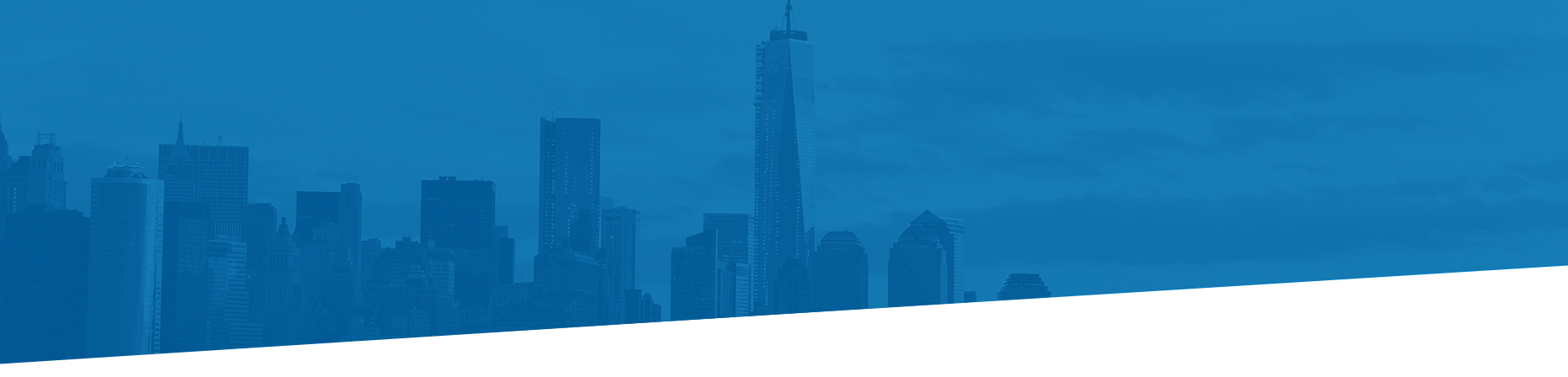
МАТЕРІАЛОЗНАВСТВО
Тема: Припої і флюси
Учбові питання:
1. Припої
2. Флюси
Література:А. Попов, Т. Пахар " Основи слюсарної справи" стр. 58 - 62
1. Припій - сплав який має температуру плавлення нижчу ніж метали, що зєднуються при паянні і служать для утворення паяльного шва. За температурою плавлення припої діляться на дві групи : легкоплавкі (мякі) і тугоплавкі ( тверді). До легкоплавких припоїв відносяться оловяно - свинцеві ( ПОС),сурмянисті (ПОССу), оловяно - свинцево - кадмієві (ПОСК), оловяно - цинкові (ОЦ). Найчастіше використовують припої ПОС - 40, ПОС - 30. Цифра у маркуванні припою вказує на процентний вміст олова у складі припою, а решта - свинець. Сурмянисті припої використовують при зєднанні оцинкованих або цинкових виробів. Оловяно - цинкові припої використовують для зєднання виробів з алюмінію. До тугоплавких( твердих) припоїв відносяться мідні і срібні сплави . Мідно - цинкові припої ( ПМЦ -36, ПМЦ - 54) застосовують для зєднання деталей із статичним навантаженням. Мідно -титанові припої(ПМТ - 49) застосовують для зєднання чавуну, твердих сплавів. Срібні припої (ПСр - 25,ПСр - 45) - для пайки міді, бронзи, латуні.
2.Флюс - речовина, яка захищає розплавлений метал від корозії при паянні. Як флюси при паянні застосовують : соляну кислоту,хлористий цинк,каніфоль, рідке скло. Соляна кислота застосовується для пайки цинку і залізних оцинкованих виробів. Хлористий цинк - паяння мякими припоями латуні,міді, заліза.Каніфоль - паяння оловяно - свинцевими припоями. Рідке скло - паяння твердими припоями.
Тема: Антифрикційні матеріали
Антифрикці́йні матеріа́ли (від англ. friction - тертя) - матеріали, що застосовуються для деталей машин (підшипники, втулки та ін.), що працюють при терті ковзання і мають низький коефіцієнт тертя. Відрізняються низькою адгезією, добрими припрацьовуваністю, теплопровідністю і стабільністю властивостей. Однією з важливих властивостей антифрикційних матеріалів є їх нездатність або мала здатність до схоплювання (адгезії) з матеріалом спряженої деталі.
Вимоги, що ставляться до антифрикційних матеріалів
Крім забезпечення низького коефіцієнта тертя до антифрикційних сплавів ставляться наступні вимоги:
- здатність утримувати мастило;
- добра припрацьовуваність, тобто здатність до швидкого збільшення реальної площі контакту у початковий період роботи пари;
- мала зношуваність поверхонь, що труться, і в першу чергу валів та осей, які працюють у парі з підшипником (мала зношувальна здатність);
- підвищений опір до заїдання та утворення задирів;
- достатня міцність, необхідна для стабільної роботи підшипника при високих питомих тисках. Якщо антифрикційний матеріал не має достатньої міцності, його наносять шаром невеликої товщини на міцніший матеріал;
- висока контактна витривалість для виключення викришування поверхні сплаву. Цей показник особливо важливий для швидкохідних машин, на деталі яких впливають циклічні напруження, що змінюються з великою швидкістю і рівень яких у важко-навантажених машинах може бути значним;
- гарна теплопровідність для відводу тепла, яке виділяється у вузлі тертя, що знижує температуру поверхонь контактуючих деталей;
- висока корозійна стійкість, оскільки в процесі експлуатації на вкладень можуть впливати агресивні речовини;
- прийнятні технологічні властивості.
Металеві антифрикційні матеріали
За структурними ознаками металеві антифрикційні матеріали ділять на дві групи: перша - матеріали з м'якою основою і твердими включеннями, друга - матеріали з твердою основою і м'якими включеннями. Основними металевими антифрикційними матеріалами слугують: сталі, алюмінієві та мідні сплави.
З числа легованих сталевих матеріалів часто застосовують сталі: марганцеві (35Г2, 40Г2, 45Г2, 50Г2 та ін), хромомолібденові (30ХМ, 3ХМА, 35ХМ, 38ХМ), хромонікелеві (40ХН, 45ХН, 30ХН3А), хромонікелеві з бромом (30ХНР, 40ХНР) і хромомарганцевистонікелеві з бромом - 40 ХГНР. Деталі піддають або об'ємному загартуванню з відпуском, або поверхневому гартуванню струмами високої частоти (СВЧ).
Для підшипників ковзання (вкладишів, втулок шарнірів та ін) використовуються різні антифрикційні сплави. До них належать сплави на мідній, цинковій, алюмінієвій та олов'яно-свинцевій основах. Останні одержали назву бабітів. Інколи застосовують антифрикційні чавуни з графітними включеннями.
Бабіти і чавуни застосовувалися на початковому етапі розвитку техніки і мають лише історичне значення. У міру зростання потужності двигунів, жорсткості режиму експлуатації, зниження металоємності відбувся перехід до твердіших підшипникових матеріалів на мідній, цинковій та алюмінієвій основі, добре сумісних зі сталями.
Мідні антифрикційні матеріали поділяються на бронзи і латуні. Найпоширеніші олов'яні бронзи. Неосновними легуючими елементами є свинець, нікель, фосфор, цинк, залізо та ін.
Меншого поширення, ніж бронзи, отримали латуні. Найчастіше як антифрикційні матеріали використовують кременисті та марганцовисті латуні, а також алюмінієво-залізисті.
Як підшипникові матеріали успішно застосовуються цинкові сплави з легуючими елементами у вигляді міді, алюмінію, магнію. Низька температура плавлення (400 ºС) і підвищена розм'якшеність забезпечують добре припрацювання. З них роблять біметалічні вкладиші підшипників ковзання.
У сучасному автомобіле- і тракторобудуванні широке розповсюдження отримали антифрикційні сплави на основі алюмінію. Алюмінієві сплави мають порівняно високу міцність, корозієстійкість, дешеві і не дефіцитні, мають низьку щільність і високу теплопровідність. Легуючими елементами слугують олово, мідь, нікель, кадмій, кремній, залізо, марганець, титан та інші елементи.
Металокерамічні антифрикційні матеріали
Цей тип матеріалів поділяють на дві групи:
- пористі підшипники,
- компактні металокерамічні антифрикційні матеріали,
Хімічний склад пористих металокерамічних антифрикційних матеріалів обирається в залежності від умов роботи підшипника і технологічного процесу.
Пористі підшипники можуть застосовуватися замість бронзових підшипників ковзання та шарикопідшипників для роботи при pv до 70 МПа. В елементах ескалаторів метрополітену, роликах вугільних транспортерів, котків мостових кранів, допоміжні пристрої двигуна дизеля, кіноапаратура, звукові протектори, патефони, вентилятори, сепаратори для шарикопідшипників і ін.
Компактні (непористі) металокерамічні антифрикційні матеріали. Переважно застосовуються в Англії і США непористі антифрикційні металокерамічні матеріали можна розбити на три групи:
- матеріали, що виготовляються з подрібненої і декарбюризованої сталевої стружки пресуванням, спіканням і подальшого гарячим штампуванням;
- металокерамічні матеріали з свинцевистої бронзи, що застосовуються у вигляді втулок, біметалевих вкладишів і стрічки (металокерамічний шар на сталевий основі);
- тришаровий матеріал, що складається із сталевої стрічки, на яку напресовуються порошки міді та нікелю.
Товщина металокерамічного шару - близько 0,5 мм.
Після спікання пори цього шару заповнюються розплавленим свинцевим бабітів (під вакуумом), який утворює також поверхневий шар (товщиною 0,02 - 0,075 мм).
Антифрикційні полімерні матеріали
Серед термопластичних матеріалів найбільшого поширення набули поліаміди, поліацеталі, поліетилен, фторопласт, серед реактопластів - епоксидні та фенолформальдегідні смоли.
При введенні до складу полімерних матеріалів твердих мастил та інших антифрикційних волокнистих та дисперсних наповнювачів зносостійкість композитів зростає від 2 до 50 разів і більше. Як антифрикційні наповнювачі застосовують тверді мастила (графіт, дисульфід молібдену, нітрид бору, слюда), окиси металів, особливо м'яких (цинк, олово, свинець, мідь), солі (хлориди, сульфіди, селеніди, телуриди), вуглецеві, базальтові та скляні волокна й інше.
Критерії вибору антифрикційних матеріалів
Матеріал до пар тертя підбирається конкретно у кожному випадку в залежності від типу виробу і умов роботи вузла.
Основними критеріями при виборі матеріалу для підшипників ковзання є:
- коефіцієнт тертя;
- питомий тиск на підшипник;
- швидкість ковзання;
- характер навантаження (статичний, циклічний);
- твердість матеріалу поверхні вала.
- Тема: Корозія металів
Коро́зія мета́лів - самопливне руйнування металів і сплавів, у результаті хімічної, електрохімічної або фізико-хімічної взаємодії з навколишнім середовищем. До основних видів корозії за її механізмом відносять хімічну, електрохімічну,
Корозія - це природний процес, який перетворює очищений метал на більш хімічно сталу форму, таку як: його оксид, гідроксид, карбонат або сульфід. Це поступове руйнування матеріалів (зазвичай металів) шляхом хімічної та / або електрохімічної реакції з довкіллям. Корозійна інженерія - це галузь, яка займається контролем та запобіганням корозії.
У найбільш поширеному вживанні цього слова, воно означає електрохімічне окислення металу внаслідок реакції з окисником, таким як кисень або сульфати. Іржавіння, утворення оксидів заліза, є відомим прикладом електрохімічної корозії. Цей вид пошкоджень, як правило, утворює оксид (и) або сіль (і) первинного металу і призводить до характерного помаранчево-бурого забарвлення. Корозія може також виникати в інших матеріалах, ніж метали, таких як кераміка або полімери, хоча у цьому сенсі, термін «деградація» є більш придатним визначенням. Корозія знижує корисні властивості матеріалів і конструкцій, такі як: міцність, зовнішній вигляд та проникність щодо рідин і газів.
Багато конструктивних сплавів піддаються корозії лише під впливом вологи в повітрі, але на процес може сильно вплинути дія певних речовин. Корозія може бути зосереджена локально, утворюючи заглибину чи тріщину, або вона може поширюватись на широку площу, більш-менш рівномірно корозуючи поверхню. Оскільки корозія - це процес, керований дифузією, вона виникає на відкритих поверхнях. Отже, способи зниження активності відкритої поверхні, такі як пасивація і хроматування, можуть підвищити корозійну стійкість матеріалу. Пасивація полягає у нанесенні на метал хімічним або електрохімічним шляхом оксидних, фосфатних й інших плівок. Проте, деякі механізми корозії менш помітні та менш передбачувані.
Хімія корозії складна; її можна вважати електрохімічним явищем. Під час корозії в певній точці на поверхні предмета, виготовленого із заліза, відбувається окислення, і ця пляма веде себе як анод. Електрони, що вивільняються в цій анодній плямі, рухаються крізь метал і переходять до іншої точки на металі і відновлюють кисень у цьому місці в присутності H+ (який, як вважають, доступний з H2CO3, що утворюється внаслідок розчинення вуглекислого газу з повітря у воді в вологому повітрі атмосфери. Іон водню у воді також може бути доступним завдяки розчиненню інших кислотних оксидів з атмосфери). Ця пляма веде себе як катод.
На перебіг корозії великий вплив має pH середовища внаслідок водневої або кисневої деполяризації[1].
Різновиди корозії
Загальна і локальна корозія
- Загальна (нерівномірна) корозія - це процес, що протікає на всій або на якій-небудь частині поверхні металу зі швидкістю 0,1 - 0,5 мм/рік. Результатом загальної корозії є суцільне руйнування поверхні металу або якої-небудь частини його поверхні, крім того глибина проникнення корозії на одних ділянках може бути дещо більше, ніж на інших. Значно частіше поверхня металу піддається локальній корозії, характерною особливістю якої, є висока швидкість руйнування металу на окремих ділянках, що досягає 1 - 10 мм/рік. Наслідком локальної корозії є руйнування металу в глибину аж до появи наскрізних отворів, при цьому сусідні ділянки можуть практично не зачіпатися корозією.
