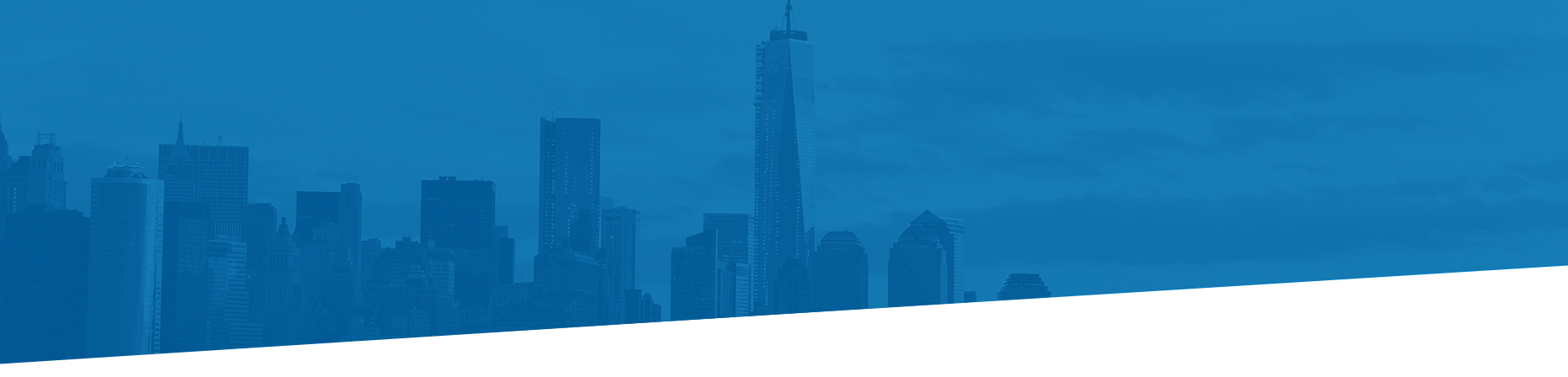
ОСНОВИ СЛЮСАРНОЇ СПРАВИ
Тема: Паяння металу
Учбові питання
1. Загальні відомості
2. Обладнання і матеріали для паяння
3. Технологія паяння мякими припоями
4. Технологія паяння твердими припоями
Література:А. Попов, Т. Пахар, " Основи слюсарної справи" стр.57 - 63
1. Паяння - процес утворення нерознімного зєднання за допомогою припою. Припой - сплав декількох металів. Паяння застосовують для отримання міцних і герметичних зєднань. Температура плавлення припою значно нижча температури плавлення зєднувальних деталей.
2. Для паяння металів необхідно мати:
а) паяльник
б) припой
в) флюс
Паяльники служать для разплавлення припою. За конструкцією вони бувають електричні, газові,імпульсні, термоповітряна паяльна станція, інфрачервона паяльна станція, автономні акумуляторні. Припої служать для зєднання металів між собою. За температурою плавлення припої діляться на мякі (температура плавлення до 400* С) і тверді( температура плавлення більше 550* С). До мяких припоїв відносяться: оловяно - свинцеві, оловяно - цинкові, оловяно - свинцево - кадмієві.До твердих припоїв відносяться: мідно - цинкові, срібні. Флюс захищає розплавлений метал від корозії. Як флюс при паянні застосовують каніфоль, віск, соляна кислота ,хлористий цинк,рідке скло.
3. Технологія паяння мякими припоями включає в себе такі операції:
а) підгонка деталей одну до одної
б)очищення місця паяння
в) нанесення на очищену поверхню флюсу
г) очищення робочого кінця паяльника напилком або шкуркою
д)лудіння паяльника (натирання нашатирем)
ж) нанесення паяльником розплавленого припою на зєднувальні деталі
4.Технологія паяння твердими припоями складається з таких операцій:
а)обпилювання і підгонка зєднувальних деталей
б)деталі зєднують і закріплюють між собою за допомогою притискних пристроїв
в) місце паяння покривають флюсом і повільно прогрівають
г) на нагрітий шов кладуть припій і розплавляють його
Тема : Рубання металу
Учбові питання:
1. Призначення
2.Обладнання і інструмент
3. Технологія рубання.
Література:А. Попов, Т. Пахар, " Основи слюсарної справи" стр.11 - 17
1. Рубання металу - слюсарна операція призначена для зняття зайвого шару металу або розрубування заготовки на частини за допомогою слюсарного інструменту. Точність рубання 0,5 - 0,7 мм.
2. Для рубання необхідне таке обладнання і інструмент:
а) слюсарні лещата або плита
б) слюсарний молоток
в) зубило
г) крейсмейсель - зубило для вирубування шпоночних канавок
Слюсарний молоток складається з таких частин як бойок ( ударна частина), середина і вузький кінець.. Середина молотка має отвір для ручки молотка. Ручка молотка виготовляється з твердої породи дерев а слюсарний інструмент для рубання - з вуглецевої інструментальної сталі. Молотки можуть мати круглий і квадратний бойки.Рекомендована вага молотка для підлітків - 500 грам, для дорослих - 600 грам. Зубило має ударну , середню і різальну частину. Кут заточки зубила залежить від оброблюваного матеріалу і для сталі складає - 60 градусів.
3.Технологія рубання включає в себе такі операції::
а) підготовка робочого інструменту
б) закріплення заготовки в лещатах або на плиті
в)розмітка заготовки
г) рубання металу
Тема: Свердління
Свердлінням називається утворення зняттям стружки отворів в суцільному матеріалі за допомогою ріжучого інструменту - свердла, що здійснює обертальний і поступальний рухи щодо своєї осі.
Свердління застосовується:
- для отримання невідповідальних отворів, невисокого ступеня точності і невисокого класу шорсткості, наприклад під кріпильні болти, заклепки, шпильки і т. Д.;
- для отримання отворів під нарізування різьблення, розгортання і зенкерування.
Розсвердлювання називається збільшення розміру отвору в суцільному матеріалі, отриманого литтям, куванням, штампуванням або іншими способами.
Свердлінням і розсвердлюванням можна отримати отвір 10-го в окремих випадках 11 - го квалітету і шорсткість поверхні rz-320-н 80. Коли потрібна більш висока якість поверхні отвору, його (після свердління) додатково зенкерують і розгортають.
