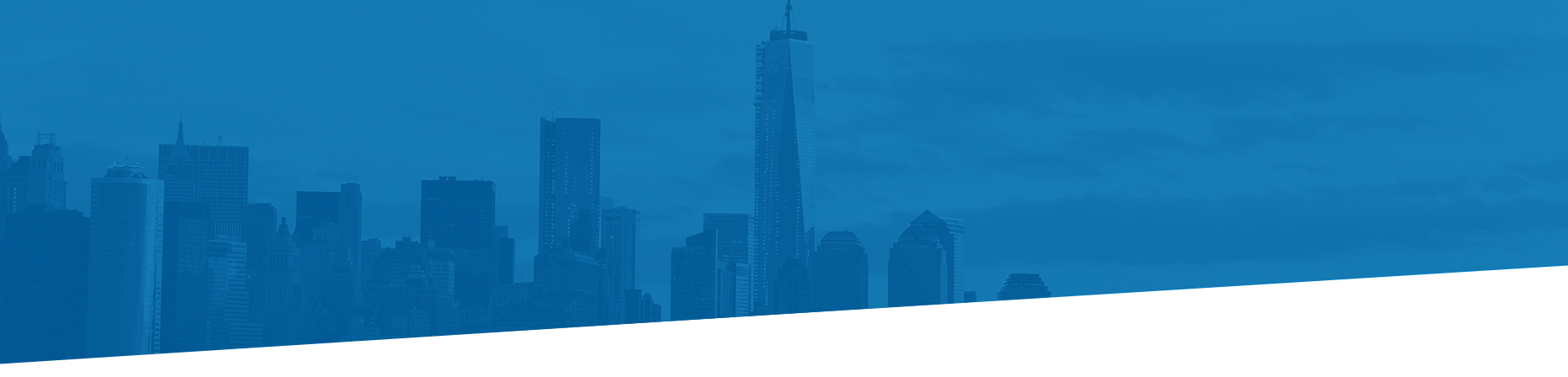
ДОПУСКИ І ТЕХНІЧНІ ВИМІРИ
Тема: Загальні відомості
Учбові питання
1. Стандартизація і взаємозамінність
2.Розміри деталі 3. Відхилення розмірів деталі
4. Допуск розміру
5. Види посадок
6.Графічне зображення полів допусків та посадок
7.Відхилення від вірної форми
8.Точність обробки
1.
Взаємозамі́нність — придатність об'єкта (машини, приладу, механізму, деталі тощо) до використання замість іншого без змінення для виконання однакових вимог[1] при складанні, ремонті чи заміні.
Ідея взаємозамінності визрівала в головах багатьох інженерів і винахідників розвинених країн Європи і Америки. Першими з них у другій половині XVIII століття були: американський винахідник Елі Вітні, тульські зброярі та французький інженер Леблан[2].
Види взаємозамінності за ступенем забезпечення точності
Повна взаємозамінність
Повністю взаємозамінними називаються деталі і вузли, що встановлюються при складанні без додаткових операцій по обробці, без регулювання та підбору.
Повна взаємозамінність можлива тільки коли розміри, форма, механічні, електричні й інші якісні і кількісні характеристики деталей і складальних одиниць після виготовлення знаходяться в заданих межах і зібрані вироби задовольняють технічним вимогам.
При повній взаємозамінності спрощується процес складання, а також ремонт виробів, тому що будь-яка зношена чи поламана деталь або складальна одиниця може бути замінена новою (запасною). Повну взаємозамінність економічно доцільно застосовувати для деталей, виготовлених з допусками квалітетів не вище 6-го.
Неповна взаємозамінність
Іноді для задоволення експлуатаційних вимог необхідно виготовляти деталі і складальні одиниці з економічно не прийнятими чи технологічно важко досяжними допусками. Такий випадок називають неповною (обмеженою) взаємозамінністю.
У разі неповної взаємозамінності для одержання необхідної точності складання застосовують:
- груповий підбір деталей (селективне складання) — метод складання машин і механізмів, при якому здійснюють відповідний підбір деталей, що працюють у парі. Деталі, які поступають на складання сортують за розмірними групами, всередині яких деталі, що сполучаються (охоплювана і охоплювальна) мають найсприятливіші для з'єднання дійсні розміри;
- регулювання положення деяких частин виробів — необхідні характеристики досягаються регулюванням спеціального елемента шляхом зміни місця, положення або введення додаткового елементу;
- припасування деталей — для досягнення заданих властивостей конструкції змінюють параметри елемента (заздалегідь призначеного), до необхідних значень для успішного збирання.
Види взаємозамінності по відношенню до об'єкта
По відношенню до об'єкта розрізняють взаємозамінність зовнішню і внутрішню.
Зовнішня взаємозамінність — це взаємозамінність покупного виробу:
- розмірна — мається на увазі взаємозамінність за розмірами і формою приєднувальних поверхонь;
- параметрична — мається на увазі взаємозамінність виробу за експлуатаційними показниками.
Наприклад, в електродвигунах зовнішню взаємозамінність забезпечують за розмірами приєднувальних поверхонь (розмірна), а також, за частотою обертання вала і потужністю (параметрична).
Внутрішня взаємозамінність поширюється на деталь, складальні одиниці і механізми, що входять в об'єкт. Наприклад, кулькові підшипники мають повну зовнішню взаємозамінність, оскільки за своїм призначенням і монтажними розмірами взаємозамінні, але разом з тим окремі їхні частини (внутрішні і зовнішні кільця, кульки) не взаємозамінні між собою, оскільки подаються на складання тільки селективно підібраними комплектами, тобто не мають внутрішньої взаємозамінності (окремі частини кулькового чи роликового підшипників не взаємозамінні).
Роль взаємозамінності
Основні переваги здійснення принципу взаємозамінності у сфері виробництва, експлуатації і ремонту полягають у наступному:
- Спрощуються, прискорюються і здешевлюються проєктно-конструкторські роботи із створення нових машин і механізмів, оскільки конфігурація, точність і технічні вимоги до основних елементів стандартизовані (різі, шліци, зубчасті передачі, шпонки, підшипники тощо).
- Завдяки відсутності припасувальних робіт і обробки по місцю складання машин значно спрощується і створюється певний ритм складального процесу, що дає можливість підвищити продуктивність складальних робіт шляхом організації конвеєрного потокового виробництва.
- Спрощується і здешевлюється виготовлення машини в результаті регламентації точності заготовок на всіх стадіях механічної обробки, застосування досконаліших методів контролю і здешевлення складання. Якість продукції стає стабільною, підвищується її надійність.
- Незалежне виготовлення деталей машин створює широкі можливості для кооперації різних виробників, а отже, створює передумови високої спеціалізації виробництва та випуску уніфікованої продукції.
- Здешевлюється експлуатація машин за рахунок прискорення ремонту і підвищення його якості.
