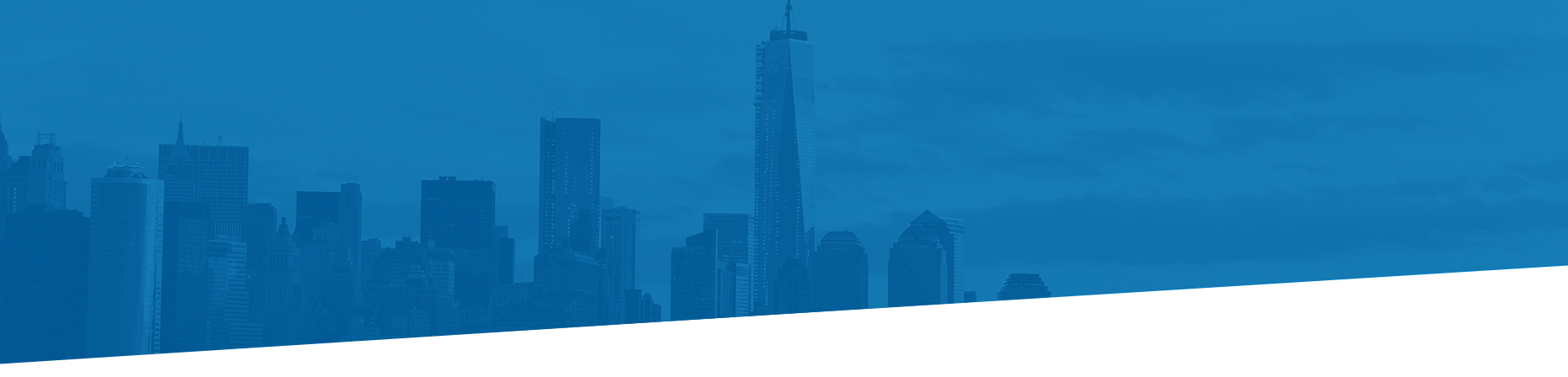
СПЕЦТЕХНОЛОГІЯ ГР.27
Тема: Джерела електричної енергії
Учбові питання
1. Акумуляторна батарея.
2. Маркування акумуляторних батарей.
3 Літій - іонний акумулятор
4 Генератор.
5.Регулювальні пристрої генератора.
1. Акумуляторна батарея являється джерелом енергії при непрацюючому двигуні. Акумуляторні батареї за принципом дії діляться на дві групи: кислотні і лужні. В свою чергу кислотні акумулятори діляться на обслуговувані і необслуговувані. Розглянемо будову кислотної акумуляторної батареї. Вона складається з окремих акумуляторів зєднаних між собою послідовно. Напруга на виході кожного акумулятора 2 В. Будова акумулятора: корпус, блок позитивно заряджених пластин,блок негативно заряджених пластин,сепаратори, електроліт,вивідні штирі. Корпус виготовляється з кислотостійкої пластмаси. Решітки пластин виготовлені з свинцю. В решітки пластин запресовуується активна маса. В негативно заряджені пластини - свинець , в позитивно заряджені - сполуки свинцю. Сепаратори запобігають виникненню короткого замикання між позитивно і негативно зарядженою пластиною. Виготовляються з пластмаси. Електроліт являє собою водний розчин сірчаної кислоти. Густина електроліту залежить від кліматичних умов експлуатації транспортного засобу. Чим нижча температура оточуючого середовища , тим вища повинна бути густина електроліту.
2. У маркуванні кислотних акумуляторних батарей вказують такі показники:
а) кількість акумуляторів
б) тип батареї
в) ємність в ампер- годинах
г) матеріал корпусу, сепаратора
Чим є лужні акумулятори
Що він собою являє і що використовується при його виготовленні? Лужний акумулятор – це накопичувач електричної енергії. У ньому активна маса негативного електрода – пластина, зроблена з пористого кадмію або заліза. В якості позитивного використовується нікелевий каркас, який заповнює окисом тривалентного цього ж матеріалу. Електролітом виступає 20% розчин їдкого калію. Електричні властивості проявляються завдяки перетворення енергії з електричної в хімічній і навпаки. Перший процес називається зарядкою. Другий – розрядкою. Зарядка лужних акумуляторів не викликає проблем, якщо використовувати якісно виготовлені засоби, щоб підтримувати батареї в робочому стані.
Пристрій
Як же влаштований цей накопичувач енергії? У загальних рисах це було змальовано, давайте зупинимося більш детально. Позитивний електрод, коли він заряджений, є гідратом окису нікелю з домішками окису барію і графіту. Останній з них збільшує електропровідність. Окис барію позитивно позначається на терміні служби електрода. Негативний же складається головним чином з порошкового заліза. Також можуть бути його окису, сірчанокислий нікель і порошок кадмію. Електроліт – це їдкий калій в який добавлений моногідрат літію (з розрахунком у 20-30 грам на один літр). Завдяки цій домішки збільшується загальний термін роботи батареї. Ось такий пристрій лужного акумулятора і воно забезпечує характеристики, що роблять цей тип джерела енергії популярним.
Випуск
Якщо говорити про те, що постачає промисловість під маркою «лужні акумулятори», то в першу чергу необхідно говорити про:
- Нікелево-залізних. У цих акумуляторах позитивні панцирні пластини розташовані між 2-ма негативними.
- Нікелево-кадмієві. У цих акумуляторах негативні пластини розташовані між 2-ма позитивними.
У них обох електроди зроблені у вигляді рамками зі сталі. В їх пази були впресовані пакети, наповнені активною масою. Самі вони зроблені з нікельованої жерсті, в якій є багато різних дрібних отворів, через які здійснюється взаємодія вмісту з електролітом. Щоб усунути можливість короткого замикання між пластинами, встановлюються сепаратори, які виконані у вигляді поліхлорвінілових сіток ебонітових або стрижнів. Є особливості й з корпусом. Так, щоб пластини і електроліт його не пошкодив, то він виготовляється з нікельованої жерсті. Для виходу газів використовується приварена кришка, в якій є отвори.
Робота
Під час функціонування до позитивних якостей, якими володіють акумулятори лужні, відносять те, що компоненти, які виникають при заряді і розряді, майже не розчиняються в електроліті. Також вони не вступають в хімічні реакції, які можуть вплинути на працездатність батареї. Завдяки цьому, також не витрачається електроліт, то лужні акумулятори мають дуже компактні розміри, порівняно з іншими. А що ж про них говорять люди? Чим є з точки зору користувачів лужні акумулятори? Відгуки дадуть зрозуміти це:
- При виборі важливо було місце, що будуть займати батареї. Акумулятори лужні ідеально підійшли по всім умовам, як по напрузі, так і по компактності.
- Батареї даного типу відрізняються надійністю роботи, тривалим терміном служби і рекомендуються всім, кому необхідно часто з ними працювати.
Особливості експлуатації
Що необхідно робити під час експлуатації? Дотримуйтесь ряд правил, і ризик виникнення проблем буде мінімальним:
- Періодично перевіряйте рівень електроліту і заряд акумулятора.
- Утримуйте в чистоті.
- Періодично заряджайте батареї, навіть якщо ви не використовуєте їх.
Про лужні акумулятори можна сказати, що вони досить стійкі до пошкоджень, але краще стежити, щоб з ними нічого не відбувалося. Також підзарядку при невикористанні необхідно робити приблизно раз на рік (за цей час розсіюється близько 25-30% заряду).
3Літій-іонний акумулятор
Літій-іонний акумулятор (англ. Lithium-ion battery, скорочено Li-ion) - один з двох основних типів літієвих електричних акумуляторів з категорії вторинних електричних батарей, який різниться з літій-полімерним акумулятором лише типом електроліту, що використовується при їх виготовленні.[1] Широко розповсюджений в побутовій електроніці.
Назву літій-іонні акумулятори одержали через те, що електричний струм в зовнішньому колі з'являється через перенос літієвих іонів від анода до катода на основі різних сполук.
Хімічний склад, експлуатаційні характеристики, вартість та безпечність акумуляторів відрізняються залежно від типу літій-іонних акумуляторів. Найбільш поширеним у переносній електроніці є акумулятори з катодом на оксиді кобальту (LiCoO2), що мають високу енергетичну густину, але мають недолік з точки зору безпеки експлуатації, особливо при пошкодженні. Літій-ферум-фосфатні (відомі як літій-залізо-фосфатні, LiFePO4), літій-манган-оксидні (LiMn2O4, Li2MnO3 або літій-манганові акумулятори LMO) та літій-нікель-манган-кобальт-оксидні (LiNiMnCoO2 чи NMC) акумулятори, що теж названі за типом катоду, пропонують нижчі рівні енергетичної густини, але мають довший життєвий цикл та безпечніші з хімічної точки зору. Такі акумулятори широко застосовуються в електроінструментах, медичному обладнанні та ін. NMC, зокрема, є лідером за використанням в автомобільній промисловості. Літій-нікель-кобальт-алюміній-оксидні (LiNiCoAlO2 або NCA), що теж названий за катодом, та літій-титанатові (Li4Ti4O12 чи LTO) акумулятори (назва останнього за анодом), спеціально розроблені для певних нішових ролей. Нові літій-сульфурні акумулятори обіцяють найвище відношення експлуатаційних характеристик до ваги
Перший літій-іонний акумулятор вивела на ринок корпорація Sony в 1991 році.
Спроби розробити літієві електричні батареї, що перезаряджаються, проводилися в 70-х р. ХХ ст., але були невдалими через неможливість забезпечення потрібного рівня безпеки при їх експлуатації оскільки літій занадто активний і настільки бурхливо реагує з водою, що може спалахнути. Було встановлено, що в ході циклів заряду-розряду електричної батареї з металевим літієвим електродом може виникнути коротке замикання всередині акумуляторної батареї. При цьому температура всередині акумулятора може досягти температури плавлення літію. У результаті бурхливої хімічної взаємодії літію з електролітом відбувається вибух
Сучасні літій-іонні акумулятори мають високі показники: 100-180 Вт·год/кг і 250-400 Вт·год/дм3, робоча напруга - 3,5-3,7 В.
Якщо ще кілька років тому розробники вважали досяжною ємність літій-іонних акумуляторів не більше кількох ампер-годин, то нині більшість причин, що обмежують збільшення ємності, подолано і багато виробників почали випускати акумулятори ємністю в сотні ампер-годин.
- Енергетична місткість: 110 ... 200 Вт·год/кг
- Внутрішній опір: 150 ... 250 мОм (для батареї 7,2 В)
- Число циклів заряд/розряд до втрати 20 % місткості: 500-1000
- Час швидкого заряду: 2-4 години
- Допустимий перезаряд: дуже низький
- Саморозряд при кімнатній температурі: 7 % в рік
- Напруга максимальна в елементі: 4,18..4,20 В (повністю заряджений)
- Напруга мінімальна: 2,5..2,75 В(повністю розряджений)
- Струм навантаження відносно місткості (С):
- - піковий: понад 2С
- - найбільше допустимий: до 1С
- Діапазон робочих температур: −20 - +60 °C
- обслуговування: не реґламентується
Сучасні малогабаритні акумулятори працездатні при струмах розряду до 2С, потужні - до 10-20С. Діапазон робочих температур: від −20 до +60оС. Але багато виробників вже розробили акумулятори, працездатні при −40 °С. Можливе розширення температурного діапазону і в бік вищих температур.
В основному Li-ion акумулятори краще всього функціонують при кімнатній температурі. Робота при підвищеній температурі скорочує термін дії їх використання.[1] Підвищена температура тимчасово протидіє внутрішньому опору акумулятора, збільшення якого призводить до його зносу.
Саморозряд становить 4-6 % за перший місяць, потім - значно менше: за 12 місяців акумулятори втрачають 10-20 % запасеної ємності.[1] Втрати ємності в кілька разів менші, ніж у нікель-кадмієвих акумуляторів, як при 20оС, так і при 40оС.
Ресурс - 500-1000 циклів.[1]
Всі літієві акумулятори мають досить прийнятні для зберігання параметри. Втрата ємності за рахунок саморозряду 5-10 % за рік.
До недоліків Li-ion акумуляторів варто віднести чутливість до перезарядження і сильного розряду, через це вони повинні мати обмежувачі заряду й розряду.[1
Принцип роботи Li-ion акумуляторів заснований на переміщенні позитивно заряджених іонів літію Li+ між позитивними й негативними електродами в процесі розрядки й зарядки. Металевий літій у цих процесах участі не бере,[1] тому не виникає будь-яких проблем з відновленням електродів, що забезпечує стабільність і безпеку при використанні батареї.
Наявність негативного електрода, який приймає і віддає іони, є загальним для всіх систем, але існує широкий вибір матеріалів, придатних для реалізації позитивного електрода й здатних забезпечувати різницю потенціалів між електродами до 3 В.
Для нормальної роботи будь-якої електрохімічної батареї необхідно як мінімум три компоненти: два електроди й електроліт , що забезпечує перенос іонів. У малогабаритних батареях електроліт може бути твердим, рідким і желеподібним. Рідкі електроліти застосовуються, як правило, у клеєних циліндричних батареях, але через високу небезпеку займання вони не знайшли застосування в інших системах. Для розробки твердих електролітів для літієвих акумуляторів, що мають можливість перезаряджання, пішло два десятиліття напружених досліджень. На їх основі стало можливим створення тонких і пласких батарей, але з невеликим діапазоном робочих температур та малою потужністю.
Літій-іонні акумулятори доступні в різних форм-факторах, які в цілому можна розділити на чотири групи:[3][4]
- Невеликі циліндричні (тверді тіла без терміналів, таких як батареї для портативних комп'ютерів)
- Великі циліндричні (тверде тіло з великими гвинтовими клемами)
- В чохлах (м'які, плоскі тіла, такі, як ті, які використовуються в мобільних телефонах)
- Призматичні (напівжорсткий пластиковий корпус з великими гвинтовими клемами), наприклад, у габариті 6T для бронетехніки[5]
Конструктивно Li-ion акумулятори, як і лужні (Ni-Cd, Ni-MH), виготовляються в циліндричному і призматичному варіантах.
У циліндричних акумуляторах згорнутий у вигляді рулону пакет електродів і сепаратора вбудований у сталевий або алюмінієвий корпус, з яким з'єднаний негативний електрод. Позитивний полюс акумулятора виведений через ізолятор на кришку.
Призматичні акумулятори виготовляються шляхом складання прямокутних пластин одна на одну. Вони забезпечують щільніше упакування в акумуляторній батареї, але, на відміну від циліндричних акумуляторів, складніше витримують стискуючі зусилля на електроди.[1] У деяких призматичних акумуляторах застосовується рулонне складання пакета електродів, що скручується в еліптичну спіраль.[1]
Деякі конструктивні заходи звичайно застосовують і для запобігання швидкому розігріву і забезпечення безпечної роботи Li-ion акумуляторів. Під кришкою акумулятора є пристрій, що реагує на позитивний температурний коефіцієнт збільшенням опору, і, який розриває електричний зв'язок між катодом і позитивною клемою при підвищенні тиску газів всередині акумулятора вище допустимої норми. Для підвищення рівня безпеки експлуатації Li-ion акумуляторів у складі батареї обов'язково застосовується також і зовнішній електронний захист, мета якого не допустити перезарядження й перерозрядження, короткого замикання й надмірного розігрівання.
Конструкція Li-ion та інших літієвих акумуляторів, як і конструкція всіх первинних батарей з літієвим анодом, відрізняється абсолютною герметичністю. Вимога абсолютної герметичності визначається як неприпустимістю витікання рідкого електроліту (негативно діючого на прилади) і недопустимість потрапляння в акумулятор кисню і вологи з навколишнього середовища, оскільки вони реагують із матеріалами електродів й електроліту, повністю виводячи акумулятор із ладу.
Вбудовані системи захисту
Li-ion акумуляторні батареї комерційного призначення мають найбільш досконалий захист, порівняно з усіма типами батарей. Як правило, у схемі захисту Li-ion батарей використовується ключ на польовому транзисторі, який при досягненні на елементі батареї напруги 4,30 В відкривається й тим самим перериває процес заряду. Крім того, наявний термозапобіжник, який при нагріванні батареї до 90оС від'єднує коло її навантаження, забезпечуючи її термозахист.
Деякі акумулятори мають вимикач, який спрацьовує при досягненні граничного рівня тиску всередині корпуса, рівного 1034 кПа (10,5 кг/м2), і розриває ланцюг навантаження. Є й схема захисту від глибокого розряду, що стежить за напругою акумуляторної батареї й розриває ланцюг навантаження, якщо напруга на елемент знизиться до рівня 2,5 В.
Внутрішній опір схеми захисту акумуляторної батареї мобільного телефону в увімкненому стані дорівнює 0,05- 0,1 Ом. Конструктивно вона складається з двох ключів, з'єднаних послідовно. Один з них спрацьовує при досягненні верхнього, а інший - нижнього порогів напруги на батареї. Загальний опір цих ключів фактично створює подвоєння її внутрішнього опору, особливо, якщо батарея складається лише з одного акумулятора.
У деяких Li-ion батареях, в яких використовують марганець, що мають 1-2 елементи; схема захисту не застосовується. Замість цього в них установлено лише один запобіжник. І такі батареї є безпечними завдяки їх невеликим габаритам та ємності. Крім того, марганець досить «терплячий» до порушень правил експлуатації Li-ion батареї. Відсутність схеми захисту зменшує вартість Li-ion батареї, але породжує нові проблеми.
При використанні недорогих зарядних пристроїв, призначених для підзарядки від мережі або від бортової мережі автомобіля, можна бути впевненим, що за наявності в батареї схеми захисту, вона відключить її при досягненні напруги кінця заряду. Якщо схему захисту в акумуляторі не передбачено, станеться перезаряд батареї і, як наслідок, її незворотний вихід з ладу. Цей процес супроводжується підвищеним нагріванням і роздуттям корпуса батареї.
Технологічні операції виробництва електродів та інших деталей, а також складання акумуляторів проводять в особливих сухих кімнатах або герметичних боксах в атмосфері чистого аргону.
При складанні акумуляторів застосовують складні сучасні технології зварювання та конструкції гермовиводів.
Закладка активних мас електродів є компромісом між бажанням досягти максимуму розрядної ємності акумулятора й вимогою гарантувати безпечну його роботу для запобігання утворення металевого літію (і тим самим можливості займання). Збільшення активних мас потенційно знижує рівень безпеки при експлуатації акумулятора.
