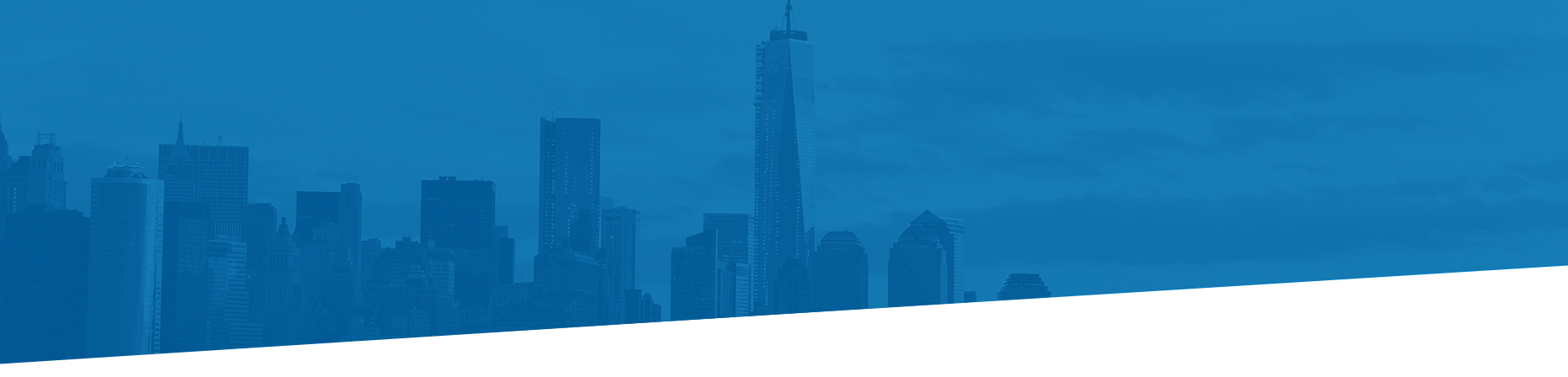
БУДОВА ВАНТАЖНОГО АВТОМОБІЛЯ
Тема: Загальна будова вантажного автомобіля
Учбові питання
1. Класифікація вантажних автомобілів
2. Технічна характеристика вантажних автомобілів
3. Загальна будова вантажного автомобіля
4. Маркування вантажних автомобілів
1.Вантажні автомобілі можна класифікувати за такими ознаками :
а) за призначенням ( загльного і спеціального)
Автомобілі загального призначення мають кузов бортової конструкції. До автомобілів спеціального призначення відносяться самоскиди, автоцистерни, рефрижератори.
б) за конструктивною схемою ( одиночні і автопоїзди) .Автопоїзди комплектуються причіпами або напівпричіпами.
в)За вантажопідйомністю вони бувають таких класів:1.Особливо малої (до 0,5т) 2.малої ( 0,5,,,2 т) 3,Середньої ( 2,,,5т) 4. Великої (5,,,15т) 5. Особливо великої ( понад 15т)
г) За повною масою вантажні автомобілі поділяють на класи: 1- до 1,2т 2-1,3...3т 3- 3...5т 4-5...8т 5 - 8...16т 6 - 16...40т 7 - понад 40т.
2. У технічній характеристиці вантажних автомобілів вказують такі показники:
а) базова модель
б)колісна формула
в)повна маса
г) вантажопідйомність
д) потужність двигуна
г) кількість циліндрів
д) осьове навантаження
3.Вантажний автомобіль складається з двигуна, кузова і шассі. Кузов включає в себе такі елементи як кабіна і вантажна платформа . За конструкцією кабіни бувають капотні ,короткокапотні і безкапотні. Шасі включає в себе такі компоненти : трансмісія , ходова частина, механізми керування.
4. У маркуванні вантажних автомобілів вказують такі показники:
А) Назва автозаводу
Б) Перша цифра - клас вантажного автомобіля
В) Друга цифра - особливості конструкції. 3 - бортовий, 4 - тягач, 5 - самоскид , 6 - цистерна , 7 - фургон , 8 - резерв, 9 - спеціальний
Домашнє завдання: О. П. Строков, М. Г. Макаренко, В. Ф. Орлов, В. О. Павленко " Основи будови та експлуатації автопоїздів" стр.5 -10
Тема: Положення про ТО і ремонт автомобільного транспорту
Погоджено
Міністерством внутрішніх справ України
21 лютого 1994 р.
Затверджено
Міністерством транспорту України
6 квітня 1994 р.
(Витяг)
2. Підприємства технічної експлуатації
рухомого складу автотранспорту
2.1. Підприємства, що здійснюють технічну експлуатацію рухомого складу, поділяються на автотранспортні, автообслуговуючі та авторемонтні.
2.2. Автотранспортні підприємства (АТП) можуть бути комплексні та кооперовані.
2.2.1. Комплексні АТП здійснюють перевезення вантажів, пасажирів, виконують профілактичне обслуговування, ремонт, зберігання та ресурсне забезпечення рухомого складу.
2.2.2. Кооперовані АТП входять до складу комбінатів, об'єднань, корпорацій або інших організацій, що здійснюють часткову централізацію управління транспортною роботою, а також часткову або повну централізацію профілактичного обслуговування та ремонту рухомого складу.
2.3. Автообслуговуючі підприємства перевізних функцій не виконують, а призначені для виконання всього комплексу профілактичного обслуговування та ремонту рухомого складу або тільки його складових елементів. До них відносяться:
- бази централізованого технічного обслуговування та ремонту (БЦТО);
- станції технічного обслуговування (СТО);
- майстерні (цехи, дільниці) та інші спеціалізовані підприємства.