Створення параметричних та уніфікованих рядів
Сучасний стан ринку техніки характеризується широкою номенклатурою виробів. Але випуск надмірно великої номенклатури виробів, схожих за призначенням і конструктивним виконанням, здорожує їх виробництво та ускладнює уніфікацію. Одним із основних шляхів виготовлення раціональної номенклатури й кількості типорозмірів виробів є використання стандартизованих рядів основних параметрів (параметричних рядів).
Параметрична стандартизація – це діяльність, що спрямована на вибір та встановлення доцільних чисельних значень параметрів, що підпорядковуються певній строгій математичній залежності.
Параметри виробів поділяють на основні та головні. Основні параметри визначають характерні конструктивні та експлуатаційні властивості виробів та процесів. Головні параметри виділяють із числа основних. Вони вирізняються стабільністю при подальших удосконаленнях, не залежать від матеріалів та технологій виготовлення і при цьому найбільш повно характеризують конструктивно-технологічні та експлуатаційні властивості виробу та процесів. Головних параметрів може бути як один, так і декілька.
Параметричними називають ряди машин однакового призначення з регламентованими конструкцією параметрами, градація яких встановлена з дотриманням визначених та чітко обґрунтованих рядів переважних чисел.
У багатьох випадках доцільно покласти в основу ряду єдиний тип машини й отримати необхідні градації зміною її розмірів або збереженням геометричної подібності модифікацій ряду. Такі ряди називаються розмірними.
В інших випадках доцільно встановити для кожної градації свій тип машин зі своїми розмірами. Такі ряди називають типорозмірними. У діапазоні параметрів, що найчастіше використовуються, доцільно збільшувати кількість членів ряду, в діапазоні нечастого використання – розширити інтервали між членами ряду.
Одним із головних умов реалізації економічного ефекту параметричних рядів є тривалість їх використання. Параметри уніфікованих рядів складаються за іншими законами, які залежать від реальних можливостей сполучення уніфікованих органів і умов технічного застосування членів ряду. Наприклад, уніфіковані ряди двигунів мають однакові шатунно-поршневі пари, але їх кількість та розташування – різне; параметричні ряди двигунів мають кількість та розміщення шатунно-поршневої пари однакове, але вона має різні діаметри та довжини ходу.
Універсалізація машин
Універсалізація машин переслідує мету розширення функцій машин, росту діапазону виконуваних нею операцій. Ця мета може досягатись як за рахунок додаткової комплектації машини пристосуваннями різного призначення чи змінними робочими органами, так і шляхом створення багатоцільової машини з широкими функціональними можливостями. Вона збільшує пристосованість машин до вимог виробництва і підвищує коефіцієнт їх використання. Головний економічний ефект від універсалізації полягає в можливості скоротити кількість об'єктів виробництва, тому що одна універсальна машина замінює декілька спеціалізованих.
Важливо також встановити доцільну межу універсалізації. Оскільки машини, призначені для надто широкого діапазону функцій, конструктивно складні, громіздкі та незручні в обслуговуванні.
Стандартиза́ція — діяльність, що полягає в установленні положень для загального та неодноразового використання щодо наявних чи потенційних завдань і спрямована на досягнення оптимального ступеня впорядкованості в певній сфері[1].
Загальний опис
Під стандартизацією розуміється діяльність, спрямована на досягнення впорядкування в певній області за допомогою встановлення положень для загального і багатократного вживання відносно реально існуючих і потенційних завдань. Ця діяльність виявляється в розробці, публікації вживанні стандартів.
Стандартом називається документ, в якому в цілях добровільного багаторазового використання встановлюються характеристики продукції, правила здійснення і характеристики процесів виробництва, експлуатації, зберігання, перевезення, реалізації і утилізації, виконання робіт або надання послуг. Стандарт також може містити вимоги до термінології, символіки, упаковки, маркування або етикеток і правил їх нанесення.
Результати стандартизації
За версією ISO найважливішими результатами стандартизації повинні бути[2]:
- підвищення ступеня відповідності продукції, процесів та послуг їх функціональному призначенню;
- усунення перешкод у торгівлі;
- сприяння науково-технічному співробітництву.
Види стандартизації за рівнем
- Міжнародна стандартизація — стандартизація, що проводиться на міжнародному рівні та участь у якій відкрита для відповідних органів усіх країн.
- Регіональна стандартизація — стандартизація, що проводиться на відповідному регіональному рівні та участь у якій відкрита для відповідних органів країн певного географічного або економічного простору.
- Національна стандартизація — стандартизація, що проводиться на рівні однієї країни.
Об'єкти стандартизації
Об'єктами стандартизації є:
- матеріали, складники, обладнання, системи, їх сукупність;
- правила, процедури, функції, методи, діяльність чи її результати, включаючи продукцію, персонал, системи управління;
- вимоги до термінології, позначення, фасування, пакування, маркування, етикетування тощо.
Суб'єкти стандартизації
Суб'єктами стандартизації є:
• Центральний орган виконавчої влади з питань стандартизації (ЦОВМ);
• рада стандартизації та технічного регулювання;
• технічні комітети стандартизації;
• інші суб'єкти, що займаються стандартизацією.
Центральні органи виконавчої влади та організації мають право у відповідних сферах діяльності та в межах повноважень з урахуванням своїх господарських та професійних інтересів організовувати і виконувати роботи із стандартизації, зокрема:
- Розробляти, схвалювати, приймати, переглядати, змінювати стандарти відповідного рівня та припиняти їх дію, встановлювати правила їх розроблення, позначення та застосування;
- Представляти Україну у відповідних спеціалізованих міжнародних та регіональних організаціях стандартизації, виконувати зобов'язання, передбачені положеннями про ці організації;
- Створювати і вести реєстри нормативно-правових актів та нормативних документів для забезпечення своєї діяльності та інформаційного обміну;
- Видавати та розповсюджувати свої стандарти, документи спеціалізованих відповідних міжнародних та регіональних організацій стандартизації, членами яких вони є чи з якими співпрацюють на основі положень про ці організації або відповідних договорів, а також делегувати ці повноваження іншим організаціям.
Мета і завдання стандартизації
Метою стандартизації в Україні є забезпечення раціонального використання природних ресурсів, відповідності об'єктів стандартизації їх функціональному призначенню, інформування споживачів про якість продукції, процесів та послуг, підтримка розвитку і міжнародної конкурентоспроможності продукції та торгівлі товарами і послугами.
Завдання стандартизації полягають у створенні умов для досягнення:
- економії всіх видів ресурсів;
- безпеки продукції, робіт і послуг для довкілля, життя, здоров'я і майна;
- безпеки господарських об'єктів з врахуванням ризику виникнення природних і техногенних катастроф та інших надзвичайних ситуацій;
- технічної та інформаційної сумісності, а також взаємозамінюваності продукції;
- якості продукції, робіт і послуг відповідно до рівня розвитку науки, техніки і технології;
- єдності вимірювань;
- обороноздатності і мобілізаційної готовності країни.