Акумулятори збирають у розрядженому стані.[1] Для приведення в дію їх необхідно зарядити.
При першому циклі заряду-розряду літій-іонні акумулятори втрачають частину ємності, тому що у процесі першого заряду крім впровадження літію в структуру вуглецевого матеріалу відбувається розкладання електроліту з утворенням плівки, що має лише іонну провідність. Утворення пасивної плівки призводить до незворотної втрати до 20-30 % закладеної ємності.[1] Для зниження цих втрат рекомендують як добавки в електроліт, так і різного роду обробку поверхні вуглецевого матеріалу. Починаючи із другого циклу, процес розряду і заряду літій-іонного акумулятора зводиться до переносу іонів літію від анода до катода й назад. Коефіцієнт використання по струму при цьому близький до одиниці.[1]
Інноваційні способи виробництва
2018 року інженери з Техаського та Дюкського університетів надрукувала браслет зі світлодіодом та літій-іонним акумулятором на 3D-принтері. Цей пристрій випромінював світло впродовж 60 секунд. Розробники визнають, що цього замало, аби починати бодай мріяти про комерційне застосування на цьому етапі, та вони мають кілька ідей, як збільшити ємність. Наприклад, хочуть замінити матеріали на основі полілактидів на 3D-друковані пасти.[6]
Хімічні процеси Li-ion акумуляторів
Для того, щоб напруга акумулятора була достатньо високою, дослідники використали оксид кобальту як активний матеріал позитивного електрода. Літійований оксид кобальту (точніше кобальтат літію) має потенціал близько 4 В відносно літієвого електрода, тому робоча напруга Li-ion акумулятора має характерне значення 3 В і вище.[1]
Матеріали на основі кобальту вимагають контролера для керування процесами заряд-розряд. Li/Ni02 (літій/оксид нікелю) має вищу ємність, ніж оксид кобальту, але він складний у виготовленні й може мати проблеми в плані техніки безпеки. Тому для підвищення безпеки в акумуляторах великої ємності почали використовувати змішані оксиди кобальту й нікелю (20-30 % нікелю).
При розряді Li-ion акумулятора відбувається деінтеркаляція (вилучення) літію з вуглецевого матеріалу (на негативному електроді) та інтеркаляція (упровадження) літію в оксид (на позитивному електроді). При заряді акумулятора процеси проходять у зворотному напрямку. Отже, у всій системі відсутній металевий (нуль-валентний) літій, а процеси розряду й заряду зводяться до переносу іонів літію з одного електрода на іншій. Тому такі акумулятори одержали назву «літій-іонні».
Процеси на негативному електроді Li-ion акумулятора. Для всіх типів Li-ion акумуляторів, які доведені до комерціалізації, негативний електрод виготовляється з вуглецевих матеріалів. Інтеркаляція літію у вуглецевих матеріалах - це складний процес, механізм і кінетика якого істотно залежать від природи вуглецевого матеріалу і природи електроліту.
Вуглецева матриця, яка застосовується в аноді, може мати впорядковану шарувату структуру, як у природного або синтетичного графіту, невпорядковану аморфну або частково впорядковану (кокс, піролізний або мезофазний вуглець, сажа та ін.).[1]
Іони літію при впровадженні розштовхують шари вуглецевої матриці і розташовуються між ними, утворюючи інтеркаляти різноманітних структур. Питомий обсяг вуглецевих матеріалів у процесі інтеркаляції-деінтеркаляції іонів літію значно не змінюється.
Крім вуглецевих матеріалів як матрицю негативного електрода використовують структури на основі олова, срібла і їх сплавів, сульфіди олова, фосфати кобальту, композити вуглецю з наночастками кремнію.[1]
Процеси на позитивному електроді Li-ion акумулятора. Якщо в первинних літієвих батареях застосовуються різноманітні активні матеріали для позитивного електрода, то в літієвих акумуляторах вибір матеріалу позитивного електрода обмежений.
Позитивні електроди літій-іонних акумуляторів створюються винятково з літійованих оксидів кобальту або нікелю і з літій-марганцевих шпінелей.[1]
У даний час як катодні матеріали все частіше застосовуються матеріали на основі змішаних оксидів або фосфатів.
3 практики видно, що з використання катодів зі змішаних оксидів досягаються найкращі характеристики акумулятора. Освоюються і технології покриття поверхні катодів тонкодисперсними оксидами. При заряді Li-ion акумулятора відбуваються реакції на позитивних пластинах:
LiCo02 → Li 1-хСоО2 + xLi+ + хе-
і на негативних пластинах:
С + xLi+ + хе- → CLix.
При прикладенні постійної напруги іони літію виходять з анода, проходять через електроліт і осідають у графіті, заряджаючи його. При відключенні напруги в електроліті утворюється подвійний шар, який не дозволяє іонам перебігти назад. Розрядка відбувається практично тільки за рахунок електричного струму через зовнішнє коло.
Маркування
Відповідно до принципів позначень МЕК (Міжнародної електротехнічної комісії) у найменуванні літій-іонних акумуляторів перша буква І означає електрохімічну систему, друга - матеріал катода (С, N або М для кобальту, нікелю або марганцю), третя буква R або Р - конструктивне виконання (циліндричне або призматичне). Цифри після букв позначають у циліндричних акумуляторах діаметр (мм, дві цифри) і висоту (десятих мм, три цифри), призматичних - довжину, ширину й висоту (мм) послідовно.[1]
Багато компаній уводять свої літерні позначення типів, але цифри в їх найменуваннях відповідають вимогам МЕК.
Заходи безпеки при поводженні з акумулятором
Для запобігання витоку електроліту, нагрівання й вибуху потрібно дотримуватись таких правил безпеки:
• не занурювати акумулятор у воду, зберігати його в сухому прохолодному місці, якщо він не використовується;
• не використовувати і не залишати акумулятор поблизу джерел відкритого вогню або тепла;
• для зарядження використовувати тільки призначені для цього акумулятора зарядні пристрої;
• не підключати акумулятор до пристроїв, не призначених для живлення від нього;
• не кидати акумулятор у вогонь і не нагрівати його;
• не замикати між собою позитивний і негативний виводи акумулятора металевими предметами або дротами;
• не зберігати акумулятор разом з металевими предметами, такими як скріпки або шпильки;
• не зчавлювати, не кидати й не піддавати акумулятор механічним впливам;
• не паяти акумулятор та не проколювати його гострими предметами.
4. Генератор - джерело електричної енергії при працючому двигуні.Генератор складається з таких основних частин: корпус, кришки корпусу,статор, ротор, вентилятор, випрямний блок,шків приводу.Статор - нерухома частина генератора, виготовляється у вигляді кільця з окремих ізольованих пластин па внутрішній поверхні якого розміщується обмотка статора.Ротор - рухома частина генератора яка складається з вала,підшипників,обмотки збудження,контактних кілець, шести пар полюсів . Живлення до обмотки збудження подається з допомогою щіток, які закріплені у щіткотримачах.
5 До регулювальних пристроїв генератора відноситься регулятор напруги . Регулятор напруги може мати перемикач " зима - літо" завдяки якому регулюється величина напруги струму генератора в залежності від сезону експлуатації транспортного засобу.
Література: В. Ф. Кисликов , В. В. Лущик " Будова й експлуатація автомобілів" стр.176 - 182
Тема : Система запалювання
Система запалювання - одна з найважливіших систем керування двигуном автомобіля. Призначається дана технологія для запалення суміші бензину і повітря в двигуні. Забезпечується це за рахунок появи іскри. Запалення є складовою частиною системи електрообладнання машини.
Безконтактна система запалювання автомобіля ВАЗ 2110 складається з таких основних елементів:
- акумулятор автомобіля;
- генератор;
- роз'єм;
- вимикач запалювання;
- датчик-розподільник;
- комутатор;
- свічки;
- котушка запалювання.
На ВАЗ 2110 відмовилися від таких звичних елементів як котушка запалювання та розподільник. Так, тут використаний спеціальний модуль запалювання, що складається з керуючої електроніки високої енергії, а також пари котушок. Важливо відзначити, що така система не вимагає частого сервісного обслуговування, т. к. рухомих деталей тут немає. Спеціальних регулювань система запалювання ВАЗ 2110 також не вимагає, оскільки для цього тут встановлений контролер. Він і здійснює всі настроювання та регулювання.
Система запалювання заснована на методі «холостій іскри». Це спеціальний метод розподілу іскри. Як відомо, циліндри у двигуні автомобіля працюють попарно (1-й циліндр з 4-м, а 2-й з 3-м). Так, іскра спрацьовує відразу в двох циліндрах: робоча іскра в тому циліндрі, де відбувається такт стиснення суміші, а холоста іскра в тому, де здійснюється такт випуску. Оскільки струм в обмотках котушок системи постійний, виходить, що на першій свічці електрони рухаються від центрального електрода до бічного, а на другій - навпаки (від бічного до центрального).
Залежно від типу двигуна на ВАЗ 2110 можуть використовуватися два типи свічок запалювання. Так, для 8-клапанних двигунів застосовуються свічки типу А17ДВРМ, а для 16-клапанних двигунів - АУ17ДВРМ (тут розмір під ключ зменшено до 16 мм). При цьому відстань між електродами свічок всього близько 1,0-1,15 мм
Як ми вже відзначали вище, за керування запалюванням відповідає такий елемент, як контролер. Щоб найбільш точно управляти системою, контролер аналізує наступну інформацію:
- температуру охолоджуючої рідини;
- поточне положення та частоту обертання колінвала;
- наявність детонації;
- витрата повітря (навантаження двигуна).
Аналіз положення колінвала здійснюється за допомогою спеціального датчика, який передає інформацію на контролер. Тільки після цього розраховується послідовність спрацьовування котушок модуля запалювання
Схема безконтактної системи запалювання
- безконтактний датчик
- датчик розподільник
- свічки запалювання
- комутатор
- котушка запалювання
- монтажний блок
- реле запалювання
- вимикач запалювання
Принцип роботи безконтактної системи запалювання
- При повороті ключа запалювання струм від акумуляторної батареї подається на монтажний блок.
- З монтажного блоку струм низької напруги розподіляється між котушкою запалювання, стартером та іншими електроприладами.
- Стартер прокручує двигун, одночасно від датчика імпульсів з двигуна надходить сигнал на транзисторний комутатор.
- Транзисторний комутатор перериває струм на первинній обмотці котушки запалювання, що створює струм високої напруги на вторинній обмотці.
- Струм високої напруги надходить на центральну клему котушки запалювання і надходить на розподільник запалювання.
- Залежно від положення колінвала струм високої напруги попадає по дротах високої напруги до відповідної свічці запалювання.
- Струм створює іскровий розряд, який запалює паливну суміш
Залежно від оборотів колінвала регулюється кут запалювання відцентровим регулятором.
Тема: Зчеплення
Зчеплення є важливим конструктивним елементом трансмісії автомобіля. Головне завдання зчеплення автомобіля - передати крутний момент від двигуна. При роботі зчеплення короткочасно від'єднує двигун від трансмісії і потім плавно їх з'єднує. Крім усього іншого зчеплення охороняє деталі трансмісії від перевантажень. Про це ми і розповімо у статті «Ремонт і технічне обслуговування зчеплення».
Зчеплення складається з приводу, що включає в себе педаль, тягу, вилку і муфту з вижимним підшипником. Як тільки водій відпустить педаль зчеплення буде включено. Включення відбувається у момент, коли ведений диск притиснутий до маховика натискним диском за допомогою пружини. Шляхом тертя поверхні веденого диска з маховиком і натискним диском відбувається процес зчеплення. Як тільки водій натисне на педаль зчеплення, він вимкнеться. Вимикання відбувається через переміщення до маховика муфти з вижимним підшипником, при цьому відсувається натискний диск від веденого диска. То є ведучі і ведені деталі зчеплення між собою роз'єднуються.
Зчеплення здійснюється за допомогою силової муфти, в якості якої можуть виступати фрикційні, гідравлічні та електромагнітні муфти. Залежно від того, яка муфта встановлена, і передача обертального моменту здійснюється силами тертя, гідродинамічними силами або за допомогою електромагнітного поля. Зчеплення призначене для з'єднання або тимчасового роз'єднання двигуна і трансмісії. Тимчасово роз'єднати двигун і трансмісію потрібно під час перемикання передач, при зупинці або гальмуванні. А після того, як автомобіль рушить з місця і після перемикання передач необхідно їх плавно з'єднати.
Трансмісія з подвійним зчепленням
Трансмі́сія з подві́йним зче́пленням (англ. dual-clutch transmisstion, DCT) - автомобільна трансмісія у якій муфта зчеплення складається з двох фрикційних муфт, які працюють почергово при перемиканні передач. Така конструкція найчастіше використовується для оснащення роботизованих коробок передач, що забезпечує парні і непарні передачі фактично окремими муфтами зчеплення. Тому часто, коли мова йде про подвійне зчеплення використовують поняття «коробка передач з подвійним зчепленням» або «трансмісія з подвійним зчепленням» (англ. dual-clutch transmission, DCT), так як муфта подвійного зчеплення тісно пов'язана з особливою конфігурацією коробки перемикання передач. Така конструкція створює можливість попереднього вибору чергової передачі чим скорочує час на перемикання передач, яке відбувається практично без розриву потоку потужності від двигуна на колеса автомобіля. Тому іншою назвою роботизованої коробки передач з подвійним зчепленням ще є - преселективна коробка передач (від англ. preselect - попередньо обрати)
Ідея створення трансмісії, що має два зчеплення, належить французькому інженеру-механіку і винахіднику Адольфу Кегрессу[fr][1]. У другій половині 1930-х він висунув ідею та спроектував автоматичну коробку перемикання передач з подвійним зчепленням, яку сподівався встановити на легендарний Citroën Traction. Але складне фінансове становище компанії на той час не дозволило планам здійснитися.
Реальне застосування подвійного зчеплення у конструкції коробок передач розпочалось з 1980 року завдяки розробкам компаній Porsche та Audi для своїх спортивних автомобілів. У 1986 році Porsche 962, оснащений саме цією коробкою, переміг у 1000-кілометровій гонці на автодромі у Монці. У подальшому подвійне зчеплення стало використовуватись у таких конструкціях коробок перемикання передач серійних автомобілів:
- DSG (нім. Direkt Schalt Getrieb) від Volkswagen[2];
- M DCT (англ. M double-clutch transmission) від BMW[3];
- «Powershift» від Ford[4];
- «Speedshift» від Mercedes-Benz;
- DDCT (англ. Dual Dry Cutch Trasmission) від Fiat Powertrain Technologies[en];
- EDC (англ. Efficient Dual Clutch) від Renault;
- DCS (англ. Dual Clutch System) від Groupe PSA;
- DCT (англ. Dual-Clutch Transmission) від Kia Motors;
- «S-tronic» від Audi;
- «Twin Clutch SST» від Mitsubishi;
- 7DT від Porsche.
Через високу технічну складність конструкції виробників подвійного зчеплення є небагато і серед них такі компанії як:
- BorgWarner («мокре» зчеплення для Volkswagen);
- Getrag з 2018 Magna PT[en] (коробки передач з як із «сухим», так і «мокрим» подвійним зчепленням для BMW, Chrysler, Dodge, Ferrari, Ford, Mercedes-Benz, Mitsubishi, Renault, Volvo);
- Schaeffler Group[en] під брендом «LuK» («сухе» зчеплення для Volkswagen);
- Ricardo plc[en] (коробка передач для Bugatti Veyron);
- ZF Friedrichshafen AG (коробка передач для Porsche);
- Fiat Powertrain Technologies[en] (коробки передач для Alfa Romeo, Fiat, Jeep, Suzuki).
Низка автомобільних компаній у конструкції трансмісій можуть використовувати компоненти від різних виробників, наприклад, в M DCT (BMW) використовується коробка передач від «Getrag», а подвійне зчеплення від «BorgWarner».
Розрізняють два основні типи конструкцій подвійного зчеплення: «сухе» (фрикційні диски у повітрі) і «мокре» (багатодискове зчеплення знаходится зануреним в оливі).
«Мокре» подвійне зчеплення
Конструктивно подвійне зчеплення мокрого типу об'єднує два пакети фрикційних дисків, поміщених у корпус. Частина дисків обох пакетів жорстко пов'язана з корпусом зчеплення. Корпус, у свою чергу, через маточини з'єднаний з двигуном. Інша частина дисків закріплена на своїх маточинах, які посаджені на первинні вали відповідних рядів передач.
Нормальне положення зчеплення - розімкнене. Замикання зчеплення (стискання пакетів дисків) здійснюється за допомогою гідроциліндрів під керуванням електрогідравлічного модуля. У вихідне положення диски повертаються за допомогою пружин.
Залежно від конструкції зчеплення пакети фрикційних дисків можуть мати концентричне (муфти розташовані в одній площині, перпендикулярно до первинного вала) або паралельне розташування (муфти розташовуються одна за одною паралельно).
Концентричне розташування муфт є компактнішим, тому застосовується в трансмісіях передньоприводних автомобілів (при поперечному розташуванні двигуна). При концентричному розташуванні зовнішня муфта обслуговує непарні передачі, внутрішня - парні передачі. В силу своєї конструкції (велика площа дисків) зовнішня муфта розрахована на передачу більшого крутного моменту. Подвійне зчеплення з паралельним розташуванням дисків застосовується, в основному, на задньоприводних автомобілях.
«Сухе» подвійне зчеплення
Подвійне зчеплення сухого типу включає ведучий диск, з'єднаний з двохмасовим маховиком, два сухих диски зчеплення, розташованих на первинних валах коробки передач, два натискних диски, дві діафрагмових пружини, два витискні підшипники і два важелі включення зчеплення. Нормальне положення сухого зчеплення - розімкнуте.
Принцип роботи зчеплення полягає у передаванні крутного моменту від ведучого диска на відповідний диск зчеплення і далі на свій первинний вал коробки передач. Кожне із сухих зчеплень працює незалежно одне від одного.
При замиканні зчеплення важіль увімкнення притискає витискний підшипник до діафрагмової пружини, яка у свою чергу передає зусилля на натискний диск і далі на диск зчеплення. Диск зчеплення притискається до ведучого диска і крутний момент передається на первинний вал коробки передач.