2.3.1. За типом рухомого складу БЦТО, СТО поділяються на такі, що обслуговують легковий, вантажний, не часто - змішаний. За розміщенням СТО поділяються на міські та дорожні.
2.3.2. Бази централізованого технічного обслуговування та ремонту (БЦТО), станції технічного обслуговування (СТО) призначені для виконання як окремих видів, так і всього комплексу профілактичних та ремонтних робіт рухомого складу, заміни та ремонту агрегатів, відновлення деталей, ремонту вузлів та систем автомобілів, які належать АТП і транспортним організаціям незалежно від форм власності, постачання запасними частинами та експлуатаційними матеріалами.
2.3.3. Майстерні (цехи, дільниці) спеціалізуються на певних видах ремонтних робіт як автомобіля в цілому, так і його складових частин, відновленні або виготовленні запасних частин.
2.3.4. Автозаправні станції (АЗС) здійснюють заправлення автомобілів паливом, мастилами та спеціальними рідинами, продаж запасних частин.
2.3.5. Ділерські пункти організовуються спільно з фірмами виготовлювачами для продажу через них певних моделей автомобілів (однієї або декількох). Ділерські пункти проводять передпродажне технічне обслуговування автомобілів, продаж запасних частин, усунення несправностей автомобілів у період гарантійного пробігу, а у деяких випадках - на весь період експлуатації. Через ділерські пункти фірми та заводи-виготовлювачі, як правило, розповсюджують рекламну і технічну інформацію про свої моделі.
2.3.6. Автостоянки призначені для зберігання рухомого складу і, за наявності певних виробничих приміщень і споруд, для виконання окремих видів профілактичного обслуговування та ремонту (прибирання, миття, мастильних робіт).
2.3.7. Мотелі та кемпінги призначені для забезпечення автотуристів інфраструктурою для їх відпочинку і зберігання рухомого складу, а також надання деяких послуг щодо миття, прибирання і ремонту автомобілів, які належать автотуристам.
2.4. Авторемонтні підприємства також відносяться до спеціалізованих виробництв і призначені для відновлення ресурсу роботи окремих агрегатів або повнокомплектних автомобілів. Від підприємств п. 2.3.3 відрізняються значно більшими обсягами виробництва і рівнем технологічних процесів.
2.5. Виробничо-технічна база (ВТБ) підприємств або підрозділів технічного обслуговування і ремонту рухомого складу автомобільного транспорту: будівлі, споруди, обладнання - повинна відповідати вимогам законів України, Відомчих будівельних норм - 01-89, Галузевих норм технологічного проектування АТП і СТО - 01-91, а також інших ГОСТІВ із системи стандартів безпеки праці, охорони природи, навколишнього середовища, інструкцій і правил проектування, що стосуються питань техніки безпеки й пожежобезпеки.
2.6. Наявність технологічного обладнання, його стан і характеристики повинні забезпечувати виконання нормативних вимог до технічного стану рухомого складу, що обслуговується, якості деталей, вузлів, механізмів, систем, що ремонтуються.
2.7. Номенклатура професій і кваліфікація персоналу, який виконує роботи по технічному обслуговуванню та ремонту автомобілів і їх складових частин, повинні відповідати вимогам "єдиного тарифно-кваліфікаційного довідника робіт і професій робітників". Розряди робітників повинні відповідати технологічним процесам, затвердженим в установленому порядку.
2.8. Власник (керівник) підприємства або підрозділу, що виконує профілактичне обслуговування та ремонт автомобілів і складових частин, зобов'язаний забезпечити виробництво потрібними ВТБ, технологічним обладнання і персоналом у відповідності до пунктів 2.5-2.7.
2.9. Підприємства або підрозділи, що виконують профілактичне обслуговування та ремонт автомобілів або його складових частин, повинні мати ліцензії на право виконання робіт, які видаються в установленому порядку відповідними державними органами.
Підставою для отримання ліцензій є виконання вимог п. 2.5, 2.6 і 2.7 цього "Положення...94". Невиконання зазначених вимог позбавляє підприємство права на отримання ліцензії або тягне за собою позбавлення раніше виданої ліцензії.
2.10. У додатку 1 наведений перелік основних матеріалів для обладнання виробничо-технічної бази АТП, СТО, зон та дільниць (не друкується).
2.11. Продукція автообслуговуючих і автотранспортних підприємств, яка використовується у складових частинах рухомого складу, що впливають на безпеку руху, токсичність відпрацьованих газів, забруднення навколишнього середовища, підлягає сертифікації.
2.12. Сертифікації підлягають роботи АТП, БЦТО, СТО по забезпеченню надійності гальмової системи рульового керування, нормативів токсичності відпрацьованих газів, активної та пасивної безпеки рухомого складу.
2.13. Сертифікація продукції та робіт, зазначених у п. 2.11, 2.12 передбачає перевірку та випробування з використанням контролюючих приладів і стендів, які дозволяють визначати відповідність розміру параметрам, що вимірюються нормативним документом.
2.14. Персонал, який використовують для виробництва сертифікованих робіт або випуску сертифікованої продукції, повинен відповідати вимогам "єдиного тарифно-кваліфікаційного довідника робіт і професій робітників", а також "Кваліфікаційного довідника посад службовців".
2.15. Гарантії на сертифіковані роботи і сертифіковану продукцію встановлюються чинними нормативними документами.