Стандартизація, як основа технічного регулювання, (діяльність, що спрямована на досягнення оптимального ступеня впорядкованості за даних умов) знаходить дуже широке застосування майже в усіх галузях, вона чітко встановлює вимоги до продукції (військове озброєння, атомна енергетика, аерокосмічна галузь тощо) та питань безпеки, вона дозволяє досягати рівня стандартної (базової) або навіть конкурентоспроможної якості (наприклад, на рівні галузевих стандартів) відповідно до мети застосування.
Національна стандартизація через процес гармонізації з міжнародними нормативними документами, що отримали міжнародне визнання, служить перепусткою на світові ринки для вітчизняних виробників.
Системи стандартів
Загально-технічні та організаційно-методичні стандарти, як правило, об'єднують в комплекси (системи) стандартів для нормативного забезпечення в певній галузі діяльності. Їх використання дає можливість спростити розробку, конструювання і підготовку виробництва нових виробів, скоротити виробничі цикли, здешевити і поруч з тим підвищити якість вдосконаленої продукції. Подальший розвиток стандартизації веде до створення великих комплексів, що охоплюють цілі галузі, а часто такі комплекси стають і міжгалузевими.
До числа міжгалузевих систем входять Єдина система конструкторської документації (ЄСКД), Єдина система технологічної документації (ЄСТД), Система метрологічних стандартів, об'єднаних назвою «Метрологія», Система стандартів безпеки праці (ССБП), Єдина система технологічної підготовки виробництва (ЄСТПВ), Система розробки і впровадження продукції у виробництво (СРПВ), Система стандартів у галузі охорони природи, Система стандартів на коди і кодування інформації тощо. До систем, які не можна назвати міжгалузевими бо мають загальнодержавне значення слід віднести Державну систему стандартизації України. Стандарти Державної системи стандартизації України позначаються перед реєстраційним номером цифрою 1.
Методичні основи стандартизації
Існує, також, низка методичних принципів, що застосовуються в діяльності зі стандартизації, серед яких найважливішими є:
- застосування системи переважних чисел полягає у використанні певних, науково обґрунтованих, рядів чисел (номіналів) при виборі номінальних значень параметрів виробів, що проєктуються і виготовляються;
- вибір та оптимізація параметричних рядів виробів, які передбачають, що параметри об'єктів стандартизації вибираються не довільно, а визначаються за єдиними правилами, які нормуються комплексом стандартів;
- уніфікація виробів полягає у виборі оптимальної кількості або в раціональному скороченні числа типів, видів, параметрів і розмірів об'єктів однакового чи близького функціонального призначення. ;
- комплексна стандартизація передбачає розробку системи стандартів, що визначають оптимальні взаємопов'язані та взаємоузгоджені норми і вимоги до самого об'єкта та його елементів, з яких він складається чи від яких він залежить.;
- випереджувальна стандартизація полягає в установленні підвищених вимог і норм відносно досягнутого рівня.
При розробці стандартів використовують науково-технічні результати науково-дослідних, дослідно-конструкторських, дослідно-технологічних, проєктних робіт, результати патентних досліджень, міжнародні, регіональні стандарти, правила, норми і рекомендації з стандартизації, прогресивні національні стандарти інших країн та іншу інформацію про сучасних досягненнях вітчизняної та зарубіжної науки, техніки і технології.
Види стандартів в Україні
Національні стандарти України (ДСТУ) містять вимоги, які стосуються забезпечення безпеки машинобудівної продукції для здоров'я людей і гігієни роботи, забезпечення вірогідності та єдності вимог під час розробки, виготовлення, експлуатації й збереження машинобудівної продукції. Вимоги державних стандартів підлягають безумовному виконанню на всій території України.
Галузеві стандарти України (ГСТУ) розробляються на продукцію, на яку відсутній державний стандарт України, або якщо буде потреба встановити нові вимоги, які перевищують або доповнюють вимоги державних стандартів.
Стандарти науково-технічних та інженерних товариств і спілок України (СНТС) розширюють результати фундаментальних і прикладних досліджень, отриманих в окремих областях знань або в сферах професійних інтересів.
Технічні умови (ТУ) є нормативним документом, що визначає необхідні експлуатаційні умови продукції, що випускається й для якої відсутній державний або галузевий стандарт.
Стандарт організації України (СОУ) розробляється на продукцію або на технологічний процес, які реалізуються на конкретному підприємстві.
Крім зазначених, до категорії нормативних документів зі стандартизації потрібно віднести: міждержавні стандарти; регіональні стандарти; міжнародні стандарти (ISO); національні стандарти інших країн. Міжнародні, міждержавні, регіональні й національні стандарти інших країн в Україні застосовують у рамках міжнародних договорів у встановленому порядку.
З 1 січня 2016, деякі європейські та міжнародні стандарти діятимуть на території України замість національних стандартів. Про це йдеться в наказі Міністерства економічного розвитку і торгівлі України № 1493 «Про прийняття європейських і міжнародних нормативних документів як національних стандартів України, змін до національних стандартів України та скасування національних стандартів України» від 30 грудня 2014 року. На виконання цього наказу було сформовано три переліки прийнятих та скасованих нормативних документів.[3] Відповідні зміни відбуваються за законом «Про стандарти, технічні регламенти та процедури оцінки відповідності» та на виконання статей 26 і 124 Угоди про асоціацію між Україною та Європейським Союзом.
2.Розрізняють такі розміри деталі: а) номінальний б) граничний в) дійсний. Номінальний розмір- розмір деталі вказаний на кресленні. Граничний розмір - розмір деталі з врахуванням відхилень. Дійсний розмір - розмір деталі отриманий внаслідок вимірювання.
3.Розміри деталі можуть мати два відхилення: верхнє і нижнє. Розрізняють два види деталей незалежно від їх зовнішньої конфігурації; отвір і вал. Отвір - деталь яка охоплює іншу деталь. Отвір - охоплювана деталь. Для отвору вводяться буквенні позначення великими буквами англійського алфавіту а для вала - ма лими буквами. D - номінальний діаметр отвору,ES - верхнє відхилення розміру отвору,EI - нижнє відхилення розміру отвору,d - номінальний розмір вала,es - верхнє відхилення розміру вала,ei - нижнє відхилення розміру вала.Максимальний граничний розмір отвору Dmax= D+ES мінімальний - Dmin =D + EI, для вала dmax = d+es dmin = d +ei.
4. Допуск розміру це алгебраїчна різниця між максамальним і мініламльним граничним розміром. Позначається буквою T. Для отвору TD= Dmax - Dmin . Для вала Td = dmax - dmin.
5. Посадка - це характер зєднання двох деталей. Є такі види посадок: посадка з зазором, посадка з натягом , перехідна посадка. Перехідна посадка передбачає як зазор так і натяг у зєднувальних деталях.
6. При графічному зображенні поля допуску розміру по вертикальній осі увибраному масштабі відкладають граничні розміри деталі. Через одержані точки проводять лінії паралельні горизонтальній осі.Через початок і кінець цих ліній проводять паралельні вертикальні лінії так, щоб утворився прямокутник довільної форми.