Порівняння двох типів подвійного зчеплення
«Мокре» зчеплення має краще охолодження, тому може застосовуватись для передавання більшого крутного моменту (до 350 Нм і більше). Наприклад, «мокре» зчеплення у коробці передач «Bugatti Veyron» забезпечує передачу крутного моменту до 1250 Нм. Межа «сухого» зчеплення - 250 Нм. Разом з тим, «сухе» зчеплення є ефективнішим в експлуатації, оскільки в ньому відсутні витрати потужності двигуна на урухомлення масляного насоса
Переваги
- Конструкція з двома поперемінно працюючими валами дозволяє добитися максимальної плавності у їзді.
- Переключення передач здійснюється за максимально короткий проміжок часу (до 0,12 с).
- Підтримання й передавання крутного моменту без відчутних втрат при перемиканні.
- Менша (до 10 %) витрата пального (навіть у порівнянні з механічними коробками перемикання передач).
- Висока динамічність при розгоні.
Недоліки
- Малий ресурс пробігу, при поміркованій експлуатаці пробіг до ремонту становить 60...80 тис. кілометрів.
- Конструкція коробок перемикання передач є складнішою у порівнянні з автоматичною чи механчною коробкою перемикання передач, що обумовлює відповідно вищу ціну.
- Не всі автомобільні майстерні можуть надати кваліфіковані послуги з ремонту і обслуговування таких трансмісій.
- Через складність і дороговизну матеріалів обслуговування трансмісій з подвійним зчепленням є зна дорожч
- Тема: Коробка передач
Щоб автомобіль пересувався по дорозі, мало мати під капотом потужний і ефективний мотор. Крутний момент від колінчастого вала повинен якось передаватися на провідні колеса транспортного засобу.
З цією метою було створено спеціальний механізм - коробка передач. Розглянемо її пристрій і призначення, а також чим відрізняються різні модифікації КП.
ПРИЗНАЧЕННЯ КОРОБКИ ПЕРЕДАЧ
Якщо сказати коротко, то коробка передач призначена для передачі крутного моменту від силового агрегату на провідні колеса. Трансмісія також перетворює швидкість обертання колінвала так, щоб водій міг розігнати машину, не розкручуючи мотор до максимальних обертів.
Даний механізм підбирається під параметри ДВС, щоб максимально використовувати весь ресурс двигуна без шкоди для його деталей. Завдяки трансмісії машина може виконувати рух як вперед, так і назад.
Всі сучасні автомобілі мають таку трансмісію, яка дозволяє тимчасово відключити жорстку зчеплення клонували з провідними колесами. Це дає можливість машині рухатися на холостому ходу, наприклад, плавно наближаючись до світлофора. Даний механізм також дозволяє не глушити двигун, коли авто зупиняється. Це необхідно для підзарядки акумулятора і роботи додаткового обладнання, наприклад, кондиціонера.
Кожна КП повинна відповідати таким вимогам:
- Забезпечувати тягу автомобіля і економічна витрата палива в залежності від потужності і обєму мотора;
- Простота у використанні (водій не повинен відволікатися від дороги при зміні швидкості ТЗ);
- Не видавати шум під час роботи;
- Високу надійність і ККД;
- Мінімальні габарити (наскільки це можливо у випадку з потужними транспортними засобами).
ПРИСТРІЙ КОРОБКИ ПЕРЕДАЧ
У пристрій будь-коробки передач входить:
- Корпус. У ньому знаходяться всі необхідні деталі, що забезпечують зчеплення мотора з приводним валом, від якого обертання надходить на колеса.
- Резервуар з маслом. Так як в даному механізмі деталі стикаються один з одним під великим навантаженням, мастило забезпечує їх охолодження і створює масляну плівку, яка захищає від передчасної вироблення на шестернях.
- Механізм передачі швидкості. Залежно від типу коробки до складу механізму можуть входити вали, набір шестерень, планетарний редуктор, гідротрансформатор, фрикційні диски, ремені і шківи.
КЛАСИФІКАЦІЯ КП
ЗА СПОСОБОМ ПЕРЕДАЧІ ПОТОКУ ПОТУЖНОСТІ
У цю категорію ввійшли такі КП:
- Механічна КП. У такій модифікації відбір потужностей проводиться зубчастої передачею.
- КП з співісними валами. Обертання передається теж через зубчасту передачу, тільки її елементи виконані в конічної або циліндричної форми.
- Планетарна. Передача обертання виробляється через планетарний ряд, шестерні якого розташовані в одній площині.
- Гідромеханічна. У такій трансмісії механічна передача (в основному планетарний тип) використовується спільно з гидротрансформатором або гідромуфтою.
- Варіаторная. Це різновид КП, в яких не використовується ступіньчаста передача. Найчастіше такий механізм працює разом з гідромуфтою і ремінним з'єднанням.
ЗА КІЛЬКІСТЮ ОСНОВНИХ ВАЛІВ З ШЕСТЕРНЯМИ
При класифікації КП за кількістю валів розрізняють:
- З двома валами і одноступіньчастим зачепленням осі. У таких трансмісіях немає прямої передачі. Найчастіше такі модифікації можна зустріти в машинах з переднім приводом. У деяких моделях із заднім розташуванням моторів також встановлена подібна коробка.
- З трьома валами і двоступіньчастим зачепленням осі. У цій категорії є модифікації з співісними і Неспіввісність валами. У першому випадку мається пряма передача. У поперечному розрізі вона має менші габарити, а в довжину трохи більші. Такі коробки використовуються в задньопривідних авто. Друга категорія не має прямої передачі. В основному така модифікація використовується в машинах з повним приводом і в тракторах.
- З кількома валами. У цій категорії КП вали можуть мати послідовне або непослідовне число зачеплень. Такі коробки передач використовуються в основному в тракторах і верстатах. Це дозволяє збільшити кількість передач.
КЛАСИФІКАЦІЯ ПЛАНЕТАРНИХ КП
Планетарні коробки передач діляться за такими параметрами:
- Дві, три, чотири і більше ступеня свободи, коли всі фрикційні елементи від'єднані;
- Тип планетарного ряду, який використовується в механізмі - епіциклічних (основний вінець має внутрішнє або зовнішнє розташування зубів).
ЗА СПОСОБОМ УПРАВЛІННЯ
У даній категорії є такі коробки:
- Ручна. У таких моделях вибір потрібної передачі здійснює водій. Існує два види ручних трансмісій: перемикання проводиться зусиллями водія або через сервопривід. В обох випадках управління здійснює людина, тільки друга категорія КП має сервопристрій Воно отримує сигнал від водія, після чого встановлює обрану передачу. В машинах найчастіше використовується гідравлічний сервопривід.
- Автоматична. Електронний блок управління визначає кілька чинників (ступінь натискання акселератора, навантаження, що надходить від коліс, обороти колінвала і ін.) І на підставі цього сам визначає, коли включити підвищену або знижену передачу.
- Робот. Це електромеханічна коробка. У ній передачі включаються в автоматичному режимі, тільки її пристрій - як у звичайній механіки. При роботі роботизованої трансмісії водій не бере участі в перемиканні передач. Блок управління сам визначає, коли яку передачу включити. При цьому перемикання відбувається практично непомітно.
ЗА КІЛЬКІСТЮ ПЕРЕДАЧ
Дана класифікація найпростіша. У ній все коробки поділяються за кількістю передач, наприклад, чотири, п'ять шість і так далі. У цю категорію входять не тільки ручні, а й автоматичні моделі.
ТИПИ КОРОБОК ПЕРЕДАЧ
Найпоширеніша класифікація - за типом самої коробки:
- Механіка. У таких моделях вибір і перемикання передач виконується повністю зусиллями водія. В основному це редуктор з декількома валами, робота якого здійснюється через шестерну передачу.
- Автомат. Така трансмісія працює в автоматичному режимі. Вибір необхідної передачі здійснюється на підставі параметрів, які заміряє система управління коробкою.
- Робот є різновидом механічної КП. Конструкція цієї модифікації практично нічим не відрізняється від звичайної механіки: в ній є зчеплення, а передачі включаються через під'єднання відповідної шестерні на відомому валу. Тільки управління вибором передач керує комп'ютер, а не водій. Гідність такої трансмісії - максимально плавне перемикання.
НЕСИНХРОНІЗОВАНИХ КП
До ще одного різновиду специфічних коробок відноситься несинхронізованих або та, в конструкції якої не передбачено наявність синхронізаторів. Це може бути тип з постійним зачепленням шестерень або зі легкими шестернями.
Щоб переключити передачу в такій коробці, водій повинен мати певний навичкою. Він повинен вміти самостійно синхронізувати обертання шестерень і муфт, визначаючи час переходу від передачі до передачі, а також вирівнюючи швидкість обертання коленвала акселератором. Професіонали називають цю процедуру перегазовкой або подвійним вижимом зчеплення.
Для виконання плавного перемикання водій повинен мати досвід в управлінні такими механізмами. Подібний тип трансмісії встановлюється в американських тягачах, мотоциклах, іноді в тракторах і спортивних автомобілях. В сучасних несинхронізованих трансмісіях можна не використовувати зчеплення.
КУЛАЧКОВА КП
Кулачкові коробки це різновид несинхронізованою моделі. Відмінністю є форма зачіпляються зубів. Для підвищення ККД коробки передач використовується прямокутна форма або кулачковий профіль зубів.
Такі коробки дуже галасливі, тому в легковому транспорті використовуються в основному на гоночних авто. Під час змагань на цей фактор не звертається увага, але в звичайному автомобілі така трансмісія не дасть можливості отримати насолоду від поїздки.
ПОСЛІДОВНА КП
Під секвентальною коробкою мається на увазі тип трансмісії, в якому перехід на знижену або підвищену передачу здійснюється виключно на один щабель. Для цього використовується ручка або ножний перемикач (на мотоциклах), який дозволяє перемістити шестерню в кошику виключно на одну позицію за одне натискання.
Схожий принцип роботи має автоматична коробка типу Привід, але вона лише імітує дію даної трансмісії. Класична секвентальная коробка встановлюється в болідах F-1. Перемикання швидкості в них здійснюється за допомогою підрульових пелюсток.
ПРЕСЕЛЕКТИВНА CP
У класичному виконанні преселективна КП вимагала попереднього вибору наступної передачі до того, як коробка на неї переключиться. Часто це виглядало так. Під час руху авто водій виставляв на селекторі наступну передачу. Механізм готувався до перемикання, але виконував це по команді, наприклад, після натискання на зчеплення.
Раніше такі КП використовувалися у військовій техніці з несинхронізованою, безвальной або планетарної трансмісією. Такі модифікації коробок полегшували управління складними механізмами, поки не були розроблені синхронізовані механічні та автоматичні коробки.
В даний час преселективна коробка використовується, але вона частіше називається трансмісією з подвійним зчепленням. У цьому випадку комп'ютер сам готує перехід на потрібну швидкість, заздалегідь під'єднуючи до незафіксованим диску відповідний вал з включеною передачею. Інша назва цього типу в сучасному виконанні - робот.
ВИБІР КОРОБКИ ПЕРЕДАЧ. ЩО КРАЩЕ?
Багато хто з перерахованих коробок передач використовуються тільки на спецтехніці або в верстатах. Основними КП, які мають широке застосування в легковому транспорті, є:
- Механічна коробка передач. Це найпростіший тип трансмісії. Щоб обертальний рух передавалося з силового агрегату на вал КП, використовується кошик зчеплення. Натисканням педалі водій від'єднує провідний вал коробки від мотора, що дозволяє йому без шкоди для механізму вибрати відповідну для даної швидкості передачу.
- Автоматична коробка передач. Крутний момент від мотора подається через гідропередачу (гідротрансформатор або гидромуфта). Робоча рідина грає роль зчеплення в механізмі. Вона приводить в рух, як правило, планетарний редуктор. Вся система управляється електронним блоком управління, який аналізує дані з багатьох датчиків і відповідно до цього вибирає передавальне число. Серед автоматичних коробок є багато модифікацій, в яких використовуються різні схеми роботи (залежить від виробника). Існують навіть автоматичні моделі з можливістю ручного управління.
- Роботизована коробка передач. Серед таких КП також є свої різновиди. Існують електричні, гідравлічні і комбіновані типи. За конструкцією робот в основному схожий на механічну коробку, тільки з подвійним зчепленням. Перше подає крутний момент від мотора до провідних колесам, а друге автоматично готує механізм до включення наступної передачі.
- Варіаторная коробка передач. У поширеному виконанні варіатор представляє собою два шківа, які з'єднані між собою ременем (одним або декількома). Принцип дії наступний. Шків розсується або зсувається, в результаті чого ремінь переміщається на елемент з більшим чи меншим діаметром. Від цього і змінюється передавальне число.
- Тема: Складові гальмівної системи
Будь-яка гальмівна система складається з привода і гальмівного механізму.
Привод може бути механічним, гідравлічним, пневматичним, електричним і комбінованим. Електричний привод на сьогодні в чистому вигляді не застосовується.
Гальмівні механізми також бувають барабанні, дискові та стрічкові. Останні, до слова сказати, можна зустріти хіба що на гусеничній техніці.
7.2.2 Привод гальмівних механізмів
На вантажних автомобілях середньої та великої вантажопідйомності використовується пневматичний привод (на догоду довжині всіх приводів), але ми зупинимося на розгляді гідравлічного привода гальм - найпопулярнішого для легкових автомобілів.
Примітка
Привод - це набір механізмів і деталей, покликаних передавати зусилля, тягу або переміщення.Ця система базується на властивості рідин не стискатися.
Складається гідропривод гальм з таких елементів
- педалі гальма;
- головного гальмівного циліндра;
- вакуумного підсилювача;
- патрубків гідропривода і гальмівних шлангів;
- передніх і задніх робочих гальмівних циліндрів, які розташовані в гальмівних механізмах.
7.2.3 Принцип роботи гальмівних механізмів
Принцип роботи полягає в наступному: педаль гальма через шток зв'язується з поршнем, який переміщується в головному гальмівному циліндрі заповненому гальмівною рідиною, як, утім, і всі патрубки та шланги гальмівної системи.
При натисканні на педаль гальма поршень у циліндрі переміщується, тисне на рідину, яка передає зусилля на робочі гальмівні циліндри гальмівних механізмів. Все просто. Якщо не зрозуміло, не варто відразу бентежитися, оскільки далі в розділі буде описано роботу кожного елемента гальмівної системи.
Окрім того, що за допомогою головного гальмівного циліндра зусилля передається від педалі до гальмівних механізмів, також головний циліндр забезпечує розділення контурів (див. далі).
Над головним гальмівним циліндром встановлено розширювальний бачок, необхідний для компенсації розширення гальмівної рідини при її нагріві та для запобігання потраплянню повітря в систему гідропривода гальм (для цього необхідно завжди стежити за рівнем гальмівної рідини в бачку і не допускати його падіння нижче позначки «MIN»).
Розширювальний бачок розділений на два резервуари (або має один резервуар, але з розділовою перегородкою), які сполучаються з головним гальмівним циліндром системи через два отвори. На поршнях є кільцеві ущільнювальні манжети, які притискаються пружинами.
Примітка
Крім проточки, поршні мають кільцеві порожнини і пласкі кутоподібні пази, які з'єднуються з резервуаром при будь-якому положенні поршнів. Це перешкоджає потраплянню повітря в гідравлічну магістраль.Увага
Одним із найнебезпечніших, з точки зору потрапляння повітря в головний гальмівний циліндр, є момент режиму розгальмовування, який часто виконується різко, кидком педалі. У такому разі рідина внаслідок її певної в'язкості повертається в головний гальмівний циліндр відносно повільно і поршні під дією пружин прагнуть начебто відірватися від рідини, внаслідок чого в магістралі створюється розрідження. При цьому запобігти потраплянню повітря в магістраль одними тільки ущільненнями майже неможливо, тому з тильного боку поршнів або в них самих розташовують порожнини, заповнені рідиною.Технології розвиваються, і, щоб не обтяжувати водія постійними перевірками рівня гальмівної рідини, в розширювальному бачку встановлюють поплавець і приєднують до нього датчик рівня гальмівної рідини. Щойно цей рівень впаде нижче заданого, на приладовому щитку в салоні автомобіля загориться відповідний сигналізатор, а може ще й спрацює звукова сигналізація.
Примітка
Запобігти потраплянню повітря в гідропривод гальмівної системи практично неможливо. Так, при заміні будь-яких елементів гальмівної системи доведеться зливати частину гальмівної рідини. А залити свіжу гальмівну рідину без потрапляння повітря неможливо.
Також при перегріванні гальмівних механізмів ця рідина може почати кипіти, утворюючи бульбашки повітря.Для видалення повітря з гідропривода гальм у найвищих точках кожного елемента гальмівної системи передбачено так звані сапуни. Сапун - це порожнистий болт, який виступає в ролі клапана, але з «ручним приводом». При відкручуванні сапуна «клапан» відчиняється, при закручуванні - зачиняється.
Примітка
Як виконуються операції з видалення повітря («прокачування», простіше) з гідропривода гальмівної системи, можна знайти в будь-якій книжці щодо ремонту та обслуговування автомобілів.Кінцевим елементом гідропривода є робочий циліндр. Якщо гальмівні механізми барабанні, то робочий циліндр є окремою деталлю, якщо гальма дискові, то він інтегрований у гальмівний супорт гальмівних механізмів
7.2.4 Регулятор тиску
У систему гідропривода гальм встановлюють регулятор тиску гальмівної рідини. Для чого він потрібен?
Задні колеса мають починати гальмування на мить раніше передніх. Це зроблено для того, щоб запобігти занесенню автомобіля, якщо його колеса потраплять на слизьку поверхню. Але процес руху досить складний, і автомобіль може бути завантажений поклажею чи пасажирами, внаслідок чого навантаження на задню вісь підвищиться. А якщо задня вісь стане важчою, для її гальмування доведеться докласти більше зусилля. От саме для того, щоб водій не був обтяжений думками про розподіл гальмівних зусиль між передньою і задньою віссю, в гідропривод гальм «врізали» регулятор.
Регулятор тиску коригує тиск гальмівної рідини в системі задніх гальмівних механізмів залежно від зміни навантаження на задні колеса.