Точність свердління в окремих випадках може бути підвищена завдяки ретельному регулюванню верстата, правильно заточеному свердлу або свердлінням через спеціальне пристосування, зване кондуктором. Свердла поділяються на спіральні, з прямими канавками, перові, для глибокого, кільцевого свердління і центрувальні
Свердла виготовляються з швидкорізальних, легованих і вуглецевих сталей, а також оснащуються пластинками з твердих сплавів.
Для свердління отворів частіше застосовують спіральні свердла і рідше спеціальні.
Спіральне свердло-двозубий (двулезвійний) ріжучий інструмент, що складається з двох основних частин: робочої і хвостовика.
Робоча частина свердла в свою чергу складається з циліндричної (калібруючої) і ріжучої частини. На циліндричній частині є дві гвинтові канавки, розташовані одна проти іншої. Їх призначення-відводити стружку з просвердлюваного отвору під час роботи свердла. Канавки на свердлах мають спеціальний профіль, що забезпечує правильне утворення ріжучих кромок свердла і необхідний простір для виходу стружки.
Форма канавки і кут нахилу ю (омега) між напрямком осі свердла і дотичній до стрічки повинні бути такими, щоб, не послаблюючи перетину зуба, забезпечувалося достатнє стружковий простір і легкий відвід стружки. Однак свердла (особливо малого діаметра) зі збільшенням кута нахилу гвинтової канавки послаблюються. Тому у свердел малого діаметра цей кут робиться менше, для свердел великих діаметрів - більше. Кут нахилу гвинтової канавки свердла становить 18-45°. Для свердління сталі користуються свердлами з кутом нахилу канавки 18 - 30°, для свердління крихких металів (латунь, бронза) - 22 - 25°, для свердління легких і в'язких металів - 40 - 45°, при обробці алюмінію, дюралюмінію і електрона-45°.
В залежності від напрямку гвинтових канавок спіральні свердла поділяють на праві (канавка спрямована по гвинтовій лінії з підйомом зліва направо, рух свердла під час роботи відбувається проти ходу годинникової стрілки) і ліві (канавка спрямована по гвинтовий лінії з підйомом справа наліво, рух відбувається по ходу годинникової стрілки). Ліві свердла застосовують рідко. Ліві і праві свердла відрізняються не тільки канавкою, а й напрямком обертання при роботі.
Розташовані уздовж гвинтових канавок свердла дві вузькі смужки на циліндричній поверхні свердла називають стрічками. Вони служать для зменшення тертя свердла об стінки отвору, направляють свердло в отвір і сприяють тому, щоб свердло не відводило в сторону. Свердла діаметром 0,25-0,5 мм виконуються без стрічок.
Зменшення тертя свердла об стінки просвердлюваного отвору досягається також тим, що робоча частина свердла має зворотний конус, тобто діаметр свердла у ріжучої частини більше, ніж на іншому кінці у хвостовика. Різниця цих діаметрів становить 0,03-0,12 мм на кожні 100 мм свердла. У свердел, оснащених пластинками з твердих сплавів, зворотна конусність застосовується від 0,03-0,15 мм на довжині пластинки.
Зуб-це виступаюча з нижнього кінця частина свердла, що має ріжучі кромки.
Зуб свердла має спинку, що представляє собою поглиблену частину зовнішньої поверхні зуба, і задню поверхню, що представляє собою торцеву поверхню зуба на ріжучої частини.
Поверхня канавки, що сприймає тиск стружки, називається передньою по-182. Геометричні параметри ріжучої частини спірального свердла. Лінія перетину передньої і задньої поверхонь утворює ріжучу кромку. Лінія, утворена перетином задніх поверхонь, являє поперечну кромку. Її величина залежить від діаметра свердла (в середньому 0,13 діаметра свердла).
Ріжучі кромки з'єднуються між собою на серцевині (серцевина - тіло робочої частини між канавками) короткою поперечною кромкою. Для більшої міцності свердла серцевина поступово потовщується від поперечної кромки і до кінця канавок (до хвостовика).
Переднім кутом у (гамма) називають кут укладений між поверхнею різання (обробленої поверхнею) і дотичній до передньої поверхні (або передньої грані).
Наявність переднього кута облітає врізання інструменту, стружка краще відділяється і отримує можливість природного сходу.
Зі збільшенням переднього кута поліпшуються умови роботи інструменту, зменшується зусилля різання, підвищується стійкість. Разом з тим послаблюється тіло ріжучої частини інструменту, яке може легко фарбуватися, ламатися; погіршується відведення теплоти, що призводить до швидкого нагрівання і втрати твердості. Тому для кожного інструменту прийняті певні значення переднього кута. Передні кути менше при обробці твердих і міцних матеріалів, а також при меншій міцності інструментальної сталі. В даному: випадку для зняття стружки потрібні великі зусилля і ріжуча частина інструменту повинна бути міцніше. При обробці м'яких, в'язких матеріалів передні кути беруться більше.
Задній кут а (альфа) - це кут нахилу задньої поверхні, утвореної дотичній до задньої поверхні (або задньої грані) і дотичній до оброблюваної поверхні. Задній кут дається для зменшення тертя задньої поверхні (або задньої грані) про оброблювану поверхню.
При занадто малих кутах а підвищується тертя, збільшується сила різання, інструмент сильно нагрівається, задня поверхня швидко зношується. При дуже великих задніх кутах послаблюється інструмент, погіршується відведення теплоти.
Передні і задні кути свердла в різних точках ріжучої кромки мають різну величину; для точок, розташованих ближче до зовнішньої поверхні свердла, передній кут більше і, навпаки, для точок, розташованих ближче до центру, передній кут менше. Якщо у периферії свердла (зовнішній діаметр) він має найбільшу величину (25 -30°), то в міру наближення до вершини свердла зменшується до величини, близької до нуля.
Як і передній, задній кут свердла змінюється за величиною для різних точок ріжучої кромки: для точок, розташованих ближче до зовнішньої поверхні свердла, задній кут менше, а для точок, розташованих ближче до центру, - більше.
Кут загострення р утворюється перетином передньої і задньої поверхонь.