7.Відхилення від вірної форми можуть бути такі
а) відхилення від круглості (овальність, огранка)
б) відхилення від профілю повздовжнього перерізу (конусоподібність, бочкоподібність, сідлоподібність)
в) відхилення від циліндричності
г) відхилення від прямолінійності осі
8. Точність обробки деталі характеризується шорсткістю її поверхні. Чим менша шорсткість поверхні тим точніше вона оброблена. Шорсткість поверхні деталі на робочих кресленнях позначають умовними значками.
Література: А.Ф. Антоненко, Р. М. Недашківський " Комплексна система технічного обслуговування тракторів і автомобілів" стр. 92 - 98. В.З.Набродов " Допуски, посадки та технічні вимірювання" стр. 4 -
24.
Тема: Система допусків і посадок
Учбові питання
1.Системи посадок
2. Система допусків
3. Квалітети точності
4. Позначення посадок на кресленнях
Література: А. Ф. Антоненко, Р. М. Недашківський " Комплексна система технічного обслуговування тракторів і автомобілів" стр. 94 - 96
1. Існують дві системи посадок: посадки в системі вала і посадки в системі отвору. В системі вала основною деталею є вал, а в системі отвору - отвір. Основний вал - вал у якого верхнє відхилення дорівнює нулю. Основний отвір - отвір у якого нижнє відхилення дорівнює нулю.
2.Система допусків забеспечує взаємозамінність у машинобудуванні , підвищення якості продукції. Поширюється на розміри до 10000мм. Цей діапазон розмірів розбитий на три групи : 1 - 500 мм, 500 - 3150 мм, 3150 - 10000мм. Усі поля допусків для отворів і валів позначаються літерами латинського алфавіту: для отворів - прописні ( А, В, С і т.д.) для валів - рядкові (а,в,с і т.д.)
3. Ступінь точності розміру деталі характеризується квалітетом. Є 19 квалітетів точності (01 - 17).Квалітет точності позначають літерами ІТ. Квалітет ІТ01 - найточніший, квалітет ІТ 17 найменш точний. Найточніші квалітети мають мале поле допуску. У машинобудуванні широко застосовують квалітети ІТ 5 - ІТ 12.
4. Умовне позначення посадки на кресленні включає в себе такі показники:
а) номінальний діаметр зєднання
б) поле допуску розміру отвору
в) квалітет розміру отвору
г) поле допуску розміру вала
д) квалітет розміру вала
Наприклад : посадка ліаметр 50 К6/ а7
де 50 - номінальний діаметр
К - поле допуску розміру вала
6 - квалітет розміру отвору
а - поле допуску розміру вала
7 - квалітет розміру вала
Тема: Види посадок
Учбові питання
1. Поняття " посадка"
2. Види посадок і їх характеристика
1. Посадка - характер зєднання двох деталей , який визначається різницею їх розмірів до складання.
2. Всі посадки діляться на такі види: з зазором, з натягом, перехідна
Посадка з зазором - посадка при якій у зєднанні вал - отвір завжди утворюється зазор, тобто найменший граничний розмір вала більший найбільшого граничного розміру вала. Посадка з натягом - посадка при якій у зєднанні деталей вал - отвір завжди утворюється натяг, тобто найменший граничний розмір вала завжди більший найбільшого граничного розміру отвору. Перехідна посадка - посадка при якій можливий як зазор так і натяг. Приклади посадок : з зазором ( поршень - циліндр) з натягом (внутрішнє кільце підшипника - вал) перехідна посадка (зовнішнє кільце підшипника - корпус).
Тема: Розміри деталі
1. Види розмірів
2. Види відхилень розмірів
Література: А.Ф. Антоненко, Р. М. Недашківський " Комплексна система технічного обслуговування тракторів і автомобілів" стр. 92 - 98. В.З.Набродов " Допуски, посадки та технічні вимірювання" стр. 4 -
24.
1.Розрізняють такі розміри деталі: а) номінальний б) граничний в) дійсний. Номінальний розмір- розмір деталі вказаний на кресленні. Граничний розмір - розмір деталі з врахуванням відхилень. Дійсний розмір - розмір деталі отриманий внаслідок вимірювання.Граничних розмірів деталі - два ( максимальний і мінімальний)
2..Розміри деталі можуть мати два відхилення: верхнє і нижнє. Розрізняють два види деталей незалежно від їх зовнішньої конфігурації; отвір і вал. Отвір - деталь яка охоплює іншу деталь. Отвір - охоплювана деталь. Для отвору вводяться буквенні позначення великими буквами англійського алфавіту а для вала - ма лими буквами. D - номінальний діаметр отвору,ES - верхнє відхилення розміру отвору,EI - нижнє відхилення розміру отвору,d - номінальний розмір вала,es - верхнє відхилення розміру вала,ei - нижнє відхилення розміру вала.Максимальний граничний розмір отвору Dmax= D+ES мінімальний - Dmin =D + EI, для вала dmax = d+es dmin = d +ei.
Тема: Вимірювальні інструменти
Правильність заданих кресленням розмірів і форми деталей в процесі їх виготовлення перевіряють штриховим (шкальні) вимірювальним інструментом, а також перевірочними лінійками, плитами та ін..
Тому крім типового, набору робочого інструмента слюсар повинен мати необхідний (ходової) контрольно-вимірювальний інструмент. До нього відносяться: масштабна лінійка, рулетка, кронциркуль і нутромер, штангенциркуль, кутник, малка, транспортир, кутомір, повірочна лінійка і т. п.
Масштабна лінійка має штрихи-ділення, розташовані один від одного на відстані 105 і іноді 025 мм. Ці ділення і складають вимірювальну шкалу лінійки. Для зручності розрахунку розмірів кожне полусантіметровое розподіл шкали відзначається подовженим штрихом, а кожне сантиметрове - ще більш подовженим штрихом, над яким проставляється цифра, яка вказує число сантиметрів від початку шкали. Масштабної лінійкою виробляють вимірювання зовнішніх і внутрішніх розмірів і відстаней з точністю до 05 мм, а при наявності досвіду - і до 025 мм. Масштабні лінійки виготовляють жорсткими або пружними, з довжиною шкали 100150200 300500750 і 1000 мм, шириною 10-25 мм і товщиною 03-15 мм, з вуглецевої інструментальної сталі марки У7 або У8.
Рулетка являє собою сталеву стрічку, на поверхні якої нанесена шкала з ціною поділки 1 мм. Стрічка укладена в футляр і втягується в нього або пружиною (самосвертивающіеся рулетки, ), або обертанням рукоятки (прості рулетки,, або вдвигается вручну (жолоби рулетки ,Самосвертивающіеся і жолоби рулетки виготовляються з довжиною шкали 1 і 2 м, а простие- з довжиною 2510 2030 і 50 м. Рулетки застосовуються для вимірювання лінійних розмірів: довжини, ширини, висоти деталей і відстаней між їх окремими частинами, а також довжин дуг і кіл і кривих.
Вимірюючи окружність циліндра, навколо нього щільно обгортають сталеву стрічку рулетки. При цьому розподіл шкали, що збігається з нульовим діленням стрічки, вказує нам довжину вимірюваної окружності. Такими прийомами користуються зазвичай при необхідності визначити довжину розгортки або діаметр великого циліндра, якщо безпосереднє вимірювання його утруднено.