7.2.5 Гальмівні рідини, що застосовуються
До гальмівної рідини пред'являють жорсткі вимоги, оскільки вона працює в украй агресивних умовах: під впливом високих і низьких температур. Тому основним показником, що характеризує гальмівну рідину, є температура її кипіння: що вона вища, то краще. Взагалі, кипіння для гальмівної рідини - це шлях до зниження ефективності гальмування практично до нуля: рідина закипіла, з'явилися пухирці повітря, педаль провалилася, а гальмування так і не почалося. Також не варто забувати про те, що низькі температури можуть призвести до замерзання гальмівної рідини, результатом чого також буде втрата ефективності гальмування.
Увага
Гальмівна рідина украй гігроскопічна. Це означає, що вона має властивість поглинати вологу, що міститься в повітрі. Попадання вологи в гальмівну рідину призведе до зниження температури її кипіння і появи кристалів льоду при замерзанні, внаслідок чого миттєво знизиться ефективність гальмівної системи в цілому.Разом з автомобілем поставляється й інструкція з експлуатації. Якщо в автомобілі її немає, відповідний посібник можна придбати окремо. У такій інструкції обов'язково буде вказано тип гальмівної рідини за класифікацією Департаменту транспорту США - DOT.
На сьогодні найпоширеніші гальмівні рідини мають позначення DOT3, DOT4, DOT4+ і DOT5.1. Причому доливати в розширювальний бачок головного гальмівного циліндра рідину вищого класу допускається (наприклад, DOT4 долити в бачок із рідиною DOT3), звичайно, за умови, що обидві рідини випущені одним і тим же виробником. І навпаки, доливати в бачок з DOT4 рідину класу DOT3 не слід.
7.2.6 Барабанні гальмівні механізми
Свого часу це був дуже поширений тип гальмівних механізмів. Улаштування найпростіше (малюнок 7.3): гальмівний щиток, що не обертається і жорстко закріплений на поворотному кулаку* (якщо це керовані передні колеса) або на цапфі (якщо це задня вісь), на гальмівний щиток встановлено робочий гальмівний циліндр, також гальмівні колодки, які одним кінцем спираються на опори, а іншим - упираються в поршні робочого гальмівного циліндра. На гальмівні колодки наклеєні або приклепані фрикційні накладки, зверху усі ці деталі накриваються гальмівним барабаном, який обертається разом із колесом.
Якщо раптом знадобилося знизити швидкість або зупинитися, водій, натискаючи на педаль гальма, через гідропривод впливає на поршні робочого гальмівного циліндра, які, переміщуючись, розсовують гальмівні колодки, притискаючи їх до поверхні гальмівного барабана.
Існує кілька схем розташування гальмівних колодок.
Цікаво
У барабанному гальмівному механізмі,одна з найпоширеніших схем розташування колодок), дві колодки встановлені послідовно одна за одною. Одна колодка - передня, інша - задня (по ходу руху). Причому обидві колодки знизу встановлені на осях, а зверху впираються в поршні робочого циліндра. При гальмуванні сили діятимуть так, що передня колодка буде нібито підклинювати, а задню колодку створювані зусилля намагатимуться відсунути від барабана. Цим може бути викликаний нерівномірний знос фрикційних накладок. Так само цей ефект призводить до того, що робочі поверхні фрикційних накладок використовуються не повною мірою.Для того щоб після гальмування гальмівні колодки повернулися у вихідне положення, встановлено відвідні пружини.
Зазор між колодками і барабаном часто регулюється автоматично. Реалізовано це просто: поршні робочих циліндрів, переміщуючись назовні під дією тиску рідини, виберуть наявний між ними і пружними кільцями осьовий зазор, після чого потягнуть кільця за собою. Рух поршнів триватиме доти, доки колодки не упруться в барабан. При відпусканні педалі відвідні пружини зможуть перемістити поршні назад тільки на величину, відповідну осьовому зазору між поршнем і кільцем, оскільки зрушити кільце вони не в змозі.
Величина зазора, як було сказано вище, відповідає необхідному зазору між колодкою і барабаном. Таким чином, у міру зношування накладок кільце переміщатиметься уздовж циліндра, підтримуючи постійну величину зазора в механізмі.
Барабанні гальмівні механізми мають низку переваг, порівняно з дисковими гальмами, однак і вад чимало.
Переваги:
- велика робоча поверхня гальмівних колодок і можливість її збільшення як за рахунок діаметра гальмівного барабана, так і його ширини (корисна властивість для вантажних автомобілів);
- відносна захищеність гальмівного механізму від пилу і бруду;
- стійкість елементів гальмівного механізму до перепаду температур.
Вади:
- мала, порівняно з дисковими гальмами, потужність, що розвивається;
- велика інерційність елементів гальмівного механізму;
- чутливість до перегріву.
7.2.7 Дискові гальмівні механізми
Єдиною перспективною альтернативою барабанних механізмів для легкових автомобілів стали дискові гальмівні механізми. У таких механізмах гальмівний диск кріпиться до маточини колеса і обертається разом із колесом. Щоб зупинити автомобіль, необхідно підвести під тиском гальмівну рідину до поршня в гальмівному супорті. Поршень, впливаючи на гальмівні колодки, передасть на них зусилля від гальмівної рідини, притисне до диска і почне уповільнювати колесо. Чимось принцип дії дискового гальма схожий на велосипедне гальмо, де роль диска відіграє поверхня обода колеса, а зупинка здійснюється притисканням колодок гальма до обода
Примітка
Існує два типи гальмівних супортів: фіксований і плаваючий. У першому випадку в гальмівному супорті є два поршні, розташовані по обидва боки від гальмівного диска. Сам супорт жорстко закріплений на поворотному кулаку. Поршні впливають на внутрішню і зовнішню гальмівні колодки. До кожного з них підводиться гальмівна рідина.
У другому випадку гальмівний супорт має поршень або поршні тільки з одного боку, при цьому він має змогу переміщатися уздовж осі обертання диска. Так, при гальмуванні поршень переміщується і тисне на внутрішню колодку, після того як колодка упреться в диск, а тиск в гідроприводі продовжить зростати, вже супорт почне переміщатися і притискати зовнішню колодку до диска.
Перший варіант міцніший, але дорожчий. Другий варіант дешевший, але не такий надійний.Ефективність дискових гальм набагато вища за ефективність барабанних. Вони простіші в обслуговуванні та ліпше відводять тепло, що виділяється при гальмуванні.
Оскільки перегрів гальмівних механізмів вважається одним із найнебезпечніших моментів, вирішили збільшити ефективність відведення тепла від гальмівного механізму. Шлях вирішення проблеми простий з точки зору ідеї та не такий простий з точки зору технологічності. У диску зробили багато отворів і каналів, через які повітря може проходити з метою охолодження диска зсередини Ефективність підвищили багаторазово. Але у всього є своя ціна, і в цьому випадку за покращене охолодження довелося заплатити низькою стійкістю до перепаду температур. Виникла ймовірність появи тріщин на диску при потраплянні на нього, наприклад, води при дуже активному гальмуванні. Причина в тому, що отвори - це концентратори напружень. Виходить, що працює принцип «Де тонко, там і рветься».
Часто на гальмівних дисках можна побачити канавки . Причина, по якій диск виготовляють з такими конструктивними особливостями, криється в тому, що при виконанні гальмування на фрикційних накладках гальмівних колодок утворюється шар відпрацьованого матеріалу (пилу), який погіршує ефективність гальмування. Шар відпрацьованого пилу зрізається канавками, оновлюючи тим самим робочу поверхню фрикційної накладки.
Проте час іде, деякі автомобілі стають більш потужними і важкими, мають високі динамічні показники і украй високу енергоозброєність*, і, щоб зупинити всю цю масу, що рухається на величезній швидкості, потрібне застосування надефективних гальмівних механізмів. Основний показник, що впливає на ефективність роботи гальм, як було сказано вище, - температура.
Існує два шляхи вирішення проблеми перегріву гальм. Перший із них - виготовити гальмівні механізми зі своєю системою охолодження, однак це занадто ускладнює конструкцію і подальше обслуговування. Другий - встановити композитні гальмівні диски, наприклад металокерамічні. Таким дискам взагалі не страшний перегрів. Але плата за металокераміку - крихкість і висока собівартість.
Примітка
* Енергоозброєність - це питомий показник, що характеризує, скільки кіловат або кінських сил потужності припадає на одиницю маси автомобіля (на кілограм або тонну). Наприклад, якщо автомобіль важить 2 т, а потужність його двигуна становить 300 к. с., то енергоозброєність цього авто становить 150 к. с./т. Але автомобіль масою 1 т і потужністю 150 к. с. матиме таку ж енергоозброєність, а значить не поступатиметься в динамічних характеристиках більш потужному, але й більш важкому «супернику».Примітка
Дискові гальмівні механізми часто обладнують датчиком зносу фрикційних накладок. У найпростішому вигляді він має вигляд підпружиненої пластини, яка при досягненні граничної товщини фрикційної накладки досягає диска і починає скрипіти.
У більш ускладненому варіанті встановлено датчик у прямому сенсі цього слова. Його показники виводяться на відповідний покажчик на щитку приладів.7.2.8 Вакуумний підсилювач гальм
Що більшою ставала маса автомобіля, то більше зусилля потрібно було прикладати до педалі гальма, щоб досить ефективно знизити швидкість або зупинити автомобіль. Було б великою помилкою не використовувати ті фізичні процеси, які відбуваються під час роботи двигуна. Помилку не зробили - встановили вакуумний підсилювач. Чому вакуумний? Він використовує розрідження, створюване у впускному колекторі двигуна. Будова такого підсилювача нескладна (малюнок 7.7): корпус, розділений діафрагмою на дві камери - вакуумну й атмосферну. На штоку педалі гальма, всередині підсилювача, встановлено стежачий клапан*, що відкриває або перекриває доступ атмосферного тиску в атмосферну камеру. Крім того, встановлено поворотну пружину діафрагми підсилювача. Після підсилювача послідовно встановлено головний гальмівний циліндр.
Примітка
З огляду на різні конструктивні особливості двигунів, розрідження може підводитися не тільки від впускного колектора, а й від спеціального вакуумного насоса.
Наприклад, для всіх дизельних двигунів використовується вакуумний насос, оскільки у них розрідження у впускному колекторі незначне.Як це працює? Досить просто: в початковому положенні (коли гальмувати ніхто не збирається) тиск в обох камерах однаковий і дорівнює тиску, створюваному у впускному колекторі. Тільки-но виникне необхідність загальмувати, необхідно буде натиснути на педаль гальма - переміщення педалі передасться через штовхач до стежачого клапана. Клапан перекриє канал, який з'єднує атмосферну камеру з вакуумною. Подальше переміщення з'єднає атмосферну камеру з атмосферою. Виникне перепад тиску, який почне впливати на діафрагму і переміщати її, долаючи зусилля поворотної пружини, а діафрагма і собі переміщатиме шток поршня головного гальмівного циліндра.
Примітка
Така конструкція вакуумного підсилювача забезпечує значне доповнення зусилля (воно може досягати п'ятикратного збільшення) на штоку поршня головного гальмівного циліндра, яке пропорційне зусиллю на педалі гальма. Якщо простіше: що дужче ви тиснутимете на педаль, то потужніше й ефективніше працюватиме вакуумний підсилювач.Тільки-но водій відпустить педаль гальма, атмосферний клапан перекриється, тиск в обох камерах підсилювача вирівняється, а діафрагма повернеться в початкове положення під дією поворотної пружини.
7.2.9 Перевірки вакуумного підсилювача
Важливо знати, що, сідаючи за робоче місце водія, слід завжди перевіряти технічний стан вакуумного підсилювача. Як це зробити? Елементарно...
Для перевірки роботи вакуумного підсилювача гальм необхідно виконати такі процедури:
1. Запустити двигун на 1-2 хвилини, а потім заглушити його. Якщо при першому натисканні на педаль гальма вона натиснута повністю, але при наступних натисканнях хід педалі стає більшим із кожним натисканням, значить, підсилювач працює правильно. Якщо висота ходу педалі залишається незмінною, значить підсилювач працює неправильно.
2. При непрацюючому двигуні натиснути на педаль гальма кілька разів. Потім натиснути на педаль гальма і запустити двигун. Якщо вона рухається вниз незначно, це є нормальною роботою підсилювача. Якщо рух педалі не змінюється, підсилювач несправний.
3. При працюючому двигуні, натиснути на педаль гальма і потім зупинити двигун. Утримувати педаль натиснутою близько 30 секунд. Якщо висота педалі не змінюється, підсилювач працює нормально, якщо педаль піднімається - підсилювач несправний.
Виконати три тести, описані вище. Якщо хоча б один із них не відповідає нормальній роботі, треба перевірити зворотний клапан, вакуумний шланг і підсилювач щодо пошкоджень.
7.2.10 Стоянкове гальмо
Стоянкове гальмо (у побуті - «ручник») призначене для утримання автомобіля під час стоянки як на рівній, так і на похилій поверхні. На легкових автомобілях стоянкова гальмівна система може виконувати роль запасної гальмівної системи.
Стоянкові гальмівні системи відрізняються за типом привода, а також за типом гальмівного механізму.
За типом привода стоянкові гальмівні системи можуть бути:
- з механічним приводом;
- з гідравлічним приводом;
- з електромеханічним приводом.
7.2.11 Стоянкова гальмівна система з механічним приводом
Проста і дешева схема впливу на гальмівні механізми задніх коліс передбачає використання тросів і важеля (або педалі), який знаходиться в салоні. Принцип дії такий: при переміщенні важеля стоянкового гальма переміщуються троси привода, які впливають на гальмівні механізми, запобігаючи у такий спосіб провертанню коліс (елементи гальмівної системи зображені на малюнку 7.1). Важіль у салоні встановлено на храповик, що дозволяє фіксувати його в робочому положенні.
Для інформування водія про те, що стоянкове гальмо в цей момент задіяне, під важелем встановлено вимикач сигналізатора на щитку приладів.
Примітка
Від важеля в салоні зусилля до гальмівних механізмів передається за допомогою тросів. У конструкції гальмівного привода стоянкового гальма використовуються один, два або три троси. Найпоширеніша схема з трьома тросами: один передній (центральний) і два задні. Передній трос з'єднаний із важелем у салоні, задні троси - з гальмівними механізмами відповідно до правого і лівого коліс. Для з'єднання переднього троса із задніми і рівномірної передачі зусилля використовується зрівнювач або балансир.Як і будь-який механізм, стоянкове гальмо необхідно регулювати, для цього передбачено регулювання довжини тросів за допомогою регулювальної гайки, встановленої часто на зрівнювачі. Повернення системи в початкове положення (зняття з гальма) проводиться при переведенні ручного важеля у відповідне положення за допомогою поворотної пружини. Пружина може розташовуватися на передньому тросі, зрівнювачі або безпосередньо на гальмівному механізмі.
Гальмівні механізми стоянкової системи можуть бути різних типів. Так, якщо ззаду застосовуються барабанні гальма, то гальмівна система використовує гальмівні механізми робочої гальмівної системи, лише в цьому випадку колодки притискаються не через робочий гальмівний циліндр, а через вплив троса системи на приводний важіль колодок. Якщо гальма дискові, то варіантів два: або передавати зусилля через приводний важіль на гальмівний супорт робочої гальмівної системи і фіксувати у такий спосіб колесо, або виготовляти диск заднього гальмівного механізму складовим (мається на увазі, що гальмівний диск буде виготовлено так, що внутрішня його поверхня виконуватиме роль гальмівного барабана).
Цікаво
Бажано завжди використовувати стоянкове гальмо, щоб запобігти закисанню тросів. Оскільки, якщо раптом трапиться екстрена та непередбачена ситуація в дорозі, скористатися гальмівною системою, як запасною, при приводних тросах, що закисли, буде неможливо.7.2.12 Стоянкова гальмівна система з гідравлічним приводом
Така стоянкова система часто використовується на спортивних автомобілях, коли стоянкове гальмо застосовується короткочасно і потрібне воно для того, щоб домогтися від автомобіля необхідної траєкторії при проходженні повороту.
По суті, використовується такий самий важіль у салоні, ті самі задні гальмівні механізми, що і в механічному приводі, але замість тросів - шланги і патрубки, заповнені гальмівною рідиною. До важеля в салоні приєднано один або два головні гальмівні циліндри. Принцип роботи той самий, що і в звичайній робочій гальмівній системі, він був розглянутий вище.
7.2.13 Стоянкова гальмівна система з електромеханічним приводом
У часи автоматизації та комп'ютеризації тяжкий тягар вмикання стоянкового гальма переклали на електромеханічний сервопривод. У салоні від важеля залишилася лише клавіша або кнопка. Троси замінили на електропроводку, а виконавчі механізми помістили на елементи робочої гальмівної системи.
З такою системою водієві не потрібно рахувати кількість клацань храповика при затягуванні «ручника», не потрібно перейматися регулюванням тросів стоянкового гальма - варто лише натиснути на кнопку або потягнути клавішу, і електроніка виконає свою справу.
На додачу до цього спрощення з'явилася система допомоги при рушанні з місця під гору, яка використовує стоянкове гальмо, і, зрештою, водій позбувся ще одного головного болю - відкочення автомобіля на початку руху.
Тема: Кузов та додаткове обладнання
У кабіні розміщені сидіння для водія і пасажирів та всі органи керування. Кабіна обладнана протисонячними козирками, склоочисниками, пристроями для обмивання вітрового скла, опалювачем. Двері кабіни мають замки, поворотні кватирки і стекла, що опускаються.
Кабіни автомобілів ГАЗ-53А, ЗИЛ-130, КрАЗ, «Урал» кріплять до рами на гумових подушках за двигуном. У автомобілях ГАЗ-66, КамАЗ, МАЗ-500А та інших кабіна розміщена над двигуном. При такому розміщенні кабіни зменшується колісна база, що підвищує маневреність, поліпшує оглядовість для водія. В таких автомобілях кабіна відкидна, що робить вільним доступ до двигуна.Кузов і оперення вантажних автомобілів.
Кузови вантажних автомобілів бувають універсальними і спеціалізованими. їх установлюють на рамі за кабіною.
Універсальний кузов призначений для перевезення різних вантажів. Він має дерев\'яну з металевим окуттям вантажну платформу, передній, задній і бокові борти. Задній та обидва бокові борти відкидаються на петлях, а в піднятому положенні утримуються запорними гаками.
