/4 Діаметр. Наріжте різьблення, вкрутіть мідні прути і наріжте їх ножівкою, залишивши відповідні кінці. Далі легкими ударами молотка кінці штифтів розрівнюютьть, утворюючи щільний шов.
Блок циліндрів, який має стружку, дозволену до ремонту, відновлюється шляхом наплавлення
Величина зносу циліндрів або гільз визначається показником нутроміра . Вимірювання проводяться в двох взаємно перпендикулярних напрямках і в трьох поясах. Один напрямок встановлюється паралельно осі колінчастого вала. Перший вимір виконують на відстані 5-10 мм від верхньої площини блоку, другий - в середній частині циліндра і третій - на відстані 15-20 мм від нижнього краю циліндра. Залежно від величини зносу встановлюється вид ремонту. Зазвичай проводиться розточування і подальше шліфування.
Розточування - це основний спосіб ремонту циліндрів і вкладишів. Циліндри або гільзи обробляються для ремонту типорозмірів на розточувальних верстатах стаціонарного або переносного типу. Втулки кріпляться в спеціальному пристрої, встановленому на столі розточувального верстата.
Під час обробки в оброблюваний отвір вставляється шліфувальна головка, з'єднана зі шпинделем верстата (бруски знаходяться в стислому стані). Спочатку проводиться попереднє, а потім і остаточне шліфування Використовується шліфувальна головка з механічним, гідравлічним або пневматичним здавлюючим пристроєм.
Пневматичний привід забезпечує постійний тиск брусків на стінки циліндрів, що підвищує якість обробки і продуктивність процесу відточування. В цьому випадку є можливість регулювати тиск брусків на оброблювану поверхню і автоматизувати процес розтискання брусків у міру зміни діаметра гільзи.
Для отримання правильної геометричної форми циліндра в процесі шліфування необхідно встановити певну довжину ходу головки. Вона повинна бути такою, щоб абразивні бруски виходили за торець циліндра на величину, що не перевищує 0, 2-0, 4 їх довжини. При більшому ходу головки спостерігаються похибки форми, зокрема, увігнуті, а при меншому значенні ходу - форма стовбура.
Шліфування проводиться при безперервній подачі охолоджуючої рідини в зону обробки. В якості охолоджуючої рідини використовується гас або суміш гасу з шпиндельним маслом.
Для попереднього відточування рекомендуються злитки з синтетичних алмазів A10MX50, а для остаточного відточування - бруски BX-100X 11 X9K38BS. Обробка здійснюється в наступних режимах: окружна швидкість обертання головки становить 280 об / хв, а швидкість зворотно-поступального руху - 90 подвійних ударів в хвилину. Припуск на попереднє шліфування встановлюється не більше 0, 08 мм, а на остаточне - 0, 04 мм.
Остаточна обробка циліндрів двигуна може здійснюватися кульовими головками, що котяться і дозволяють отримати поверхню необхідної точності і шорсткості. Процес здійснюється після розточування або одночасно за один прохід отвір циліндра обробляється фрезою і кулькою головки.
Рекомендується наступний режим різання і прокатки: частота обертання - 450 об / хв; подача на 1 оборот - 0,08 мм; глибина різання - 0,25 мм; сила тиску на м'яч - 20 кгс.
Незалежно від способу кінцевої обробки циліндрів (вкладишів), їх внутрішній діаметр повинен мати однаковий ремонтний розмір.
Балони можна відновити, натиснувши на гільзи, якщо їх знос перевищує останній ремонтний розмір або є глибокі ризики і потертості на стінках. Для цього балони обробляються під ремонтну втулку, товщина якої повинна бути не менше 3-4 мм. У верхній частині циліндра під плечем гільзи розточується кільцева виїмка. Гільзи пресуються натягом 0, 05-0, 10 мм на гідравлічному пресі, пресуються і обробляються (розточування і шліфування) до номінального розміру. Іноді гільзи обробляються до розміру, меншого номінального розміру, щоб використовувати перероблені старі поршні.
Втулки, що підключаються, пресуються і притискаються спеціальними знімачами.
Деформації розтрубів корінних підшипників перевіряються калібрувальним качалкою. Якщо вона входить в гнізда і повертається без особливих зусиль, то деформацій немає.
Знос, а також величина перекосу розтрубів корінних підшипників може бути встановлена спеціальним пристроєм.
Зношені і деформовані поверхні вкладишів корінних підшипників розточуюються до номінальних розмірів. Зняті кришки підшипників повинні бути промарковані (ставиться номер блоку циліндрів і серійний номер кришки). Площини роз'єму кришки фрезеруються до певного розміру (0, 6-0, 8 мм) і управляються індикаторним пристроєм. Також фрезерується зовнішній паз в передній кришці і фігурний паз в задній кришці корінного підшипника. Оброблені і прийняті кришки збираються разом з блоком циліндрів відповідно до їх маркування.