Для перенесення розмірів на масштабну лінійку і контролю розмірів деталей в процесі їх виготовлення користуються кронциркулем і нутромером.
Кронціркуль застосовується для вимірювання зовнішніх розмірів деталей: діаметрів, довжин, товщини буртиков, стінок і т. П. Він складається з двох вигнутих по великому радіусу ніжок довжиною 150-200 мм, з'єднаних шарніром , При вимірі кронциркуль беруть правою рукою за шарнір і розсовують його ніжки так, щоб їх кінці стосувалися перевіряється деталі і переміщалися по ній з невеликим зусиллям. Розмір деталі визначають накладенням ніжок кронциркуля на масштабну лінійку.
Більш зручним є пружинний кронциркуль Ніжки такого кронциркуля під тиском кільцевої пружини прагнуть розійтися, але гайка, навернути на стягнутий гвинт, укріплений на одній ніжці і вільно проходить крізь іншу, перешкоджає цьому. обертанням гайки по гвинту з дрібною різьбою встановлюють ніжки на розмір, який, не може змінитися довільно.
Точність вимірювання кронциркулем 025-05 мм. Виготовляють його з вуглецевої інструментальної сталі У7 або У8 а вимірювальні кінці на довжині 15-20 мм гартують.
Нутромер служить для вимірювання внутрішніх розмірів: діаметрів отворів, розмірів пазів, виточок і т. П. На відміну від кронциркуля він має прямі ніжки з відігнутими губками. Пристрій нутромера аналогічно пристрою кронциркуля.
При вимірюванні діаметру ніжки нутромера розводять до легкого дотику зі стінками деталі і потім вводять в отвір прямовисно. Заміряний розмір отвору буде відповідати дійсному тільки в тому випадку, коли нутромер НЕ буде перекошений, т. Е. Лінія, що проходить через кінці ніжок, буде перпендикулярній осі отвору. Відлік розміру проводиться по вимірювальної лінійці; при цьому одну ніжку нутромера наголошують в площину, до якої під прямим кутом притиснута торцева грань вимірювальної лінійки, і виробляють по ній відлік розміру.
Виготовляють нутроміри з вуглецевої інструментальної сталі У7 або У8 з загартуванням вимірювальних кінців на довжині 15-20 мм.
Точність вимірювань, яку можна отримати за допомогою масштабної лінійки, складного метра або рулетки, далеко не завжди задовольняє вимогам сучасного машинобудування. Тому при виготовленні відповідальних деталей машин користуються більш досконалими масштабними інструментами, які дозволяють визначати розміри з підвищеною точністю. До таких інструментів в першу чергу відноситься штангенциркуль.
Штангенциркуль широко використовується в машинобудуванні для вимірювання зовнішніх і внутрішніх розмірів, глибин, буртиков і висот деталей. Універсальність, простота відліку, доступність і широкий діапазон виміру дозволяють використовувати штангенциркуль на різних роботах. Конструкції випускаються промисловістю штангенциркулів дають можливість робити відлік розмірів з точністю до 01 і 005 мм. Штангенциркулі, з точністю відліку розмірів до 002 мм в даний час не випускаються.
Штангенциркуль складається з штанги, на якій нанесена шкала лінійки. Штанга виконана заодно з губками. За штанзі переміщається рамка з губками рамки. Безпосередньо на рамці нанесена шкала ноніуса. При зімкнутих губах інструменту поділу лінійки і шкали ноніуса точно збігаються. Вимірювану деталь злегка затискають між губками штангенциркуля, фіксують рамку затискним гвинтом, а потім за шкалами штанги і ноніуса виробляють відлік розміру. Вимірювання глибини здійснюється за допомогою глибиноміра. Залежно від кількості поділів ноніуса справжніх розмірів деталі можна визначати з точністю 01-005 мм. Наприклад, якщо шкала ноніуса довжиною 9 мм розділена на 10 рівних частин, то, отже, кожне ділення ноніуса дорівнює 9: 10 = 09 мм, т. Е. Коротше поділу на лінійці на 10 -09 = 01 мм. При щільно зсунутих губах штангенциркуля нульовий штрих ноніуса збігається з нульовим штрихом штанги, а десятий штрих ноніуса - з дев'ятим штрихом штанги. При такій (так званої нульової) установці губок штангенциркуля перший розподіл ноніуса не дійде до першого поділу лінійки-штанги на 01 мм, друге - на 02 мм, третє - на 03 мм і т. Д. Якщо пересунути рамку таким чином, щоб перший штрих ноніуса збігся з першим штрихом штанги, то зазор між губками буде дорівнює 01 мм. При збігу, наприклад, "шостого штриха ноніуса з будь-яким штрихом штанги зазор буде дорівнює 01 мм і т. д. Для відліку дійсного розміру по штангенциркулем кількість цілих міліметрів потрібно взяти за шкалою штанги до нульового штриха ноніуса, а кількість десятих часток міліметра - за ноніусом, визначивши, який штрих ноніуса збігається зі штрихом основної шкали.Мал. 2. Штангенциркуль (а); пристрій ноніуса (б і в)
Слід зазначити, що виробництво штангенциркулів з довжиною шкали ноніуса 9 мм, поділеній на 10 рівних частин, промисловістю припинено, проте в навчальних цілях штангенциркулем із зазначеним ноніусом користуються.
Згідно ГОСТ у 166-63 інструментальна промисловість нашої країни випускає штангенциркулі наступних типів:
ШЦ-1 - з двостороннім розташуванням губок-для зовнішніх і внутрішніх вимірювань і з лінійкою для вимірювання глибин (рис. 2 а); межі вимірювання від 0 до 125 мм; точність відліку за ноніусом 01 мм;
ШЦ-П - з двостороннім розташуванням губок - для зовнішніх і внутрішніх вимірювань і для розмітки; межі вимірювання від 0 до 200 і від 0 до 320 мм; точність відліку за ноніусом 01 і 005 мм;
ШЦ-Ш - з одностороннім розташуванням губок; межі вимірювання 0-500250-710320-1000500- 1400 і 800-2000 мм. Точність відліку за ноніусом 01 і 005 мм, а також штангенциркуль з пристроєм для розмітки (ТУ 2-034-803-69) з межами вимірювання 1500-3000 і 2000-4000 мм. Точність відліку за ноніусом 01 мм.
У штангенциркуля ШЦ-I шкала ноніуса зроблена більшої і має довжину 19 мм Така шкала більш зручна для відліку, так як кожне ділення ноніуса одно НЕ 09 а 19 мм. Принцип визначення розміру з точністю 01 мм при цьому не змінюється. Точність відліку 01 мм в ряді випадків буває недостатньою. Для більш точного відліку шкалу ноніуса де-л ють довжиною 39 мм і ділять її на 20 частин; тоді ціна однієї поділки ноніуса складе 39: 20 = 195 мм. Таким чином, якщо на лінійці штанги нанесена звичайна міліметрова шкала, то перший штрих ноніуса буде «відставати» від другого штриха лінійки на 005 мм, другий штрих ноніуса від четвертого штриха лінійки - на 005X2 = 01 мм і т. д.