Спеціалізовані кузови використовують для перевезення будь-якого одного вантажу (кузови -самоскиди, кузови-цистерни та інші)
До оперення належать капот, крила, підніжки, облицювання радіатора.
Кузови легкових автомобілів можуть бути несучими, тобто такії, що сприймає силові навантаження, і рамної конструкцій. Автомобілі дуже малого (4 особи) і малого (4-5 осіб) класу обладнані кузовами несучої конструкції. Автомобілі середнього (5-6 осіб) і вищого (5-7 осіб) мають рамний кузов. Кузов легкового автомобіля чотиридверний, несучої конструкції. Він складається з основи, передньої частини, задньої стінки, боковини і криші. До передньої частини кузова прикріплена коротка рама, до якої знизу кріпиться поперечина передньої підвіски.
До корпусу кузова на петлях навішено четверо дверей. У задній частині кузова розміщено багажник з кришкою, що закривається.
У кузові встановлено передні і задні сидіння із спинками. Для вентиляції кузова передбачено люк для приливу повітря, який установлено перед вітровим склом. У кузові є пристрій для обігрівання. Оперення кузова складають передні і задні крила, капот, бризговики, передній і задній буфери та облицювання радіатора.Додаткове обладнання кузова (кабіни).
Система опалення призначена для обігрівання кузова легкового чи кабіни вантажного автомобілів.
Система опалення, яка встановлена у кабіні вантажних автомобілів і в кузові легкового автомобіля , використовує тепло системи охолодження двигуна.
На автомобілі ГАЗ-53А опалювач кабіни встановлюють під щитком приладів. Він складається з радіатора, зовнішнього люка припливу повітря, рукоятки керування кришкою люка, кришки зовнішнього люка, повітропроводу подачі теплого повітря для обдування вітрового скла і з\'єднувальних шлангів.
Радіатор опалення з\'єднується шлангами із сорочкою охолодження головки блока циліндрів і водяним насосом двигуна.
Під час руху автомобіля, коли відкрита кришка зовнішнього люка припливу повітря, зустрічний потік повітря надходить у люк і через решітку і кожух до радіатора . Проходячи через радіатор, повітря нагрівається і через розподільник надходить до кабіни.
Система вентиляції призначена для обміну повітря в кабіні або кузові (легкового) автомобіля. Конструктивно система опалення об\'єднана із системою вентиляції.
Пристрої для обдування, очищення і обмивання вітрового скла кабіни (кузова). Щоб запобігти обмерзанню чи запотіванню вітрового скла, передбачено його обдування за допомогою вентилятора системи опалення автомобіля. Повітря через вентилятор подається до радіатора 7 опалення, там нагрівається і надходить по повітропроводах до двох щілин, які містяться на панелі кузова (кабіни) з внутрішнього боку вітрового скла. Вентилятор вмикається перемикачем .
Для очищення вітрового скла від води і снігу застосовують склоочисники. На автомобілі ГАЗ-53А встановлюють двошвидкісний склоочисник, що складається з двох щіток та електричного привода . Електродвигун через черв\'ячний механізм приводить у дію щітки склоочисника. За допомогою перемикача вмикають електродвигун і регулюють частоту обертання його вала. . Автомобіль ЗИЛ-130 обладнаний склоочисником з пневматичним приводом від системи гальм. Для вмикання склоочисника і регулювання швидкості руху його щіток користуються краном, головка якого встановлена на панелі щитка приладів.
Для обмивання вітрового скла на автомобілях установлюють спеціальний пристрій . Він складається з електричного насоса розміщенного в бачку омивника який знаходиться під капотом, жиклерів встановлених зовні перед вітровим склом, жиклери з\'єднують шлангами кнопки для вмикання омивача як правило кнопка включення омивача об\'єднана з перемекачем щиток склоочисника. Щоб обмити скло, натискують на кнопку омивача прицьому запускаеться електронасос, завдяки чому вода з бачка подається до жиклерів і оприскує вітрове скло. Одночасно вмикають і склоочисник.
На кабіні вантажних автомобілів зовні встановлюють два дзеркала заднього вигляду; на легкових автомобілях дзеркало встановлюють всередині кузова, а також на лівих передніх дверях кузова або передньому лівому крилі.
Буксирний пристрій.
Вантажні автомобілі часто використовують як тягачі для буксирування причепів або інших автомобілів. Для цього автомобілі обладнують буксирним пристроєм , який має вигляд стержня з гаком 7, установленим у задній частині рами автомобіля. У цьому місці рама підсилена додатковими поперечками і розкосами.
Гак буксирного пристрою запирають защіпкою 6 і стопорною защіпкою 4у яка утримує пристрій від передчасного саморозкриття. При закритому положенні гак фіксують шплінтом 5, який вводять в отвір защіпки.
Стержень гака встановлено в корпус З, у якому між двома упорними шайбами 10 розміщено гумовий буфер 2, затиснутий гайкою 1, накрученою на стержень гака. Така будова пристрою оберігає раму автомобіля і з\'єднувальні елементи причепа від різких ударів і струсів, які виникають під час рушання автомобіля з місця чи при гальмуванні.Види кузова легкового автомобіля
Седан
Основними елементами є: моторний відсік, пасажирський салон, багажне відділення. При цьому пасажирський салон може мати два ряди сидінь передні і задні, але при цьому салон відповідно буває 4-х або 5-ти місцевим. Такий тип автомобілів буває 4-х дверними.
Купе
Даний тип кузова купе по зовнішньому вигляду аналогічний седану. Різниця полягає лише в тому, що кузов має дві бічних дверей.
Фургон бувають пасажирські вантажні та вантажно-пасажирські
Комбі (хетчбек) Так називають кузов, який є двохоб\'ємний конструкцією із задніми дверима. Даний кузов використовується для перевезення пасажирів і вантажів. Причому габаритні розміри автомобіля мають порівнянні з легковими авто значення.
Як правило, автомобілі, виконані в кузові комбі, мають задні сидіння, що збільшує їх вантажопідйомність і об\'єм багажного відділення. У сучасному обході даний тип кузова називають не інакше як хетчбек. Нова назва перекладається як «двері ззаду».Автомобільне скло
За своїми експлуатаційними характеристиками автомобільні скла діляться на три типи:
• триплекс
• сталініт
• пластикові
Сталініт (загартоване скло) проходять термічну обробку, яка забезпечує їх руйнування на дрібні осколки з негострими краями, знижуючи ризик поранення людей. Автомобільне скло триплекс формується з трьох окремих шарів. Два «несучих» шару, які мають скла триплекс, виготовлені із стандартного листового флоат-скла. Між цими шарами, завдяки спеціальній технології, розміщується так звана проміжна плівка.
Триплекс (багатошарове ламіноване скло) - це два листа скла, з\'єднані між собою прошарком з поливинилбутиральной плівки. Завдяки цій еластичною прошарку триплекс володіє підвищеною стійкістю до зовнішніх впливів. Вироби з багатошарового скла безпечні, оскільки при їх руйнуванні (в результаті сильного удару)
Пластикове скло - це скло, яке містить в якості одного з основних компонентів полімерні органічні речовини. Такі скла, залежно від результатів випробувань на вигин, поділяються на жорсткі і гнучкі. мічної навантаження та ін) осколки скла залишаються приклеєними до плівці.
Тема: Ходова частина
Учбові питання
1. Види підвісок
2. Кути встановлення керованих коліс
3. Важільна підвіска
4. Ресори
5. Амортизатори
6. Маркування шин
Література: В. Ф. Кисликов , В. В. Лущик " Будова й експлуатація автомобілів" стр.272 - 287
1. За характером взаємодії коліс однієї осі транспортного засобу підвіски діляться на два види ; залежна і незалежна. Залежна підвіска забеспечує жорсткий звязок між колесами тобто при зміні положення одного колеса міняється положення іншого. При незалежній підвісці жорсткий звязок між колесами відсутній .
2.Передні керовані колеса незалежно від конструкції підвіски встановлюються під певним кутом як в горизонтальній так і вертикальній площині. Це дає можливість зменшити опір рухові ТЗ і зменшити спрацювання протектора шин. Розвал коліс - кут між площиною колеса і вертикальною площиною паралельною повждовжній осі ТЗ. Сходження коліс - це різниця відстаней між внутрішніми поверхнями боковин шин яка вимірюється спереду і ззаду. Розвал і сходження коліс залежать від марки ТЗ.
3. Важільна підвіска ТЗ включає в себе такі елементи : Верхні і нижні важелі, амортизатори, пружини, шарові опори , буфери стискання, осі важелів, саленблоки, стабілізатор поперечної стійкості, поворотні цапфи.
4. Ресора - пружний елемент підвіски. Ресора складається з окремих листів ,які в центральній частині скріплені між собою болтовим зєднанням. Щоб пакет листів тримався разом на листи ресори одівають хомути. Найдовший лист ресори називають корінним листом. Листи ресори виготовляють з легованої сталі. Для усунення металевого скрипу листів ресори їх змащують графітною змазкою або ставлять між листами протискрипні шайби.
5. Амортизатори служать для гасіння коливань кузова ТЗ. За конструкцією вони бувають однотрубні і двохтрубні . Однотрубні амортизатори всередині мають один циліндр поділений на дві частини. Одна частина зоповнюється газом а інша амортизаторною рідиною. Такі амортизатори ще називають газомасляними. Двохтрубні амортизатори крім циліндра мають компенсаційну камеру. Двохтрубні амортизатори заповнюються амортизаційною рідиною кількість якої залежить від марки ТЗ, мають чотири клапани (клапан стискання, клапан віддачі , перепускний і випускний клапани). Амортизатор змінної довжини називається телескопічним.
6. У маркуванні шин вказують такі показники:
а) тип шини
б) ширина профілю шини
в) висота профілю шини
г) посадочний діаметр в дюймах
Наприклад 165/70 R 13
де 165 - ширина профілю шини в мм, 70 - висота пофілю шини в процентах від ширини , R - радіальна шина, 13 - посадочний діаметр 13х 25,4
Тема : Рульове керування автомобіля
На повороті внутрішнє колесо, що котиться по дузі меншого радіусу, має повертатися на більший кут, ніж зовнішнє. Це забезпечується пристроєм, який називається рульовою трапецією. Вона складається з балки, поворотних важелів, поперечної рульової тяги
Конструкція рульової трапеції передбачає постановку осей шворнів поворотних цапф під деякими кутами. Розрізняють поздовжній бічний нахил осей шворнів.
Нахили осей викликають реактивні зусилля і моменти, додані до керованих колесіс, які прагнуть повернути їх у положення прямолінійного руху. Ця властивість рульового управління називається стабілізацією коліс. Вона полегшує водіння автомобіля і забезпечує йому більшу стійкість при русі.
Для стабілізації коліс рекомендується черв'ячну рульову передачу 9 конструювати оборотною (несамогальмівною), але для запобігання впливу на рульовий штурвал ударів, які сприймаються колесами від нерівностей дороги, - з підвищеним внутрішнім тертям.
Керовані колеса також встановлюють під деякими кутами до вертикальної площини.
Для зменшення зусилля, що витрачається на поворот керованих коліс, і пом'якшення поштовхів від нерівностей дороги на потужних вантажних автомобілях встановлюють підсилювачі рульового управління - пневматичні (на автомобілях типу КрАЗ) і гідравлічні (МАЗ-509, ЗІЛ-130, ЗІЛ-131, ГАЗ-66 ).
Справність рульового механізму має винятково велике значення для безпеки руху, тому необхідно регулярно перевіряти люфт (вільний хід) рульового штурвала (він не повинен перевищувати 25-36 °) і кути установки коліс. Кут сходження коліс регулюється зміною довжини поперечної рульової тяги, а кут розвалу, як правило, не регулюється
Будова рульового керування
. Система включає в себе рульовий механізм і рульовий привід.
Повертаючи кермо, водій повертає передні колеса автомобіля.
З одного кінця рульового вала закріплено кермо, а протилежний кінець вала входить в рульовий механізм. На цьому кінці закріплена або шестерня (рейковий рульовий механізм), або черв'ячний вал (черв'ячний рульовий механізм).
Рульовий механізм перетворює обертання керма в площинне переміщення рульових тяг, повертаючи керовані колеса на необхідні кути. У зв'язку з тим що рульовий механізм виконано за схемою редуктора (пристрою, що знижує оберти і, як наслідок, збільшує крутний момент), він ще й збільшує зусилля водія, прикладене до рульового колеса. Зазвичай зусилля, яке прикладається водієм, збільшується в 15...30 разів. Саме таке передавальне відношення мають кермові механізми.Цілком зрозуміло, що чим більше передавальне відношення рульового редуктора, тим легше водієві повертати передні колеса. Однак збільшення передавального числа понад зазначене обмежено погіршенням керованості автомобіля: при великих значеннях передавального числа навіть для незначного повороту коліс водієві доведеться повертати кермо на великі кути.
Ряд легкових автомобілів обладнано підсилювачем рульового механізму, що додатково знижує зусилля, необхідне для повороту керма.
Рейковий рульовий механізм
У більшості сучасних легкових автомобілів використовується система рульового керування з рейковим механізмом
У цьому випадку на кінці рульового вала 1, з в'язаного з рульовим механізмом, закріплено шестерню. Вона знаходиться в зачепленні із зубчатою рейкою . Дана зубчаста пара розташована всередині картера рульового механізму. Повертаючи кермо, ми обертаємо шестерню, а вона
змушує зубчасту рейку переміщуватися усередині картера вліво або вправо. Кінці рейки через кермові тяги з'єднані з поворотними кулаками передніх коліс, і при переміщенні рейки відбувається поворот керованих коліс.
Черв'ячний кермовий механізм
У даному механізмі один з кінців кермового вала зв'язаний з черв'яком, що знаходиться в зачепленні з роликом, який, у свою чергу, зв'язаний з рульовою сошкою
Сошка, переміщуючись вліво чи вправо, через кермові тяги і поворотні кулаки забезпечує переміщення передніх коліс на необхідні кути.
На сьогодні існують два типи підсилювачів рульового керування:
- гідравлічний;
- електромеханічний.
Система з гідравлічним посиленням рульового керування має:
- насос (з розширювальним бачком);
- контрольний клапан;
- виконавчий механізм;
- власне робочу рідину.
Насос створює надлишковий тиск робочої рідини в системі. При обертанні рульового колеса контрольний клапан зміщується і відкриває канал у виконавчий механізм для робочої рідини під тиском. У виконавчому механізмі знаходиться поршень, пов'язаний через шток (тягу) з рульовою трапецією. Під тиском робочої рідини поршень переміщується, створюючи додаткове зусилля на рульовому приводі, зменшуючи тим самим зусилля водія для обертання рульового колеса.
Залежно від того, в який бік обертається кермо, робоча рідина під тиском подається в порожнину над поршнем або під ним.
Коли рульове колесо стоїть по центру, насос перекачує робочу рідину без навантаження фактично вхолосту. Тільки-но кермо починає повертатися, тиск рідини в системі зростає і досягає максимуму при крайньому (правому або лівому) положенні рульового колеса.
Увага
В автомобілі з гідравлічним підсилювачем рульового керування забороняється тривалий час утримувати кермо в одному з крайніх положень, оскільки це може призвести до пошкодження нагнітального насоса.
Насос може приводитися ременем від двигуна або ж від окремого електродвигуна.
Електромеханічний підсилювач рульового керування
Гідравлічний привод підсилювача рульового керування «вибагливий»: необхідно регулярно стежити за всіма з'єднаннями, щоб учасно виявити й усунути витік робочої рідини. Крім того, є імовірність засмічення робочої рідини. У разі необхідності зняття рульового механізму виникає потреба в зливі робочої рідини. А при заправці гідропривода свіжою робочою рідиною необхідно виконувати операції з видалення повітря із системи. Зовсім інша річ - електромеханічний підсилювач: немає робочої рідини, патрубків, прокачування та є електродвигун і блок керування, який контролює частоту обертання рульового колеса. Блок керування також відстежує швидкість автомобіля і кути повороту керма. При певних значеннях швидкості він може посилати сигнал на електродвигун з метою «затиснення» або «відпускання» керма.
Існує кілька схем установки електродвигуна підсилювача:
- на рульовій колонці;
- на валу-шестерні рульового механізму;
- на рульовому механізмі.
Численні тести автомобілів з електромеханічним підсилювачем показали, що найліпша схема встановлення електродвигуна - на рульовому механізмі, оскільки цим досягається найліпший зворотний зв'язок рульового керування.
Примітка
Під зворотним зв'язком рульового керування розуміють зв'язок із дорогою. Адже, коли ми обертаємо кермо, колеса повертаються, впливаючи таким чином на дорогу, а під час руху на колесо діє безліч сил, пов'язаних із його коченням. Так от: передача всіх цих сил від дороги на колесо та далі на кермо і є зворотним зв'язком. Виражається цей зв'язок, переважно, в пропорційно зростаючому зусиллі на рульовому колесі, яке залежить від кута повороту керма і швидкості руху автомобіля. Термін найчастіше застосовується для автомобілів із підсилювачем рульового керування.
Якщо на машині з підсилювачем керма зворотного зв'язку немає, значить зусилля на кермовому колесі не змінюється залежно від кута повороту керма і швидкості проходження автомобілем повороту. Коли автомобіль стоїть на місці або рухається повільно, то легкість обертання керма тільки на ліпше. Однак при маневруванні на швидкості відсутність на кермі зусилля, що пропорційно підвищується, може зіграти злий жарт, оскільки за об'єктивними і суб'єктивними відчуттями важко буде обрати єдино правильне положення керма.