3. Вимоги до технічного стану рухомого складу,
що допускається до експлуатації
3.1. Технічний стан та обладнання рухомого складу автотранспорту повинні відповідати вимогам таких нормативних документів:
3.2. Автомобілі, які не відповідають вимогам нормативних документів, до експлуатації не допускаються.
3.3. Власники (керівники) підприємств, а також посадові особи, яким посадовою інструкцією поставлена за обов'язок організація виконання вимог вищенаведених нормативних документів або контролю за їх виконанням, несуть відповідно до законів України всю повноту відповідальності за експлуатацію РС, який не відповідає вимогам указаних нормативних документів, а також за наслідок, що наступив через це.
4. Система профілактичного обслуговування
та ремонту рухомого складу
4.0.1. Основою технічної політики, яка визначається цим "Положенням...94", є планово-попереджувальна система профілактичного обслуговування та ремонту. Система являє собою сукупність засобів, нормативно-технічної документації та виконавців, потрібних для забезпечення технічної справності рухомого складу.
4.0.2. Профілактичне обслуговування є технічним впливом, який виконується в плановому порядку, примусово, тобто обов'язково через визначені пробіги або відрізки часу роботи рухомого складу. Профілактичне обслуговування має на меті підтримання автомобіля у технічно справному стані та належному зовнішньому вигляді, забезпечення надійності, економічності, безпеки руху, захист навколишнього середовища та зменшення інтенсивності погіршення параметрів технічного стану.
4.0.3. Ремонт виконується за потребою, виявленою під час профілактичного обслуговування або в процесі експлуатації, та має на меті поновлення технічно справного стану.
4.0.4. Визначення технічного стану рухомого складу та його основних частин проводиться за допомогою контролю (діагностування), який виконує підвійну роль - є елементом системи управління технічним станом автомобілів та елементом технологічного процесу технічних впливів.
4.0.5. Мета контролю (діагностування) при профілактичному ремонті полягає:
- у визначенні дійсної потреби у виконанні планових робіт;
- у прогнозуванні (за змогою) моменту виникнення несправності (визначенні запасу ходу);
- в оцінці якості виконання робіт.
4.0.6. Мета контролю (діагностування) при ремонті полягає:
- в уточненні, відшукуванні причини несправності або поломки;
- у визначенні найбільш ефективного способу усунення несправності: на місці, зі зніманням або заміною агрегату, вузла, механізму;
- в оцінці якості виконання робіт.
4.1. Профілактичне обслуговування
4.1.1. Профілактичне обслуговування рухомого складу поділяється на такі види:
- передпродажна підготовка рухомого складу (ПП) (підготовка рухомого складу до введення в експлуатацію);
- щоденне обслуговування (ЩО);
- обов'язкові роботи профілактичного обслуговування (ОР).
4.1.2. Передпродажна підготовка (ПП) містить регулювальні, заправні, мастильні, кріпильні роботи з метою приведення автомобіля, що продається, у відповідність до вимог технічної документації на його складання та регулювання, а також параметрів технічної характеристики. ПП виконується за рахунок фірми (заводу)-виготовлювача на дилерських пунктах, а також на інших підприємствах, через які фірми (заводи)-виготовлювачі реалізують свою продукцію або здійснюють фірмове обслуговування. Придбавши автомобілі країн СНД, заводи-виготовлювачі яких не проводять ПП, власник транспортного засобу повинен провести підготовку його до введення в експлуатацію. У такому разі контроль технічного стану автомобіля, виконання робіт та перевірка їх якості виконуються засобами та силами покупця. Покупцю надається право домовитися у договорі на купівлю (якщо такий складається) про відшкодування витрат на підготовку автомобіля до введення в експлуатацію.
4.1.3. Щоденне обслуговування (ЩО) містить перевірку технічного стану рухомого складу, яка спрямована на забезпечення безпеки руху, а також роботи щодо підтримання належного зовнішнього вигляду, заправлення паливом, мастилами та охолоджувальною рідиною, а для деяких видів рухомого складу санітарну обробку кузова. ЩО виконується після роботи рухомого складу на лінії. Перевірка технічного стану проводиться також перед виїздом на лінію та при зміні водіїв на лінії. При міжміських, міжнародних перевезеннях перевірка технічного стану рухомого складу проводиться водієм щоденно перед початком руху. В разі виявлення несправності водій, за змогою, ліквідує її, за незмогою - оцінює її вплив на безпеку руху та приймає рішення щодо подальшого самостійного руху (до найближчого населеного пункту, СТО, кінцевого пункту маршруту) або виклику технічної допомоги.
4.1.4. Роботи ЩО виконуються водієм за рахунок підготовчо-заключного часу. Тривалість підготовчо-заключного часу залежить від переліку робіт, які повинен виконувати водій під час ЩО. Перелік робіт ЩО встановлюється розпорядженням керівника підприємства, в ньому також зазначається перелік несправностей, які повинні усуватися водієм під час ЩО, а також місце на підприємстві, де ці роботи повинні виконуватись.
У разі виявлення несправностей, які водій не має змоги або права усувати особисто, рухомий склад здається водієм у зону ремонту.
4.1.5. На великих підприємствах виконання прибирально-мийних, заправних, контрольно-оглядових робіт, санітарна обробка кузовів може виконуватись на спеціалізованих постах робітниками відповідних професій, внаслідок чого змінюється трудомісткість підготовчо-заключного часу водіїв.
4.2. Обов'язкові роботи
4.2.1. Технічні впливи, які виконуються в обов'язковому порядку примусово - після певного пробігу рухомого складу або годин чи днів роботи, називаються обов'язковими роботами (ОР).