Штангенінструмент з точністю відліку за ноніусом 005 мм відносяться до вимірювальних інструментів підвищеної точності. Вони мають установче пристосування-мікрометричний пристрій, що дозволяє точно регулювати переміщення рамки з рухомою губкою і швидко встановлювати заданий розмір.
Інструменти для перевірки кутів. У машинобудуванні найбільш поширеним інструментом для перевірки і розмітки прямих кутів і для контролю взаємно перпендикулярного розташування деталей є сталеві косинці з кутом 90 ° ( ГОСТ 3749-65), а також малки, транспортири, кутоміри, шаблони і ін..
Косинці виготовляють трьох класів точності: 0 1 і 2. Найбільш точні косинці - класу 0. Точні косинці з фасками називаються лекальними ). Для перевірки прямих кутів кутник накладають на перевіряється деталь і визначають правильність обробки перевіряється кута на просвіт. При перевірці зовнішнього кута кутник накладають на деталь його внутрішньою частиною а при перевірці внутрішнього кута - зовнішньою частиною. Наклавши кутник однією стороною на оброблену сторону деталі, злегка притискаючи його, поєднують іншу сторону кутника з оброблюваної стороною деталі та по утворився просвіту судять про точність виконання прямого кута ( Іноді розмір просвіту визначають за допомогою щупів. Необхідно стежити за тим, щоб кутник встановлювався в площині, перпендикулярній до лінії перетину площин, що утворюють прямий кут
Проста малка складається з обойми і лінійки, закріпленої шарнірно між двома планками обойми. Шарнірне кріплення обойми дозволяє лінійці займати по відношенню до обоймі положення під будь-яким кутом. Малку встановлюють на необхідний кут за зразком деталі або за кутовими плитках. Необхідний кут фіксується гвинтом з смушевій гайкою.
Проста малка служить для вимірювання (перенесення) одночасно тільки одного кута.
Універсальна малка служить для одночасного перенесення двох або трьох кутів.
Подвійна малка складається з двох лінійок (рис. 4 б), з'єднаних шарнірно з важелем. Кінець лінійки зрізаний під кутом 45 °, а кінці лінійки - під кутом 30 і 60 °. Лінійка і важіль мають поздовжні прорізи, по яких переміщається гвинт; гвинт може бути закріплений в різних місцях прорізи.
При вимірюванні кутів лінійки подвійний малки встановлюють під кутом, який потрібно перевірити (рис. 4 в). Якщо необхідно перевірити відразу два-три кути, то важіль також встановлюють під потрібним кутом. Коли малка встановлена на певний кут і гвинти закріплені, її накладають на деталь і переглядають на світло, спостерігаючи, чи збігаються межі лінійок малки з поверхнями деталі чи ні. В процесі перевірки не слід сильно натискати малкою на деталь, так як цим можна збити установку лінійок. Якщо при накладенні малки на деталь між гранями лінійок і поверхнями деталі помітні просвіти, це означає, що деталь виготовлена неправильно.
Малка особливо зручна в тих випадках, коли по готової (зразковою) деталі потрібно виготовити ряд інших, подібних їй. В цьому випадку малку встановлюють по зразковою деталі, а все нові деталі перевіряють по цій установці.
За допомогою косинців і малки можна лише перевірити правильність виконання заданих кутів, але судити про величину відхилення не можна.
Косинці і малки виготовляють з вуглецевих інструментальних сталей У7 і У8 з наступним загартуванням.
Для вимірювання або розмітки кутів, для настройки малок або визначення величини перенесених ними кутів користуються кутомірними інструментами з незалежним кутом. До таких інструментів належать і кутоміри.
Транспортири зазвичай застосовуються для вимірювання і розмітки кутів на площині. Кутоміри бувають прості і універсальні.
Простий кутомір складається з лінійки і транспортира При вимірах кутомір накладають на деталь так, щоб лінійка і нижня частина полки транспортира збігалися зі сторонами вимірюваної деталі. Величину кута визначають за вказівником, що переміщається по шкалі транспортира разом з лінійкою. Простим кутоміром можна вимірювати величину кутів з точністю 05-1 °.
Оптичний кутомір складається з корпусу, в якому закріплено скляний диск зі шкалою, що має ділення в градусах і хвилинах. Ціна малих поділок. З корпусом жорстко скріплена основна (нерухома) лінійка. На диску змонтовані лупа, важіль і укріплена рухома лінійка. Під лупою паралельно скляному диску розташована невелика скляна платівка, на якій завдано покажчик, ясно видимий через окуляр. Лінійку можна переміщати в поздовжньому напрямку і за допомогою важеля закріплювати в потрібному положенні. Під час повороту лінійки в ту або іншу сторону будуть обертатися в тому ж напрямку диск і лупа. Таким чином, визначеного положення лінійки буде відповідати цілком певне положення диска і лупи. Після закріплення лінійок затискним кільцем, спостерігаючи через лупу, роблять відлік показань кутоміра.
Оптичним кутоміром можна вимірювати кути від 0 до 180 °. Допустимі похибки свідчення оптичного кутоміра ± 5 '.
Перевірочні лінійки служать для перевірки площин на прямолінійність. В процесі обробки площин найчастіше користуються лекальними лінійками. Вони підрозділяються на лінійки лекальні з двостороннім скосом, тригранні і чотиригранні
Лекальні лінійки виготовляють з високою точністю, вони мають тонкі ребра з радіусом заокруглення 01-02 мм, завдяки чому можна досить точно визначити відхилення від прямолінійності за способом світлової щілини (на просвіт). Для цього лінійку своїх ребром встановлюють на перевіряється поверхню деталі проти світла (рис. 56). Наявні відхилення від прямолінійності будуть при цьому помітні між лінійкою і поверхнею деталі. При хорошому освітленні можна виявити відхилення від прямолінійності величиною від 0005 до 0002 мм. Лекальні лінійки виготовляють довжиною від 25 до 500 мм з вуглецевої інструментальної або легованої сталі з наступним загартуванням.
Зберігання вимірювального інструмента і догляд за ним. Точність і довговічність інструменту залежать не тільки від якості виготовлення і вмілого звернення, але також і від правильного зберігання і догляду за ним
Найпростіший вимірювальний інструмент зберігається зазвичай у ящику верстата, де його мають у своєму розпорядженні в певному порядку за типами інструменту і розмірами. Штангенциркулі і лекальні лінійки зберігаються в спеціальних футлярах з кришками. Для запобігання інструменту від іржі його змазування-мают тонким шаром чистого технічного вазеліну, попередньо добре протерши сухою ганчіркою. Перед вживанням інструменту мастило видаляється чистою ганчіркою або промиванням в бензині.
При появі плям іржі інструмент необхідно покласти на добу в гас, після чого промити бензином, насухо протерти і знову змастити.