Тема: Технічне обслуговування двигуна
Учбові питання:
- Операції ЩТО
- Операції ТО - 1
- Операції ТО - 2
- При ЩТО виконують такі операції:
А) Очистити двигун від бруду
Б)Перевірити герметичність систем і механізмів двигуна зовнішнім оглядом
В) Запустити двигун і перевірити його роботу прослуховуванням на різних режимах
2. При ТО - 1 виконують операції ЩТО і додатково:
А) Перевірити кріплення опор двигуна
Б) Змастити підшипники насоса системи охолодження
В) Перевірка дії фільтру відцентрової очистки масла
Г) Зливання відстою і бруду з паливних фільтрів
3. При ТО - 2 виконують операції ТО - 1 і додатково:
А) Перевірка кріплення вузлів і агрегатів на двигуні
Б) Заміна масла в піддоні картера
В) Промивання масляних фільтрів
Г) Перевірка компресії двигуна
Д) Перевірка натягу приводних пасів
Ж) Заміна фільтрувальних елементів паливних фільтрів
Тема: Операції ТО двигуна
Учбові питання
- Прослуховування двигуна
- Перевірка герметичності системи охолодження
- Перевірка кріплення головки циліндрів
- Перевірка натягу приводних пасів
- Перевірка компресії в циліндрах двигуна
- Прослуховування двигуна виконують за допомогою автостетоскопа. За характером стуків і шумів визначають несправність. Сильний глухий стук в нижній частині блока, який добре чути під час різкої зміни частоти обертання колінвала свідчить про спрацювання корінних підшипників . Стуки шатунних підшипників дещо меншої сили ніж корінних. Стук поршневого пальця прослуховується у верхній частині блока циліндрів. При наявності великого теплового зазору в клапанах виникають металеві стуки в клапанній коробці. Стуки , які виникають в області розміщення розподільних шестерень свідчать про спрацювання їх зубів.
- Герметичність системи охолодження перевіряють візуальним оглядом. В першу чергу звертають увагу на цілісність зєднувальних патрубків і шлангів, перевіряють надійність їх зєднання. Після цього перевіряють відсутність витікання рідини через ущільнення насосу системи охолодження. Цілісність серцевин радіатора системи охолодження і радіатора опалювача салону.
- Під час проведення ТО - 2 перевіряють кріплення головки циліндрів до блок - картера. Для проведення цієї операції необхідно мати динамометричний ключ з допомогою якого контролюють зусилля затягування різьбових зєднань. Дану операцію проводять на холодному двигуні. Порядок підтягування гайок і зусилля підтягування приводяться в довідниках. Операцію проводять у три прийоми. Якщо схема підтягування гайок кріплення відсутня, підтяжку починають з центральної гайки і навхрест до країв головки циліндрів.
- Для перевірки натягу приводних пасів необхідно мати динамометр і лінійку. Регулювальні дані беруться з довідникових таблиць. Величину прогину паса визначають посередині довгої вітки при зусиллі 4 - 5 кгс. При необхідності проводять регулювання способом передбаченим для даної марки двигуна ( натяжним роликом, зміною положення генератора, зміною положення корпусу компресора).
- Компресію в циліндрах двигуна перевіряють з допомогою компресометра, який включає себе такі елементи: манометр, рукоятка і перехідна резинова втулка. Дана операція проводиться на прогрітому до робочої температури двигуні ( бензиновий - 80 градусів, дизельний - 95 градусів). Викручуються свічки запалювання або витягуються форсунки в дизельному двигуні. В дані отвори вставляється компресометр і з допомогою стартера прокручується двигун. Компресометр вимірює тиск газів в кожному циліндрі. Одержані дані порівнюють з табличними. Допустиме відхилення компресії для бензинових двигунів - 1атм, дизельних - 2атм.
Тема: Технічне обслуговування електрообладнання
Учбові питання
1 Операції ЩТО
2 Операції ТО - 1
3 Операції ТО - 2
1.Під час проведення ЩТО виконують такі операції:
А) Очищення приладів електрообладнання від пилу і бруду
Б) Перевірка дії освітлювальних приладів
В) Перевірка дії контрольно - вимірювальних приладів і приладів сигналізації
2. Під час проведення ТО - 1 виконують операції ЩТО і додатково:
А) Перевіряють кріплення проводів до приладів електрообладнання
Б) Перевіряють надійність кріплення агрегатів електрообладнання
В) Перевіряють натяг приводного пасу генератора
3. Під час проведення ТО - 2 виконують операції ТО - 1 і додатково:
а) Очищають свічки запалювання від нагару
б) Перевіряють і при необхідності регулюють зазор між електродами свічки запалювання
в) Перевіряють стан проводів високої і низької напруг
г) зачищають контакти звукового сигналу і при необхідності регулюють його звук
д) перевіряють рівень електроліту в АКБ і ступінь її зарядженості
Тема: Технічне обслуговування трансмісії
Учбові питання
1 Операції ЩТО
2 Операції ТО - 1
3 Операції ТО - 2
- Під час проведення ЩТО виконують такі операції:
А) Перевірка герметичності картерів вузлів трансмісії
Б) Перевірка дії зчеплення
В) Перевірка справності агрегатів трансмісії
2. Під час проведення ТО - 1 виконують операції ЩТО і додатково:
А) Перевірка вільного ходу педалі зчеплення
Б) Підтягують кріплення агрегатів трансмісії
В) Перевірка рівня масла в картерах агрегатів трансмісії
3. Під час проведення ТО - 2 виконують операції ТО - 1 і додатково:
А) Мащення підшипників муфти зчеплення і проміжної опори карданної передачі
Б) При необхідності замінюють масло в картерах агрегатів трансмісії
Тема: Технічне обслуговування ходової частини
Учбові питання
1 Операції ЩТО
2 Операції ТО - 1
3 Операції ТО - 2
1. Під час проведення ЩТО проводять такі операції:
А) Перевірка стану вузлів ходової частини ( рами, підвіски , коліс)
Б) Перевірка тиску повітря в шинах
2. Під час проведення ТО - 1 проводять операції ЩТО і додатково:
А) Перевірка люфту підшипників коліс
Б) Перевірка надійності кріплення вузлів ходової частини ( рами, коліс, ресор)
В) Мащення шкворнів поворотних цапф, пальців ресор
3. Під час проведення ТО - 2 проводять операції ТО - 1 і додатково:
А) Перевірка розвалу і сходження передніх коліс
Б) Підтяжка кріплення амортизаторів
В) Перевірка справності амортизаторів
Г) Перестановка коліс за схемою
Тема: Технічне обслуговування рульового керування
Учбові питання
1 Операції ЩТО
2 Операції ТО - 1
3 Операції ТО - 2
1.Під час проведення ЩТО виконують такі операції:
А) Перевірка люфту рульового колеса
Б)Перевірка люфту в шарнірних зєднаннях рульового приводу
В) Перевірка шплінтування рульових тяг
2. Під час проведення ТО - 1 виконують операції ЩТО і додатково:
А) Перевірка рівня масла в картері рульового механізму
Б) Змастити шарнірні зєднання рульових тяг і втулок шкворнів
В) Перевірка кріплення рульової сошки
3. Під час проведення ТО - 2 виконують операції ТО - 1 і додатково:
А) Перевірка кріплення рульового колеса на валу
Б) Перевірка кріплення гайок рульових пальців
В) Перевірка кріплення рульової колонки і картера рульового механізму
Тема: Технічне обслуговування гальмівної системи
Учбові питання
1 Операції ЩТО
2 Операції ТО - 1
3 Операції ТО - 2
1. Під час проведення ЩТО виконують такі операції:
А) Перевірка герметичності системи
Б) Перевірка працездатності системи
2. Під час проведення ТО - 1 виконують операції ЩТО і додатково:
А)Перевірити вільний хід гальмівної педалі
Б)Перевірити дію стоянкового гальма
В) Спускають конденсат з повітряного балону
Г) Перевірити шплінтування пальців штоків гальмівних камер
3. Під час проведення ТО - 2 виконують операції ТО -1і додатково:
А) Перевіряють кріплення вузлів і агрегатів гальмівної системи
Б) Перевіряють рівень гальмівної рідини в бачку головного циліндра
В) Перевіряють зазор між колодками і барабаном
Тема: Операції ТО трансмісії і ходової частини
Учбові питання:
1. Перевірка і регулювання вільного ходу педалі зчеплення
2.Перевірка рівня масла в картерах вузлів трансмісії
3. Регулювання підшипників ступиць коліс
4. Перевірка і регулювання сходження керованих коліс
1. Вільний хід педалі зчеплення перевіряють за допомогою лінійки з поділками, для чого лінійку встановлюють так, щоб вона впиралася в підлогу і була притиснута до педалі. Потім рукою натискають на педаль до упору натискного підшипника. Відчувається збільшення опору рухові педалі і за поділками на лінійці визначають величину вільного ходу. Одержану величину порівнюють з табличними даними і якщо вона не відповідає технічним вимогам - регулюють. Величину вільного ходу регулюють зміною довжини тяги або зміною довжини штовхача робочого циліндра муфти зчеплення.
2. Рівень масла в картерах вузлів трансмісії перевіряють викручуючи заливні пробки. Нормальний рівень масла повинен бути на рівні заливних отворів в картерах вузлів трансмісії.
3. При регулюванні конічних підшипників ступиць передніх коліс поступають слідуючим чином:
А) Піднімають колеса домкратом до його вільного обертання
Б) Знімають ковпак ступиці
Г) Розшплінтовують регулювальну гайку
Д) Затягують регулювальну гайку так , щоб колесо оберталося туго
Ж) Відпускають регулювальну гайку на півоберту. При цьому колесо повинно вільно обертатися.
З) Фіксують регулювальну гайку
Аналогічно регулюють підшипники ступиць задніх коліс
4. Для перевірки і регулювання сходження керованих коліс потрібно мати телескопічну лінійку.
А)Транспортний засіб встановлюють на рівній поверхні , керовані колеса встановлюють в положення яке відповідає прямолінійному рухові.
Б) Встановлюють лінійку між передніми колесами на рівні осей обертання . Наконечники впираються в покришки шини.
В) Відстань між колесами вимірюють спочатку в передній частині коліс а потім - в задній.
Г) Різницю значень відстаней порівнюють з табличними даними і якщо вона відрізняється - приступають до регулювання
Д) Сходження керованих коліс регулюють зміною довжини поперечної рульової тяги .при чому бокові наконечники тяг повинні мати однакову довжину
Тема: Операції ТО механізмів керування
Учбові питання:
1. Перевірка люфту рульового колеса
2. Перевірка зусилля на ободі рульового колеса
3. Регулювання гальм
4. Прокачування гідроприводу гальм
1. Люфт рульового колеса проводять в такій послідовності:
А)Закріплюють за допомогою замків на ободі рульового колеса люфтомір
Б) Стрілку - покажчик люфтоміра установлюють на рульовій колонці
В) Колеса транспортного засобу ставлять прямо
Г) Повертають рульове колесо вліво до початку повороту коліс і становлюють стрілку - покажчик на рульовій колонці так, щоб вона була проти нуля шкали люфтоміра.
Д) Повертають рульове колесо вправо до початку повороту коліс і за шкалою люфтоміра визначають величину вільного ходу
2. Зусилля на ободі рульового колеса визначають слідуючим чином:
А) Встановлюють динамометр на ободі рульового колеса
Б) Повертають рульове колесо до тих пір, поки не почнуть повертатися керовані колеса
В) За шкалою динамометра фіксують зусилля повороту
3. Регулювання гальм включає в себе такі операції як: а) регулювання вільного ходу гальмівної педалі б) регулювання гальмівних механізмів. Вільний хід гальмівної педалі регулюють аналогічно як і вільний хід педалі зчеплення. Регулювання гальмівних механізмів поділяється на часткове і повне. Часткове регулювання виконують обертаючи червяк регулювального механізму( гальмівні системи з пневмоприводом) або ексцентрик ( гальмівна система з гідроприводом) наближаючи чи віддаляючи гальмівну колодку від барабану. Повне регулювання гальм здійснюють після заміни колодок або накладок , повертаючи опорні пальці на яких закріплені гальмові колодки в нижній частині.
4. Прокачування гідроприводу гальм виконують дві особи: одна знаходиться в кабіні водія, інша - біля гальмівного механізму. Дану операцію виконують в такій послідовності:
А) Перевірити рівень гальмівної рідини в бачку і при необхідності довести його до нормального
Б)Очистити від бруду і зняти захисні ковпачки на клапанах випускання повітря
В) На клапан випускання повітря надіти гумовий шланг і занурити його вільний кінець у скляну посудину з гальмівною рідиною
Г) Особа, яка знаходиться в кабіні водія декілька разів натискує на гальмівну педаль і утримує її в натисну тому стані
Д) Особа , яка знаходиться біля гальмівного механізму відкручує клапан випускання повітря на півоберта
Ж) Після того, як гальмівна педаль впала клапан випуску повітря закручують і операцію прокачування повторюють до тих пір, поки в посуну не буде витікати гальмівна рідина без бульбашок повітря.
З) Послідовність прокачування гальмівних механізмів залежить від марки транспортного засобу і може бути вказана в інструкції по експлуатації
Тема: Поточний ремонт автомобіля
Організація ремонту. Поточний ремонт виконується на автотранспортних підприємствах, станціях технічного обслуговування або базах централізованого технічного обслуговування і ремонту переважно агрегатним методом. Для заміни несправних агрегатів і вузлів на справні на автотранспортних підприємствах, в об'єднаннях і транспортних управліннях створюється оборотний фонд відповідно до нормативів.
Для автобусів, автомобілів-таксі, автомобілів швидкої медичної допомоги, пожежних машин, автомобілів, що перевозять небезпечні вантажі, і для інших видів рухомого складу; до яких пред'являються підвищені вимоги безпеки руху, рекомендується проводити поточний ремонт не тільки за потребою, але і як регламентований планово-попереджувальний ремонт з попередження відмов в терміни, обумовлені Положенням про технічне обслуговування і ремонт рухомого складу автомобільного транспорту.
Для забезпечення технічно справного стану кузова, кабіни, рами рухомого складу і встановленого на них обладнання-після половини встановленого пробігу до капітального ремонту проводиться регламентований поточний ремонт, який включає роботи з перевірки їх технічного стану і усунення виявлених несправностей. При цьому виробляються поглиблений огляд і діагностування, виконання необхідних робіт з відновленням або заміною деталей і. складальних одиниць, які досягли граничного стану, герметизація зварних швів і ущільнень, усунення вм'ятин і тріщин, видалення наслідків корозії, нанесення профілактичного протикорозійного покриття і при необхідності забарвлення. У помірно холодних, холодних і дуже холодних кліматичних районах регламентований поточний ремонт кузовів, кабін та рам автомобілів потрібно проводити щорічно перед настанням холодів.
Частина операцій поточного (планово-попереджувального) ремонту малої трудомісткості може виконуватися спільно з технічним обслуговуванням в порядку супутнього ремонту.
Виявлення потреби в поточному ремонті автомобілів виробляється, як правило, під час виконання операцій технічного обслуговування рухомого складу, в процесі огляду і діагностування автомобіля.
Технологія поточного ремонту. Основний обсяг робіт з поточного ремонту автомобілів на АТП проводиться за потреби на постах в зоні ремонту та на виробничих ділянках. Частина робіт, технологічно пов'язаних з операціями ТО-1 і ТО-2 виробляється на. лініях або постах обслуговування.
Організація технологічного процесу TP повинна враховувати, що весь обсяг виконуваних робіт включає в себе разборочно-складальні роботи, що виконуються на автомобілі, і роботи з окремими агрегатами, вузлами і деталями, що виконуються на відповідних виробничих ділянках. Розбірно-складальні роботи виконуються на універсальних або спеціалізованих постах. Роботи по ремонту деталей, вузлів і агрегатів виробляються, як правило, на спеціалізованих виробничих ділянках, оснащених необхідним технологічним обладнанням.
Обладнання, яке застосовується при поточному ремонті автомобілів, можна розділити на підйомно-транспортне, контрольно-діагностичне та регулювальне, складально: розбірних і ремонтне.
Тема: Капітальний ремонт автомобіля
Перед тим як провести капітальний ремонт автомобіля, попередньо необхідно демонтувати всі прилади електрообладнання, платформу і кабіну. Потім шасі авто піддаються мийці зовнішнього типу. Якщо капітальний ремонт проводиться в літній час, то перед цим необхідно зробити злив масла з основних агрегатів.
Процес розбирання автомобіля проводиться досить акуратно і повільно. Знімаються вузли укладаються в спеціалізовану тару. Це можуть бути металеві піддони або кошика. А вже потім подаються в мийну машину.
Деталі, які виготовлені з кольорового лиття, а також підшипники омиваються в спеціальних установках. Нагар на окремих частинах видаляється за допомогою механічних або хімічних пристосування. Якщо є необхідність, то можна зробити заміну і ремонт всіх необхідних деталей. При цьому заздалегідь, перед тим як приступати до капітального ремонту, варто вивчити інтернет магазин авто запчастин і комплектуючих, для того щоб знати що можна буде в ньому придбати, а що ні.
Для того щоб видалити накип зі стінок блоків і головок циліндрів, можна застосовувати кислотні та лужні розчини.
Після того як миття і очищення були зроблені, всі деталі проходять сортування і контроль на підготовлених, спеціалізованих для цих цілей столах. У процесі контролю виявляються дефекти і необхідність повної заміни деталей.
Процес дефектації проводиться спільно з технічними умовами, для того щоб зробити процес дефектації. Іншими словами він проводиться під суворим контролем даного документа. Після того як все вимито і необхідні деталі і вузли відремонтовані або замінені, варто проводити процес складання агрегатів автомобіля.
Даний процес виробляють по підгрупах і вузлів. Ведеться він на універсальних або спеціалізованих постах, в залежності від того, яка потужність ремонтного підприємства. Після того як агрегати і вузли були зібрані, всі вони проходять контроль і випробування із застосуванням спеціалізованих стендів.
Після того як всі агрегати фарбують, вони надходять на складання загальну автомобіля. Саме туди відправляються рама, кабіна і вузли електроустаткування, а також платформа.
Після складання автомобіля, весь агрегат проходить випробування і обкатку. Всі виявлені дефекти виправляються, а також проводиться регулювання всіх механізмів автомобіля, а далі його підфарбовування, якщо є необхідність. Після цих маніпуляцій, автомобіль відправляється на майданчик для зберігання.
Тема: Механізм газорозподілу
Призначення та класифікація механізмів газорозподілення 2-х та 4-х тактних двигунів їх характеристика
Призначення газорозподільного механізму
Газорозподільний механізм (ГРМ) призначений для вприскування пального і випуску відпрацьованих газів у двигунах внутрішнього згорання. Сам механізм газорозподілу буває нижньоклапанним (коли розподільний вал знаходиться в блоці циліндрів) і верхньоклапанним (передбачає розташування розподільного валу в головці блоку циліндрів). Існують й альтернативні механізми газорозподілу, такі як гільзова система ГРМ, десмодромна система і механізм зі змінними фазами.