ОР - профілактичні, мають на меті знизити інтенсивність спрацювання, запобігти поломкам, несправностям, відмовам механізмів під час процесу експлуатації, уникаючи зривання графіків перевезення пасажирів, вантажів та можливих дорожньо-транспортних пригод.
4.2.2. До ОР належать:
- контрольно-діагностичні, які виконуються у плановому порядку;
- мастильні;
- регулювальні;
- кріпильні;
- заміна агрегатів, вузлів, механізмів, деталей, яка виконується у плановому порядку;
- протикорозійний захист;
- підготування рухомого складу до сезону експлуатації;
- усунення несправностей, виявлених під час виконання вищевказаних робіт.
4.2.3. Контрольно-діагностичні ОР складаються з трьох етапів:
- контролю функціонування, тобто встановлення факту виконання об'єктом діагностування своїх функцій без їх кількісної оцінки (наприклад, для двигуна - пуск, випробування на різних навантажувально-швидкісних режимах);
- загального діагностування, тобто кількісної оцінки основних параметрів агрегатів, вузлів, механізмів за допомогою спеціальних діагностичних засобів;
- пошуку несправностей, тобто відшукування місця, причини, деталі (деталей), які викликали відхилення від параметрів, що вимагаються, або невиконання функцій.
4.2.4. Перелік ОР, їх періодичність, а також зміна переліку та періодичності залежно від тривалості експлуатації автомобіля (вік рухомого складу) фірми або заводи-виготовлювачі наводять у сервісних книжках, заводських інструкціях та інших документах.
Фірми (заводи)-виготовлювачі рухомого складу, постійно працюючи над підвищенням надійності та довговічності моделей, що випускаються, у процесі їх удосконалювання змінюють зміст і періодичність виконання ОР.
4.2.5. Обов'язкові роботи, які мають рівні інтервали їх виконання, фірми (заводи)-виготовлювачі групують у різні за змістом та інтервалом групи, тобто ОР-1, ОР-2... і т.д. Заводи-виготовлювачі країн СНД іменують їх ТО-1; ТО-2; СО. У США - А; В; С. Так само контрольно-діагностичні роботи, що входять до ОР-1; ОР-2... і т.д., іменуються Д-1; Д-2... і т.д.
4.2.6. Власнику транспортного засобу (керівнику підприємства) надається право залежно від складності дорожніх умов, інтенсивності експлуатації зменшувати (коректувати) періодичність виконання ОР та поповнювати їх перелік роботами, потреба виконання яких у примусовому порядку виявлена під час процесу експлуатації.
4.2.7. Обов'язкові роботи виконуються на спеціалізованих постах, лініях комплексного підприємства або на інших спеціалізованих підприємствах на договорних засадах (СТО, БЦТО).
4.2.8. Транспортний засіб після виконання ОР повинен мати ресурс, що забезпечить безвідмовну роботу на пробігу (терміні експлуатації) не менше, ніж до чергових ОР.
4.2.9. Власник (керівник) транспортного підприємства або підприємства, що виконує профілактичне обслуговування, а також службова особа, якій доручена організація технічної експлуатації рухомого складу, несуть всю повноту відповідальності за небажані наслідки, спричинені порушеннями термінів, об'ємів та якості виконання ОР.
4.3. Ремонт
4.3.1. У відповідності до призначення та об'єму робіт, що виконуються, ремонт поділяється на:
- поточний ремонт, у т.ч.:
- поточний ремонт повнокомплектного автомобіля (ПРА);
- поточний ремонт агрегату, вузла, механізму (ПР);
- капітальний ремонт, у т.ч.:
- капітальний ремонт повнокомплектного автомобіля (КРА);
- капітальний ремонт агрегату, вузла, механізму (КР);
- відновний ремонт деталі (В).
4.3.2. Поточний ремонт повнокомплектного автомобіля (ПРА), призначений для усунення несправностей, поломок, відмов, які виникли під час процесу експлуатації протягом інтервалу між виконанням ОР.
ПРА складається з таких технологічних елементів:
- діагностичних робіт, що мають на меті визначення причин, місця несправності, деталі (деталей), що спричинили несправність;
- визначення найбільш ефективного шляху усунення несправності;
- виконання робіт;
- контролю якості робіт.
ПРА виконується безпосередньо на автомобілі шляхом ремонту несправного агрегату, вузла, механізму або заміни несправного агрегату, вузла, механізму.
4.3.3. Поточний ремонт агрегату, вузла, механізму (ПР), знятого з автомобіля під час виконання ОР або ПРА, має на меті з мінімальними витратами коштів відновити спроможність агрегату, вузла, механізму виконувати свої функції, використовуючи ресурс, що залишився в ньому. ПР виконують шляхом заміни деталі (деталей), що відмовила, крім корпусних та основних.
ПР виконується на ремонтних дільницях автотранспортних підприємств для поповнення проміжних комор. Агрегати, вузли, механізми після ПР використовуються під час виконання ОР або ПРА за умови виконання вимог п. 4.2.8.
Агрегати, вузли, механізми, що відремонтовані поточним ремонтом, не можуть бути товарною продукцією, внаслідок чого виконувати поточний ремонт агрегатів, вузлів, механізмів на СТО, БЦТО допустимо в тому разі, якщо СТО, БЦТО взяли на себе виконання ОР для якого-небудь підприємства і тільки для рухомого складу цього підприємства.
4.3.4. Капітальний ремонт агрегатів, вузлів, механізмів (КР) має на меті відновлення їх функцій та ресурсу до рівня нових.