- Основними видами локальної (місцевої) НКТ є:
- пітингова (виразкова) корозія;
- корозія плямами;
Сліди загальної корозії (іржі) на металевих частинах електромеханічної засувки водогону- корозія у вигляді борозенок (канавок);
- корозія у вигляді плато;
- мейза-корозія;
- контактна корозія;
- підплівкова корозія;
- гальванічна корозія.
Місцева (локальна) корозія буває у вигляді плям, виразок, точок (пітингова); вона може бути вибіркової (наприклад, знецинкування латуні), міжкристалітною (інтеркристалітною), транскристалітною; до місцевої корозії відноситься також корозійне розтріскування. В умовах експлуатації виробів для силового елементу конструкції найбільш небезпечна міжкристалітна корозія корозійне розтріскування, для резервуару, трубопроводу або реактору - точкова або виразкова корозія, оскільки порушується герметичність при появі хоча б одного наскрізного отвору, для поверхонь тертя - загальна корозія[2][3][4].
Хімічна корозія
Хімічна корозія відбувається в середовищах, які не проводять електричного струму. Вона обумовлюється дією на
метали неелектролітів (спирту, бензину, мінеральних мастил тощо) і сухих газів (кисню, оксидів азоту, хлору, хлороводню, сірководню та інше) при високій температурі (так звана газова корозія).
У результаті взаємодії металів із зовнішнім середовищем їх поверхня вкривається тонким шаром (плівкою) різних хімічних сполук (продуктів корозії): оксидів, хлоридів, сульфідів тощо. Інколи цей шар такий щільний, що крізь нього не може проникати агресивне середовище. В таких випадках з часом швидкість корозії зменшується, а то й зовсім припиняється. Наприклад, алюміній в атмосфері повітря кородує значно повільніше від заліза, хоч за своїми хімічними властивостями він активніший від заліза. Це пояснюється тим, що поверхня алюмінію вкривається суцільною, досить щільною і міцною оксидною плівкою, яка ізолює метал від доступу кисню, а оксидна плівка заліза, навпаки, є крихкою і ламкою, містить багато пор і тріщин, через що кисень повітря крізь неї легко проникає до поверхні заліза, і тим обумовлюється безперервне його руйнування.
Електрохімічна корозія
Електрохімічна корозія більш поширена і завдає значно більшої шкоди, ніж хімічна. Вона виникає при контакті двох металів у середовищі водних розчинів електролітів. На відміну від хімічної електрохімічна корозія супроводжується переміщенням валентних електронів з одної ділянки металу на іншу, тобто виникненням місцевих електричних струмів внаслідок утворення на кородуючій поверхні так званих гальванічних пар.
Подвійний електричний шар на границі метал-електролітПри зануренні цинкової пластинки в кислоту атоми цинку з її поверхні поступово переходять у розчин у вигляді іонів Zn2+, а їхні валентні електрони залишаються на поверхні металу. Внаслідок цього на границі метал-електроліт утворюється подвійний електричний шар. Внутрішню обкладку цього шару утворюють негативні заряди надлишкових електронів (позначених знаком -), а зовнішню обкладку - позитивні заряди іонів цинку (позначених знаком +). Внаслідок взаємного притягування протилежних зарядів іони цинку, що переходять у розчин, розміщуються поблизу поверхні металу. Нормальний електродний потенціал цинку складає -0,7618 в[5].
Подальший процес розчинення цинку стає можливим лише завдяки тому, що іони водню підходять до поверхні цинку і приєднують надлишкові електрони. При цьому іони цинку перестають утримуватись у подвійному електричному шарі негативними зарядами і вільно дифундують у глибину розчину, а на їх місце з поверхні металу переходять нові іони цинку і т. д. Таким чином, приєднання надлишкових електронів з поверхні металу іонами водню електроліту забезпечує безперервний перехід іонів цинку в розчин, тобто його розчинення, (кородування).
Обидва ці процеси відбуваються на поверхні того самого металу - на цинковій пластинці. Але при певних умовах їх можна просторово роз'єднати. Так, коли поряд з цинковою пластинкою занурити в розчин мідну і обидві пластинки з'єднати металічним провідником, то перший процес (розчинення цинку) буде відбуватися на цинковій пластинці, а другий (відновлення іонів водню) - на мідній.
Мідь, як відомо, з розведеною сульфатною кислотою не взаємодіє. Тому іони міді не переходять у розчин і на її поверхні не буде надлишків електронів. Але коли обидві пластинки з'єднати мідною дротиною, то концентрація надлишкових електронів почне вирівнюватись на обох пластинках і електрони з цинкової пластинки почнуть переміщатися на мідну. Якщо в систему включити гальванометр, то він покаже наявність електричного струму. Однак концентрація електронів, на обох пластинках не може бути однаковою. Це пояснюється тим, що іони водню легше розряджаються (приєднують електрони) на поверхні міді, ніж на поверхні цинку. Через це процес відновлення іонів водню і виділення вільного водню буде відбуватися практично лише на мідній пластинці, а на цинковій; майже зовсім
припиниться. Але швидкість розчинення цинку при цьому значно збільшиться, оскільки надлишкові електрони, з поверхні цинку будуть швидко переміщатися на мідну пластинку і там приєднуватися іонами водню.
Приклад розчинення цинку, що перебуває в контакті з міддю, у розчині сульфатної кислоти є прикладом утворення і роботи гальванічних пар, які лежать в основі електрохімічної корозії. Гальванічні пари можна утворювати з будь-яких двох металів, які контактують між собою і занурені в розчин електроліту. При цьому швидкість кородування активнішого металу значно збільшується, а менш активний метал зовсім не кородує. На ньому відбувається лише відновлення іонів водню тими електронами, що прибувають з поверхні активнішого металу.
Електрохімічна корозія металів виникає не тільки в присутності сильних, а й слабких електролітів і навіть тонкого шару вологи, якою вкриваються металічні конструкції в атмосфері повітря. Будучи дуже слабким електролітом, вода теж дисоціює, утворюючи іони Н+ і ОН−, хоч і в незначній кількості. Але при розчиненні в ній різних солей, що містяться в повітрі у вигляді пилу, і газів - CO2, SO2 і ін., концентрація різних іонів, у тому числі й іонів водню, збільшується і стає достатньою для виникнення і перебігу електрохімічної корозії.
Електрохімічна корозія у присутності вологи
Схема корозії заліза в контакті з міддюПрикладом електрохімічної корозії в присутності вологи, повітря є процес кородування залізної конструкції з мідними заклепками. Коли така конструкція вкривається шаром вологи (розчином електроліту), то залізні і мідні ділянки її поверхні утворюють гальванічні пари. При цьому атоми заліза як більш активного металу переходять у розчин у вигляді двовалентних іонів Fe2+, а втрачені ними валентні електрони переміщаються на мідь і там приєднуються катіонами водню, відновлюючи їх до вільного водню.
Гальванічні пари на кородуючій поверхні можуть утворюватись не лише при контакті двох металів з великими поверхнями, а й при контакті основного металу з нерозчинними в ньому домішками інших металів, які завжди містяться в технічних металах. У таких випадках на кородуючій поверхні металу утворюється безліч невеликих за розмірами так званих мікрогальванічних пар, роботою яких обумовлюється електрохімічне кородування основного металу.
Як при контакті двох різних металів (утворенні макрогальванічних пар), так і при наявності в основному металі нерозчинних домішок інших металів (утворенні мікрогальванічних пар) потік електронів (електричного струму) спрямований від більш активного металу до менш активного. Більш активний метал кородує (руйнується), а менш активний не кородує. На ньому лише відновлюються іони водню тими електронами, що прибувають від атомів
Наслідки локальної ерозійної корозії на рухомій частині водопровідної поворотної засувки «Батерфляй» після 5 років використанняактивнішого металу.
Швидкість електрохімічної корозії тим більша, чим більше утворюється на кородуючій поверхні гальванічних пар, тобто чим більше є контактів основного металу з іншими менш активними металами або чим більше він забруднений домішками менш активних металів. Чим чистіший метал, тим менше він піддається корозії, а дуже чисті метали майже зовсім не кородують.
Швидкість електрохімічної корозії залежить також від різниці активності металів, що утворюють гальванічні пари. Чим більш віддалені ці метали один від одного в електрохімічному ряді напруг, тим більша швидкість корозії. На швидкість корозії впливає також електроліт і температура. Чим сильніший електроліт, тобто чим більше міститься в ньому іонів, зокрема іонів водню, і чим вища температура, тим більша швидкість електрохімічної корозії
Корозія металів завдає величезних збитків господарству. Внаслідок корозійного руйнування втрачається близько 10 % щорічного видобутку металів. Тому заходам боротьби з корозією приділяється значна увага. Способів боротьби з корозією багато і вони досить різноманітні.
Одним з найпоширеніших способів боротьби з корозією є покриття металу (головним чином заліза) масляними фарбами. Захисна дія фарби ґрунтується на тому, що оліфа, піддаючись полімеризації, утворює на поверхні металу суцільну еластичну плівку, яка ізолює метал від дії атмосферних хімічних агентів. Інколи для захисту металу від корозії (наприклад, алюмінію і деяких сталевих виробів) штучно створюють оксидну плівку обробкою їх поверхні сильними окисниками.
Використовуються також стійкі до абразивного зношування ліофобні поліуретанові покриття.
Схема корозії оцинкованого залізаЗначного поширення одержав також спосіб покриття одного металу іншим. Наприклад, дахове залізо покривають тонким шаром цинку. З цією метою залізні листи занурюють на короткий час у розплавлений цинк. Сам по собі цинк в атмосфері повітря не піддається корозії, оскільки на його поверхні утворюється досить стійка захисна оксидна плівка ZnO. При пошкодженні цинкового шару (тріщини, подряпини тощо) цинк з залізом у присутності вологи повітря утворює гальванічну пару. При цьому електрохімічному корозійному руйнуванню піддається цинк як активніший метал, а залізо не руйнується доти, поки не буде зруйнований весь захисний шар цинку. Конкуренцію традиційному цинкуванню складає покриття сталевих листів алюцинком.
На цьому ж принципі ґрунтується і так званий протекторний спосіб захисту металів від корозії. Суть цього способу полягає в тому, що металеву конструкцію сполучають металічним провідником з активнішим металом, який піддається корозійному руйнуванню. Наприклад, у парові котли інколи вводять листи цинку, які сполучають залізними стержнями з стінками котла. При цьому утворюється в середовищі води гальванічна пара, внаслідок чого цинк, як активніший метал руйнується, а залізні стінки котла не піддаються корозії. Так само можна захищати і підземні трубопроводи.
Схема корозії луженого залізаІнколи металеві вироби вкривають захисним шаром менш активного металу. Прикладом цього може служити біла жерсть, з якої виробляють консервні банки. Її одержують зануренням на короткий час залізних листів у розплавлене олово. Олово дуже добре захищає залізо доти, поки його шар суцільний. Але коли захисний шар пошкоджується і залізо приходить у дотик з агресивним середовищем, воно з оловом утворює гальванічну пару і залізо як активніший метал піддається корозійному руйнуванню. При цьому залізо кородує значно скоріше, ніж у тому випадку, коли воно не вкрите шаром олова.
Досить поширеним є гальванічний спосіб покриття одного металу іншим (шляхом електролізу). Цим способом покривають нікелем (нікелювання), хромом (хромування), міддю (міднення), сріблом (сріблення), золотом (золочення) і іншими металами. Гальванічним способом можна наносити дуже тонкий і рівномірний шар захисного металу. Гальванічні покриття не тільки захищають металічні вироби від корозії, а й надають їм гарного зовнішнього вигляду.
Для боротьби з корозією в середовищі рідин застосовують спеціальні добавки, так звані інгібітори, тобто сповільнювачі корозії. Інгібіторами можуть бути різні речовини: хромат натрію, дихромат калію, фосфат натрію тощо, а також желатин, клей та інші органічні речовини. Інгібітори сприяють утворенню на кородуючій поверхні металу міцної захисної плівки, внаслідок чого швидкість корозії може зменшуватись у десятки і сотні разів. Особливо важливу роль відіграють інгібітори при взаємодії металів з кислотами. Так, наприклад, коли додати деякі інгібітори до хлоридної кислоти, то її можна зберігати в сталевій тарі, хоч хлоридна кислота з залізом взагалі реагує досить жваво.
Крім того, останнім часом стали широко застосовувати сплави з високими антикорозійними властивостями. Такі сплави одержують шляхом добавок до основного металу інших металів - нікелю, кобальту, хрому і ін. Прикладом антикорозійних сплавів може служити сталь із вмістом 15-20 % Со. Така сталь цілком стійка до дії кислот. З неї виготовляють різну хімічну апаратуру.
Тема Діелектрики
Діелектрики це - речовини (матеріал), що погано проводить електричний струм.
В техніці використовують тверді, рідкі та газоподібні діелектрики.
Тверді діелектрики це фарфор, гума, скло і т.д.
В якості рідких діелектриків використовують трансформаторне, конденсаторне, кабельне масло.
Найчастіше в якості газоподібного діелектрика використовують повітря.
Тіла виготовлені з діелектрика називають ізоляторами.
Молекула діелектрика складається з позитивних і негативних йонів, а також електронів. Вільних електронів в діелектриках дуже мало.
На практиці діелектрики не вважається абсолютним ізолятором. Зазвичай елементарні заряди молекули діелектрика знаходяться в хаотичному тепловому коливальному русі біля центрів рівноваги. Якщо включити діелектрик в коло постійної напруги, то під дією сил електричного поля елементарні заряди молекул діелектрика перемістяться в напрямку діючих на них сил. В результаті зміщення зарядів в середині діелектрика в колі виникає короткочасний струм поляризації. Через дуже короткий час цей струм зникає.