Хвостовики у спіральних свердл можуть бути конічними і циліндричними. Конічні хвостовики мають свердла діаметром від 6 до 80 мм. Ці хвостовики утворюються конусом морзе. Свердла з циліндричними хвостовиками виготовляють діаметром до 20 мм хвостовик є продовженням робочої частини свердла.
Свердла з конічним хвостовиком встановлюють безпосередньо в отвір шпинделя верстата (або через перехідні втулки) і утримуються завдяки тертю між хвостовиком і стінками конічного отвору шпинделя. Свердла з циліндричним хвостовиком закріплюють в шпинделі верстата за допомогою спеціальних патронів. На кінці конічного хвостовика є лапка, що не дозволяє свердлу провертатися в шпинделі і служить упором при видаленні свердла з гнізда. У свердел зЦиліндричним хвостовиком є поводок, призначений для додаткової передачі крутного моменту свердлу від шпинделя.
Шийка свердла, що з'єднує робочу частину з хвостовиком, має менший діаметр, ніж діаметр робочої частини, служить для виходу абразивного кола в процесі шліфування, на ній позначена марка свердла і матеріал.
Спіральні свердла виготовляються з вуглецевої інструментальної сталі у10а, легованої сталі, хромокремністой 9хс, швидкорізальної р6м5.
Для виготовлення свердел все ширше застосовують металокерамічні тверді сплави марок вк6, вк8 і т15к6. Найбільш поширеним є спіральні свердла з, швидкорізальної сталі.
Свердла, оснащені пластинками з твердих сплавів, знаходять широке застосування при свердлінні і розсвердлюванні чавуну, загартованої сталі, пластмас, скла, мармуру та інших твердих матеріалів.
У порівнянні зі свердлами, виготовленими з інструментальних вуглецевих сталей, вони мають значно меншу довжину робочої частини, великий діаметр серцевини і менший кут нахилу гвинтової канавки. Ці свердла мають високу стійкість і забезпечують високу продуктивність праці.
Існує кілька типів свердел діаметром від 5 до 30 мм, оснащених твердими сплавами типу вк. Корпуси цих свердел виготовляються зі сталі марок р9, 9хс і 40х.
Свердла з гвинтовими канавками забезпечують значно кращий вихід стружки з отворів, особливо при свердлінні в'язких металів. Це досягається завдяки тому, що на довжині 1,5 -2 діаметра свердла канавка пряма, а далі до хвостової частини свердла гвинтова.
Свердла з прямими канавками застосовують при свердлінні отворів в крихких металах. Вони простіше у виготовленні, але для свердління глибоких отворів ці свердла застосовувати не можна, так як утруднюється вихід стружки з отвору.
Свердла з косими канавками застосовують для свердління неглибоких отворів, так як довжина канавок для виходу стружки у них дуже мала.
Свердла з отворами для підведення охолоджуючої рідини до ріжучих кромок свердла призначається для свердління глибоких отворів в несприятливих умовах. Ці свердла мають підвищену стійкість, так як охолоджуюча рідина, що подається під тиском 1-2 мпа (10 - 20 кгс/см2) в простір між зовнішньою поверхнею свердла і стінками отвору, забезпечує охолодження ріжучих крайок і полегшує видалення стружки.
Свердло кріплять в спеціальному патроні, що забезпечує підведення охолоджуючої рідини до отвору в хвостовій частині свердла. Ці свердла особливо ефективні при роботі з жароміцними матеріалами.
При свердлінні отворів свердлами з наскрізними каналами режим різання підвищується в 2 - 3 рази, а стійкість інструменту - в 5-6 разів. Свердління таким способом здійснюють на спеціальних верстатах в спеціальних патронах.
Твердосплавні монолітні свердла призначені для обробки жароміцних сталей. Ці типи свердел можуть бути застосовані для роботи на свердлильних машинах (матеріалом служить твердий сплав вк15м) і для роботи на токарних металорізальних верстатах (твердий сплав вк10м).
Корпусу твердосплавних свердел виготовляють зі сталі р6м5, 9хс, 40х, 45х.у свердлах прорізається паз під пластинку з твердого сплаву, яку закріплюють мідним або латунним припоєм.
Комбіновані свердла, наприклад свердло-зенковка, свердло-розгортка, свердло-мітчик, застосовують для одночасного свердління і зенкування, свердління і розгортання або свердління і нарізування різьблення.
Центрувальні свердла служать для отримання центрових отворів в різних заготовках. Їх виготовляють без запобіжного конуса і з запобіжним конусом.
Парові свердла найбільш прості у виготовленні, застосовуються для свердління невідповідальних отворів діаметром до 25 мм, головним чином при обробці твердих поковок і виливків, східчастих і фасонних отворів. Свердління, як правило, здійснюють тріскачками і ручними дрилями.
Ці свердла виготовляють з інструментальної вуглецевої сталі у10, у12, у10а і у12а, а найчастіше з швидкорізальної сталі р6м5.
Перове свердло має форму лопатки з хвостовиком. Його ріжуча частина-трикутної форми з кутами при вершині 2 ф =118-н 120° і заднім кутом а = 10 ~ 20°.
Перові свердла поділяють на двосторонні і односторонні, найбільш поширеними є двосторонні. Кут заточування одностороннього перового свердла приймається зі сталі в межах 75 - 90°, а для кольорових металів - 45-60° . Кут заточування двостороннього перового свердла приймається 120-135°.
Перові свердла не допускають високих швидкостей різання і непридатні для свердління великих отворів, так як стружка з отвору не відводиться, а обертається разом зі свердлом і дряпає поверхню отвору. Крім того, в процесі роботи свердло швидко тупиться, зношується, втрачає ріжучі якості і йде в сторону від осі отвору.
Свердління є одним з найпоширеніших методів отримання отвору різанням. Ріжучим інструментом тут служить свердло, яке дає можливість як отримувати отвори в суцільному матеріалі (свердління), так і збільшувати діаметр вже просвердленого отвору (розсвердлювання).
При свердлінні оброблювану деталь закріплюють на столі свердлильного верстата прихватами, в лещатах, на призмах і т. П., а зверху повідомляють два спільних руху-обертальний і поступальний (спрямоване уздовж осі свердла). Обертальний рух називається головним (робочим) рухом. Поступальний рух уздовж осі свердла називається рухом подачі.