Капітально відремонтовані агрегати, вузли, механізми повинні відповідати вимогам технічної документації заводів-виготовлювачів.
4.3.5. КР виконується спеціалізованими підприємствами. Можливе виконання КР дільницями автотранспортних підприємств за умови виконання вимог п. 4.3.4.
4.3.6. Капітально відремонтовані агрегати, вузли, механізми використовуються під час виконання капітального ремонту повнокомплектних автомобілів як товарна продукція спеціалізованих підприємств.
4.3.7. Капітальний ремонт повнокомплектного автомобіля (КРА) проводиться в разі недоцільності або неможливості замінити застарілий або зношений автомобіль, експлуатація якого призводить до збитків.
КРА виконується у спеціалізованих підприємствах згідно з діючими нормативними документами або у виробничих підрозділах власника транспортних засобів шляхом заміни агрегатів, вузлів, механізмів на нові або капітально відремонтовані. КРА може виконуватись знеособленим або незнеособленим методом. Приймання рішення про потребу та місце виконання КРА надається власнику автомобіля (керівнику підприємства).
4.3.8. Відновний ремонт деталей (В) призначений для відновлення номінального розміру та якості зношених основних, корпусних та інших деталей.
Відновлені деталі повинні відповідати вимогам ТУ і робочих креслень заводів-виготовлювачів автомобілів, агрегатів, вузлів, механізмів.
Виконання В вимагає складних, сучасних технологій і, як правило, проводиться у спеціалізованих підприємствах.
4.4. Списання рухомого складу
4.4.1. За наявності запасних частин, можливостей придбувати або ремонтувати базові агрегати (рами, кабіни, кузови) автомобіль може підтримуватись у технічно справному стані достатньо тривалий час (більше 10-15-20 років). Виходячи з цього, критеріями доцільності списання рухомого складу повинні бути показники економічної неефективності його експлуатації (прибутки від експлуатації не покривають витрат на утримання автомобіля).
Цілком, певна інформація про економічну неефективність подальшої експлуатації рухомого складу може бути отримана тільки в разі функціонування у підприємстві системи обліку витрат і прибутків кожного автомобіля (помашинний облік).
4.4.2. Пропозиції щодо потреби списання рухомого складу подаються керівнику підприємства посадовими особами, які відповідають за технічну службу або за експлуатацію рухомого складу. Такі пропозиції повинні вміщувати економічне обгрунтування припинення експлуатації рухомого складу у підприємстві.
4.4.3. Право прийняття рішення про припинення експлуатації рухомого складу в підприємстві та подальше його списання або продаж належить власнику автотранспорту. Власник автотранспорту може делегувати це право керівнику підприємства, об'єднання.
4.4.4. Власник автотранспорту встановлює порядок списання та ліквідації рухомого складу.
5. Контроль за технічним станом рухомого складу
5.1. Експлуатація рухомого складу призводить до зміни його технічного стану і зростання вірогідності виникнення несправностей, відмов, поломок, наслідком яких можуть бути зривання графіків перевезення пасажирів, вантажів, забруднення навколишнього середовища, пошкодження вантажів, а в окремих випадках, за несприятливий збіг обставин, і дорожньо-транспортні пригоди зі значними матеріальними втратами.
5.2.3 метою запобігання виникнення несправностей, відмов та поломок, які спричинені неякісним виконанням профілактичного обслуговування та ремонту рухомого складу, у підприємствах, які займаються технічною експлуатацією рухомого складу автотранспорту, повинна ефективно функціонувати система контролю за його технічним станом (далі - система контролю).
5.3. Власник підприємства або особа, якій власником делеговано за контрактом керування підприємством, несе всю повноту відповідальності за неефективне функціонування системи контролю та шкоду, заподіяну внаслідок цього підприємству та оточенню.
5.4. Керівник підприємства має право визначати штати та організацію системи контролю, виходячи з умов роботи підприємства та його можливостей.
5.5. Керівник підприємства має право делегувати організацію і забезпечення функціонування системи контролю або окремих її елементів іншим працівникам підприємства за умови, що працівник за своєю кваліфікаційною характеристикою може бути допущений до виконання цієї роботи.
5.6. Система контролю повинна забезпечувати виконання таких функцій:
- перевірка технічного стану рухомого складу перед виїздом його на лінію;
- перевірка технічного стану рухомого складу під час його заїзду до місця стоянки або зберігання;
- облік рухомого складу під час виїзду на лінію та повернення;
- контроль технічного стану рухомого складу перед ставленням його для виконання технічних впливів;
- контроль якості виконання технічних впливів на рухомий склад;
- контроль за якістю продукції, що випускається виробничими дільницями підприємств;
- контроль за додержанням технологічної дисципліни;
- контроль за якістю профілактичного обслуговування та ремонту рухомого складу, його складових частин, виготовлення та відновлення запасних частин, які виконані іншими підприємствами;
- контроль за якістю експлуатаційних та ремонтних матеріалів, що надходять у підприємство;
- контроль за технологічною точністю обладнання, контрольновимірювальних приладів та інструментів;
- аналіз та виявлення причин відмов, поломок, несправностей рухомого складу, розроблення пропозицій щодо їх усунення.
5.7. Перевірка технічного стану рухомого складу перед виїздом на лінію виконується водієм перед отриманням дорожнього листа в обсязі, передбаченому ЩО та "єдиним тарифно-кваліфікаційним довідником робіт і професій робітників".
Водій не має права виїжджати на лінію на рухомому складі, який має несправності, що не допускають його експлуатацію.