Тема: Шорсткість поверхні
Шо́рсткість пове́рхні - характеристика нерівностей, виражена у числових величинах, що визначають ступінь їхнього відхилення на базовій довжині від теоретично гладких поверхонь заданої геометричної форми[1].
Нормальний профіль та параметри шорсткості
Шорсткість поверхні - важливий показник у технічній характеристиці виробу та точності його виготовлення, що впливає на експлуатаційні властивості деталей і вузлів машин - стійкість до зносу поверхонь тертя, витривалість, корозійну стійкість, збереження натягу у пресових з'єднаннях тощо.
Параметри шорсткості
Шорсткість відноситься до мікрогеометрії твердого тіла і визначає його найважливіші експлуатаційні властивості. Перш за все зносостійкість від стирання, міцність, щільність (герметичність) з'єднань, хімічна стійкість, зовнішній вигляд. Залежно від умов роботи поверхні призначається параметр шорсткості при проектуванні деталей машин. Державним стандартом ДСТУ ISO 4287:2012 визначено номенклатуру з 6-ти параметрів оцінки шорсткості поверхні, з яких для характеристики шорсткості вибирається один або декілька. Ці параметри такі: Висотні
- Ra - середнє арифметичне відхилення профілю (середнє арифметичне абсолютних значень відхилень профілю в межах базової довжини);
- Rz - висота нерівностей профілю по 10 точках (сума середніх абсолютних значень висот п'яти найбільших виступів і глибин п'яти найбільших впадин профілю в межах базової довжини);
- Rmax - найбільша висота профілю (відстань між лінією виступів профілю і лінією впадин профілю в межах базової довжини).
Крокові:
- S - середній крок місцевих виступів профілю (середнє арифметичне значення кроку нерівностей профілю по вершинах в межах базової довжини);
- Sm - середній крок нерівностей профілю по середній лінії (середнє арифметичне значення кроку нерівностей профілю в межах базової довжини).
Висотно-кроковий:
- tp - відносна опорна довжина профілю (відношення опорної довжини профілю до базової довжини, де p - значення рівня перерізу профілю).
Виступи шорсткості розподіляються на поверхні стінок рівномірно або нерівномірно, причому в загальному випадку вони можуть мати різну форму й розміри. В трубах промислового сортаменту через технологічну недосконалість їх виготовлення шорсткість розподілена нерівномірно. У випадку штучної шорсткості, як, напр., у дослідах І.Нікурадзе, шорсткість рівномірна за висотою.
Залежність шорсткості поверхні від виду обробки
Параметри шорсткості та види обробки, що їх забезпечують
Види обробки при формоутворенні Ra, мкм Rz, мкм Базова довжина, мм
Піскоструменева обробка, кування в штампах, відрізання, лиття в кокіль, лиття під тиском. 80; 63; 50; 40 320; 250; 200; 160 8,0
Кування в штампах, точіння чорнове, попереднє стругання, попереднє фрезерування, лиття в кокіль, лиття під тиском 40; 32; 25; 20 160; 125; 100; 80 8,0
Кування в штампах, свердління, чорнове зенкерування, чорнове та чистове точіння, стругання, лиття в кокіль та під тиском 20; 16,0;12,5; 10,0 80; 63; 50; 40 8,0
Свердління, чорнове та чистове зенкерування, чорнове та чистове точіння, стругання, вальцювання, лиття в кокіль та під тиском 10,0; 8,0; 6,3; 5,0 40; 32; 25; 20 2,5
Протягування, чистове точіння, зенкерування, свердління, стругання, вальцювання, високоточне литво, попереднє шліфування 5,0; 4,0; 3,2; 2,5 20; 16; 12,5; 10,0 2,5
Чистове зенкерування, розвертування, протягування, чистове та тонке точіння, чистове стругання, попереднє та чистове шліфування, шабрування, вальцювання, прецизійне литво 2,5; 2,0; 1,6; 1,25 10,0; 8,0; 6,3 0,8
Чистове зенкерування, нормальне та точне розвертування, протягування, чистове та тонке точіння, тонке фрезерування, чистове шліфування, прецизійне литво 1,25; 1,00; 0,80; 0,63 6,3; 5,0, 4,0; 3,2 0,8
Точне та тонке розвертування, протягування, чистове та тонке точіння, хонінгування, шабрування, вальцювання, прецизійне литво 0,63; 0,50; 0,40; 0,32 3,2; 2,5; 2,0; 1,60 0,8
Точне та тонке розвертування, протягування, тонке точіння, чистове та тонке шліфування, притирання, хонінгування, прецизійне литво пластмас 0,32; 0,25; 0,20; 0,160 1,60; 1,25; 1,00; 0,80 0,25
Тонке розвертування, тонке шліфування, притирання, хонінгування, прецизійне литво пластмас 0,160; 0,125; 0,10; 0,080 0,80; 0,63; 0,50; 0,40 0,25
Полірування, притирання, дзеркальне хонінгування, прецизійне литво пластмас 0,080; 0,063; 0,050; 0,040 0,40; 0,32; 0,25; 0,20 0,25
Полірування, тонке притирання, дзеркальне хонінгування, прецизійне литво пластмас 0,040; 0,032; 0,025; 0,020 0,20; 0,16; 0,125; 0,100 0,25
Полірування, тонке притирання 0,020; 0,016; 0,012; 0,010 0,100; 0,080; 0,063; 0,050 0,08
Полірування, тонке притирання 0,012; 0,010; 0,008 0,050; 0,040; 0,032 0,08
Примітка. Жирним шрифтом виділені параметри шорсткості, яким надається перевага у використанні
Вибір параметрів шорсткості
При виборі шорсткості поверхонь деталей треба знати їх функціональне призначення та конструктивні особливості. Наприклад, для поверхонь тертя відповідальних деталей установлюють допустимі значення Ra (або Rz), Rmax і tp, а також напрямок нерівностей. Для поверхонь циклічно навантажених деталей установлюють Rmax, Sm і S. Слід враховувати, що параметр Ra дає повнішу оцінку шорсткості, ніж Rz, тому що для його визначення вимірюють і сумують величини більшого числа точок дійсного профілю, тоді як при визначенні параметра Rz вимірюють тільки величину п'яти впадин і п'яти виступів. В окремих випадках встановлюють вимоги до напрямку нерівностей. При цьому слід враховувати, що найменший коефіцієнт тертя та знос деталей, що труться буде, якщо напрямок руху не збігається з напрямком нерівностей. Таке можна отримати при довільному напрямку нерівностей, що утворюються при хонінгуванні чи суперфінішуванні.
Умовне позначення шорсткості
Шорсткість поверхонь на креслениках деталі вказують для усіх поверхонь, що виконуються за цим креслеником, незалежно від методів їх утворення, крім поверхонь, шорсткість котрих не обумовлена вимогами конструкції.
Вид обробки поверхні вказують у позначенні шорсткості тільки у випадках, коли він є єдиним, для отримання потрібної якості поверхні.