Свердління застосовується при виконанні багатьох слюсарних робіт. Воно виконується на приводних свердлильних верстатах і вручну-ручними дрилями, за допомогою механізованого інструменту - електричними і пневматичними дрилями, а також електроіскровим і ультразвуковим методами.
Свердла, їх конструкція і призначення. За конструкцією і призначенням свердла поділяються на ряд видів.
Перові свердла являють собою простий ріжучий інструмент (). Вони застосовуються головним чином в тріскачках і ручних дрилях для свердління невідповідальних отворів діаметром до 25 мм.
Спіральні свердла з циліндричним і конічним хвостовиками ) використовуються як для ручного свердління, так і при роботі на верстатах (свердлильних, револьверних та ін.).
Свердла для глибокого свердління застосовуються на спеціальних верстатах для отримання точних отворів малого діаметра. Під глибоким свердлінням зазвичай розуміють свердління отворів, довжина яких перевищує їх діаметр в 5 разів і більше.
Центрові свердла служать для отримання центрових поглиблень на оброблюваних деталях.
Комбіновані свердла дозволяють проводити одночасну обробку одновісних отворів, а також одночасне свердління і зенковання або розгортання отворів (
Для виготовлення свердел, як правило, застосовують такі інструментальні матеріали: вуглецеву інструментальну сталь марок у10а і у12а, леговані сталі - хромистую марку x і хромокремнієву-просту -9хс; швидкорізальну сталь марок р9 і р18. В останні роки для цієї мети знаходять застосування також металокерамічні тверді сплави вк6, вк8 і т15к6.
Свердла з швидкорізальних сталей роблять зварними: робочу частину - з швидкорізальної сталі, а іншу частину - з менш дорогої конструкційної сталі. Найбільш поширеними є спіральні свердла з швидкорізальних сталей.
Елементи та геометричні параметри спірального свердла. Спіральне свердло має робочу частину, шийку, хвостовик для кріплення свердла в шпинделі верстата і лапку, що служить упором при вибиванні свердла з гнізда шпинделя (рис. 2, а). Робоча частина в свою чергу розділяється на ріжучу і направляючу.
Ріжуча частина, на якій розташовані всі ріжучі елементи свердла, складається: з двох зубів( пір'я), утворених двома спіральними канавками для відводу стружки (рис. 2, б); перемички(серцевини) - середній частині свердла, що з'єднує обидва зуба '(пера); двох передніх поверхонь, по яких збігає стружка, і двох задніх поверхонь; двох стрічок, службовців для направлення свердла, калібрування отвору і зменшення тертя свердла об стінки отвору; двох головних ріжучих крайок, утворених перетином передніх і задніх поверхонь і виконують основну роботу різання; поперечної кромки (перемички), утвореної перетином обох задніхПоверхня. На зовнішній поверхні свердла між краєм стрічки і канавкою розташована йде по гвинтовий лінії кілька поглиблена частина, звана спинкою зуба.
Зменшення тертя свердла об стінки просвердлюваного отвору досягається також тим, що робоча частина свердла має зворотний конус, тобто. Діаметр свердла у ріжучої частини більше, ніж на іншому кінці, у хвостовика. Різниця у величині цих діаметрів становить 0,03-0,12 мм на кожні 100 мм довжини свердла.
У свердел, оснащених пластинками твердих сплавів, зворотна конусність приймається від 0,1 до 0,03 мм на кожні 100 мм довжини.
До геометричних параметрів ріжучої частини свердла (рис. 109, в, г, д) відносяться: кут при вершині свердла, кут нахилу гвинтової канавки, передній і задній кути, кут наклойа поперечної кромки (перемички).
Кут при вершині свердел а 2ф розташований між головними ріжучими крайками. Він має великий вплив на роботу свердла. Величина цього кута вибирається в залежності від твердості оброблюваного матеріалу і коливається в межах від 80 до 140°. Для сталей, чавунів і твердих бронз 2<р= 116-м 18°; для ла-туней і м'яких бронз 2ф=130°; для легких сплавів - дуралюміну, силуміну, електрона і бабіту 2ф=140°; для міді 2ф=125°; для ебоніту і целулоїду 2ф = 80-до 90°.
Для підвищення стійкості свердел діаметром 12 мм і вище застосовують подвійну заточку свердел; при цьому головні ріжучі кромки мають форму не прямий, як при звичайній заточуванні (рис. 3, в), а ламаної лінії (рис. 109, г). Основний кут 2ф= 116-4-118° (для сталей і чавунів), а другий кут 2ф=70-г-75°.
Кут нахилу гвинтової канавки позначається грецькою літерою омега. Зі збільшенням цього кута процес різання полегшується і поліпшується вихід стружки. Однак свердло (особливо малого діаметра) зі збільшенням кута нахилу гвинтової канавки послаблюється. Тому у свердел малого діаметра цей кут робиться меншим, ніж у свердел великого діаметру.
Кут нахилу гвинтової канавки повинен вибиратися в залежності від властивостей оброблюваного металу. Для обробки, наприклад, червоної міді та алюмінію цей кут потрібно брати рівним 35-40°, а для обробки сталі (о = 25° і менше.
Якщо розсікти спіральне свердло площиною, перпендикулярній головній ріжучої кромці, то ми побачимо передній кут
Передній кут у (гамма) в різних точках ріжучої кромки має різну величину: він більше у периферії свердла і помітно менше у його осі. Так, якщо у зовнішнього діаметра передній кут у = 25 г 30°, то у перемички він близький до 0°. Мінливість величини переднього кута відноситься до недоліків спірального свердла і є однією з причин нерівномірного і швидкого його зносу.
Задній кут свердла а (альфа) передбачений для зменшення тертя задньої поверхні об поверхню різання. Цей кут розглядається в площині аа, паралельної осі свердла. Величина заднього кута також змінюється у напрямку від периферії до центру свердла; у периферії він дорівнює 8-и2″, а у осі а = 20н-26°.
Свердла, оснащені пластинками твердих сплавів, в порівнянні зі свердлами, виготовленими зі сталей, мають меншу довжину робочої частини, більший діаметр серцевини і менший кут нахилу гвинтової канавки. Ці свердла мають високу стійкість і забезпечують більш високу продуктивність. Особливо ефективне застосування свердел з пластинками твердих сплавів при свердлінні і розсвердлюванні чавуну, твердої сталі, пластмас, скла, мармуру та інших твердих матеріалів.