5.8. Перевірка технічного стану рухомого складу під час його заїзду до місця стоянки або зберігання проводиться на спеціально обладнаному посту біля в'їзду на територію підприємства - контрольно-перепускному пункті (КПП) контролером-приймальником або механіком, якщо це поставлено йому за обов'язок і відображено у посадовій інструкції.
Перевірка технічного стану під час заїзду проводиться зовнішнім оглядом для перевірки комплектності рухомого складу (скло, фари, ліхтарі, дзеркала, склоочисники, вогнегасники і т.ін.) та виявлення пошкоджень, вм'ятин, ударів, подряпин, які рухомий склад міг дістати під час ДТП.
Перевіряються зазори у з'єднаннях рульової передачі, герметичність гальмових приводів автомобіля та причепа, знімаються дані спідометра, відмічається час заїзду. Опитується водій про помічені ним протягом робочої зміни несправності в агрегатах і вузлах автомобіля. За потреби та наявної можливості ці зауваження перевіряються. За результатами огляду, у відповідності до посадової інструкції, приймаються відповідні рішення.
5.9. Контролер-приймальник на КПП:
- фіксує час виїзду рухомого складу на лінію відміткою у дорожньому листі;
- під час заїзду рухомого складу відмічає у "Відомості приймання рухомого складу" технічний стан автомобіля і причепа, що приймаються, відмічає у дорожньому листі час заїзду і дані спідометра;
- на технічно несправний автомобіль виписує "Листок обліку ПО і ПР автомобіля". Виписування "Листка обліку..." може здійснюватись іншими способами та засобами за командою контролера-приймальника;
- направляє автомобіль залежно від його технічного стану до зони стоянки, зберігання або ремонту (можливе використання водія-перегонника).
5.10. Перед виконанням профілактичного обслуговування або поточного ремонту рухомий склад проходить огляд і, якщо потрібно, діагностування на відведених для цього постах. Пости мають бути обладнані засобами діагностики.
Перевірку рухомого складу на цих постах виконують контролери приймальники (оператори-діагности, техніки-діагности). Допускається виконання цієї функції майстром дільниці, обумовивши це у посадовій інструкції.
5.11. Контроль якості виконання профілактичного обслуговування та ремонту рухомого складу проводиться:
- на постах, спеціально відведених для цього. Пости мають бути обладнані засобами діагностики, можливе виконання;
- на постах для виконання робіт згідно з п. 5.10;
- безпосередньо на постах, де виконуються технічні впливи.
Перевірку якості виконаних робіт проводять контролери-приймальники (оператори-діагностики, техніки-діагностики). Допускається виконання цієї функції майстрами дільниці, обумовивши це у посадовій інструкції.
Водночас з перевіркою якості виконання технічних впливів перевіряється повнота і вірність заповнення "Листка обліку ПО і ПР автомобіля". Робиться відмітка про приймання робіт.
5.12. Особливо звертається увага на виконання робіт з агрегатами, які забезпечують безпеку руху:
- гальма і гальмовий привод;
- рульова передача і рульовий привод;
- шини (ремонт пошкоджень, тиск);
- буксирні пристрої, дишель причепа, страхувальний трос;
- газобалонна апаратура.
До виконання цих робіт допускаються тільки певні робітники, прізвища яких обумовлені у наказі (розпорядженні) по підприємству. У випадку, якщо роботи із зазначеними агрегатами, системами виконані іншими особами, приймати ці роботи заборонено. Про ці випадки приймальник робіт зобов'язаний доповідати керівнику підприємства рапортом.
5.13. Контроль якості продукції, що виготовляється дільницями автотранспортних підприємств, проводиться на дільницях з використанням установленого на них обладнання. Контроль і приймання продукції здійснює контролер-приймальник або майстер дільниці, якщо це обумовлено у його посадовій інструкції.
Приймання продукції до складів підприємства без контролю її якості забороняється.
5.14. Контроль за дотриманням технологічної дисципліни у виробництві здійснюють інженери-технологи, начальники та майстри виробництва. Відповідальність за дотримання технологічної дисципліни у відповідній галузі несуть:
- усі виконавці операцій ПО та ремонту;
- бригадири бригад ремонтних робітників;
- майстри дільниць і зон;
- інженери-технологи;
- начальники виробництва;
- головні інженери підприємств.
Виконавці, бригадири, майстри дільниць мають бути забезпечені потрібними технологічними документами.
За відсутності технологічних документів відповідальність з виконавців, бригадирів, майстрів за порушення дисципліни знімається.
5.15. Контроль за якістю ПО та ремонту рухомого складу та його складових частин, що виконуються іншими підприємствами, може мати вибірковий, періодичний або систематичний характер. Контроль проводиться силами та засобами підприємства-замовника, якщо не домовлені з виконавцем інші методи контролю.
Виконання цієї функції покладається за рішенням головного інженера підприємства на працівників виробництва із зазначенням цих обов'язків у посадовій інструкції.
5.16. На всі експлуатаційні та ремонтні матеріали, що надходять до підприємства, мають бути відповідні документи, які підтверджують їх сортність, марку, склад і т.ін. Контроль за їх якістю здійснює начальник служби матеріально-технічного забезпечення.
Придбання підприємством матеріалів, на які не можуть бути отримані названі документи, допускається тільки з дозволу головного інженера підприємства.
5.17. Контроль за технологічною точністю обладнання, контрольно-вимірювальних приладів та інструментів здійснюється службою головного механіка у порядку виконання технічного обслуговування обладнання, періодичної перевірки та атестації контрольно-вимірювальних приладів і періодичної перевірки міряльного інструменту. Відповідальність за своєчасне та якісне проведення зазначених робіт несе головний механік підприємства або особа, на яку посадовою Інструкцією покладено виконання цих робіт.