Струм витоку цей струм може протікати через діелектрик довгий час. Діелектрик завжди має йони та вільні електрони, хоча їх дуже мало. Під дією електричного поля вони почнуть переміщатись. Величина струму витоку значно більша ніж струму поляризації. Проходячи через діелектрик струм витоку виділяє тепло.
Якщо включити діелектрик в коло змінної напруги то процес поляризації буде проходити періодично спочатку в одному напрямку, а потім в іншому й в колі виникне змінний струм. Процес який безперервно повторюється потребує затрат енергії . Періодичне переміщення в матеріалі діелектрика йонів та вільних електронів провокує виникнення струму витоку.
Характеристики діелектрика:
- питомий опір
- діелектрична проникність
- кут діелектричних втрат
- електрична міцність
Питомий опір
Технічний діелектрик не являється абсолютним ізолятором. Тому під час роботи він пропускає електричний струм. Величина цього струму дуже мала по відношенню до робочого струму, що протікає по струмоведучим частинам. Струм має два шляхи для протікання через діелектрик (по об'єму) або через його поверхню. Загальний струм витоку Iу дорівнює сумі струмів, що проходить через діелектрик і струму, що проходить по поверхні діелектрика Iпов .
Протікаючи двома шляхами струм долає опір діелектрика rоб та поверхневий опір діелектрика
За одиницю об'ємного опору приймають опір вирізаного з даного матеріалу кубика з ребром 1см, якщо струм проходить через дві його протилежні грані Об'ємний опір вимірюють в омсантиметрах і визначається
Опір одиниці поверхні діелектрика називають питомим поверхневим опором позначається ƥS і вимірюється в омах.
За одиницю поверхневого опору приймають опір прямокутника (будь-яких розмірів), виділеного на поверхні матеріалу якщо струм проходить через дві протилежні сторони цього прямокутника
Питомий опір діелектрика залежить від стану речовини (твердий, рідкий, газоподібний), складу діелектрика, вологості, температури навколишнього середовища.
Діелектрична проникність
Величина що характеризує ємкість діелектрика поміщеного між обкладками конденсатора. Ємність конденсатора залежить від величини площини обкладок, відстанню між обкладками або товщини діелектрика, а також матеріалу діелектрика.
Кут діелектричних втрат
В ідеальному діелектрику ємкісний струм випереджає по фазі напругу на 90°. В реальному діелектрику цей кут менше 90° . На зменшення кута має вплив струм витоку, який називається струмом провідності. Різниця між 90° і кутом зсуву між напругою і струмом що проходить в колі з реальним діелектриком, називається кутом діелектричних втрат позначається δ, а тангенс кута tg δ.
Діелектричні втрати пропорційні квадрату напруги, частоті змінного струму, ємності конденсатору і тангенсу кута діелектричних втрат.
Отже, чим більше tg δ тим більші втрати енергії в діелектрику, тим гірше матеріал діелектрика. Матеріали з великим tg δ (0.08-0.1) вважаються поганими діелектриками, матеріали з малим tg δ (0.0001) вважаються хорошими діелектриками.
Електрична міцність
Властивість діелектрика витримувати ту чи іншу електричну напругу визначається електричною міцністю діелектрика.
Електричною міцністю, Eпр називається середня напруженість електричного поля, при якій відбувається електричний пробій. Напруга, при якому відбувається електричний пробій, називають «пробивною напругою», Uпр.
Пробій твердого діелектрика
Розрізняють два види пробою твердого діелектрика:
- тепловий
- електричний
Електричний пробій - це руйнування структури речовини під дією електричного поля.. В слабому електричному полі електричні заряди пружно зміщуються, визиваючи поляризацію діелектрика. Якщо напруженість поля досягає величини пробивної відбувається зрив заряжених частинок з початкового положення що й призводить до пробою.
Тепловий пробій - пробій, спричинений втратою матеріалом електроізоляційних властивостей, пов'язаної з надмірним зростанням крізної електропровідності або діелектричних втрат від розігрівання в електричному полі до відповідних температур.
Процес нагрів постійно збільшується поки матеріал не нагріється настільки до коли не відбудеться його руйнування.
Пробій газоподібного діелектрика
Пробій газоподібного діелектрика визваний створенням і рухом йонів в газоподібному середовищі при високому значенні напруженості електричного поля. В деякий момент швидкий рух йонів призводить до їх зіткнень з нейтральними молекулами газу і створенню нових йонів. Це явище супроводжується різким збільшенням числа йонів в наслідок чого опір газу зменшується, наступає пробій газоподібного діелектрика.
Пробій рідкого діелектрика
На пробивну міцність рідких діелектриків впливає волога, гази, механічні та хімічні домішки. Пробій рідких діелектриків виникає в наслідок перегріву рідини і руйнуванню їх молекул.
Тема : Чавун
Чаву́н - сплав заліза з вуглецем (понад 2 % вуглецю за масою) та іншими елементами, який характеризується наявністю евтектичного перетворення: нестабільного (цементитного) або стабільного (графітного)[1]. Чисте залізо має обмежене застосування. В техніці зазвичай використовують сплави заліза з вуглецем, які поділяють на сталі і чавуни. Сталі містять до 2 % вуглецю, а чавуни - від 2,14 до 6 % вуглецю.
У чавуні, окрім заліза і вуглецю, завжди є низка інших домішок: кремній, марганець, фосфор, сірка та інші, які потрапляють у чавун або з сировини і палива при його виробництві, або додаються спеціально. Домішки, знаходячись у чавуні навіть у незначній кількості - сотих частках відсотка - можуть значною мірою впливати на властивості чавуну.
За застосуванням чавуни поділяються на переробні, що використовуються для переробки на сталь, ливарні, що використовуються для лиття, та спеціальні чавуни - феросплави, що використовуються як добавки при виробництві сталі.
Порівняно зі сталями чавуни мають нижчі механічні властивості, але значно кращі технологічні (ливарні, оброблюваність різанням, антифрикційні властивості, зносостійкість). Це зумовлює широке використання чавуну для виготовлення багатьох деталей у різних галузях машинобудування.[2
Чавун не піддається куванню через свою ламкість і спочатку його вважали небажаним відходом виробництва, утворення якого зменшувало вихід придатного продукту - криці. Перший європейський чавун виплавляли на теренах Священної Римської імперії наприкінці XIV ст., майже одночасно в австрійській Штирії та Північній Італії. [джерело?] Лише згодом з чавуну навчилися робити відливки і почали використовувати його в ливарництві. З нього виготовляли посуд, гармати, прилади для камінів тощо. Ще пізніше навчилися повторно переплавляти його з рудою у кричному горні й отримувати з нього ковке залізо. При цьому було помічено, що виплавка напівпродукту - чавуну - в одному агрегаті і подальша його переробка на ковке залізо в іншому агрегаті має велику економічну ефективність порівняно з прямим сиродутним процесом отримання заліза у сиродутних горнах. Витрата деревного вугілля скоротилася вдвічі, вихід заліза збільшився у півтора раза, зросла продуктивність виробництва заліза. Після цього металурги почали будувати доменні печі, єдиним продуктом яких був лише рідкий чавун. Весь подальший розвиток металургії заліза відбувався як вдосконалення цього двоступеневого способу виробництва сталі[
Основним способом отримання чавуну є доменне виробництво, одержаний в такий спосіб чавун називається доменним чавуном. У відносно незначній кількості також одержують так званий синтетичний чавун в електричних печах зі сталевих відходів з додаванням карбюризаторів.
Чавун при доменному виробництві одержують із залізорудної сировини (виготовлених з залізної руди окатків або агломерату) в спеціальних вертикальних печах, які називаються доменними печами, або домнами. Доменні печі - це складні споруди з вогнетривкого матеріалу із зовнішньою сталевою обшивкою. Висота сучасних доменних печей сягає 30 м, а внутрішній діаметр у найширшій частині - до 13 м.
Добова продуктивність доменної печі, в залежності від її корисного об'єму, може становити від 2000 т до 10000 т чавуну на добу. Доменна піч після її пуску працює безперервно 5-6 років, а то й і до 10 років. Потім її ремонтують і знову пускають у роботу.
Операції з підготовки шихти, завантаження її в домну, випуску чавуну і шлаку механізовані. Шихту завантажують через верхню частину домни (колошник). Спочатку засипають шар коксу, потім шар суміші руди з коксом і флюсами, потім знову шар коксу і т. д. Кокс служить джерелом тепла для підтримання потрібної температури в домні і для одержання відновника - монооксиду вуглецю CO, а флюси (найчастіше вапняк CaCO3) - для перетворення пустої породи (SiO2, глини тощо) в легкоплавкі сполуки - шлак.
Горіння коксу підтримується вдуванням у нижню частину домни (горно) попередньо нагрітого до 800-1000°С повітря. Найвища температура (до 2000 °C) досягається в нижній частині домни у зоні горіння коксу, а найнижча (до 200 °C) - у найвищій частині - на колошнику.
В результаті згоряння коксу в нижній частині домни утворюється діоксид вуглецю CO2, який, піднімаючись вгору і проходячи крізь шар розжареного коксу, перетворюється в монооксид вуглецю CO:
- Монооксид вуглецю як сильний відновник, проходячи через шари шихти, відновлює оксиди заліза (залізну руду). Причому ступінь відновлення залежить від температури. При температурі 200-500°С Fe2O3 відновлюється до Fe3O4:
- при 600 °C Fe3O4 відновлюється до FeO:
Вище 700 °C FeO відновлюється до вільного заліза, яке утворюється у твердому стані (так зване губчасте залізо):
При вищих температурах у процесах відновлення оксидів заліза бере участь, крім монооксиду вуглецю, і вільний вуглець, що міститься у коксі:
Відновлення заліза з руди закінчується при температурі 1000-1100 °C. При цій температурі частково відновлюються й інші елементи зі сполук, що входять до складу руди як домішки, - манган, силіцій, фосфор тощо.
Утворюване губчасте залізо частково реагує з розжареним вуглецем і утворює хімічну сполуку - карбід заліза Fe3C:
Ця сполука не підлягає правилам звичайної валентності. Карбід заліза Fe3C називають цементитом. Цементит в залізі утворює розчин, який називають чавуном.
Температура плавлення чавуну нижча, ніж чистого заліза, і залежить від вмісту вуглецю. Температура плавлення заліза 1538 °C, а чавун із вмістом вуглецю 4,3 % плавиться при 1130 °C. Це найнижча температура плавлення чавуну. Доменний чавун містить звичайно 3-4 % вуглецю і плавиться при 1200-1300°С.
У розплавленому чавуні легко розчиняються силіцій, манган, фосфор, сірка й інші домішки, які й залишаються в чавуні. Розплавлений чавун струмками та краплинами стікає в найнижчу частину домни (горно), звідки його періодично випускають. Пуста порода, що міститься в залізній руді, видаляється у вигляді шлаку. Шлак утворюється за такими хімічними рівняннями. Вапняк, що додається до шихти як флюс, при 800-1000°С розкладається на оксид кальцію CaO і діоксид вуглецю CO2. Утворюваний CaO як оксид з основними властивостями взаємодіє з силіцієвим ангідридом SiO2 й амфотерним оксидом алюмінію Al2O3 пустої породи з утворенням відносно легкоплавких силікату кальцію і алюмінату кальцію:
- CaCO3 = CaO + CO2 ↑
- CaO + SiO2 = CaSiO3
- CaO + Al2O3 = Ca(AlO2)2
Шлак плавиться при температурі близько 1100 °C і стікає в горно. Оскільки шлак легший ніж чавун, він збирається над розплавленим чавуном і захищає його від окиснення. Розплавлений шлак, як і чавун, періодично випускають з домни.
Чавуни, які виплавляють у доменних печах поділяють на:
• переробні, які використовуються для виробництва сталі у кисневих конверторах, електропечах, мартенівських печах;
• ливарні, які використовуються для одержання виливків у ливарних цехах машинобудівних чи ливарних заводів. Частка цих чавунів зменшується й не перевищує 10 %.
Широке застосування чавунів у машинобудуванні пояснюється порівняно невеликою вартістю й добрими технологічними властивостями чавунів - високою рідкотекучістю й незначною (~ 1 %) усадкою під час кристалізації та наступного охолодження, здатністю легко оброблятися різанням, можливістю зміни властивостей термообробкою й легуванням. Найкращі ливарні властивості мають евтектичні чавуни, оскільки в них менший температурний інтервал кристалізації.
Залежно від хімічного складу та умов кристалізації карбон в чавунах може кристалізуватися як у вільному стані у вигляді графіту, так і у вигляді сполуки з ферумом - цементиту Fe3C. Залежно від стану карбону в чавунах, їх класифікують на білі та машинобудівні чавуни.
У білих чавунах весь вуглець перебуває в цементиті. Завдяки цементиту такі чавуни мають білий блискучий злам, від кольору якого і походить їх назва. Структуру білих чавунів у рівноважному стані творять дві фази - ферит та цементит. Завдяки твердому цементиту, кількість якого збільшується зі збільшенням вмісту карбону, білі чавуни мають високу твердість (450...550 НВ), дуже крихкі, практично не підлягають різанню лезовим інструментом. Тому в машинобудуванні білі чавуни мають обмежене застосування. Їх використовують тільки як зносотривкий матеріал для відливання деталей шламових насосів, гідроциклонів, доменних печей, кульових млинів для розмелювання руд. З виливків білого чавуну отримують ковкі чавуни.
Машинобудівні чавуни відливають за таких умов, що забезпечують повну або часткову графітизацію - виділення графіту. Тому властивості цих чавунів визначаються не тільки структурою металевої основи (ферит, перліт), але й формою, розмірами, кількістю й характером розташування в основі графітних виділень. Виливки з цих чавунів добре обробляються різанням й не підлягають обробці тиском.
Виливки з чавунів з пластинчастим графітом одержують безпосередньо заливанням розплавленого металу в ливарні форми. Графіт під час кристалізації формується у вигляді вигнутих пелюсток, пластинок. Такий графіт називають пластинчастим. Наявність у структурі вільного графіту зумовлює матовий сірий колір зламу, від якого походить інша назва цих чавунів - сірі чавуни.