Свердла, оснащені пластинками твердих сплавів, випускаються чотирьох типів: спіральні з циліндричним хвостовиком; спіральні з конічним хвостовиком; з прямими канавками і конічним хвостовиком і з косими канавками і циліндричним хвостовиком.
Процес різання при свердлінні. В процесі свердління під впливом сили різання ріжучі поверхні свердла стискають прилеглі до них частинки металу, і коли тиск, створюване свердлом, перевищує сили зчеплення частинок металу, відбувається утворення елементів стружки і відділення її.
При свердлінні в'язких металів (сталь, мідь, алюміній та ін.) окремі елементи стружки, щільно зчіплюючись між собою, утворюють безперервну стружку, завивається в спіраль. Така стружка називається зливний. Якщо оброблюваний метал крихкий, наприклад чавун або бронза, то окремі елементи стружки надламуються і відокремлюються один від одного. Така стружка, що складається з окремих роз'єднаних між
Собою елементів (лусочок) неправильної форми, носить назву стружки надлому.
В процесі свердління розрізняють наступні елементи різання: швидкість різання, глибина різання, подача, товщина і ширина стружки.
Головний робочий рух свердла (обертальний) характеризується швидкістю "різання.
Подачею при свердлінні називається переміщення свердла уздовж осі за одйн його оберт. Вона позначається через s і вимірюється в мм / об. Свердло має дві головні ріжучі кромки.
Правильний вибір подачі має велике значення для збільшення стійкості інструменту. Величина подачі при свердлінні і розсвердлюванні залежить від заданої частоти і точності обробки, твердості оброблюваного матеріалу, міцності свердла і жорсткості системи верстат - інструмент - деталь.
Товщина зрізу (стружки) а вимірюється в напрямку, перпендикулярному ріжучої кромці свердла. Ширина зрізу ь вимірюється уздовж ріжучої кромки і дорівнює її довжині.
Таким чином, площа поперечного перерізу стружки стає більше зі збільшенням діаметра свердла, а для даного свердла - зі збільшенням подачі.
Оброблюваний матеріал чинить опір різанню і видаленню стружки. Для здійснення процесу різання до інструменту повинні бути прикладені сила подачі ро, що перевершує сили опору матеріалу осьовому переміщенню свердла, і крутний момент мкр, необхідний для подолання моменту опору м і для забезпечення головного обертального руху шпинделя і свердла.
Сила подачі р0 при свердлінні і крутний момент залежать від діаметра свердла d, величини подачі і властивостей оброблюваного матеріалу. Наприклад, при збільшенні діаметра свердла і подачі вони також збільшуються.
Стійкістю свердла називається час його безперервної (машинної) роботи до затуплення, тобто між двома переточками. Стійкість свердла зазвичай вимірюється в хвилинах.
В процесі різання при свердлінні виділяється велика кількість тепла внаслідок деформації металу, тертя виходить по канавках свердла стружки, тертя задньої поверхні свердла про оброблювану поверхню і т.п. Основна частина тепла несеться стружкою, а інша розподіляється між деталлю і інструментом. Для запобігання від затуплення і передчасного зносу при нагріванні свердла в процесі різання застосовують змащувально-охолоджуючу рідину, яка відводить тепло від стружки, деталі та інструменту.
До охолодних рідин, якими користуються при свердлінні металу, відносяться мильна і содова вода, масляні емульсії та ін.
Вибір режимів різання при свердлінні полягає у визначенні такої подачі і швидкості різання, при яких процес свердління деталі виявляється найбільш продуктивним і економічним.
Теоретичний розрахунок елементів режиму різання проводиться за нормативами, що діють на заводі, або за довідниками в наступному порядку: вибирають подачу, потім підраховують швидкість різання і по знайденій швидкості різання встановлюють число обертів свердла. Потім вибрані елементи режиму різання перевіряють по міцності слабкої ланки механізму головного руху і потужності електродвигуна верстата.
Зазвичай у виробничих умовах при виборі елементів режиму різання, свердління, зенкерування, розгортання і т.д. Користуються готовими даними технологічних карт.
Знос і заточка свердел. Знос свердел з швидкорізальної сталі відбувається по задній поверхні, стрічках і кутах, а іноді і по передній поверхні.
Задня поверхня свердла зношується в результаті тертя об поверхню різання, передня - в результаті тертя об утворену стружку. Затупившееся свердло в процесі роботи видає характерний скрипучий звук, який свідчить про необхідність направити свердло в переточку.
Форма заточування впливає на стійкість свердла і швидкість різання, що допускається свердлом. Розрізняють такі форми заточування свердел: нормальну одинарну і подвійну заточку, заточку з підточуванням перемички, з підточуванням стрічки і ін. (
Підточка перемички полягає в утворенні додаткових виїмок у вершини свердла з обох сторін уздовж його осі на довжині 3-15 мм, після чого довжина перемички скорочується до 0,1 d. При цьомуЗначно зменшується сила подачі р0, а стійкість свердла збільшується в 1,5 рази.
Багато новаторів виробництва працюють над вдосконаленням конструкції свердел з метою підвищення їх стійкості.
Заточка свердел виконується в заточувальних майстернях фахівцями-заточниками на спеціальних верстатах.
У ряді випадків заточку свердел виробляють на простих заточувальних верстатах (точилах), обладнаних спеціальним пристосуванням. При заточуванні вручну свердло тримають лівою рукою можливо ближче до ріжучої частини (конусу), а правою рукою - за хвостовик. Притискаючи ріжучу кромку свердла до бічної поверхні заточувального кола, плавним рухом правої руки похитують свердло, домагаючись, щоб його задня поверхня отримала правильний нахил і прийняла належну форму. Знімати треба невеликі шари металу при слабкому натиску свердлом на коло.
Необхідно стежити за тим, щоб ріжучі кромки мали однакову довжину і були заточені під однаковими кутами. Свердло з ріжучими крайками різної довжини або з різними кутами нахилу може зламатися або просвердлити отвір більшого діаметру. Після заточування задньої поверхні свердла його головні ріжучі кромки повинні бути прямолінійними.