Для двотактних двигунів механізм газорозподілу реалізується за допомогою впускних і випускних вікон в циліндрі. Для чотиритактних двигунів найбільш розповсюдженою є верхньоклапанна система, яку ми і розглянемо нижче.
Газорозподільний механізм 4-х тактного двигуна.
Будова газорозподільного механізму.
У сучасних двигунах газорозподільний механізм розташовується в головці блоку циліндрів двигуна. До його складу входять такі основні елементи:
Розподільний вал. Це складна по конструкції деталь, яка виготовляється із міцної сталі або чавуну з високою точністю обробки. Залежно від конструкції ГРМ розподільний вал може встановлюватися в головці блоку циліндрів або в картері двигуна (таке компонування зараз не застосовується). Це основна деталь, яка відповідає за послідовне відкриття та закриття клапанів.
На валу є опорні шийки і кулачки, які штовхають стрижень клапана або коромисло. Форма кулачка має певну геометрію, оскільки від цього залежить тривалість і ступінь відкриття клапана. Також кулачки виконані різноспрямованими, щоб забезпечувати поперемінну роботу циліндрів.
Привід. Крутний момент від колінчастого валу передається через привід на розподільний вал. Привід буває різним залежно від конструктивного рішення. Шестерня колінвала вдвічі менша за шестерню розподільного валу. Таким чином, колінчастий вал обертається вдвічі швидше. Залежно від типу приводу до його складу входять:
ланцюг чи ремінь;
шестірні валів;
натягувач (натяжний ролик);
Впускні та випускні клапани. Вони розташовані в головці блоку циліндрів і є стрижнями з плоскою головкою на одному кінці, яка називається тарілкою. Впускні та випускні клапани відрізняються за конструкцією. Впускний виготовляється цільною деталлю. Також він має більший діаметр тарілки для забезпечення найкращого наповнення циліндра свіжим зарядом. Випускний часто виготовляють із жароміцної сталі та з порожнім стрижнем для кращого охолодження, так як у роботі він піддається вищим температурам. У середині порожнини знаходиться натрієвий наповнювач, який легко плавиться та відводить частину тепла від тарілки до стрижня.
На тарілках клапанів зроблені спеціальні фаски, які забезпечують щільніше прилягання до отворів голівки блоку циліндрів. Це місце називається сідлом. Крім самих клапанів, у механізмі передбачені додаткові елементи, що забезпечують його правильну роботу:
Пружини. Повертають клапани у вихідне положення після натискання.
Маслозйомні ковпачки. Є особливими ущільнювачами, які не допускають попадання масла в камеру згоряння по стрижню клапана.
Направляюча втулка. Встановлюється в корпус ГБЦ та забезпечує точний рух клапана.
Сухарі. З їх допомогою пружина кріпиться на стрижні клапана.
. Штовхач.Через штовхачі передається зусилля від кулачка розподільного валу на стрижень. Виготовляються із високоміцної сталі. Вони бувають різних видів (механічні (склянки), роликові, гідрокомпенсатори). Тепловий зазор між механічними штовхачами та кулачками розподільного валу регулюється вручну. Гідрокомпенсатори або гідроштовхачі автоматично підтримують потрібний тепловий проміжок і не вимагають регулювання.
Коромисло або важелі. Просте коромисло є двоплечним важелем, який здійснює коливальні рухи. У різному компонуванні коромисла можуть працювати по-різному.
Принцип роботи
Колінчастий вал передає момент, що крутить, за допомогою приводу на розподільчий.
Кулачок на розподільчому валу натискає на штовхач чи коромисло.
Клапан переміщається всередину камери згоряння, відкриваючи доступ свіжому заряду або газам, що відпрацювали.
Після того, як кулачок проходить активну фазу впливу, клапан повертається на місце під дією пружини.
Варто також відзначити, що за повний робочий цикл розподільний вал робить 2 обороти, поперемінно відкриваючи клапана в кожному циліндрі, залежно від порядку їх роботи. Тобто, наприклад, при схемі роботи 1-3-4-2 в той самий момент часу в першому циліндрі будуть відкриті впускні клапани, а в четвертому випускні. У другому та третьому клапани будуть закриті.
За розташуванням розподільного валу
Існують два типи положення распредвала:
нижнє;
верхнє.
При нижньому розташуванні розподільний вал знаходиться в блоці циліндрів поряд з колінчастим валом. Зусилля від кулачків передається через штовхачі на коромисла, у своїй застосовуються спеціальні штанги. Вони є довгими стрижнями і зв'язують штовхачі внизу з коромислами нагорі. Нижнє розташування вважається не вдалим, але має і свої плюси. Зокрема, більш надійне з'єднання розподільного валу з коленвалом. Цей тип розташування на сучасних моторах не застосовується.
l
Для двотактних двигунів механізм газорозподілу реалізується за допомогою впускних і випускних вікон в циліндрі.
Чим вище обороти коленвала, тим більша потужність. Але, конструкція двотактних двигунів має таку особливість - чим швидше починає рухатися поршень, тим гірше продувається камера згоряння циліндра, оскільки вікна подачі та випуску газів, що відпрацювали, залишаються відкритими дуже мало часу.
Камерне продування - це видалення газів і впорскування палива в циліндр з картера. Паливо починає всмоктуватися і перебувати в картері під час руху поршня вгору. Потім, коли поршень йде вниз, впускний канал закривається і відкривається продувне вікно, через яке подається нова порція палива і виганяються гази попередньої суміші палива, що відпрацювала (дивіться малюнок вище, посередині).
Така проста конструкція двотактного двигуна виключає необхідність встановлювати газорозподільний механізм (ГРМ), насоса продування, клапанів та вузла мастила.
Тема ;Система охолодження двигуна
Система охолодження
- Принцип роботи системи охолодження
Система охолодження призначена для охолодження деталей двигуна, що нагріваються в результаті його роботи. На сучасних автомобілях система охолодження, крім основної функції, виконує ряд інших функцій, в тому числі:
Залежно від способу охолодження розрізняють наступні види систем охолодження: рідинна (закритого типу), повітряна (відкритого типу) та комбінована. В системі рідинного охолодження тепло від нагрітих частин двигуна відводиться потоком рідини. Повітряна система для охолодження використовує потік повітря. Комбінована система об'єднує рідинну і повітряну системи.
На автомобілях найбільшого поширення набули система рідинного охолодження. Дана система забезпечує рівномірне і ефективне охолодження, а також має менший рівень шуму. Тому, пристрій і принцип дії системи охолодження розглянуті на прикладі системи рідинного охолодження.
Конструкція системи охолодження бензинового і дизельного двигунів подібні. Система охолодження двигуна включає безліч елементів, серед яких радіатор охолоджувальної рідини, масляний радіатор, теплообмінник опалювача, вентилятор радіатора, відцентровий насос, а також розширювальний бачок і термостат. У схему системи охолодження включена «сорочка охолодження» двигуна. Для регулювання роботи системи використовуються елементи управління.
Радіатор призначений для охолодження нагрітої охолоджуючої рідини потоком повітря. Для збільшення тепловіддачі радіатор має спеціальне трубчасте пристрій.
Поряд з основним радіатором в системі охолодження можуть встановлюватися масляний радіатор і радіатор системи рециркуляції відпрацьованих газів. Масляний радіатор служить для охолодження масла в системі змащення.
Радіатор системи рециркуляції відпрацьованих газів охолоджує відпрацьовані гази, чим досягається зниження температури згоряння паливно-повітряної суміші і утворення оксидів азоту. Роботу радіатора відпрацьованих газів забезпечує додатковий насос циркуляції охолоджуючої рідини, що входить в систему охолодження.
Теплообмінник опалювача виконує функцію, протилежну радіатора системи охолодження. Теплообмінник нагріває, що проходить через нього, повітря. Для ефективної роботи теплообмінник опалювача встановлюється безпосередньо біля виходу нагрітої охолоджуючої рідини з двигуна.
Для компенсації зміни обсягу охолоджуючої рідини внаслідок температури в системі встановлюється розширювальний бачок. Заповнення системи охолоджувальною рідиною зазвичай здійснюється через розширювальний бачок.
Циркуляція охолоджувальної рідини в системі забезпечується відцентровим насосом. У побуті відцентровий насос називають помпою. Відцентровий насос може мати різний привід: шестерінчастий, пасової та ін. На деяких двигунах, обладнаних турбонаддувом, для охолодження наддувочного повітря і турбокомпресора встановлюється додатковий насос циркуляції охолоджуючої рідини, що підключається блоком управління двигуном.
термостат призначений для регулювання кількості охолоджувальної рідини, що проходить через радіатор, чим забезпечується оптимальний температурний режим в системі. Термостат встановлюється в патрубку між радіатором і «сорочкою охолодження» двигуна.
На потужних двигунах встановлюється термостат з електричним підігрівом, який забезпечує двоступенева регулювання температури охолоджуючої рідини. Для цього в конструкції термостата передбачено три робочих положення: закрите, частково відкрите і повністю відкрите. При повному навантаженні на двигун за допомогою електричного підігріву термостата проводиться його повне відкриття. При цьому температура охолоджуючої рідини знижується до 90 ° С, зменшується схильність двигуна до детонації. В інших випадках температура охолоджуючої рідини підтримується в межах 105 ° С.
вентилятор радіатора служить для підвищення інтенсивності охолодження рідини в радіаторі. Вентилятор може мати різний привід:
- механічний (постійне з'єднання з колінчастим валом двигуна);
- електричний (керований електродвигун);
- гідравлічний (гідромуфта).
Найбільшого поширення набув електричний привід вентилятора, що забезпечує широкі можливості для регулювання.
Типовими елементами управління системи охолодження є датчик температури охолоджуючої рідини, електронний блок управління і різні виконавчі пристрої.
Датчик температури охолоджуючої рідини фіксує значення контрольованого параметра і перетворює його в електричний сигнал. Для розширення функцій системи охолодження (охолодження відпрацьованих газів в системі рециркуляції відпрацьованих газів, регулювання роботи вентилятора і ін.) На виході радіатора встановлюється додатковий датчик температури охолоджуючої рідини.
Сигнали від датчика приймає електронний блок управління і перетворює їх в управлінський вплив на виконавчі пристрої. Використовується, як правило, блок керування двигуном з устанавленнимі відповідним програмним забезпеченням.
У роботі системи управління можуть використовуватися такі виконавчі пристрої: нагрівач термостата, реле додаткового насоса охолоджуючої рідини, блок управління вентилятором радіатора, реле охолодження двигуна після зупинки.
Принцип роботи системи охолодження
Роботу системи охолодження забезпечує система управління двигуном. У сучасних двигунах алгоритм роботи реалізований на основі математичної моделі, яка враховує різні параметри (температуру охолоджуючої рідини, температуру масла, зовнішню температуру і ін.) І задає оптимальні умови включення і час роботи конструктивних елементів.
Охолоджуюча рідина в системі має примусову циркуляцію, яку забезпечує відцентровий насос. Рух рідини здійснюється через «сорочку охолодження» двигуна. При цьому відбувається охолодження двигуна і нагрів охолоджуючої рідини. Напрямок руху рідини в "сорочці охолодження" може бути поздовжнім (від першого циліндра до останнього) або поперечним (від випускного колектора до впускного).
Залежно від температури рідина циркулює по малому або великому колу. При запуску двигуна сам двигун і охолоджуюча рідина в ньому холодні. Для прискорення прогріву двигуна охолоджуюча рідина рухається по малому колу, минаючи радіатор. Термостат при цьому закритий.
У міру нагрівання охолоджуючої рідини термостат відкривається, і охолоджуюча рідина рухається по великому колу - через радіатор. Нагріта рідина проходить через радіатор, де охолоджується зустрічним потоком повітря. При необхідності рідина охолоджується потоком повітря від вентилятора.
Після охолодження рідину знову надходить в «сорочку охолодження» двигуна. В ході роботи двигуна цикл руху охолоджувальної рідини багаторазово повторюється.
На автомобілях c турбонаддувом може застосовуватися двоконтурна система охолодження , В якій один контур відповідає за охолодження двигуна, інший - за охолодження наддувочного повітря.
Тема : Система мащення
Елементи системи мащення
Масляний насос забезпечує в системі безперервну циркуляцію масла і подачу його під тиском до деталей.
На сучасних автотракторних двигунах застосовують шестеренчасті масляні насоси, які мають просту будову й забезпечують надійну роботу.
Односекційний масляний насос складається з корпуса 1 і кришки 2. Корпус насоса кріпиться всередині картера до перетинок нижньої площини циліндрів двома болтами і фіксується на перетинці двома штифтами, запресованими в корпус. До нижньої частини корпуса болтами фіксується маслоприймач 7. В отворах корпуса 1 і кришки 2 встановлений на підшипниках ведучий вал 3. На одному кінці вала є шліци, призначені для встановлення шестерні приводу насоса. На валу за допомогою шпонки або шліців жорстко закріплюється ведуча шестерня 4. Її зубці входять в зачеплення із зубцями веденої шестерні 6, яка виготовляється окремо або разом з валиком 9. Якщо шестерня 6 виготовляється окремо, вона вільно обертається на запресованому у корпус валику 9.
Між зубцями шестерень 4 і 6 та стінками корпуса 1 є невеликий зазор - 0,05...0,1мм.
Насос працює так:
- При обертанні колінчастого вала шестерні масляного насоса обертаються в різні сторони;
- Під дією створеного при обертанні шестерень розрідження, масло із піддона картера через сітку 8 маслоприймача 7 і вхідний канал 10 надходить до шестерень 4 і 6;
- Потрапляючи між зубцями шестерень 4, 6 і корпусом 1 насоса, воно переноситься зубцями у вихідний канал 5;
- Оскільки шестерні обертаються з великою швидкістю, то в канал 5 масло подається під тиском. Величина тиску, створеного насосом, як і його подача, залежать від розмірів насоса, частоти обертання шестерень, опору в трубопроводах і каналах та від спрацювання деталей насоса.
У холодну пору року масляний насос, особливо нового двигуна, подає велику кількість масла, тиск якого в системі (від насоса до головного масляного канала) зростає через опір трубопроводів проходженню масла надмірної в'язкості. Щоб запобігти пошкодженню фільтра й інших деталей системи, в корпусі насоса є редукційний запобіжний клапан, який автоматично обмежує величину максимального тиску в системі. При значному підвищенні тиску стаканчик 12 (або кулька) стискає пружину 13 і частина масла по перепускному каналу 11 надходить в піддон картера. Змінюючи попереднє стискання пружини 13 регулювальним гвинтом 14, який фіксується відносно корпуса насоса контргайкою, регулюють максимальний тиск масла в системі (0,65...0,70 МПа).
Без редукційного клапана після пуску охолодженого двигуна з холодним та густим маслом тиск у магістралі перевищував би 100 МПа.
На дизелях модифікації СМД-60 встановлюється двосекційний масляний насос. Він має основну секцію, яка подає масло в головний масляний канал, і додаткову, яка подає масло до масляного радіатора.
Для забезпечення мащення тертьових поверхонь перед пуском дизеля, що полегшує пуск і зменшує спрацювання деталей, на дизелях модифікації СМД-60 і ЯМЗ-240 встановлений насос передпускового прокачування масла.
Фільтри забезпечують очищення масла від сторонніх предметів, які потрапили при перевезенні і зберіганні, а також від металевих і мінеральних частинок, що утворилися в процесі спрацювання деталей, згоряння палива й окислення масла.
На сучасних дизелях застосовується багатоступеневе очищення масла із використанням фільтрів грубої і тонкої очистки.
Фільтрами грубої очистки масла на всіх дизелях є металева сітка маслозаливної горловини і металева сітка, встановлена в корпусі маслоприймача.
Фільтри тонкої очистки очищують масло від механічних частинок невеликого розміру (до 2...3 мкм) і смолистих речовин. Фільтруючі елементи таких фільтрів змінні (картонні, паперові, з тканини та деревного борошна).
На сучасних тракторних двигунах такими фільтрами є центрифуги з частотою обертання ротора 5000...9000 хв1 (об/хв). У дизеля ЯМЗ-240Б основну частину масла, яка надходить у головну масляну магістраль, очищає фільтр зі змінними фільтрувальними елементами з деревного борошна, а меншу частину, яка знову повертається в піддон картера, - центрифуга.
Залежно від характеру сил, які обертають ротор, центрифуги бувають реактивними або активно-реактивними. Центрифуга, яка встановлена в системі так, що через неї проходить весь потік масла після масляного насоса, називається повнопоточною. Центрифуга, через яку проходить частина масла, називається неповнопоточною.
Повнопоточна реактивна масляна центрифуга дизеля СМД-60 складається з нерухомої і рухомої (ротора) частин і змонтована в корпусі 1. В корпус 1 вкручено пустотілу вісь 6 з нижньою 31 і верхньою 30 опорними шийками. На осі нерухомо (за допомогою гайки 10) закріплюється захисний ковпак 12, а ротор - з можливістю обертання відносно осі і вісьовим переміщенням 0,2-0,6 мм за допомогою гайки 8, упорної шайби 9 і гайки 11. Між ковпаком 12 і корпусом 1 встановлюється ущільнювальна паронітова прокладка 15.
В корпусі 1 є вхідні і вихідні канали, які з'єднуються з відповідними каналами осі 6. Вихідний канал осі - це відвідна трубка 2, запресована у вісь, а вхідний канал - місткість між внутрішньою поверхнею осі і зовнішньою поверхнею трубки 2. Для сполучення об'єму ротора з відповідними каналами на осі виконують отвори 28 і 26. Між вхідними 16 і вихідними 21 каналами корпуса встановлений запобіжний клапан, який підтримує необхідний тиск у центрифузі.
Запобіжний клапан 19 виготовлений у вигляді циліндричного плунжера з виточкою в середній частині для проходження масла по каналу 16 до центрифуги. До плунжера на різьбі приєднаний шток 23, який проходить крізь отвір упора 20. Шток 23 відносно клапана 19 зафіксований шплінтом. Між торцем штока і гніздом отвору порож нини запобіжного клапана 19 встановлений перепускний кульковий клапан, який складається з кульки 17 і пружини 18. На штоці 23, між упором 20 і шайбою, встановленою в канавку штока, діє пружина 22. Отвір під запобіжний клапан в корпусі 1 закривається заглушкою 24.