Пластинчастий графіт порушує суцільність металевої основи, створює на краях пелюсток зони сильної концентрації напружень, і тому сірі чавуни характеризуються низькою міцністю на розтягування, згинання, скручування й дуже низькою пластичністю. Максимальна границя міцності на розтягування цих чавунів не перевищує 450 МПа. За ГОСТ 1412-85 марки чавунів з пластинчастим графітом позначаються літерами СЧ (С - сірий, Ч - чавун) і числами, які відповідають мінімально допустимим значенням границі міцності на розтягування σв у МПа·10−1 (наприклад СЧ 35).
Їх рекомендується використовувати для виробів, що підлягають переважно стисканню. Та завдяки пластинчастому графіту в сірих чавунах вдало поєднуються добрі антифрикційні властивості, зносотривкість, здатність гасити вібрації та мала чутливість до концентраторів напружень. З них відливають різні деталі для машин, махові колеса, шківи, плити, станини та столи верстатів, корпуси електродвигунів тощо.
Чавуни з кулястим графітом, як порівняти з іншими чавунами, мають вищу пластичність, ударну в'язкість й одночасно міцність (за що їх називають високоміцними), що насамперед зумовлено кулястою формою графіту, яка забезпечується сфероїдизуванням. Сфероїдизування полягає у введенні в розплав малих додатків (0,03...0,06 %) сфероїдизувальних металів - магнію, церію, кальцію, під дією яких графіт кристалізується у формі кульок, які мінімально послаблюють металеву основу чавуну.
За ДСТУ 3925-99 умовне позначення марки містить літери ВЧ (В - високоміцний, Ч - чавун), цифрове позначення мінімального допустимого значення границі міцності на розтягування σв у МПа та через дефіс - відносне видовження δ у відсотках. Максимальну міцність має чавун марки ВЧ 1000-2.
З них виготовляють розподільні й колінчасті вали, блок-картери, головки циліндрів, шатуни, поршні, поршневі кільця в автомобілебудуванні; супорти, шпинделі, зубчасті колеса у верстатобудуванні; плити гідравлічних пресів, напрямні та плунжери ливарних машин, напірних труб для води, нафти, агресивних рідинних та газових середовищ.
Чавуни з вермикулярним графітом також одержують модифікуванням маґнію, тільки в меншій кількості, що зумовлює утворення вермикулярного графіту у формі графітних пелюсток із заокругленими краями, менших розмірів та грубіших як порівняти з пластинчастим графітом. Марки цих чавунів позначають подібно як і високоміцних, наприклад ЧВГ 400-4.
За однакової структури металевої основи механічні властивості чавунів з вермикулярним графітом проміжні між властивостями сірих з пластинчастим та високоміцних з кулястим графітом. Вони переважають сірі чавуни за пластичністю, ударною в'язкістю, корозійною тривкістю, герметичністю, а високоміцні - за здатністю гасити вібрації, оброблятися різанням, меншою вартістю (дешевші на 20...30 %).
Ковкі чавуни одержують шляхом тривалого графітизувального відпалу виливків з білого маловуглецевого (2,4...2,9 % С) чавуну. Відпал при високій температурі спричиняє розкладання метастабільного цементиту з утворенням графіту компактної форми з кошлатими краями, так званого графіту відпалу. За впливом на механічні властивості чавуну такий графіт займає проміжне положення між пластинчастим і кулястим графітом. Структура металевої основи ковких чавунів - від феритної до перлітної - залежить від хімічного складу та режиму термічної обробки виливків з білого чавуну.
За ГОСТ 1215-79 марки ковких чавунів позначають літерами КЧ (К - ковкий, Ч - чавун), після яких вказуються мінімально допустимі значення границі міцності на розтяг у МПа·10−1 й через дефіс - відносного видовження у відсотках (наприклад, КЧ 30-6).
Істотним недоліком виробів з ковких чавунів є висока вартість внаслідок тривалого високотемпературного відпалу та обмеження розмірів.
Тема: Сталь
Ста́ль[ - сплав заліза з вуглецем, який містить від 0.02 до 2,14 % вуглецю і домішок (кремній, марганець, сірка, фосфор та гази).
За вмістом вуглецю сталі поділяють на дві групи:
- м'яка сталь, або технічне залізо (містить до 0,3 % вуглецю)
- тверда сталь (містить від 0,3 до 2,14 % вуглецю)
Сталь отримано з чавуну у II ст. до нашої ери китайськими металургами. Спосіб отримав назву «сто очищувань» і полягав у багаторазовому інтенсивному обдуванні повітрям розплавленого чавуну під час його перемішування. Це призводило до зменшення частки вуглецю в металі й наближення його до властивостей сталі.
У Європі подібний спосіб пудлінгування освоєно лише у другій половині XVIII ст. (патенти братів Томаса і Джорджа Кранеджі та Г. Корта).
Суть процесу переробляння чавуну на сталь полягає у зменшуванні до потрібної концентрації вмісту вуглецю і шкідливих домішок - фосфору і сірки, які роблять сталь крихкою і ламкою.
Залежно від способу окиснювання вуглецю є різні способи переробляння чавуну на сталь: конверторний, мартенівський і електротермічний. До фінансової кризи в 2008 році Україна залишалася однією з небагатьох країн, де широко використовували мартенівський спосіб виплавляння сталі, що є досить енергозатратним та екологічно шкідливим. Наразі більшість мартенівських печей в Україні виведено з експлуатації, а ті що лишилися, невдовзі також будуть закриті. Мартенівський спосіб виплавляння сталі не витримує конкуренції, що загострилася на світових ринках після 2008 р. Таким чином зараз в Україні, як і в усьому світі, переважну більшість сталевої продукції виробляють конвертерним способом. Україна станом на 2008 р. займає п'яте місце у світі за обсягами експорту сталі, 76,46 % сталі, що її виробляють на світовому ринку, припадає на десять провідних країн.
Станом на 2016 р. Україна входить у десятку світових виробників сталі .
Киснево-конверторний спосіб одержання сталі
За цим способом окиснювання надлишку вуглецю та інших домішок чавуну проводять киснем повітря, який продувають крізь розплавлений чавун під тиском у спеціальних печах - конверторах. Конвертор - це грушоподібна сталева піч, обфутерована всередині вогнетривкою цеглою. Він може повертатися навколо своєї осі. Місткість конвертора 50-60 т сталі. Матеріалом його футеровання служить або динас (до складу якого входять головним чином SiO2; що має кислотні властивості), або доломітна маса (суміш CaO і MgO, які одержують з доломіту MgCO3 • CaCO3. Ця маса має основні властивості. Залежно від матеріалу футеровання печі конверторний спосіб поділяють на два види: бессемерівський і томасівський.
Бессемерівським способом переробляють чавуни, які містять мало фосфору і сірки й багаті на силіцій (не менше 2 %). Такі чавуни можуть називатися бесемерівськими чавунами. При продуванні кисню спочатку окиснюється силіцій з виділенням значної кількості тепла. Внаслідок цього початкова температура чавуну приблизно з 1300 °C швидко піднімається до 1500-1600 °С. Вигоряння 1 % Si обумовлює підвищення температури на 200 °C.
Близько 1500 °C починається інтенсивне вигоряння вуглецю. Разом з ним інтенсивно окиснюється й залізо, особливо під кінець вигоряння силіцію і вуглецю:
- Si + O2 = SiO2
- 2C + O2 = 2CO ↑
- 2Fe + O2 = 2FeO
Монооксид заліза FeO, що утворюється, добре розчиняється в розплавленому чавуні і частково переходить у сталь, а частково реагує з SiO2 й у вигляді силікату заліза FeSiO3 переходить у шлак:
- FeO + SiO2 = FeSiO3
Фосфор повністю переходить з чавуну в сталь, бо P2O5 при надлишку SiO2 не може реагувати з основними оксидами, оскільки SiO2 з останніми реагує більш енергійно. Тому фосфористі чавуни переробляти в сталь цим способом не можна.
Усі процеси в конверторі йдуть швидко - протягом 10- 20 хвилин, бо кисень повітря, що продувається через чавун, реагує з відповідними речовинами відразу по всьому об'єму металу. При продуванні повітря, збагаченого киснем, процеси прискорюються.
Монооксид вуглецю CO, що утворюється при вигорянні вуглецю, пробулькуючи вгору, згоряє там, утворюючи над горловиною конвертора факел світлого полум'я, який в міру вигоряння вуглецю зменшується, а потім зовсім зникає, що і служить ознакою закінчення процесу.
Одержувана при цьому сталь містить значні кількості розчиненого монооксиду заліза FeO, який сильно знижує якість сталі. Тому перед розливною сталь треба обов'язково розкиснювати за допомогою різних розкисників - феросиліцію, феромангану або алюмінію:
- 2FeO + Si =2Fe + SiO2
- FeO + Mn = Fe + MnO
- 3FeO + 2Al = 3Fe + Al2O3
Монооксид мангана MnO як основний оксид реагує з SiO2 і утворює силікат мангана MnSiO3, який переходить у шлак. Оксид алюмінію як нерозчинна при цих умовах речовина теж спливає наверх і переходить у шлак. Незважаючи на простоту і велику продуктивність, бессемерівський спосіб тепер не досить поширений, оскільки він має ряд істотних недоліків. Так, чавун для бессемерівського способу повинен бути з найменшим вмістом фосфору і сірки, що далеко не завжди можливо. При цьому способі відбувається дуже велике вигоряння металу, і вихід сталі становить лише 90 % від маси чавуну, а також витрачається багато розкисників. Серйозним недоліком є неможливість регулювання хімічного складу сталі.
Бесемерівська сталь містить звичайно менше 0,2 % вуглецю і використовується як технічне залізо для виробництва дроту, болтів, дахового заліза тощо.
Томасівським способом переробляють чавун з великим вмістом фосфору (до 2 % і більше). Такий чавун називають томасівським чавуном. Основна відмінність цього способу від бессемерівського полягає в тому, що футеровку конвертора роблять з оксидів магнію і кальцію (які одержують з доломіту MgCO3 • CaCO3). Крім того, до чавуну додають ще до 15 % CaO. Внаслідок цього шлакоутворюючі речовини містять значний надлишок оксидів з основними властивостями.
У цих умовах фосфатний ангідрид P2O5, який виникає при згорянні фосфору, взаємодіє з надлишком CaO з утворенням фосфату кальцію, що переходить у шлак:
- 4P + 5O2 = 2P2O5
- P2O5 + 3CaO = Ca3(PO4)2
Реакція горіння фосфору є одним з головних джерел тепла при цьому способі. При згорянні 1 % фосфору температура конвертора піднімається на 150 °C.
Сірка виділяється в шлак у вигляді нерозчинного в розплавленій сталі сульфіду кальцію CaS, який утворюється внаслідок взаємодії розчинного FeS з CaO за реакцією:
- FeS + CaO = FeO + CaS
Усі останні процеси відбуваються так само, як і при бессемерівському способі. Недоліки томасівського способу такі ж, як і бессемерівського. Томасівська сталь також маловуглецева і використовується як технічне залізо для виробництва дроту, дахового заліза тощо.
Мартенівський спосіб відрізняється від конверторного тим, що випалювання надлишку вуглецю в чавуні відбувається за рахунок не лише кисню повітря, а й кисню оксидів заліза, які додаються у вигляді залізної руди та іржавого залізного брухту.
Мартенівська піч складається з плавильної ванни, перекритої склепінням з вогнетривкої цегли, і особливих камер регенераторів для попереднього підогріву повітря і горючого газу. Регенератори заповнені насадкою з вогнетривкої цегли. Коли перші два регенератори нагріваються пічними газами, горючий газ і повітря вдуваються в піч через розжарені третій і четвертий регенератор. Через деякий час, коли перші два регенератори нагріваються, потік газів спрямовують у протилежному напрямку і т. д.
Плавильні ванни потужних мартенівських печей мають довжину до 16 м, ширину до 6 м і висоту понад 1 м. Місткість таких ванн досягає 500 т сталі. В плавильну ванну завантажують залізний брухт і залізну руду. До шихти додають також вапняк як флюс. Температура печі підтримується при 1600-1650 °C і вище. Вигоряння вуглецю і домішок чавуну в перший період плавки відбувається головним чином за рахунок надлишку кисню в горючій суміші за тими ж реакціями, що і в конверторі, а коли над розплавленим чавуном утвориться шар шлаку - за рахунок оксидів заліза
- 4Fe2O3 + 6Si = 8Fe + 6SiO2
- 2Fe2O3 + 6Mn = 4Fe + 6MnO
- Fe2O3 + 3C = 2Fe + 3CO ↑
- 5Fe2O3 + 2P = 10FeO + P2O5
- FeO + С = Fe + CO ↑
Внаслідок взаємодії основних і кислотних оксидів утворюються силікати і фосфати, які переходять у шлак. Сірка теж переходить у шлак у вигляді сульфіду кальцію:
- MnO + SiO2 = MnSiO3
- 3CaO + P2O5 = Ca3(PO4)2
- FeS + CaO = FeO + CaS
Мартенівські печі, як і конвертори, працюють періодично. Після розливки сталі піч знову завантажують шихтою і т. д. Процес переробки чавуну в сталь у мартенах відбувається відносно повільно протягом 6-7 годин. На відміну від конвертора в мартенах можна легко регулювати хімічний склад сталі, додаючи до чавуну залізний брухт і руду в тій чи іншій пропорції. Перед закінченням плавки нагрівання печі припиняють, зливають шлак, а потім додають розкисники. В мартенах можна одержувати і леговану сталь. Для цього в кінці плавки додають до сталі відповідні метали або сплави.