5.18. Аналіз та виявлення причин відмов, поломок, несправностей рухомого складу, розробка пропозицій щодо їх усунення виконуються керівником технічного відділу підприємства, за необхідності - з використанням спеціалістів інших організацій. Об'єкти, глибина і деталізація аналізу визначаються головним інженером підприємства. По закінченні аналізу керівник технічного відділу опрацьовує пропозиції усунення виявлених причин відмов, поломок, несправностей рухомого складу. Організація реалізації пропозицій здійснюється головним інженером підприємства.
5.19. Працівникам Державної автомобільної інспекції надане право перевірки в автотранспортних підприємствах організації системи контролю та її функціонування в галузі забезпечення безпеки руху та охорони навколишнього середовища.
5.20. Громадські організації допускаються до ознайомлення з окремими питаннями організації та функціонування системи контролю з дозволу керівника підприємства.
Тема: Безпека праці під час ТО і ремонту автомобілів
Технічне обслуговування й ремонт автомобілів виконують у призначених для цього місцях (на постах). На робочих місцях мають забезпечуватися безпечні умови для проведення робіт; обладнання, інструмент та прилади мають відповідати характеру виконуваної роботи й унеможливлювати травматизм.
У разі примусового переміщання автомобілів з поста на пост потокової лінії передбачають світлову або звукову сигналізацію. Після сигналу про початок пересування конвеєра робітники повинні покинути робочі місця, вийти з оглядової ями й відійти від конвеєра. Для екстреного зупинення конвеєра на кожному посту є кнопки «Стоп».
Електричне обладнання діагностичного стенда з біговими барабанами (пульт керування, апаратні шафи, блоки барабанів тощо) має бути надійно заземлене.
Наприкінці зміни слід вимкнути рубильник стенда, закрити крани паливних баків, перекрити вентиль подачі стисненого повітря.
Під час роботи під перекинутою кабіною автомобіля положення обмежувача треба зафіксувати защіпкою, в разі опускання кабіни - надійно закрити запірний механізм і правильно встановити запобіжний крюк у пазу опорної балки.
Пуск двигуна треба здійснювати стартером, як виняток - пусковою рукояткою. Аби уникнути травмування кисті, рукоятку слід брати так, щоб всі пальці правої руки розташовувалися по один бік ручки. Повертати колінчастий вал треба тільки знизу вгору, довкола - забороняється.Пускати газовий двигун, якщо є витікання газу, не допускається.
Регулювальні роботи з двигуном, що працює, слід виконувати на спеціальному посту з місцевою вентиляцією для видаляння відпрацьованих газів.
Забороняється підтягувати деталі газобалонного обладнання автомобіля й виконувати інший ремонт, якщо у вузлах і трубопроводах є газ під тиском.
У приміщеннях для ТО й ремонту автомобілів забороняється залишати порожню тару з паливом та мастильними матеріалами. Розлите паливо або оливу слід негайно прибрати, використовуючи пісок чи тирсу. Після завершення роботи всі використані ганчірки слід скласти у спеціальну тару.
Технічне обслуговування й ремонт приладів системи живлення, знятих з автомобіля, виконують у цеху (на дільниці). Біля ванни, для миття деталей системи живлення, біля верстаків для розбирання-складання, перевірки й регулювання приладів, а також біля токарного верстата мають бути вентиляційні відсмоктування.
Роботи, пов'язані із зачищанням деталей перед паянням та лудінням, виконують на робочих місцях, обладнаних місцевою вентиляцією. Паливні баки й тару з-під пальних сумішей перед ремонтом треба промити гарячою водою, пропарити гострою парою, промити каустичною содою та просушити гарячим повітрям. Перед паянням і заварюванням слід відкрити пробки.
Займання треба гасити за допомогою вогнегасників, піском або струменем розпиленої води. Балони з газом слід поливати холодною водою, щоб запобігти підвищенню тиску в них.
Роботи з акумуляторними батареями треба виконувати в ізольованих приміщеннях із дотриманням вимог безпеки, викладених нижче.
Усі особи, які причетні до роботи з акумуляторними батареями, повинні пройти спеціальний інструктаж з техніки безпеки.
Уразі потрапляння електроліту або кислоти на шкіру необхідно негайно змити їх водою, 10%-м розчином соди чи нашатирного спирту.
Закінчивши роботу з акумуляторами, перед уживанням їжі треба прополоскати рот і старанно вимити руки гарячою водою з милом. Заходити в їдальню в спецодязі забороняється. Щоденно вранці, після завершення роботи та ввечері необхідно чистити зуби.
На робочих місцях мають бути аптечки з йодом, ватою, марлею та 10%-м розчинами соди й нашатирного спирту.
Питну воду слід зберігати у шафі в закритій місткості.
У робочих приміщеннях забороняється палити, а також зберігати продукти харчування.
Після закінчення кожної зміни треба робити вологе прибирання підлог, столів, верстаків та інструментів.
При акумуляторному цеху мають бути обладнані роздягальня та вмивальня з шафами для зберігання домашнього одягу й окремо - спецодягу.
Забороняється транспортувати акумуляторні батареї вручну (незалежно від кількості їх).
В акумуляторних та зарядних приміщеннях мають бути вікна, що відчиняються.
Підлога робочого приміщення (акумуляторного цеху), де ремонтуються акумулятори, має бути цегляною або бетонною, не слизькою й без вибоїн.