Правильність заточування свердел перевіряють спеціальним шаблоном.
Свердлінням називається утворення зняттям стружки отворів в суцільному матеріалі за допомогою ріжучого інструменту - свердла . Свердління застосовують для отримання отворів не високого ступеня точності, і для отримання отворів під нарізування різьблення, зенкерування і розгортання.
Свердління застосовується:
Для отримання невідповідальних отворів невисокого ступеня точності і значної шорсткості, наприклад під кріпильні болти, заклепки, шпильки і т. Д.;
Для отримання отворів під нарізування різьблення, розгортання і зенкерування.
Свердління можна отримати отвір з точністю по 10 - му, в окремих випадках-по 11-му квалітету і шорсткістю поверхні rz 320...80.
Свердла бувають різних видів і виготовляються з швидкорізальних, легованих і вуглецевих сталей, а також оснащуються пластинками з твердих сплавів.
Свердло має дві ріжучих кромки. Для обробки металів різної твердості, застосовують свердла з різним кутом нахилу гвинтової канавки. Для свердління стали користуються свердлами з кутом нахилу канавки 18 ... 30 градусів, для свердління легких і в'язких металів - 40...45 градусів, при обробки алюмінію, дюралюмінію і електрона - 45 градусів.
Хвостовики у спіральних свердел можуть бути конічними і циліндричними. Конічні хвостовики мають свердла діаметром 6 ... 80мм. Ці хвостовики утворюються конусом морзе.
Шийка свердла, що з'єднує робочу частину з хвостовиком, має менший діаметр, ніж діаметр робочої частини.
Свердла бувають оснащені пластинками з твердих сплавів, з гвинтовими, прямими і косими канавками, а також з отворами для підведення охолоджуючої рідини, твердосплавних монолітів, комбінованих, центрувальних і перових свердел. Ці свердла виготовляють з інструментальних вуглецевих сталей у10, у12, у10а і у12а, а частіше - з швидкорізальної сталі р6м5.
Щоб підвищити стійкість ріжучого інструменту і отримати чисту поверхню отвору, при свердлінні металів і сплавів користуються охолоджуючою рідиною
Просвердлюваний матеріал
Алюміній
Мильна емульсія або обробка всуху
Дюралюміній
Мильна емульсія або суміш спирту зі скипидаром
Технологія свердління отворів включає в себе такі операції:
1. Накернювання місць свердління отворів
2. Вибір обладнання і інструменту
3. Просведлювання отворів
Тема: Нарізання різьби
Як нарізати зовнішню різьбу
Нарізанням різьби називається утворення гвинтової поверхні шляхом зняття стружки чи пластичним деформуванням на зовнішніх або внутрішніх циліндричних і конічних поверхнях.
Нарізання зовнішньої і внутрішньої різьби відбувається за однаковим принципом, відрізняються ці процеси інструментом, який для цього використовують. Зовнішню різьбу нарізають за допомогою плашок, а внутрішню - мітчиком.
Плашка - інструмент, виготовлений із загартованої сталі, для нарізання зовнішньої різьби трикутного профілю вручну або на токарному верстаті (Плашка схожа на гайку із просвердленими отворами.
Плашки бувають суцільні, розрізні (мають проріз 0,5-1,5 мм) та розсувні, а за формою - круглі, квадратні, шестигранні, призматичні. Суцільними плашками можна нарізати різьбу тільки одного діаметра, а розрізними можна дещо регулювати діаметр різьби
Круглі плашки закріплюють у плашкотримачах ( за допомогою гвинтів, розташованих по колу воротка. Цими гвинтами також регулюють розмір діаметра розрізних плашок.
Послідовність нарізання зовнішньої різьби
1. Визначтеся з параметрами різьби (діаметр, крок, довжина частини нарізування). Доберіть інструмент.
2. Виберіть стрижень для нарізання різьби і відмітьте на ньому частину, яка має нарізуватися.
3. Зафіксуйте стрижень вертикально в лещатах так, щоб кінець, який виступає, був на 20-25 мм довший за частину, яка нарізуватиметься. Зробіть фаску на кінці стрижня і змастіть його мастилом.
Поверхня стрижнів під різьбу має бути чистою. Плашка швидко зношується, якщо стрижні вкриті іржею.
Пам'ятайте:
- різьбу може зіпсувати найменше перекошення інструмента;
- у процесі нарізання різьби треба уникати різких рухів, повертати плашку плавно;
- слід регулярно знімати щіткою мета лічну стружку, що утворюється під час роботи;
- якщо сталося перекошення, то зовнішню різьбу ще можна перенарізати (а внутрішню - ні).
4. Виберіть відповідну плашку і закріпіть її гвинтами у плашкотримачі (маркування має бути зверху, а заглиблення - навпроти стопорних гвинтів; закріпіть плашку). Накладіть стрижень і вріжте плашку в стрижень.
5. Наріжте різьбу, обертаючи плашкотримач за ручки: трохи натискаючи на плашку, робіть по 1-2 оберти (у напрямку нарізання) і півоберту назад; натискайте на плашку у процесі роботи доти, доки вона сама не піде по різьбі.
6. Згвинтіть і зніміть зі стрижня плашку.
7. Протріть різьбу чистою ганчіркою.
8. Перевірте різьбу гайкою.
Діаметр нарізаної різьби вимірюють штангенциркулем, а для визначення кроку різьби використовують різьбомір. Діаметр стрижня для нарізання різьби визначають за таблицею. Найкращою різьбою є та, коли діаметр стрижня на 0,3-0,4 мм менший від зовнішнього діаметра різьби.
Як нарізати внутрішню різьбу (в отворі)
Внутрішню різьбу, тобто різьбу в отворі, нарізають за допомогою мітчиків. Мітчик схожий на гвинт із повздовжніми канавками. Встановлюється у вороток.