Ротор центрифуги із алюмінієвого сплаву складається з остова 4 і кришки 7, з'єднаних між собою за допомогою упорної шайби і гайок. Зверху упорної шайби 9 встановлюється мідна прокладка, в канавках остова, між остовом 4 і кришкою 7, ущільнювальне гумове кільце 14. Виступ (колонка) у верхній частині остова 4 тримає ротор на опорних шийках осі 6. Верхня 30 і нижня 31 шийки осі - це опори остова 4, а середня 32 розмежовує місткості очищеного і неочищеного масла. В нижній частині остова 4 виконують литі приливки. В різьбових отворах приливків встановляються дві форсунки 3 з каліброваними отворами діаметром 2,3 мм. Форсунки розташовані по дотичній до кола обертання (в протилежні сторони) радіусом 40 мм. У верхній частині остова двома гвинтами закріплений масловідбивач 5 і насадка 13.
Масло від насоса під тиском надходить по отворах у блок-картері і корпусі 1 до вхідного каналу 16 і отворів 28 в осі 6. Із отворів 28 масло через отвори масловідбивача 5 потрапляє до внутрішньої стінки насадки 13, звідки направляється до осі 6 і вверх. Це забезпечує рівномірніший розподіл осаду сторонніх домішок на внутрішніх стінках кришки 7, обмежує їх змивання зі стінок кришки 7 масла, яке надходить в ротор. Через різницю діаметрів опорних шийок 30 і 31 осі 6 утворюється осьова сила, що піднімає ротор уверх. При роботі центрифуги ротор не тисне на опорні шийки 30 і 31.
Частина масла з верхньої частини ротора подається до форсунок. Витікаючи з великою швидкістю через соплові отвори форсунок, масло утворює реактивний крутний момент, який обертає ротор центрифуги. При обертанні ротора з великою швидкістю механічні частинки і продукти спрацювання масла під дією відцентрових сил відкидаються до стінок кришки і осідають у вигляді спресованої маси. Очищене масло по отворах 26 осі 6 подається в масловідвідну трубку 2, канал 21 центрифуги і в головну масляну магістраль дизеля.
При підвищенні тиску у вихідному каналі 21 центрифуги підвищується тиск і в каналі 16 для підведення масла до центрифуги. Масло діє на плунжер 19 запобіжного клапана і він, стискуючи пружину 22, переміщується вправо разом зі штоком 23. Правий кінець плунжера виходить із розточки корпуса 1 і частина масла із впускного каналу 16 центрифуги надходить в картер 29 для зливання масла з форсунок і звідти-в піддон картера. Тиск на вході в центрифугу знижується. Запобіжний клапан відрегульований на відкривання при тиску у вихідному каналі 0,45...0,57 МПа. При зростанні різниці тисків у каналах 16 і 21 до 0,6...0,7 МПа, що може бути при пуску холодного двигуна, масло надходить по отворах плунжера до кульки 17 перепускного клапана, стискає пружину 18 і переміщає кульку вліво. Із вхідного каналу 16 неочищене масло подається до вихідного каналу 21.
При зменшенні різниці тисків пружинами 18 і 22 перепускний і запобіжний клапани повертаються у початкове положення.
Осад зі стінок кришки ротора знімається дерев'яним скребком під час технічного обслуговування, потім стінки кришки промиваються дизельним паливом.
Робота реактивної центрифуги (відео)
Центрифуга з активно-реактивним приводом дизеля Д-240 відрізняється від центрифуги з реактивним приводом відсутністю форсунки і все масло, яке дається в ротор центрифуги, спрямовується в головну масляну магістраль. Це дозволяє подовжити строк роботи масла, оскільки воно не збагачується киснем, менше окисляється і вигоряє. Крім того, при цьому зменшується загальний потік масла і відповідно витрати енергії на привод масляного насоса.
На нижній частині осі 1 ротора центрифуги нерухомо прикріплено насадку 7. В ній виконуються канали (позначені буквою Н), розміщені по дотичних до кола обертання у протилежних напрямах. Проти каналів Н насадки є два отвори, які з'єднують впу скний канал центрифуги з каналами насадки, та чотири радіальних отвори в колонці 8 остова ротора, що з'єднують канали насадки з робочим об'ємом ротора центрифуги.
У верхній частині колонки 8 ротора аналогічно виконують три канали, позначені літерою В. Вхід до каналів розташований у протилежному від обертання ротора напрямі. Проти каналів В колонки виконано чотири радіальних отвори осі 1.
Масло, яке під тиском подається до каналів Н насадки 7, за дотичною лінією спрямовується на великій швидкості в порожнину НП колонки. Потік масла створює активний момент, який змушує ротор обертатися. Потім отворами в колонці масло рухається в порожнину ротора, де під дією відцентрових сил очищується від домішок.
Очищене масло піднімається у верхню частину ротора і тангенціальними каналами В колонки спрямовується у порожнину ВП, розташовану між колонкою 8 і віссю 1. Під час проходження масла через канали В також виникають реактивні сили, крутішії момент яких співпадає з активним моментом насадки 7. Ці два моменти обертають ротор. Масло з порожнини ВП каналами осі 1 надходить в масловідвідну трубку 6 і далі - в головну магістраль.
Останнім часом замість центрифуги, навіть на тракторних двигунах, почали встановлювати фільтри для очищення масла з паперовими фільтруючими елементами
Масляний радіатор. Для нормальної роботи двигуна температура масла в системі маїцення повинна бути 70...85°С. При нагріванні масла вище 90°С його в'язкість значно знижується. Воно випаровується, гірше охолоджує і змащує деталі. Зростають його витрати. Масляний радіатор забезпечує зниження температури масла на 10...20°С.
На двигунах з повітряним охолодженням радіатор (змійовик) з ребрами встановлюється під кожухом вентилятора, перед циліндрами.
Радіатори двигунів з рідинним охолодженням подібні за конструкцією, але відрізняються за розмірами, кількістю охолоджувальних трубок та способом їх розміщення.
Масляний радіатор дизеля ЯМЗ-240Б складається з верхнього 4 і нижнього 1 бачків, між якими в один ряд встановлені овальні сталеві трубки 2. На трубки спіраллю навиті сталеві стрічки (ребра) З, які збільшують поверхню охолодження. Бачки розділені перетинками 6 на відсіки, що забезпечує ефективніше охолодження масла через збільшення шляху і часу проходження його через радіатор. Для нижньої стінки бачка 4 приварені сталеві трубки 5 і 7 з гумовими трубопроводами вхідних і вихідних каналів систем мащення дизеля і коробки передач (2/3 об'єму масляного радіатора призначені для охолодження масла дизеля - моторної секції, а 1/3 об'єму - коробки передач).
Масляний радіатор розташований перед рідинним радіатором системи охолодження і прикріплений до нього. Він включається в роботу залежно від пори року за допомогою спеціального крана.
Роботу системи мащення контролюють такими приладами і пристроями:
- рівень масла у піддоні картера масломірною лінійкою;
- тиск масла в головній магістралі електричним або механічним (мембранним) манометрами та сигнальними (індикаторами) лампочками;
- температуру масла - дистанційними термометрами.
На всіх дизелях встановлені масломірні лінійки, на більшості дизелів з рідинним охолодженням контролюється лише тиск масла, на дизелях з повітряним охолодженням - тиск і температура масла.
Дистанційні манометри бувають електричні і трубчасті.
Електричний манометр складається з датчика і покажчика, включених в електричну схему. Корпус датчика 6 вкручується в остов. До нього по каналу підводиться масло із головного масляного каналу. Між корпусом і кришкою датчика встановлено діафрагму 4. З одного боку на діафрагму тисне масло, з іншого вона з'єднана з рухомим контактом 7 реостата 5. Один кінець реостата з'єднаний з мінусовою клемою акумуляторної батареї, другий - з плюсовою.
В корпусі електромагнітного покажчика встановлений екран, три котушки 3, рухомий магніт зі стрілкою 2, закріпленою рухомо на осі, і нерухомого магніту для встановлення стрілки на нульову позначку шкали. Екран запобігає впливу побічних магнітних полів на роботу покажчика.
При роботі електричної схеми величина струму в котушках 3 залежить від положення рухомого контакту 7 на реостаті 5, а самого контакту 7 - від величини тиску в системі. При підключенні струму до котушок 3 утворюється сумарне магнітне поле. Взаємодіючи з ним, стрілка 2 встановлюється у відповідне положення, пропорційне величині тиску в головній масляній магістралі.
Вентиляція картера двигуна
При роботі двигуна через нещільності між поршневими кільцями, поршнем і гільзою циліндра в картер надходять горюча суміш і відпрацьовані гази, які містять пари палива, води і сірчистого газу. Пари палива, які конденсуються на стінках циліндра і потрапляють в піддон картера, розріджують масло. Пари води, конденсуючись в піддоні картера, утворюють піну і емульсії. Сірчистий газ, сполучаючись з водою, яка є в маслі, утворює сірчану кислоту. Кислота, потрапляючи з маслом на робочі поверхні деталей, роз'їдає і прискорює їх спрацювання.
Для виведення газів із картера застосовується система вентиляції картера двигуна. У сучасних автомобільних карбюраторних двигунів застосовують примусову систему вентиляції картера, на дизелях тракторів вентиляція відбувається за допомогою сапуна. Він встановлюється в заливній горловині системи мащення або окремо на кришці головки циліндрів і сполучає картер з атмосферою. За рахунок різниці тисків в картері й атмосфері, гази, виходять із картера. Це зменшує дію парів палива, води і відпрацьованих газів на масло і запобігає можливості витікання масла через зазори в площинах рознімання деталей. В корпусі сапуна встановлений фільтр, переважно із дроту, який утримує краплі масла.
Тема : Газобалонні установки
Газобалонні установки бувають двох типів: для стисненого газу і для зрідженого газу. В установках першого виду використовується метан, який знаходиться в балонах під тиском 200 - 250 атм , в установках другого типу знаходиться пропан під тиском 16 атм. Установка для зрідженого газу ( пропан) складається з газового балона, виносного заправочного пристрою,, мультиклапана,газової магістралі, газовий фільтр клапан,редуктор_ випарник , дозатор, електронний блок керування.. Заправочний пристрій служить для безпечного підєднання заправочного рукава на АЗС.. Мультиклапан монтується на горловині балона і включає в себе показчик рівня газу, заборну трубку, клапани ( заправочний і витратний). Газовий клапан - фільтр служить для очистки газу і перекриття газової магістралі під час стоянки або при роботі на бензині. Редуктор - випарник знижує тиск газу до атмосферного і переводить його в газоподібний стан. Дозатор призначений для регулювання обертів холостого ходу.. Принцип дії установки слідуючий : газ в рідкому стані під тиском поступає в редуктор - випарник, проходячи через газовий клапан - фільтр, в редукторі тиск газу понижується до атмосферного і він випаровується і поступає в змішувач для приготування робочоє суміші. Для запобігання обмерзання редуктора він підігрівається охолоджуваною рідиною двигуна.
Тема: Система освітлення і сигналізації
Сучасний автомобіль включає в себе цілий комплекс освітлювальних приладів, які в сукупності складають систему освітлення. У число її головних завдань входить:
- освітлення проїжджої частини та узбіччя;
- додаткове освітлення дороги під час туману, дощу, снігопаду;
- інформування інших водіїв про виконувані маневри;
- Попередження про гальмуванні;
- інформування про габарити машини;
- попередження про виниклу поломки, в результаті якої автомобіль створює перешкоду на проїзній частині;
- забезпечення читаності реєстраційного знака у вечірній і нічний час;
- освітлення салону, підкапотного простору та багажника.
ОСНОВНІ ЕЛЕМЕНТИ СИСТЕМИ
Всі елементи системи освітлення можна розділити на дві основні категорії:
- зовнішні;
- внутрішні.
ЗОВНІШНІ ЕЛЕМЕНТИ
Зовнішні елементи автомобільної оптики забезпечують освітлення дороги і інформування інших водіїв. До числа таких приладів відносяться:
- фари ближнього і дальнього світла;
- протитуманні фари;
- покажчики поворотів;
- задні блок-фари;
- габаритні вогні;
- освітлювачі номерного знака.
ПЕРЕДНІ ФАРИ
Передні фари сучасних автомобілів складаються з цілого комплексу елементів:
- ближнього і дальнього світла;
- денних ходових вогнів;
- габаритних вогнів.
Найчастіше вони розташовані в єдиному корпусі. Також в передні фари багатьох автомобілів встановлюють поворотники.
Будь-яка машина комплектується двома передніми фарами, які розташовуються симетрично на правій і лівій частинах кузова.
У вечірній і нічний час для освітлення дороги використовується ближнє світло. Завдяки асиметричності світлових пучків, він додатково забезпечує освітлення узбіччя дороги. За умови правильного регулювання фар таке світло не доставляє дискомфорту водіям зустрічних автомобілів.
Дальнє світло відрізняється більшою інтенсивністю. Його використання допомагає вихоплювати з темряви велику зону дорожнього полотна. Однак використовувати дальнє світло допустимо тільки при відсутності зустрічного потоку. В іншому випадку фари будуть засліплювати інших водіїв.
ГАБАРИТНІ ВОГНІ
Для того щоб інші водії могли оцінити габарити машини, в системі освітлення передбачені габаритні вогні. Вони використовуються і в момент зупинки або стоянки машини. Розташовуються габарити як в передніх, так і в задніх фарах.
ПОВОРОТНИКИ
Поворотники - основний інструмент попередження про виконання маневру. Вони використовуються при повороті і розвороті, перестроюванні або обгоні, з'їзді на узбіччя і при подальшому початку руху.
Встановлюватися дані елементи можуть як в передні і задні фари, так і окремо від них. Часто на бічних елементах кузова і дзеркалах заднього виду розміщуються дублюючі прилади. Всі вони мають насичений жовто-оранжевий колір і працюють синхронно в режимі миготіння. Автомобілі, призначені для американського ринку, мають червоний колір поворотников.
ДЕННІ ХОДОВІ ВОГНІ
Денні ходові вогні з'явилися в системі освітлення автомобіля порівняно недавно, тому вони є не в кожному транспортному засобі. Від габаритів ДХВ відрізняються більш інтенсивним світлом.
ПРОТИТУМАННІ ФАРИ
Цей вид автомобільної оптики застосовується в умовах поганої видимості: під час туману, дощу або снігу. Широкий світловий промінь з усіченої частиною не відбивається від атмосферних опадів і не засліплює водія під час руху. У той же час ВТФ забезпечують достатнє освітлення дорожнього полотна.
Противотуманки встановлюються не тільки на передній, а й на задній частині кузова. Втім, дані освітлювальні елементи не є обов'язковими, тому на багатьох моделях машини ВТФ можуть бути відсутні зовсім.
ЗАДНІ БЛОК-ФАРИ
Задні автомобільні фари також встановлюються на автомобіль парно і включають в себе кілька елементів. Найбільш прості варіанти задніх фар складаються з стоп-сигналу і габаритних вогнів. У багатьох моделях в блок також входять поворотники і ліхтар заднього ходу, рідше - задні протитуманні фари.
Основним елементом освітлювальної системи в задній частині є стоп-сигнали, що інформують про гальмування або зниження швидкості автомобіля. Для більшої надійності елементи можуть дублюватися на спойлері або на задньому склі транспортного засобу.
Також не менш важливими є ліхтарі заднього ходу. Вони виконують функції освітлення і попередження інших водіїв про початок руху машини назад.
ВНУТРІШНІ ЕЛЕМЕНТИ ОСВІТЛЮВАЛЬНОЇ СИСТЕМИ
Внутрішні елементи відповідають за висвітлення в салоні і багажнику транспортного засобу. У систему входять:
- лампи в салоні автомобіля;
- підсвічування багажника;
- лампи освітлення приладової панелі;
- лампа в бардачку;
- габаритні вогні в дверях.
Освітлення салону, багажника і простору під капотом (при наявності) забезпечує додатковий комфорт водія в темну пору.
Підсвічування приладової панелі необхідна для більш легкого зчитування інформації при русі в темряві.
Габаритні вогні в дверях необхідні для інформування інших учасників дорожнього руху про зміну габаритів автомобіля при відкритих дверях.
ЯК ВІДБУВАЄТЬСЯ УПРАВЛІННЯ СИСТЕМОЮ ОСВІТЛЕННЯ
Управління всіма приладів освітлення водій здійснює з салону транспортного засобу за допомогою спеціальних перемикачів.
Включення ближнього і дальнього світла, протитуманних фар і габаритів в більшості моделей машин здійснюється за допомогою підрульового перемикача або клавіші на панелі приладів:
- перше положення перемикача - всі прилади вимкнені;
- друге положення - включаються габарити;
- третє положення - загоряється ближнє світло фар.
Також перемикач, розміщений з лівого боку під кермом, забезпечує зміну ближнього і дальнього світла в передніх фарах.
При наявності противотуманок на перемикачі може бути встановлена додаткова секція, яка регулює включення і виключення ВТФ. Також управління може відбуватися за допомогою окремої клавіші.
Комбінований перемикач використовується і для введення в дію правого і лівого поворотів. Але при цьому аварійна сигналізація включається за допомогою окремої клавіші, що знаходиться на приладовій панелі.
Багато елементів системи освітлення загоряються автоматично при виконанні певних дій з боку водія:
- стоп-сигнали - при натисканні на педаль гальма;
- ліхтар заднього ходу - при включенні задньої передачі;
- прилади освітлення багажника і бардачка - при їх відкритті;
- підсвічування ніг водія і габарити в дверях - при відкритті дверей.
АВТОМАТИЧНІ СИСТЕМИ УПРАВЛІННЯ ОСВІТЛЕННЯМ
У міру розвитку технологій автомобілебудування також впроваджуються додаткові функції автоматичного керування освітлювальними приладами:
- включення ближнього світла;
- активне головне освітлення;
- адаптивне освітлення;
- корекція головного освітлення;
- управління дальнім світлом.
Всі перераховані системи регулюються в автоматичному режимі на основі даних, що зчитуються спеціальними датчиками при зміні дорожньої обстановки і умов руху.
Комплекс елементів, що входять в систему освітлення автомобіля, призначений для забезпечення безпеки водія, його пасажирів та інших водіїв. Без освітлювальних приладів поїздка на автомобілі у вечірній і нічний час недопустима. Постійно вдосконалюючись, система освітлення забезпечує необхідні комфорт і безпеку під час вечірніх і нічних поїздок, а також при переміщенні в умовах недостатньої видимості.