Електротермічний спосіб має перед мартенівським і особливо конверторним цілий ряд переваг. Цей спосіб дозволяє одержувати сталь дуже високої якості і точно регулювати її хімічний склад. Доступ повітря в електропіч незначний, тому значно менше утворюється монооксиду заліза FeO, що забруднює сталь і знижує її властивості. Температура в електропечі - не нижче 2000 °C. Це дозволяє проводити плавку сталі на сильно основних шлаках (які важко плавляться), при яких повніше видаляється фосфор і сірка. Крім того, завдяки дуже високій температурі в електропечах можна легувати сталь тугоплавкими металами - молібденом і вольфрамом. Але в електропечах витрачається дуже багато електроенергії - до 800 кВт•год на 1 т сталі. Тому цей спосіб застосовують лише для одержання високоякісної спецсталі.
Електропечі бувають різної місткості - від 0,5 до 180 т. Футеровку печі роблять звичайно основною (з CaO і MgO). Склад шихти може бути різний. Інколи вона складається на 90 % із залізного брухту і на 10 % із чавуну, інколи у ній переважає чавун з добавками у певній пропорції залізної руди і залізного брухту. До шихти додають також вапняк або вапно як флюс. Хімічні процеси при виплавці сталі в електропечах ті ж самі, що і в мартенах.
Сталі класифікують за різними ознаками:
- хімічним складом:
- вуглецеві:
- маловуглецеві (до 0,25 % С);
- середньовуглецеві (0,3...0,55 % С);
- високовуглецеві (0,6...0,85 % С;)
- леговані (залежно від того, які елементи введено до їхнього складу):
- хромисті;
- марганцевисті;
- хроммарганцевисті;
- хромнікелеві;
- вуглецеві:
- якістю (якість сталі залежить від металургійного процесу виробництва; якість визначається вмістом в сталі газів кисню, водню, азоту та шкідливих домішок сірки і фосфору):
- звичайної якості;
- якісні;
- високоякісні;
- особливо високоякісні.
- способом розкиснення:
- спокійні;
- напівспокійні;
- киплячі (кипляча сталь - не повністю розкиснена в печі. Виділення газів відбувається й при затвердінні виливка, тому в ньому утворюється велика кількість розосереджених газових бульбашок. Вони зникають при подальшій гарячій прокатці. Найдешевша.)
- призначенням:
- конструкційні;
- інструментальні;
- особливих властивостей.
Властивості сталей залежать від їх складу і структури, які формуються присутністю та процентним вмістом наступних складових.
Карбон - складова, із збільшенням вмісту якої у сталі, збільшується її твердість і міцність, при цьому пластичність зменшується.
Кремній і марганець у межах (0,5...0,7 %) істотного впливу на властивість сталі не роблять.
Сірка є шкідливою домішкою, утворює з залізом хімічну сполуку FeS (сірчисте залізо). Сірчисте залізо у сталях утворює із залізом евтектику з температурою плавлення 1258 К, яка обумовлює червоноламкість матеріалу при обробці тиском з підігріванням. Вказана евтектика при термічній обробці розплавляється, у результаті чого між зернами втрачається зв'язок з утворенням тріщин. Крім цього, сірка зменшує пластичність і міцність сталі, стійкість до зношування та корозійну стійкість.
Фосфор надає сталі холодноламкості (крихкість при понижених температурах). Це пояснюється тим, що фосфор спричиняє сильну внутрішньокристалічну ліквацію.
Ферит - залізо з об'ємноцентрованою кристалічною ґраткою і сплави на його основі є фазою м'якою і пластичною.
Цементит - карбід заліза, хімічна сполука з формулою Fe3C, навпаки, надає сталі твердості та крихкості.
Перліт - евтектоїдна суміш двох фаз - фериту і цементиту, містить 1/8 цементиту і тому має підвищену міцність і твердість порівняно з феритом. Тому доевтектоїдні сталі набагато пластичніші, ніж заевтектоїдні.
Для покращення механічних та інших характеристик сталей застосовують легування. Головна мета легування переважної більшості сталей - підвищення міцності за рахунок розчинення легуючих елементів у ферит та аустеніті, утворення карбідів та збільшення прогартовуваності. Крім того, легуючі елементи можуть підвищувати стійкість проти корозії, теплостійкість, жаростійкість (окалиностійкість), жароміцність та ін. Такі елементи як хром, марганець, молібден, вольфрам, ванадій, титан утворюють карбіди, а нікель, кремній, мідь, алюміній карбідів не утворюють. Марганець та нікель знижують критичні точки А1 і А3, а решта - підвищують. Крім того, легуючі елементи зменшують критичну швидкість охолодження при гартуванні, що необхідно враховувати при призначенні режимів гартування (температури нагрівання та середовища для охолодження). При значній кількості легуючих елементів може суттєво змінитись структура, що приводить до утворення нових структурних класів в порівнянні з вуглецевими сталями.
Тема: Хіміко-термічна обробка сталі
Хіміко-термічна обробка сталі на додаток до змін у структурі сталі також приводить до зміни хімічного складу поверхневого шару шляхом додавання різних хімічних речовин до певної глибини поверхневого шару. Ці процедури вимагають використання контрольованих систем нагрівання та охолодження в спеціальних середовищах. Серед найпоширеніших цілей, що ставляться при використанні цих технологій є підвищення твердості поверхні при високій в'язкості серцевини, зменшення сил тертя, підвищення стійкості до зношування, підвищення стійкості до втоми та покращення корозійної стійкості. До цих методів належать:
- Цементація (C) збільшує твердість поверхні м'якої сталі через збільшення концентрації вуглецю у поверхневих шарах.
- Азотування (N) як і цементація збільшує поверхневу твердість та зносостійкість сталі.
- Ціанування і нітроцементація (N+C) - це процес одночасного насичення поверхні сталей вуглецем і азотом. При ціануванні використовують розплави солей, які мають в своєму складі групу NaCN, а при нітроцементації - суміш аміаку з газами, які мають в складі вуглець (СО, СН4 та ін.). Після ціанування і нітроцементації проводять гартування і низьке відпускання.
- Сульфатування (S) - насичення поверхні сіркою, що покращує припрацювання тертьових поверхонь деталей, зменшується коефіцієнт тертя.
- Дифузійна металізація - насичення поверхневого шару виробу різними металами. Дифузійна металізація проводиться для підвищення твердості, корозійної стійкості, жаростійкості, блиску і естетичного вигляду. Найпоширеніші види дифузійної металізації: алітування, хромування, борування, берилізація, титанування.
- Тема : Термічна обробка сталі
- Основні види термічної обробки сталі.
Після прокату, лиття, кування, обробки різанням і інших видів обробки відбувається нерівномірне охолодження заготовок. У результаті чого з'являється неоднорідність, як структури, так і властивостей, а також поява внутрішніх напружень. А також виливка при затвердінні виходять неоднорідними за хімічним складом. Для усунення таких дефектів і застосовують відпал.
Відпал- називається вид термічної обробки, що складається в нагріві металу, що має нестійкий стан в результаті попередньої обробки і приводить метал у більш стійкий стан. При цьому процесі заготівлі та вироби отримують стійку структуру без залишкових напружень.
Цілі відпалу - зняття внутрішніх напружень, усунення структурної та хімічної неоднорідності, зниження твердості і поліпшення оброблюваності, підготовка до подальших операціях.
Відпал ділиться на повний, неповний, дифузний, рекрісталізаційний, низький, ізотермічний і нормалізаційного. Повний відпал застосовується для зниження твердості, міцності сталі, а пластичність при цьому підвищується. При повному відпалі у металі відбувається, перекристалізація сталі і зменшення розміру зерна, за рахунок чого і досягаються зазначені вище властивості.
Неповний відпал застосовується, для поліпшення оброблюваності різанням і для підготовки стали до загартовування.
Ізотермічний відпал полягає, в нагріві стали до певної температури і відносно швидкому охолодженні, також до певних температур і наступному охолодженні на повітрі. При цьому виходить, більш однорідна структура сталі. Ізотермічна витримка виробляється в розплаві солі.
Дифузійний відпал полягає, в нагріві стали до 1000-1100 градусів за Цельсієм, витримці (10-15 годин) при цій температурі і наступному повільному охолодженні. У результаті такого відпалу відбувається, вирівнювання неоднорідності стали за хімічним складом. Така висока температура необхідна для прискорення дифузійних процесів. При високій температурі нагріву і тривалої витримці виходить грубозерниста структура, яка усувається наступним повним відпалом.
Рекрісталізаційний відпал необхідний для зняття наклепу і внутрішньої напруги після холодних деформацій та підготовки до подальшого деформуванню. У результаті такого відпалу утворюється однорідна дрібнозерниста структура з невеликою твердістю і значною в'язкістю.
Низький відпал застосовують для того, щоб лише зняти внутрішнє напруження, яке виникає після механічної обробки.
Нормалізація складається, з нагріву сталі, її витримці при певній температурі і після чого залишають охолоджуватися на повітрі. Нормалізація - це більш дешева термічна операція, ніж відпал, так як печі використовують тільки для нагрівання і витримки.
До термічної обробки сталі також, відносять загартування. Суть цього процесу полягає, в нагріві стали до високих температур і після чого сталь швидко охолоджують. Мета гартування - це надання сталі підвищеної міцності, твердості, але при цьому знижується в'язкість і пластичність. Загартування характеризується двома властивостями -загартованість і прокалюваність. Загартованість характеризується певною твердістю, яка сталь набуває після гарту, а також залежить від змісту вуглецю в даній сталі. Стали з дуже низьким вмістом вуглецю (до 0,3) загартуванню не піддаються і вона для них не застосовується.
Прокаливаемость - це глибина проникнення загартованої зони (області).
Прокаливаемость залежить від хімічного складу сталі. З підвищенням вмісту вуглецю прокаливаемость збільшується. На прокаливаемость впливає також швидкість охолодження. Чим вище швидкість охолодження, тим більше прокаливаемость. Тому при гарті в воді прокаливаемость вища, ніж при загартуванні в маслі. Великі розміри гартованих деталі, також приводять до значного зменшення прокаливаемости.
Способи охолодження також відносять до однієї з операцій термообробки.
За способом охолоджування розрізняють види загартування: в одному середовищі, в двох середовищах, ступіньчаста і ізотермічна. Загартуванню в одному середовищі простіше і найбільш частіше застосовується, але недолік її полягає в тому, що виникає внутрішня напруга. При загартуванні в двох середовищах, виріб спочатку охолоджують спочатку в одному середовищі, а потім в іншій (вода, масло, повітря).
Ступіньчасте гартування виконують шляхом швидкого охолодження в соляній ванні, потім роблять витримку і охолоджують на повітрі. Ступіньчасте гартування застосовують для деталей з вуглецевої сталі невеликого перерізу (8-10 мм). ступінчасту загартування застосовують в основному для виробів великого перетину.
При ізотермічної загартуванню, як і при ступінчастій, деталі переохолоджувати в середовищі, далі на повітрі. Переваги цього способу гарту полягає в більшої в'язкості, відсутності тріщин, мінімальному викривленні. Ізотермічну загартування застосовують для виробів складної форми. Суттєву роль відіграють також способи занурення деталей в охолоджуючу рідину. Наприклад довгі вироби витягнутої форми (свердла, мітчики) занурюють в строго вертикальному положенні, щоб уникнути жолоблення.
Відпуск сталі- це вид термічної обробки, наступний за загартуванням і полягає в нагріві стали до певної температури, витримки та охолодженні. Мета відпуску сталиі- зняття внутрішніх напружень, підвищення в'язкості і пластичності.
Розрізняють низький, середній і високий відпуск. Низький відпуск проводиться при температурі 150-200 градусів Цельсія. У результаті знімаються внутрішні напруги, відбувається збільшення пластичності і в'язкості без помітного зниження твердості і зносостійкості. Низькому відпуску піддають різальний і вимірювальний інструмент, а також деталі, які повинні володіти високою зносостійкістю і твердістю.
При середньому відпуску нагрівання проводиться до 350-450 градусів Цельсія. При цьому відбувається деяке зниження твердості при значному збільшенні пружності і опірності дії ударних навантажень. Застосовується для пружин, ресор, ударного інструменту.
Високий відпуск проводиться за 550-650 градусів Цельсія. При цьому твердість і міцність знижуються значно, але дуже сильно зростають в'язкість і пластичність, проте створюється оптимальний варіант для конструкційних сталей поєднання механічних властивостей. Застосовується для деталей, які піддаються дії високих навантажень. Термічна обробка, що складається з гарту і високого відпустки, називається поліпшенням. Вона є основним видом обробки конструкційних сталей. Тривалість витримки залежить від розмірів деталей: чим вони більші, тим довше витримка. Низький відпустку інструментів зазвичай відбувається протягом 0,5-2,5 години. Для вимірювальних інструментів проводять більш тривалу відпустку до 10-15 годин.
Поряд з гарячою обробкою сталі, застосовується також обробка холодом.
Обробка холодом полягає в тому, що гартованих деталі на деякий час занурюють у середу має температуру нижче 0 градусів Цельсія.
Проводити обробку холодом потрібно відразу після гарту. Такій обробці піддають вимірювальний інструмент, частини точних механізмів, деталі шарикопідшипників. Обробка холодом не зменшує внутрішніх напружень, тому після неї необхідний відпустку.
Термомеханічна обробка відноситься до комбінованих способів і являє собою пластичну деформацію металу з загартуванням. Як при гарті, так і при пластичній деформації підвищення міцності завжди пов'язано із зменшенням пластичності. Перевагою є те, що при великому збільшенні міцності характеристики пластичності знижуються незначно, а ударна в'язкість в 1,5-2 рази вище в порівнянні з тією ж маркою стали після гарту низьким відпусткою. Термомеханічна обробка ділиться на два способи: високотемпературний і низькотемпературний.
При високотемпературному - сталь нагрівають і піддають деформації. Відразу після деформації сталь піддається загартуванню, після гарту виробляють низький відпустку.
При низькотемпературному - сталь нагрівається і охолоджується, після чого її деформують. Після деформації слід гарт. Після гарту слід низький відпустку.