Зібраний блок циліндрів з кришками встановлюється і фіксується на пластині розточувального верстата. Отвори корінних підшипників розточуються за один прохід фрезами, встановленими на борштангу до розмірів, встановлених кресленням або технічними характеристиками. Після розточування перевіряються розміри отворів, шорсткість поверхні і міжосьовий інтервал між основними отворами підшипників і втулками розподільного вала.
Ремонт головки блоку циліндрів і сідел клапанів. Основними дефектами ГБЦ є: тріщини в різних місцях, викривлення поверхні інтерфейсу з блоком циліндрів, знос отворів в направляючих втулках клапанів і різьблення, ослаблення посадки сідла клапанів в розетках.
ГБЦ з клапанними деталями працює в дуже суворих умовах - при високих температурах і впливі механічних і теплових навантажень.
Тому в залежності від дефекту і його розташування необхідно правильно встановити спосіб ремонту. Тріщини можна закладати епоксидними пастами, зварюючи загальним підігрівом головки, ямковим ремонтом, штифтом.
Викривлення привалочної площини головки з блоком циліндрів усувається шліфуванням або фрезеруванням з подальшим подрібненням. При цьому повинна бути витримана мінімально допустима глибина камери згоряння, яка вказана в технічних характеристиках. Величина викривлення площини встановлюється на пластину фарбою або за допомогою лінійки
Зношені отвори в направляючих втулках і під втулками направляючого клапана обробляються розгортками до номінального або ремонтного розміру. Якщо знос більше допустимого значення, втулку замінюють.
Знос і раковини на фасках сідлів клапанів усуваються шляхом шліфування або заміни сідла. Зробіть притирання сідла клапаном або позіхання з подальшим шліфуванням і притиранням. При позіханні використовується набір з чотирьох зенкерів з кутами нахилу ріжучих кромок 30 або 45, 75 і 15 °. Зенкери з кутами 75 і 15 ° є допоміжними і використовуються для отримання необхідної робочої фаски. На рис. 75 показує послідовність звуження сідла клапана.
Робочі фаски сідлів клапанів шліфуються абразивними кругами під відповідним кутом. Для двигуна ЗІЛ-130 впускні клапани шліфуються під кутом 60 °, а випускні - під кутом 45 ° до осі напрямних вводів. Ширина робочої фаски сідла клапана повинна бути 1, 5-2, 0 мм для двигунів ГАЗ і 2, 5-3, 0 мм для двигунів ЗІЛ.
При великих зносах сідла клапана, коли утоплення калібру перевищує допустиме значення, зазначене в специфікаціях, сідло клапана замінюється на нове. Для цього зношене сідло клапана розточується, а потім притискається сідло клапана, що підключається, карбуючи його спеціальною оправкою. Далі робоча фаска полірується або приколюється до отримання необхідного розміру. Потім проводиться притирання робочою поверхнею клапана.
Притирання виконується на спеціальних верстатах, які повністю механізують процес і дозволяють обробляти всі клапани одночасно. Для притирання використовуйте пасту для притирання або пасту GOI. Рекомендується спочатку обкласти пастою грубішого помелу. Для отримання кінцевої фінішної поверхні використовується тонка паста. Притирання повинна забезпечувати щільне, герметичне з'єднання між робочими фасками клапана і сідлом, виключаючи можливість проникнення газу. Клапан і сідло повинні мати плоску матову смужку певної ширини по всьому колу фаски (рис. 76). Для двигунів ЗІЛ ширина смуги повинна дорівнювати l/2 ширина робочої фаски сідла.
Якість притирання перевіряється пристроєм, який створює надлишковий тиск повітря (0,7 кгс/см) над клапаном2). Тиск встановлюється манометром і воно не повинно помітно знижуватися протягом 1 хвилини.
Коли втягування сідла клапана в розтрубі ослаблено, його видавлюють, а отвір заточують для установки сідла ремонтного розміру. При натисканні використовуються різні знімачі.
Ремонт поршнів.
Основними дефектами поршня є нагар на дні і канавках, знос канавок під кільцями, отвори в барабанах, тріщини і подряпини на стінках.
Для очищення пазів поршня від нагару використовується пристрій у вигляді сталевої стрічки з ручками, на внутрішній поверхні яких закріплені фрези. Вставляючи різці в паз і повертаючи пристрій навколо поршня, нагар видаляється.
Поршні зі зношеними канавками для поршневих кілець замінюються новими відповідними розмірами.
Зношений отвір в поршневих котушках відновлюється шляхом розгортання, а потім установки збільшеного поршневого штифта. Незначні ризики або подряпини на зовнішній поверхні поршня видаляються зачисткою наждачним папером. Поршні з тріщинами і глибокими подряпинами замінюються на нові.