Хвостовик призначений для закріплення мітчика у воротку, на ньому вказане маркування по діаметру. Робоча частина складається із забірної і калібрувальної. Забірна - це конусоподібна частина мітчика, яка виконує основну роботу, а калібрувальна - зачищає і калібрує. Канавки призначені для формування різців і виведення стружки
Для нарізання внутрішньої різьби потрібно прикласти значні зусилля. Щоб полегшити роботу і отримати чистішу різьбу, мітчики для ручної обробки металу випускають у комплекті: чорновий, середній і чистовий (і наносять на них відповідно 1,2,3 риски чи кільця). Вони відрізняються глибиною прорізування канавок різьби й формою зубця (у чорнового - трапецієподібний; у середнього - трикутник із закругленою вершиною; у чистового - трикутник з гострою вершиною
Для надійного кріплення мітчиків під час роботи потрібен вороток - тримач мітчика
Щоб зменшити нагрівання і отримати чистішу різьбу, використовують змащувально-охолоджувальні рідини - їх вибирають залежно від матеріалу деталі.
Якщо використовують електродриль, то заготовку треба затиснути в лещата. Свердло має бути направлене вертикально відносно заготовки. Щоб свердло при врізанні в заготовку на початку свердління не відвело вбік, центр майбутнього отвору треба накернити. Спочатку свердлять, лише злегка натискаючи на руків'я свердлильної стійки. Коли свердло врізалося в матеріал і з'явилася чиста стружка, натискання можна посилити. Якщо в товстих заготовках треба отримати отвори діаметром понад 5 мм, попередньо використовують тонше свердло, а потім розсвердлюють до необхідного діаметра.
При свердлінні отворів у металевих заготовках, особливо з твердих металів, свердло в результаті тертя сильно нагрівається і може втратити свої різальні властивості через зниження твердості. Щоб тертя зменшити, свердло змащують. Від перегрівання його захищають охолоджувальними рідинами. Для одночасного змащення й охолодження свердел застосовують комбіновані мастильно-охолоджувальні рідини.
Після свердління отвір треба обов'язково очистити від стружки.
Отже, перш ніж нарізати різьбу в отворі, треба визначити:
- діаметр різьбової частини гвинта, який буде вкручуватися;
- діаметр мітчика;
- діаметр отвору для нарізання різьби.
Діаметр отвору залежить від матеріалу деталі й інструмента, яким нарізується різьба. При нарізанні мітчиками матеріал деталі видавлюється в різному ступені в різних металів. Якщо просвердлити отвір точно по внутрішньому діаметру різьби, то метал, який видавлюється, защемить інструмент, і мітчик зламається.
- Метали тверді і крихкі дають менші зміни величини отвору, ніж м'які й в'язкі.
- Якщо діаметр внутрішнього отвору замалий, мітчик буде працювати зі значним напруженням і може вийти з ладу.
- Якщо діаметр отвору під різьбу завеликий, профіль нарізаної різьби буде неповним, що знизить надійність з'єднання.
Послідовність дій під час нарізання внутрішньої різьби
- 1. Просвердліть отвір потрібного діаметра.
- 2. Металеву заготовку з отвором закріпіть у струбцині перпендикулярно до площини лещат.
- 3. Перевірте надійність закріплення заготовки.
- 4. На хвостовик чорнового мітчика надіньте вороток.
- 5. Робочу частину мітчика змастіть мастилом.
- 6. Вертикально без перекосу встановіть мітчик в отвір, кутником перевірте правильність положення мітчика
- 7. Плавно поверніть вороток за годинниковою стрілкою на 1-2 оберти стежачи за тим, щоб вісь обертання мітчика збігалася з віссю отвору.
- 8. Щойно мітчик вріжеться в метал і встановиться, візьміть вороток обома руками і обертайте його, злегка натискаючи, за таким правилом: 1-2 оберти за годинниковою стрілкою і півоберта проти годинникової стрілки (
- 9. Замініть чорновий мітчик на середній і повторіть нарізування різьби.
- 10. Доведіть різьбу до кінця чистовим мітчиком.
- 11. Вигвинтіть мітчик і зніміть з нього вороток.
- 12. Перевірте внутрішню різьбу шпилькою або болтом
Проганяючи по різьбі другий і третій мітчики, треба їх щоразу змащувати. Середній і чистовий мітчики рекомендують вводити в отвір без воротка, і, лише переконавшись, що вони пішли по різьбі й почали обертатися, надіти на квадрат хвостовика вороток і нарізати. Через кожні три оберти воротка треба перевіряти його вертикальність кутником.
Правила роботи з мітчиком
- Під час нарізання різьби мітчик треба змащувати мастилом.
- Зауважте, що мітчик легко ламається - він виготовлений з високотвердої крихкої інструментальної сталі.
- Тримайте мітчик рівно, інакше можливе його перекошування чи поломка мітчика (правильність встановлення контролюйте кутником).
- Якщо мітчик обертається туго, вигвинтіть його і з'ясуйте причину (можливо, замалий діаметр отвору, чи отвір забився стружкою, чи мітчик затуплений).
- Обертайте мітчик плавно, не допускаючи різких рухів.
- Якомога частіше знімайте щіткою металеві ошурки.
Правила безпечної праці під час нарізання різьби
- 1. Не допускайте перекошування мітчика, особливо обережно нарізайте різьбу в дрібних отворах.
- 2. Своєчасно змащуйте інструмент мастилом.
- 3. Надійно закріплюйте плашку і мітчик у тримачах.
- 4. Не чіпайте руками гребінці нарізаної різьби - можна поранитися їхніми гострими і рваними краями.
- 5. Очищаючи інструмент, користуйтеся щіткою, щоб уникнути потрапляння стружки в очі і травмування рук.
- 6. Зламаний мітчик не можна видаляти з отвору ударами: скалки загартованого мітчика можуть травмувати.
Тема: Клепання
Суть клепання та його застосування
У конструкціях промислових установок, машин і механізмів слюсареві доводиться зустрічатися з різними видами з'єднання деталей.
Усі з'єднання деталей машин можна поділити на дві групи: рухомі і нерухомі; останні можуть бути рознімними і нерознім- ними.
Рознімними вважаються такі з'єднання, при яких створюється можливість легко і без пошкоджень роз'єднувати деталі. В основному це з'єднання за допомогою гвинтів, болтів, шпонок тощо.
Нерознімними називаються з'єднання, які можна роз'єднати, тільки зруйнувавши елементи з'єднань. До нерознім- них належать з'єднання, зроблені клепанням, зварюванням, паянням та склеюванням.
У сучасному машинобудуванні клепання в значній кількості випадків замінене на більш продуктивне електрозварювання. Однак у ряді галузей машинобудування його ще застосовують.