Низькотемпературна обробка отримала незначне застосування. Найбільш часто застосовують високотемпературну обробку. Її зручність в тому, що заготовки відразу після закінчення гарячої обробки тиском: кування або прокату, можуть піддаватися гарту без спеціального нагріву, використовуючи тільки тепло після гарячого деформування. Перевага цього процесу полягає в економії палива, для нагріву під загартування, скорочення часу виготовлення деталей, підвищення механічних властивостей, збільшення міцності, ударної в'язкості при незначному зниженні пластичності. - Тема: Мідь і її сплави
Латинська назва міді cuprum, «купрум» бере своє походження від назви острова Кіпр (грец. Κύπρος, у латинській передачі Kúpros), де у давнину існував широкий промисел мідних предметів.
Алхіміки звали мідь словом Venus («Венера»), пов'язуючи її з планетою Венера.
Густина 8,940 r/см3. tпл 1084,5 °С; tкип 2567 °С. Хімічно малоактивна, але на повітрі завжди вкрита шаром оксидів або основного карбонату. Домішки: Ag, As, Fe, Bi, Sb, Hg, Ge. Взаємодіє з галогенами, сіркою, селеном, утворює комплексні сполуки з ціанідами і ін. В основних гірських породах її середній вміст трохи вищий (10−2). Мідь характерна для основного і кислого магматизму. При першому вона концентрується в магматичних і скарнових родовищах і поствулканічних колчеданних рудах. У звʼязку з гранітним магматизмом формуються мідно-порфірові і жильні родовища.
Початок мідної доби поклало освоєння людьми техніки гарячого кування і литва, якому багато сприяло поширення гончарного виробництва. Печі й керамічні форми для відливання дали можливість освоїти методи переробки самородної міді. Сталося це на Близькому Сході приблизно у IV тисячолітті до н. е., в Європі і Китаї в II-III тисячолітті до н. е., а в Перу на початку I тисячоліття до н. е.
Наступний етап розвитку технологій настав вже наприкінці III тисячоліття до н. е., коли була відкрита можливість отримання металів не лише з руди. У зв'язку з відносною простотою отримання з руди і порівняно невисокою температурою плавлення мідь - найперший метал, який був освоєний людиною. Одночасно, швидше за все випадково, було встановлено, що, якщо в тигель, де плавиться мідь, додати трохи олова і цинку якість отриманого матеріалу суттєво покращиться.
На початку II тисячоліття до нашої ери мідь стала замінюватися бронзою. Приблизно у цю ж пору зʼявилися й перші залізні вироби, але мʼяке залізо (не придатне до лиття, оскільки вимагало надмірно високих температур), як матеріал для зброї і сільськогосподарських знарядь, не могло конкурувати з бронзою, - бронзова доба тривала ще 1000 років, аж до освоєння технологій навуглецьовування, гартування і зварювання сплавів заліза.
І пізніше бронза зберігала свою роль, тому що перевершувала залізо в технологічності, - якщо форму залізному виробу можна було надавати лише куванням (тому навіть старовинні цвяхи мали квадратний перетин), то бронзові знаряддя можна було виливати. З XV століття бронза знову стала стратегічним матеріалом, оскільки виявилося, що вона незамінна для виготовлення гармат.
Мідь і її сплави з глибокої давнини служили для карбування монет і медалей.
Отримання міді
Мідь отримують з мідних, мідно-молібденових, мідно-нікелевих і поліметалічних руд. Заводи випускають чорнову (99 %), рафіновану вогневим (99,6 % Cu) і електролітичним (99,95 % Cu) методами мідь.
Процес добування міді включає три основні етапи:
- збагачення мідної руди;
- виплавка чорнової міді;
- рафінування міді.
Враховуючи дуже малий вміст міді в рудах (1-2 %), руду спочатку збагачують флотаційним способом. Розмелену руду змішують з флотаційними реагентами піноутворювачами та водою і продувають пульпу повітрям. Пухирці повітря прилипають до зерен рудних мінералів, спливають і утворюють піну, а пуста порода, яка добре змочується водою, опускається на дно.
Докладніше: Флотація мідних сульфідних рудПісля фільтрації піни та просушування отримують концентрат з вмістом 10-35 % міді. Для зменшення вмісту сірки збагачену руду піддають окислювальному випалу при температурі 600-900 °C. Після цього руда поступає в полуменеві печі з температурою в зоні плавки 1450 °C, де відбувається дисоціація вищих сульфідів і карбонатів. Продукти дисоціації сплавляють між собою, утворюючи штейн - легкоплавкий сплав з температурою плавлення 900-1150 °C і вмістом 10-60 % Cu, 10-58 % Fe, 22-25 % S. Крім того, штейн містить домішки нікелю, цинку, свинцю, золота, срібла. Виплавка чорнової міді відбувається в горизонтальних конверторах з боковим дуттям продувкою штейну повітрям. Температура в конвертері становить 1200-1300 °C. Спочатку окислюється залізо:
Окисел заліза в вигляді шлаку спливає на поверхню і зливається. У другий період продування:
Закис міді розчиняється в розплаві та взаємодіє з напівсірчистою міддю з утворенням чорнової міді:
Тепло в конвертері виділяється за рахунок перебігу хімічних реакцій, без подавання палива. Таким чином, в конвертері отримують чорнову мідь, що містить 98,5-99,5 % Cu; 0,3-0,5 % S; 0,01-0,04 % Fe; 0,3-0,5 % Ni.
Рафінування чорнової міді проводять вогневим (окислення домішок при продуванні розплаву повітрям), або електролітичним способом за рахунок електролізу в водному розчині сірчаної кислоти та мідного купоросу. При проходженні струму анодні плити чорнової міді розчиняються і на катодах осаджується чиста електролітична мідь, а домішки випадають на дно ванни.
Найбільше міді добувають у Чилі. На долю цієї країни припадає третина світового виробництва. Далі за видобутком йдуть США, Індонезія та Перу.
Маркування промислової міді
Марки промислової міді та її хімічний склад визначається в ДСТУ ГОСТ 859-2003[7]. Скорочена інформація про марки міді та аналоги у зарубіжних стандартах наведена нижче:
Марки міді EN, DIN Cu, % O, % P, %
М00 Cu-OFE 99,96 0,03 0,0005
М0 Cu-PHC, OF-Cu 99,93* 0,04 0,002
М1б Cu-OF1, Cu-ETP1 99,95* 0,003 0,002
М1 Cu-OF, Cu-ETP, Cu-FRHC, SW-Cu, E-Cu, E Cu58 99,90* 0,05 -
М1ф Cu-DHP, SF-Cu 99,90* - 0,012 - 0,04
М2 99,7* 0,07 -
М3 99,5* 0,08 -Специфічні особливості міді, що властиві різним маркам, визначаються не вмістом міді (відмінності складають не більше 0,5 %), а вмістом конкретних домішок (їх кількість може відрізнятися у 10-50 разів). Часто використовують класифікацію марок міді за вмістом кисню:
- безкиснева мідь: М00б, М0б з вмістом кисню до 0,001 % і М1б до 0,003 %;
- рафінована мідь (М1ф, М1р, М2р, М3р) з вмістом кисню до 0,01 %, але з підвищеним вмістом фосфору;
- мідь високої чистоти (М00, М0, М1) з вмістом кисню 0,03-0,05 %;
- мідь загального призначення (М2, М3) з вмістом кисню до 0,08 %.
Сортамент промислового постачання
Промислова мідь постачається після наступних видів обробки тиском:
- холоднодеформований прокат - це тягнені (прутки, дріт, труби) і холоднокатані (листи, стрічка, фольга) вироби. Він випускається в твердому, напівтвердому і мʼякому (відпаленому) станах;
- гарячедеформований прокат - результат пресування (прутки, труби) або гарячого вальцювання (листи, плити), при температурах вище температури рекристалізації (150-240 °C);
Сортамент промислової міді наступний:
- Мідні прутки - випускаються пресованими (20-180 мм) і холоднодеформовані, в твердому, напівтверді і мʼякому станах (діаметр 3-50 мм) за ДСТУ ГОСТ 1535^2006[8].
- Плоский мідний прокат загального призначення випускається у вигляді фольги, стрічки, листів і плит з ДСТУ ГОСТ 1173:2006[9].
- Фольга мідна - холоднокатана: 0,05-0,1 мм (випускається тільки в твердому стані)
- Стрічки мідні - холоднокатані: 0,1-6 мм.
- Листи мідні - холоднокатані: 0,2-12 мм і гарячекатані: 3-25 мм (механічні властивості регламентуються до 12 мм).
- Плити мідні - гарячекатані: понад 25 мм (механічні властивості не регламентуються).
- Мідні труби загального призначення виготовляються холоднодеформованими (в мʼякому, напівтверді і твердому станах) і пресованими (великих перерізів) за ДСТУ ГОСТ 617:2007[10].
Мідь - малоактивний метал, в електрохімічному ряду напруг вона стоїть правіше за водень. Вона не взаємодіє з водою, розчинами лугів, соляною і розведеною сірчаною кислотою. Проте в кислотах - сильних окислювачах (наприклад, у азотній і концентрованій сірчаній) - мідь розчиняється:
Чиста мідь має достатньо високу стійкість до корозії: продукти окиснення утворюють при звичайній температурі лише тонкий поверхневий шар . В сухому повітрі це оксиди міді (червоний Cu2O непомітний, чорний CuO призводить до потемніння), у вологій атмосфері, що містить вуглекислий газ, мідь покривається зеленуватим нальотом основного карбонату міді:
В сполуках мідь може проявляти ступені окиснення +1, +2 і +3, з яких +2 - найбільш характерний і стійкий. Мідь(II) утворює стійкий оксид CuO і гідроксид Cu(OH)2. Цей гідроксид амфотерний, добре розчиняється у кислотах і в концентрованих лугах:
Солі міді (II) знайшли широке застосування в народному господарстві. Особливо важливим є мідний купорос - кристалогідрат сульфату міді(II) CuSO4.
Механічні властивості
Механічні властивості чистої міді (у мʼякому стані) наступні[8]:
- умовна границя текучості σ0,2 = 70 МПа;
- границя міцності σв = 200 МПа;
- відносне видовження після руйнування при розтягування δ = 35-40 %;
- твердість за шкалою Брінелля 40 HB;
- модуль Юнга E = 110-128 МПа;
- модуль зсуву G = 48 МПа.
Використання чистої міді
Використовується у чистому вигляді в електротехніці, вирізняється високою електро- і теплопровідністю.
Більше половини міді, що добувається, використовується в електротехніці для виготовлення різних проводів, кабелів, струмопровідних частин електротехнічної апаратури. Для цього переважно використовується чистий метал (від 99,98 до 99,999 % Cu), що пройшов електролітичне рафінування.
Завдяки високій теплопровідності мідь - незамінний матеріал теплообмінників і холодильної апаратури. Крім цього, з міді виготовляють деталі хімічної апаратури та інструмент для роботи з вибухонебезпечними або легкозаймистими речовинами.
Широко застосовується мідь в гальванотехніці для нанесення мідних покриттів, одержання тонкостінних виробів складної форми, виготовлення кліше в поліграфії та ін.
Сплави на основі міді
Залежно від марки (складу) сплави можуть використовуватися в різних галузях техніки як конструкційні елементи (в тому числі у вигляді припоїв[11]), як матеріали з антифрикційними властивостями, із стійкістю до корозії або заданою електро- і теплопровідністю. Велике значення мають наступні мідні сплави:
- латунь - основна добавка цинк (Zn). Вона має жовтуватий колір. Позначається звичайна латунь буквою Л з цифрою, що вказує на процентний вміст у латуні міді, а все інше - цинк. Наприклад, Л62 (62 % міді). Латунь твердіша за мідь, вона ковка і в'язка, тому легко вальцюється в тонкі листи або виштамповується у найрізноманітніші форми. Недолік: вона з часом окислюється і чорніє. Домішки кремнію (Si), олова (Sn), алюмінію (Al) підвищують міцність, антифрикційні властивості й корозійну стійкість латуні на повітрі, у морській воді й атмосфері. Марганець додає жаростійкості, а залізо твердості. Свинцева латунь добре полірується, а домішка до алюмінієвої латуні миш'яку, нікелю й заліза підвищує її стійкість до кислот;
- бронза - сплави з різними елементами, головним чином металами - оловом, алюмінієм, берилієм (Be), свинцем (Pb), кадмієм (Cd) та іншими, крім цинку (Zn) і нікелю (Ni). Порівняно з латунню бронза міцніша, стійкіша до корозії, мають антифрикційні властивості. Позначають бронзу Бр, а далі йдуть елементи, які входять у її склад та їх процентний вміст (крім міді). Наприклад, БрОФ 8,0-0,3 містить 8 % олова й 0,3 % фосфору, решта - мідь. Із бронз виготовляють крани, вентилі, втулки навантажених підшипників тощо Берилієва бронза після загартовування, за твердістю й пружними властивостями перевершує високоякісну сталь, а кадмієві й хромисті бронзи мають високу тепло- і електропровідність;
- мідно-нікелеві сплави - (константан (МНМц 40-1,5), манганин (МНМц 3-12), куніаль (МНА 13-3), мельхіор (МНЖМц 30-0,8-1), нейзильбер («нове срібло»)(МНЦ 15-20)). Мідно-нікелеві сплави мають високу корозійну стійкість і особливі електричні властивості, які змінюються залежно від вмісту нікелю. Крім нікелю, до складу сплаву можуть входити й інші елементи.
З часів античності мідь використовувалась у складі монетних сплавів, які отримали особливе поширення у новітню добу. Це сплави: мідь-цинк-олово, мідь-алюміній мідь-нікель, бронза, латунь, мельхіор. Литі мідні зливки античної Греції та Риму представляють інтерес для нумізматики. Мідні монети, що карбувались як еквівалент срібним, мали особливо великі розміри та вагу, як, наприклад шведські мідні дошки-плоти чи мідні гроші. З появою розмінної монети мідні монети пристосувались до потреб грошового обігу.
Мідь у інших сплавах
Дюралюміній - є сплавом алюмінію, де основним легуючим елементом є мідь (вміст 4,4 %), а також, магній (1,5 %) та марганець (0,5 %).