Вибір поршневих кілець.
Зношені і поршневі кільця, що втратили пружність, замінюють новими. Підбір нових кілець роблять відповідно до розмірів поршня та циліндра. При підборі до поршня кільця роблять прокатку його канавкою і якщо немає заїдань, то щупом визначають зазор. У разі заїдання кільця в канавці або малого зазору кільце шліфують на аркуші дрібнозернистого наждакового паперу, покладеного на повірочну плиту. Величина зазору по висоті канавки повинна перевищувати 0,052-0,082 мм верхнього і 0,035- 0,70 мм - інших компресійних кілець.При підборі по циліндру визначають зазор в стику кільця, встановленого в циліндр. Кільце можна встановлювати калібр, внутрішній діаметр якого дорівнює діаметру циліндра. При відсутності або малій величині зазору здійснюють підпилювання стиків кілець особистим напилком. При цьому площини стиків кілець повинні бути паралельними. Технічними умовами встановлено кожного двигуна певна величина зазору. Для компресійних кілець проміжок повинен бути 0,3-0,5 мм, а для малознімних кілець -0,15-0,45 мм. При проміжку більше нормального кільця бракуються.
Ремонт поршневого пальця. Зношені поршневі пальці відновлюють хромуванням. Здійснюють нарощування пористого хрому, який добре утримує олію. Після нанесення шару хрому пальці шліфують під необхідний розмір. При зносі діаметром більше 0,03 мм пальці ремонтують або замінюють новими. Рекомендується при капітальному ремонті двигуна встановлювати поршневі пальці лише номінального розміру
Ремонт шатуну. Основними дефектами шатуна є: вигин та скручування стрижня, знос отвору втулки верхньої головки та отвори під втулку, знос отвору та торцевих поверхонь нижньої головки. Зношені втулки верхньої головки шатуна зазвичай замінюють новими. Іноді втулки розточують або розгортають під збільшений ремонтний розмір поршневого пальця. Зношений отвір головки під втулку відновлюють обробкою під ремонтні розміри (шатуни двигунів ЯМЗ-236 та ЯМЗ-238) .Отвір нижньої головки шатуна під вкладиш розточують і шліфують під номінальний розмір після обробки поверхонь стикових кришки з шупом. Останні фрезерують або шліфують, використовуючи спеціальні пристрої. За наявності гальванічної ділянки доцільно отвір нижньої головки шатуна ремонтувати залишенням. Після залишення отвір відновлюють до номінального розміру. Цей метод ремонту дозволяє зберегти жорсткість деталі та міжцентрову відстань між отворами верхньої та нижньої головок шатуна.Вигин та скручування стрижня шатуна усувають правкою. Для редагування та контролю шатунів застосовують різні пристосування. На рис. 80 показана одна з конструкцій пристосувань, що застосовуються. На даному пристрої одночасно перевіряють вигин і скручування шатуна, а також відстань між центрами його головок. При виявлених відхиленнях, що перевищують допустимі величини, шатун правлять спеціальним ключем без зняття з пристрою. При цьому верхня головка шатуна повинна займати положення між вертикальною та горизонтальною плитамиШатун щільно встановлюється в пристрої за допомогою великої качалки 8; пропущеної через стійки 9. Малу качалку 10 вставляють у оброблений отвір верхньої головки шатуна. Спочатку попередньо перевіряють скрученість шатуна. Для цього шатун, встановлений в горизонтальному положенні, вручну повертають так, щоб мала качалка 10 по черзі упиралася на сухарі стійок 11. Наявність зазору вкаже про скручування шатуна.
Визначення величини скручування та вигину проводиться при знаходженні шатуна у вертикальному положенні. При цьому мала качалка 10, стикаючись з упорами коромисла 4, знаходиться в контакті зі штифтами індикаторів 2 / і 7, які вказують величину скрученості шатуна. Індикатор 5 встановлює відхилення відстані між осями отворів верхньої та нижньої головок, а індикатор 6 - непаралельність осей отворів. Після редагування та контролю, різко переміщуючи рукоятку 13, вибивають велику качалку 8, звільняючи шатун. Перед початком роботи індикатори пристрою налаштовують за еталонним шатуном.
Ремонт колінчастого валу. Основними дефектами колінчастого валу є: вигин, знос шатунних та корінних шийок, знос отвору під підшипник провідного валу коробки передач та отворів фланця валу під болти кріплення маховика.
Вигин колінчастого валу двигуна перевіряють на стенді, призмах, встановлених на контрольній плиті або в центрах токарного верстата за допомогою індикатора. Вигин (биття середньої корінної шийки щодо крайніх) понад допустиме за технічними умовами усувають правкою на пресі.