У випадку, коли структуру (напрямок шорсткості) і спосіб обробки поверхні не вказують, знак шорсткості зображують без полиці.
Крім того, якщо знак шорсткості поміщають в правому верхньому куті кресленика (він відноситься до усіх поверхонь деталі), а якщо за ним у дужках вказано символ шорсткості, то цей параметр відноситься до решти поверхонь, шорсткість яких не вказана безпосередньо.
Значення параметрів шорсткості вказують на кресленнях за такими правилами (див. рис.):
- Ra вказується без символу, а інші параметри із символом;
- при вказанні діапазону параметрів записують межі у два рядки;
- при вказанні декількох параметрів шорсткості їх значення записують у стовпець, зверху вниз у такому порядку: Ra, Rz, Rmax, Sm, S, tp;
- якщо шорсткість нормується параметром Ra чи Rz з числа наведених вище у таблиці, то базову довжину в позначенні шорсткості не вказують.
Позначення шорсткості поверхонь на зображенні виробу розміщають на лініях контуру, виносних лініях (по можливості ближче до розмірної лінії) або на полицях ліній-виносок.
Допускається при недостачі місця розміщати позначення шорсткості на розмірних лініях або на їх продовженні, а також розривати виносну лінію.
Вимоги до шорсткості в залежності від функції поверхні
Параметри шорсткості та види поверхонь деталей машин
Елемент деталі Параметр шорсткості
Неробочі контури деталей. Поверхні деталей, що встановлюються на бетонних, цегляних і дерев'яних основах. Rz 320...160
Наскрізні отвори для кріпильних деталей. Виточки, проточки. Отвори масляних каналів на приводних валах. Кромки деталі під зварні шви. Опорні поверхні пружин стиснення. Монтажні площини станин, корпусів, лап. Rz 80
Внутрішній діаметр шліцьових з'єднань (не шліфованих). Вільні (неспряжувані) торцеві поверхні вал, муфт, втулок. Поверхні головок болтів. Rz 40
Торцеві поверхні під підшипники кочення. Поверхні втулок, кілець, маточин, що прилягають до інших поверхонь, але не є посадочними. Неробочі торці валів, втулок, планок. Шийки валів 12-го квалітету діаметром 80-500 мм. Поверхні отворів 12-го квалітету діаметром 18-500 мм і 11-го квалітету. Rz 20
Неробочі торцеві поверхні зубчастих та черв'ячних коліс і зірочок. Рівці, фаски, виточки, зенковки, заокруглення тощо Болти і гайки нормальної і підвищеної точності (крім різі). Rz 10...40
Кульові поверхні ніпельних з'єднань. Рівці під ущільнюючі гумові кільця для рухомих і нерухомих торцевих з'єднань. Радіуси закруглень на силових валах. Поверхні осей для ексцентриків. Опорні площини рейок. Поверхні виступаючих частин деталей, що швидко обертаються. Поверхні напрямних типу «ластівчин хвіст». Опорні площини рейок. Шийки валів 9-го квалітету діаметром 80-500 мм, 11-го квалітету діаметром 3-30 мм. Поверхні отворів 7-го квалітету діаметром 180-500 мм, 9-го квалітету діаметром 18-360 мм, 11-го квалітету діаметром 1-10 мм Ra 2,5
Зовнішні діаметри шліцьового з'єднання. Отвори підгінних і регульованих з'єднань (вкладиші підшипників тощо) з допуском зазору - натягу 25-40 мкм. Гідроциліндри, що працюють з гумовими манжетами. Отвори підшипників ковзання. Тертьові поверхні малонавантажених деталей. Робочі поверхні дисків тертя. Шийки валів 6-го квалітету діаметром 120-500 мм, 8-го квалітету діаметром 6-80 мм. Поверхні отворів 6-го квалітету діаметром 50-500 мм, 7-го квалітету діаметром 10-180 мм, 9-го квалітету - 1-18 мм Ra 1,25
Поверхні дзеркал циліндрів, які працюють з гумовими манжетами. Торцеві поверхні поршневих кілець при діаметрі не менше 240 мм. Вали що підганяються і регульованих з'єднаннях з допуском зазору - натягу 7-25 мкм. Тертьові поверхні навантажених деталей. Посадочні поверхні 7-го квалітету з тривалим збереженням заданої посадки: осі ексцентриків, точні черв'яки, зубчасті колеса. Спряжені поверхні бронзових зубчастих коліс. Робочі шийки розподільних валів. Штоки і шийки валів в ущільненнях. Шийки валів 5-го квалітету діаметром 30-500 мм, 6-го квалітету діаметром 10-120 мм. Поверхні отворів 6-го квалітету
діаметром 3-50 мм, 6-го квалітету діаметром 1-10 мм Ra 0,63
Шийки валів 5-го квалітету діаметром понад 1 до 30 мм, 6-го квалітету діаметром понад 1 до 10 мм. Вали в "регульованих з'єднаннях (шийки шпинделів, золотники) з допусками зазору - натягу 16-25 мкм. Отвори регульованих з'єднань (вкладиші підшипників) з допуском зазору - натягу 4-7 мкм. Тертьові елементи навантажених деталей. Гідроциліндри, що працюють з поршневими кільцями Ra 0,32
Поверхні деталей, що працюють на тертя, від зносу яких залежить точність роботи механізму Ra 0,160
Робочі шийки валів прецизійних швидкохідних верстатів і механізмів. Шийки валів що підганяються і регульованих з'єднаннях з допуском зазору - натягу 2,5-6,5 мкм. Поверхні отворів що підганяються і регульованих з'єднань з допуском зазору - натягу до 2,5 мкм Ra 0,080
Дзеркальні валики координатно-розточувальних верстатів та ін. Ra 0,040
Тема: Класи точності обробки поверхонь
Система допусків ділиться на класи точності в залежності від призначення деталей і ступеня точності, з якою вони повинні оброблятися. :
Перший клас, найточніший, застосовується при обробці особливо точних виробів, наприклад вимірювальних інструментів і приладів, кілець шарикопідшипників.
Другий клас - основний в сучасному машинобудуванні. З цього класу точності виготовляють відповідальні деталі металообробних верстатів, автомобільних і тракторних двигунів, текстильних, взуттєвих і багатьох інших машин.
Третій клас застосовується у важкій і загальному машинобудуванні для виготовлення деталей, які потребують особливої точності.
Класи 2а і За є проміжними класами. У багатьох випадках практично вдається посадку другого класу замінити відповідними посадками класу 2а, а посадки третього класу - посадками класу За, що дає зниження вартості обробки деталей.
Четвертий клас застосовується при виготовленні невідповідальних деталей з відносно великими допусками.
П'ятий клас застосовується при виготовленні невідповідальних деталей різних грубих механізмів.
У ряді галузей промисловості, наприклад в авіаційній, п'ятий клас застосовується для деталей з вільними розмірами.
Сьомий, восьмий і дев'ятий класи застосовуються при виготовленні найгрубіших виробів, в заготівельних операціях і при обробці деталей з вільними розмірами.