Мідь у хімічних сполуках
Мідний купорос (у природі зустрічається у вигляді мінералу халькантит, хімічна формула CuSO4 • 5Н2О) використовується як окремо в 1...2, так і в суміші зі свіжогашеним вапном в 1...4 % концентрації (бордоська рідина) у сільському господарстві для боротьби з хворобами рослин. У промисловості мідний купорос використовується при виробництві штучних волокон, органічних барвників, мінеральних фарб, миш'якових хімікатів, для збагачення руди при флотації.
Оксиди міді (Cu2O, CuO) використовуються для отримання оксиду ітрію-барію-міді YBa 2 Cu 3O7-δ, який є основою для отримання високотемпературних надпровідників.
Оксид міді (іноді з додаванням оксиду барію або оксиду бісмуту для збільшення ємності) використовується як катод у мідно-окисидному гальванічному елементі (винайденому в 1882 році Лаландом) - хімічному джерелі електричного струму в якому анодом є цинк (рідше олово), а електролітом служить гідроксид калію.
Біологічна роль
Позитивний вплив
Багата на мідь їжа: устриці, печінка корів або овець, бразильські горіхи, какао і чорний перець. До непоганих джерел міді належать також омари. горіхи, кунжутне та соняшникове насіння, зелені маслини, авокадо, пшеничні висівки.Мідь важливий елемент для всіх рослин і тварин. Відомо понад 50 білків та ферментів, у яких знайдено мідь. В основному мідь міститься в крові в складі білків плазми, які називаються церулоплазмінами. Поглинаючись у кишечнику мідь переноситься до печінки завдяки звʼязку із альбуміном. Мідь сприяє росту і розвитку, бере участь у кровотворенні, імунних реакціях. Мідь потрібна для перетворення заліза організму в гемоглобін. У крові більшості молюсків і членистоногих мідь використовується замість заліза для транспортування кисню у складі гемоціаніну, аналога гемоглобіну у головоногих, надаючи крові блакитний відтінок.
Відзначено[12] на основі досліджень, що сполуки міді в формі сульфату у певних дозах діють бактеростатично, протигрибково, антитоксично, у курчат стимулюють ріст, а у курей несучість і якість яєць, посилюють біотрансформацію білків корму в білки тіла, підвищують загальну резистентність організму сільськогосподарської птиці.
Вважається, що мідь і цинк конкурують один з одним у процесі засвоювання в травній системі, тому надлишок одного з цих елементів в їжі може викликати недостачу іншого елемента. Здоровій дорослій людині необхідне надходження міді у кількості 1...2 мг щоденно[13]. Захворювання, що викликаються дефіцитом міді: анемія, водянка, дерматози, затримка росту, депігментація волосся, часткове облисіння, втрата апетиту, сильне схуднення, зниження рівня гемоглобіну, атрофія серцевого мʼяза.
Негативний вплив
Надлишкове надходження міді в організм веде до відкладення її в тканинах (хвороба Вільсона). При надходженні в організм людини надлишкової кількості міді може виникнути бронхіальна астма, захворювання нирок, захворювання печінки, а також просто інтоксикація організму. Симптоми передозування
- безсоння, дратівливість, депресія;
- мʼязові болі, анемія;
- подразнення слизових оболонок, запальні захворювання;
- погіршення памʼяті;
- розлади шлунково-кишкового тракту.
Цікаві факти
- Індіанці культури Чонос (Еквадор) ще у XV-XVI століттях виплавляли мідь із вмістом 99,5 % і використовували її як монети у вигляді сокирок розмірами сторін по 2 мм і 0,5 мм завтовшки. Ця монета ходила по всьому західному узбережжю Південної Америки, в тому числі і в державі інків[14].
- У Японії мідним трубопроводам для газу в будинках присвоєно статус «сейсмостійких».
- Інструменти, виготовлені з міді і її сплавів, не утворюють іскор при ударах, а тому застосовуються там, де існують особливі вимоги безпеки (вогненебезпечні, вибухонебезпечні виробництва).
- Польські вчені встановили, що в тих водоймах, де присутня мідь, коропи відрізняються великими розмірами. У ставках чи озерах, де міді немає, швидко розвивається грибок, який вражає коропів[15].
- Тема; Алюміній і його сплави
Алюміній як елемент був відкритий в 1825р., Коли були отримані перші невеликі грудочки цього металу. Початок його промислового освоєння відноситься до кінця 19-го сторіччя - після відкриття технології його одержання шляхом електролізу глинозему, розчиненого в розплавленому кріоліті. Цей принцип лежить і в основі сучасного промислового витягу алюмінію з глинозему у всіх країнах світу.
Алюміній являє собою сріблясто-білий пластичний метал. У повітряному середовищі він швидко покривається окисной плівкою, яка захищає його від корозії. Алюміній хімічно стійкий проти азотної і органічних кислот, але руйнується лугами, а також соляної та сірчаної кислотами. Найважливіша властивість алюмінію - невелика щільність, він в три рази легше заліза. Механічні властивості алюмінію невисокі: опір на розрив - 5-9 кгс / мм?, відносне подовження - 25-45%. Висока пластичність (досягається відпалом при температурах 350-410 ° С) цього металу дозволяє прокатувати його в дуже тонкі аркуші, наприклад, фольга може мати товщину до 0,005 мм. Алюміній добре зварюється, проте важко обробляється різанням. Для підвищення міцності в алюміній уводять кремній, марганець, мідь та інші компоненти. Значні природні запаси алюмінію, його невелика щільність, високі антикорозійні властивості, хороша електропровідність сприяли широкому розповсюдженню цього металу в різних галузях техніки. Алюміній і його сплави застосовуються в літако- та машинобудуванні, при будівництві будівель і ліній електропередачі, в багатьох галузях промисловості. З нього виготовляють різні ємності і арматуру для хімічної промисловості, в харчовій промисловості застосовується пакувальна фольга з алюмінію і його сплавів (для обгортки кондитерських і молочних виробів). Широке визнання отримала алюмінієвий посуд. Алюміній добре піддається різним тонким покриттям і забарвленням, тому його використовують і як декоративний матеріал.
Алюміній всіх марок містить більше 99% чистого алюмінію. Залежно від хімічного складу він підрозділяється на алюміній особливої, високої та технічної частоти, позначається буквою А і цифрою, що показує десяті й соті частки відсотка після 99%, наприклад, А85 - містить 99,85% алюмінію.
Так як міцність алюмінію дуже незначна, то в якості конструкційних матеріалів застосовують його сплави. Сплави підрозділяються на деформовані - в основному, дюралюміній і ливарні - головним чином силумін.
Дюралюміній - сплав алюмінію з міддю (2,2-5,2%), магнієм (2-2,7%) і марганцем (0,2-1,0%). Його піддають гарту у воді після нагрівання до температури близько 500 ° С і зміцнюючих старінню. За своїми механічними властивостями він наближається до середньовуглецевої сталі. Застосовується, головним чином, у вигляді різного прокату - листи, куточок, труби і т.д. як конструкційний матеріал він використовується для транспортного та авіаційного машинобудування.
Силумін - сплав алюмінію і кремнію, володіє хорошими ливарними властивостями, м'який, застосовується для виготовлення невідповідальних деталей методом лиття та тиску. Крім алюмінію і кремнію (10-13%) у цей сплав входять: залізо (0,2-0,7%), марганець (0,05-0,5%), кальцій (0,07-0,2%) , титан (0,05-0,2%), мідь (0,03%) і цинк (0,08%). Можуть використовуватися сплави алюмінію з цинком, магнієм і т.д.
Технологічний процес виробництва алюмінію
Виробництво алюмінію - складний технологічний процес. У вільному вигляді алюміній внаслідок своєї активності не зустрічається. Його отримують з мінералів - бокситів, нефелінів і алунітів, при цьому спочатку роблять глинозем, а потім з глинозему шляхом електролізу отримують алюміній. Технологічна схема виробництва алюмінію складається з процесів:
1. отримання глинозему Al2O3 шляхом вилуговування концентрованим розчином лугу подрібненого бокситу і його подальшого прожарювання.
2. розчинення глинозему в розплаві кріоліту і його електроліз у ванні з вугільним анодом і покритим вугільними блоками катодом (рис. 1). Аніони алюмінію нейтралізують на катоді і випадають в розплав. На виробництво 1 т алюмінію йде 17-18 тис. КВт електроенергії.
3. електролітичне рафінування,
Алюміній всіх марок містить більше 99% алюмінію
Тема: Електроди для дугового зварювання металів
Як ми писали вище, електроди складно класифікувати лише по одному параметру. Але в основному усі стержні передусім діляться за типом матеріалу, з яких вони виготовлені, а також по покриттю (чи обмазке). Ось коротка класифікація електродів :
- Плавкі електроди. Їх виготовляють з металу, наприклад, чавуну, алюмінію, сталі або міді. Матеріал, з якого виготовлений електрод, підбирається відповідно до металу, який необхідно зварити. Плавкі електроди одночасно є і анодом, і катодом. Це найпоширеніший тип стержнів на даний момент.
- Неплавкі електроди. Виготовляються з вугілля, графіту або вольфраму. Їх використовують в парі із зварювальним дротом, тому що такі стержні не здатні сформувати зварювальний шов. При використанні вугільних стержнів використайте пряму полярність замість зворотної. Вольфрамові стержні незамінні при аргонодуговой зварюванні за рахунок високої температури плавлення, але рідко використовуються при ручному дуговому зварюванні.
- Електроди без покриття або обмазки. Вони використовуються в зв'язці з флюсом, який безперервно подається упродовж усього зварювального процесу. При ручному дуговому зварюванні такі стержні не використовуються.
- Електроди з покриттям або обмазкой. Найпоширеніші електроди на ринку. Покриття електродів для ручного дугового зварювання виконує відразу декілька функцій: захищає метал від негативного впливу кисню, забезпечує стабільне горіння дуги, покращує якості зварного з'єднання. Такі електроди використовуються не лише при ручному дуговому зварюванні, але і при напівавтоматичній і автоматичній.
Види електродів за призначенням
Залежно від зварюваного металу вибирається режим роботи зварювального апарату і електроди. Для різних металів потрібні різні електроди, це називається призначенням. Призначення вказується однією буквою на упаковці і на самому стержні.
Електроди з маркіровкою "У" використовуються для зварювання низьколегованих і вуглецевих сталей. Буквою "Л" означають стержні, використовувані для зварювання легованих конструкційних сталей, а для високолегованих використовується позначення "В". Буквою "Т" означають стержні для теплостійких металів, а буквою "Н"-стержні для наплавлення.
Види покриттів для електродів
На ряду з матеріалом виготовлення і призначенням вибирається і тип покриття електроду. Вибір покриття також залежить від зварюваного металу. Покриття (чи обмазка) виконує захисну функцію. При плавленні електроду покриття виділяє захисні речовини і шлак, що покращує якість шва, виходять надійні і довговічні зварні з'єднання. Виробники використовуються наступні види покриттів електродів :
- Кисле покриття. Маркірується буквою "А" на упаковці і самому електроді. Використовується для вузьконаправлених завдань, наприклад, для нижніх зварювальних швів. Можна використати як зі змінним, так і з постійним струмом.
- Рутилове покриття. Маркується буквою "Р". Одне з найпопулярніших покриттів як у новачків, так і у професіоналів. В порівнянні з іншими покриттями майже не токсично і забезпечує хороше якості швів. При згоранні утворює шлак із захисними властивостями. Склад може бути різноманітним, але в основі завжди двоокис титану або просто рутил. Звідси і назва.
- Целюлозне покриття. Маркується буквою "Ц". Підходить для виконання будь-яких зварних з'єднань, забезпечує хорошу якість шва, але при цьому сприяє сильному розбризкуванню металу. Ми рекомендуємо використати електроди з целюлозним покриттям при зварюванні трубопроводу, оскільки при такій роботі недоліки не критичні.
- Основне покриття. Позначається буквою "Б". Найпопулярніший вид покриття на ряду з рутиловим. Імітує зварювання під газом за рахунок виділення вуглекислоти при горінні дуги. Ми рекомендуємо використати стержні з основним покриттям тільки у поєднанні з постійним струмом і зворотною полярністю. Якщо використати змінний струм, то зварювальний шов вийде неякісним і знадобляться додаткові заходи по поліпшенню міцності шва.
- Інші види покриттів. Маркуються буквою "П". У складі містять легуючі речовини. Завдяки цьому якість шва покращується. В цілому, інші види покриттів використовуються найрідше.
- Спеціальні види покриттів. Позначаються буквою "С" або написом "спеціальні" на упаковці. Використовуються для складного зварювання під водою, оскільки містять у своєму складі рідке скло і смоловмісні речовини.
Як бачите, електроди вибираються виходячи з конкретних завдань. Для ручного дугового зварювання найчастіше використовують стержні з рутиловим покриттям, оскільки вони універсальні.
Вибір діаметру електроду
Більшість зварювальників класифікують зварювальні стержні саме по діаметру, що правильно. Адже від товщини деталі безпосередньо залежить діаметр електроду. І навіть якщо ви виберіть стержень з потрібним покриттям і з потрібного матеріалу, але розмір буде неправильним, ви не отримаєте якісний шов.
Діаметр електроду вказується в міліметрах на упаковці або на самому стержні. При цьому від діаметру залежить і довжина електроду. Для зварювання в домашніх умовах зазвичай використовують електродів для дугового зварювання з діаметром від2 до4 мм. Це універсальний розмір, відповідний для більшості зварювальних робіт. Товщі електроди використовуються на заводах або в приватних майстернях.
Вибір електродів залежно від типу шва
Також доцільно проводити вибір електродів для ручного дугового зварювання за типом шва, яким ви збираєтеся варити метал. Окрім стандартних горизонтальних, вертикальних, похилих і швів під кутом існують також косі, стикові, із скосами і багато інших. Це корисно швидше для досвідчених майстрів, але і зварювальникам початківцям варто знати цю інформацію. Тепер поговоримо про те, які бувають марки електродів для ручного дугового зварювання.