Колінчастий вал встановлюють на призми крайніми корінними шийками, а штоком преса через мідну або латунну прокладку тиснуть на середню шийку з протилежної сторони згину. При цьому величина прогину повинна бути приблизно в 10 разів більше вигину, що усувається. Вал витримують під навантаженням на пресі протягом 2-4 хв. Після виправлення рекомендується вал піддати термічній обробці, тобто. нагріти до 180-200°З витримати при цій температурі протягом 5-6 год. Потім вал перевіряють на биття. Биття середніх шийок по відношенню до крайніх шийок не повинно перевищувати 0,05 мм. Зношені шатунні та корінні шийки колінчастого валу відновлюють шліфуванням під ремонтний розмір. Встановлюють один ремонтний розмір для всіх шатунних шийок та один ремонтний розмір для корінних шийок залежно від найменшого діаметра, отриманого в результаті обмірювання та рекомендованого технічними умовами ремонтного розміру. Завершують обробку шийок валу поліруванням або суперфінішуванням до отримання необхідної шорсткості поверхні. Потім промивають масляні канали та зовнішню поверхню валу гасом у спеціальній ванні.При відновленні шийок колінчастого валу важливо правильно вибрати настановні бази. Рекомендується встановлювати колінчастий вал на верстаті на ті ж самі базові поверхні, які застосовувалися при виготовленні. Тоді виходять мінімальні похибки, пов'язані з його встановленням
У тих випадках, коли використані всі ремонтні розміри та подальше зменшення діаметра валу неприпустимо, а міцність його достатня, шийки можна відновлювати наплавленням з подальшою обробкою під номінальний розмір.
.
Як технологічна база можуть бути прийняті прошліфовані корінні шийки при шліфуванні шатунних шийок. При цьому вісь обертання шатунних шийок повинна точно збігатися з віссю верстата шпинделя. Зношування отвору під підшипник ведучого валу коробки передач відновлюють постановкою втулки. На рис. 81 наведено ескіз відновленого колінчастого валу двигуна ЗІЛ-130, На токарно-гвинторізному верстаті розточують отвір у валі до діаметра потім запресовують ремонтну втулку до упору, розточують отвір у втулці розміром 52 і знімають фаску 3X30°
Зношений отвір у фланці вала для болтів кріплення маховика обробляється розгорткою для ремонту розмірів у вузлі маховика. При складанні ставлять болти кріплення маховика збільшеного ремонтного розміру.
Після ремонту необхідно провести контроль за колінчастим валом, щоб встановити якість виконаних робіт і виявити можливі мийки і тріщини.
Заміна підшипників.
Підшипники шатунів і головні горловини колінчастого вала виконані у вигляді сталевих тонкостінних вкладишів, залитих з внутрішньої сторони антифрикційним сплавом. Заводи випускають вкладиші як номінальних, так і ремонтних розмірів. Коли вони зношуються, вкладиші замінюються без будь-якої додаткової підгонки.
Тема: Ремонт деталей трансмісії
Зчеплення може мати такі дефекти:
а) спрацювання фрикційних накладок
б) жолоблення і тріщини дисків
в) спрацювання кулачків відтискних важелів
г) тріщини в кожусі зчеплення
При спрацюванні фрикційних накладок їх замінюють на нові закріплюючи заклепками або спеціальним клеєм. Головки заклепок повинні утопати на глибину 1 - 1,5мм. При жолобленні веденого диску його правлять з допомогою вилочної правки. Торцеве биття допускається не більше 1,5 мм у крайніх точках від центру. Нерівномірно спрацьовані робочі поверхні ведучих дисків проточують на токарному верстаті до видалення слідів спрацювання та шліфують. Спрацьовані кулачки відтискних важелів наварюють і механічно обробляють до потрібного розміру згідно з шаблоном. Тріщини в кожусі зчеплення заварюють. Корпусні деталі агрегатів трансмісії можуть мати такі дефекти: а) тріщини б) спрацювання посадочних місць під підшипники , жолоблення зєднувальних площин. Тріщини в корпусах заварюють,посадочні місця під підшипники відновлюють шляхом завтулювання, жолоблення зєднувальних площин усувають фрезеруванням. Шестерні які мають спрацьовані зуби вибраковують. Шестерні із спрацьованими шліцевими канавками ремонтують розточуючи отвори і запресовують у них шліцеві втулки. Зігнуті вали агрегатів трансмісії правлять в холодному стані. Скручені вали вибраковують. Посадкові місця валів у разі значного спрацювання наплавляють і обточуюють до номінального розміру.. Спрацьовані шліцеві і шпонкові канавки заварюють і фрезерують нові. Пошкоджені підшипники кочення замінюють на нові. Погнуті карданні вали випрямляють і динамічно балансують. Спрацьовану різьбу проточують і нарізають нову.