Клепанням називається операція одержання нерознім- них з'єднань за допомогою заклепок різної форми і розмірів. Клепання поділяється на холодне, гаряче і мішане.
Холодне клепання виконується заклепками діаметром до 10 мм без розігрівання замикаючої головки. При клепанні в холодному стані діаметр отвору під заклепку беруть на
1-0,2 мм більший від діаметра заклепки.
Гаряче клепання виконується заклепками діаметром понад 10 мм, нагрітими до певної температури. У цьому випадку заклепки слід вибирати діаметром, на 0,5-1 мм меншим від діаметра отвору. При клепанні в
нагрітому стані стержень заклепки краще заповнює отвір у склепуваних деталях, а при охолодженні заклепка краще стягує склепані деталі.
Мішане клепання застосовують при встановленні довгих заклепок, коли нагрівають не весь стержень, а тільки його кінцеву частину, з якої висаджується замикаюча головка.
Клепання називається звичайним, якщо обидві головки заклепки знаходяться над поверхнями склепаних деталей, і п о- т а й н и м, коли головки заклепки розміщені врівень з поверхнями склепаних деталей. Клепання можна виконувати вручну за допомогою механізованого інструменту і на спеціальних пресах та машинах.
Заклепочні з'єднання
Щоб зробити не роз'ємне з'єднання металевих заготовок або деталей, застосовують заклепочне з'єднання за допомогою одного або кількох рядів заклепок. Місце з'єднання склепуваних частин називається заклепочним швом.
Заклепка - це циліндричний стержень з двома головками, які і роблять з'єднання деталей не роз'ємним.
За призначенням заклепочні з'єднання поділяються на міцні (для різних металевих конструкцій), щільні (для виготовлення резервуарів, що працюють під невеликим тиском) і міцнощільні (для виготовлення парових котлів або інших резервуарів, які працюють під великим тиском). Щільні шви не дуже міцні, але рідин і газів не пропускають.
Металеві листи або деталі з'єднують заклепочними швами кількома способами: встик (з однією або з двома накладками) і внапустку. Якщо склепувані листи покласти краями впритул, вздовж стику покласти з одного боку смужку-накладку і приклепати до неї кожний з листів, то це буде шов встик з однією накладкою. Коли ж з'єднувані листи накладають кінцями один на один і склепують їх - це буде шов внапустку. За кількістю рядків заклепок в кожному з основних швів заклепочні з'єднання поділяються на однорядні і дворядні. Щоб надати заклепочним швам міцності, провадять їх чеканку або обварюють.
Клепання поділяється на три основних види: холодне, гаряче та змішане. При з'єднанні деталей заклепками діаметром до 8 мм застосовують холодне клепання. При застосуванні заклепок діаметром більше 8 мм провадять гаряче клепання. В цьому разі заклепку нагрівають до такої температури, щоб під ударами молотка або пневматичного інструмента з стержня заклепки можна було утворити замикаючу головку.
Змішане клепання застосовують тоді, коли треба склепати заготовки або деталі значної товщини. При цьому нагрівають не всю заклепку, а лише її кінцеву частину, з якої дістають замикаючу головку.
Техніка клепання
Деталі, які треба з'єднати за допомогою заклепочного з'єднання, накладають одну на одну так, щоб вісь одного отвору збігалася з віссю другого отвору. В ці отвори закладають заклепку (рис. 240).Елементи заклепки
Обидві частини деталі, які з'єднують, щільно притискують одну до одної так, щоб між головкою заклепки і матеріалом деталі не було зазора. Це роблять спеціальним інструментом - натягачем.
Після цього молотком наносять часті удари, по стержню заклепки, що виступає над поверхнею деталі так, щоб з нього утворилася друга головка заклепки, яка міцно з'єднує обидві деталі між собою.
Щоб надати утвореній головці потрібної форми і щільніше з'єднати деталі між собою, застосовують спеціальний інструмент - обтискач. Обтискач встановлюють на утворену головку заклепки і роблять удари доти, доки головка набере правильної сферичної форми.
В залежності від того, як буде розташована головка заклепки, заклепочні з'єднання поділяються на звичайні і внутрішні.
Звичайні заклепочні з'єднання це такі, в яких головки заклепок виступають над поверхнею заготовки або деталі.
Якщо головки заклепок не виступають над поверхнею деталі, а сховані в товщі матеріалу, тобто є потайними, таке з'єднання називають внутрішнім.
Шви заклепочних з'єднань
В заклепочному з'єднанні заклепки розташовуються в шахмат- ному порядку або паралельними рядами Треба додержувати встановлених норм розташування заклепок, тобто відстані між ними і відстані від центра заклепки до кінця кромки листів, які з'єднують. Так, для однорядних швів шаг заклепки (відстань між центрами двох сусідніх заклепок) повинен дорівнювати трьом діаметрам заклепки, а відстань від центра першої заклепки до кромки листа повинна бути не менше 1,5 діаметра заклепки. Якщо отвори під заклепки пробивають під пресом і в металі виникають внутрішні напруження, відстань від центра першої заклепки до кромки листа повинна бути не менше 2,5 діаметрів заклепки.Заклепочні шви
У дворядному заклепочному з'єднанні шаг заклепок становитиме 4 діаметри заклепки, а відстань між рядами повинна бути не менше 2 діаметрів.
Тема; Перевірка справності слюсарного інструменту
1. Ударна частина молотка, зубила не повинна мати заусениць
2. Молоток повинен бути надійно посаджений на рукоятку і надійно зафіксований
3 Кут заточки свердла , робочої частини зубила перевіряють з допомогою шаблона
4 Робоча частина зубила не повинна мати сколів, тріщин, вмятин
5 Робоча поверхня напилка повинна бути сухою , не мати слідів корозії
6. Напилок повинен надійно зафіксований на рукоятці
7 Різьбонарізний інструмент повинен бути надійно зафіксований у тримачах
8.Блискуча поверхня напилка , надфіля свідчить про те, що він тупий
9. Гострі і правильно відрегульовані ручні ножниці по металу легко ріжуть папір
10 При використанні електроінструменту перевірити стан ізоляції електропроводів, наявність захисних пристроїв, заземлення , відсутність іскріння між обертовими частинами електродвигунів і щіток