Марки електродів, відповідні для ручного дугового зварювання
Існують також види електродів для ручного дугового зварювання, що розділяються по марках. Марка використовуваного електроду так само залежить від металу, який вам треба зварити.
Для зварювання вуглецевих низьколегованих сталей використовуються наступні марки:
- Э42: марки АНО—6, АНО—17, ВСЦ-4М.
- Э42: УОНИ—13/45, УОНИ-13/45А.
- Э46: АНО—4, АНО—34, ОЗС—6.
- Э46А: УОНИ-13/55К, АНО—8.
- Э50: ВСЦ-4А,550-У.
- Э50А: АНО—27, АНО-ТМ, ИТС-4С.
- Э55: УОНИ-13/55У.
- Э60: АНО-ТМ60, УОНИ—13/65.
Для зварювання легованих сталей (у тому числі високоміцних) :
- Э70: АНП—1, АНП—2.
- Э85: УОНИ—13/85, УОНИ-13/85У.
- Э100: АН-ХН7, ОЗШ—1.
- Э125: НИИ-3М, Э150: НИАТ—3.
Для наплавлення металу : ОЗН-400М/15Г4С, ЭН-60М/Э-70Х3СМТ, ОЗН-6/90Х4Г2С3Р, УОНИ—13/Н1-БК/Э-09Х31Н8АМ2, ЦН-6Л/Э-08Х17Н8С6Г, ОЗШ-8/11Х31Н11ГСМ3ЮФ.
Для зварювання чавуну : ОЗЧ—2/Cu, ОЗЧ—3/Ni, ОЗЧ—4/Ni.
Для зварювання алюмінію і його сплавів : ОЗА—1/Al, ОЗАНА—1/Al.
Для зварювання міді і її сплавів : АНЦ/ОЗМ—2/Cu, ОЗБ-2М/CuSn.
Для зварювання нікелю і його сплавів : ОЗЛ—32.
Електроди для дугового зварювання Електроди виготовляють зі сталевого зварювального дроту. Зварювальний дріт можуть виготовляти з шести марок низьковуглецевої сталі, 30 – з легованої і 39 – з високолегованої сталі. Усі марки сталі мають обмежений вміст вуглецю, сірки і фосфору. Дугове зварювання стержнями зі сталевого дроту (голими електродами) не застосовують внаслідок нестійкого горіння дуги і великого насичення металу шва киснем і азотом повітря. Для підвищення стійкості горіння дуги і захисту розплавленого металу від взаємодії з повітрям на дріт , що складається зі стабілізуючих (сполуки лужних (калію, натрію) і лужноземельних (кальцію) металів), клейових (рідке скло), шлакоутворюючих, легуючих і розкислюючих речовин. Склад покриття електродів Стабілізуючими речовинами є сполуки лужних (калію, натрію) і лужноземельних (кальцію) металів, які іонізуються в дузі легше, ніж кисень і азот повітря, та поліпшують стійкість горіння дуги. Легуючими елементами є хром, марганець, вольфрам, 13 молібден та інші. Їх вносять в електродні покриття при зварюванні легованих сталей і одержання стійких до спрацювання наплавок. Розкислювачі елементи (Mn, Ti, Si та інші) мають більшу спорідненість з киснем, ніж залізо. Вони відновлюють залізо з оксидів, утворюють нерозчинні в залізі оксиди відповідних елементів, які спливають у шлак. Розкислювачі та легуючі елементи вносять у покриття переважно у вигляді подрібнених феросплавів. Шлакоутворювальними речовинами є оксиди (ТіО2, SіО2, МnО), карбонати (СаСО3, МgСО3) та фториди (СаF2), які вносять у покриття у вигляді мінералів (кремнезему, мармуру) і руд (титанової, манганової). Вони утворюють шлак при плавленні покриття. Шлак покриває краплини 3 електродного металу в дузі та зварювальну ванну на металі 1 шва та захищають розплавлений метал від азоту і кисню повітря. Шлакова кірка 2 відділяється від поверхні шва після остигання шва та шлаку. Органічні сполуки (наприклад, целюлозу) вносять в електродні покриття для газового захисту. Ці сполуки утворюють навколо дуги під час згоряння захисні гази (СО, Н2) та захищають розплавлений метал від взаємодії з повітрям. Виготовлення покриття електродів. Кускові матеріали шихти покриття подрібнюють, розмелюють, просіюють і змішують з рідким склом. Одержану масу наносять опресуванням на електродні стержні. Отримані електроди просушують і прокалюють Класифікація електродних покрить за хімічним складом Електродні покриття поділяють за хімічним складом на кислі й основні. Кислотні оксиди SіО2, ТіО2 та інші переважають у шлаках кислих покриттів. Марганцева та титанова руди входять у покриття цих електродів у вигляді концентратів рутилу (понад 90 % двооксиду титану), польового шпату, граніту, а також газоутворюючи речовини та розкислювачі, що скріплені рідким склом. Електроди з кислим покриттям використовують для зварювання вуглецевих і низьколегованих сталей. Електроди з рутиловим покриттям мають найліпші зварювальні властивості (хорошу стабільність дуги, можливість здійснювати зварювання як на постійному, так і змінному струмі, якісне формування металу шва та легке відділення від нього шлакової кірки). 14 Основні електродні покриття Основними компонентами є мармур, плавиковий шпат, розкислювачі і легуючі елементи. Стабілізуючими речовинами є кальцій і натрій або кальцій і калій. Кальцій входить до складу мармуру (СаСО3) і плавикового шпату (СаF2), а натрій і калій є складовими натрієвого (Na2О∙n(SiO2)) чи калієвого (К2О∙n(SiO2)) рідкого скла відповідно. Оксид вуглецю СО утворюється під час дисоціації мармуру та перешкоджає взаємодії розплавленого металу в дузі з навколишнім середовищем. Електроди з основним покриттям сприяють легуванню наплавленого металу без значних втрат легуючих елементів. Основні шлаки сприяють очищенню металу шва від сірки і фосфору. Вміст сірки в металі зменшується за реакціями: FеS + Мn = МnS + Fe, (1) FeS + СаО = СаS + Fе, (2). Сульфіди МnS і СаS мало розчиняються в металі, тому значна їх частина переходить у шлак. Електроди з основним покриттям застосовують для зварювання відповідальних деталей і утворення зносостійких наплавок. Класифікація сталевих електродів за призначенням Сталеві електроди за призначенням поділяють на 4 групи: 1. Для зварювання вуглецевих і легованих конструкційних сталей. 14 типів електродів передбачено залежно від границі міцності металу шву. Марки електродів – Э38, Э42, Э46, ..., Э150. Цифри означають гарантовану границю міцності шва у кг/мм2 ; 2. Для зварювання легованих теплостійких сталей встановлено 9 типів електродів залежно від хімічного складу наплавленого металу. Наприклад, Э-09МХ, Э-09Х1М, Э-09М та ін 3. Для зварювання високолегованих сталей з особливими властивостями передбачено 45 типів електродів. Наприклад, Э12X13, Э-10Х17Т, Э-10Х17Н13С4 та ін.; 4. Електроди для наплавлення поверхневих шарів з особливими властивостями за хімічним складом наплавленого металу і призначенням поділено на 44 типи. Наприклад, для наплавлення деталей, які працюють в умовах ударних навантажень (Э-10Г2, Э30Г2ХМ), для наплавлення штампів гарячого штампування (Э- 15 10Х2ГМ, Э-90Х4М4ВФ), для наплавлення металорізального інструменту (Э-105В6Х5М3Ф3).
Все про роботу з електродами, що не плавляться, їх види і характеристики
До певної міри електроди, що не плавляться, парадоксальні. З одного боку, завдяки даним розхідникам зварювальний шов виходить філігранним, а різ – бездоганно чистим. З іншого, метал шва та різ вони безпосередньо не створюють.
Розплавниками, що не плавляться, метали зварюють уже 140 років. У 1882 р. російський вчений Микола Бенардос вперше запропонував використати вугільний електрод для дугового зварювання. З того часу її так і називають – «спосіб Бенардоса».
Розгадка у цьому, що це стрижні або мають неметалеву природу (вугільні і графітові), або зроблені з тугоплавкого вольфраму. Тож під час роботи не плавляться.
Звідси і акуратний результат: електроди, що плавляться, його не дають, оскільки часто заливають лінію зварювання своїм металом. Розплавники, що не плавляться, задіяні тільки як присадочний дріт, який підтримує стійке горіння електричної дуги. З її запаленням запускають аргон, гелій чи азот, що захищають місце зварювання від окиснення киснем.
На матеріалі
Щоб підібрати найбільш придатний для конкретної роботи електрод, що не плавиться, визначтеся з параметрами:
- який вид зварювання ви обираєте;
- з яким металом збираєтесь працювати;
- який діаметр має стрижень;
- Струм якої сили знадобиться.
- графітові використовують переважно для зварювання під флюсом (захисним порошком) в автоматичному та напівавтоматичному режимі;
- з'єднують кольорові сплави, нержавіючі сталі, мідну та алюмінієву проводку;
- "Діаметр стрижнів з графіту великий – від шести міліметрів і вище. Тому діапазон їх можливостей неширокий;"
- практично не ламаються, не окислюються, порівняно з вугільними аналогами, стійкішими до коливань температур та вологості. У той же час до їх складу входить графітовий вуглець, який здатний помножити вуглецеву частку в металі, що обробляється. А це призводить до погіршення якості готового шва.
- вугільні підходять для повітряно-дугового різання, при якій стиснене повітря, що безперебійно подається в область зварювання, миттєво очищає площину заготовки від розплавленого металу. На виході маємо гладку та пряму лінію розрізу;
- зварюють низьколеговану сталь та кольорові метали. А якщо поверхня стрижня покрита шаром міді, можуть також заварювати та спаювати;
- забезпечують зварювання без дроту. Але професіонали все ж таки радять застосовувати присадковий матеріал;
Зварювання вугільними розхідниками проводять двома способами. Зліва направо, коли присадку розміщують за електродом. І у зворотному напрямку, висуваючи пруток вперед.
- формою поділяються на: круглі для стандартного зварювання, плоскі для зварювання повітряно-дуговим методом і для такого ж різання – круглі;
- сила струму для роботи з вугільними електродами на великих об'єктах становить 580 А. У домашніх майстернях, завдяки низькій теплопровідності стрижнів, для створення дуги вистачає 3-5 А.
- вольфрамові застосовують для аргонодугового зварювання;
Вибирайте аргон високої чистоти. Вживання неякісного газу призводить до потемніння зварювального шва.
- температура плавлення вольфраму вища, ніж у електричної дуги. Це продовжує термін служби зварювального обладнання;
- випускають із різним діаметром сердечника стрижня, під який підбирають силу струму. Наприклад, мінімальний 1-міліметровий присадний дріт вимагає п'ятдесят ампер, максимальний 4-міліметровий – понад триста.
Нюанси маркування електродів з вольфраму
Зорієнтуватися в неабиякому асортименті електродів, що не плавляться, допомагають маркування.
- "Літера"розповідає про активуючі добавки у вольфрамових провідниках і позначається кирилицею або латиницею.
- ЕВЛ – з оксидом лантану;
- ЕВІ\Y – з оксидом ітрію;
- ЕВТ – з діоксидом торію;
- ЕВЧ W – чистий вольфрам.
- Класифікація за кольором електродів, що не плавляться, вказує на хімічний склад і робочі умови.
Зеленим (вольфрамом без домішок) та білим (з добавкою цирконію) електродом з'єднують деталі з алюмінію, магнію та сплавів на змінному струмі. На постійному функціонують розхідник червоний (збагачений оксидом торію та стикуючий нержавіючі сталі, молібден, мідь та нікель) та темно-синій (з оксидом ітрію, призначений для складних конструкцій зі сталей, титану та міді). Сірий (з оксидом церію), синій і золотий (з домішкою лантану) – універсали, що забезпечують зварювання міді, бронзи, всіх типів.та на обох видах струму.
"Огляд сильних та слабких сторін"
Крім властивостей, що диктуються матеріалом, тугоплавкі електроди мають спільні риси. Якісним зварюванням роблять:
- стабільність дугового розряду у будь-якому режимі підключення;
- можливість змінювати кут нахилу, швидкість подачі та різновиди присадки, завдяки чому варіюється хімічний склад металу;
- здатність поєднувати елементи з різнорідних металів;
- мінімізація ризику появи дефектів при зварюванні та різанні завдяки точковій спрямованості високих температур.
Але є й проблеми:
- збільшуються енерговитрати;
- роботу ведуть лише у закритому приміщенні, щоб вітер не видував захисний газ на шляху до пальника;
- доводиться зачищати патьоки від розпалювання дуги, які можуть виникнути навколо зварювальної зони.
Чому важливі заточення стрижня та полярність
І все-таки будь-які проблеми переборні, особливо якщо дотримуватися перевірених правил. Перед початком роботи розплавники, що не плавляться, обов'язково заточують, оскільки від геометрії кінчика стрижня залежить конфігурація зварювального шва і параметри плавлення металу. Заточування графітових провідників проводять під кутом 60-70º, вольфрамових – 10-30º.
Заточіть відразу обидва краї електрода, що не плавиться. Коли один перегріється, просто поверніть утримувач на 180 º і зварюйте іншим кінцем. Економія часу очевидна!
Потрібні параметри зварювального зчеплення також визначає полярність. Для утворення глибокого тонкого шва вона має бути пряма: електрод підключений до «-», метал поставлений на «+». При зворотній полярності стик виходить широким та плоским.
"І насамкінець ще один парадокс. Неплавлячі провідники при тривалому зварюванні все ж таки потроху скорочуються по довжині."
Цей процес уповільнюється, якщо першим подають інертний газ і потім запалюють дугу. А робочий ресурс саме вольфрамових електродів продовжує попереднє запалювання на окремій графітовій пластині дуги, яку потім переносять до місця зварювання.