Покриття стелажів, стін і підлоги має бути кислототривким, а поверхня стін, крім того, - гладенькою по висоті не менше ніж 1,75 м.
Поверхня робочих столів, на яких розбирають і складають акумуляторні батареї, має бути рівною, без щілин і тріщин, а покриття - стійким проти сірчаної кислоти.
Свинцевий порошок, глет і сурик для акумуляторних майстерень треба доставляти в металевій, герметичне закритій тарі й зберігати в окремому приміщенні.
Непридатні пластини, свинець та його відходи треба зберігати в окремому ящику, що закривається.
В акумуляторному цеху обов'язково має бути водопровід, щоб у разі потрапляння кислоти на шкіру робітника її можна було б змити.
Електропроводка в акумуляторній майстерні має бути герметичною й виконуватися в металевих трубах, покритих асфальтовим лаком. Освітлення акумуляторного цеху й зарядного приміщення, а також зарядна установка мають бути вибухобезпечного виконання. В зарядному приміщенні не можна встановлювати генератори й відкриті електродвигуни. Воно має бути обладнане припливно-витяжною вентиляцією для видаляння шкідливих газів, що виділяються під час заряджання акумуляторів. У приміщенні категорично забороняється палити й користуватися відкритим вогнем, оскільки водень, який виділяється під час заряджання акумуляторів, сполучаючися з киснем повітря, утворює гримучий газ, що легко вибухає.
Тріщини в мастиці акумуляторних баків треба згладжувати металевим предметом. Не допускається розплавляти мастику на діючій батареї полум'ям паяльної лампи, оскільки гази, що містяться в акумуляторі, можуть вибухнути.
Електроліт слід приготовляти вливанням тонкої струминки кислоти в дистильовану воду. Не можна вливати воду в сірчану кислоту, оскільки розчинення кислоти у воді супроводжується розбризкуванням, що може спричинити тяжкі опіки. Забороняється приготовляти електроліт у скляній нетермостійкій посудині, оскільки вона може луснути від теплоти, яка виділяється в процесі розчинення сірчаної кислоти. Зберігати кислоту й електроліт допускається тільки в спеціально відведеному приміщенні, підлога та стіни якого мають кислототривке покриття.
У приміщенні для заряджання акумуляторних батарей не можна виконувати інші роботи (розбирання, складання, ремонт). Температура в цьому приміщенні має бути не нижчою ніж +10 °С.
У зарядному приміщенні мають бути вмивальники, бочки з 10%-м розчином питної соди, а також протипожежні засоби (вогнегасники, вода, пісок, лопати тощо).
Одночасне заряджання понад десяти акумуляторних батарей має відбуватися в ізольованих приміщеннях зі стелажами.
Одночасне заряджання менше ніж десяти акумуляторних батарей можна виконувати в приміщеннях ремонтних цехів, але акумуляторні батареї обов'язково треба встановлювати у витяжній шафі. Будова шаф має внеможливлювати просочування водню в приміщення.
Під час заряджання акумуляторних батарей не можна користуватися навантажувальною вилкою.
З'єднувати акумуляторні батареї, що заряджаються, треба за допомогою освинцьованих затискачів, які щільно прилягають і виключають можливість іскріння. Забороняється з'єднувати акумуляторні батареї дротом. Зварювальні, бляшано-кузовні, фарбувальні роботи слід виконувати в окремих ізольованих приміщеннях, обладнаних припливно-витяжною вентиляцією.
Демонтаж і монтаж шин автомобілів слід здійснювати на спеціально відведених місцях (постах). Перед демонтажем шини потрібно випустити повітря з камери. Під час накачування необхідно стежити за показами манометра, не допускаючи підвищення тиску повітря в шині понад установлену норму.
Миття автомобілів, агрегатів і деталей здійснюють на мийній дільниці, підлога якої має вологостійке покриття та уклон для стікання рідини. Дільницю обладнують припливно-витяжною вентиляцією, а мийні ванни - витяжними зонтами. Перед приготуванням і використанням мийних розчинів слід надягти гумові фартух, чоботи, рукавички, а також захисні окуляри.
Пожежна безпека. Пожежі на автопідприємствах можуть виникнути з таких причин:
- порушення правил використання відкритого вогню, електричної енергії;
- виконання зварювальних робіт у приміщеннях і на територіях, захаращених пальними матеріалами;
- використання непідготовленої техніки в пожежонебезпечних місцях;
- експлуатація несправних систем опалення, електродвигунів електронагрівальних приладів;
- порушення норм зберігання пожежонебезпечних несумісних матеріалів, вибухонебезпечних речовин.
До організаційних протипожежних заходів належать:
- розроблення правил та інструкцій з протипожежної безпеки;
- організація вивчення цих правил та інструкцій;
- визначення терміну, місця й порядку проведення протипожежного інструктажу;
- організація належного протипожежного нагляду за об'єктами.
За здійснення всіх протипожежних заходів на АТП відповідає особа з числа керівного складу.
Кожне автопідприємство повинне мати первинні засоби пожежогасіння, до яких належать:
- 4- внутрішні крани з пожежними рукавами й стволами;
- вогнегасники пінні, вуглекислотні, порошкові;
- ящики й бочки з піском, водою;
- покривала азбестові, повстяно-азбестові, брезентові;
- ручний пожежний інструмент (гаки, ломи, сокири, пожежні відра тощо).
Правила застосування пожежного інструменту й вогнегасників вивчають на вступному та наступних (на робочому місці) інструктажах.
Усі проходи, проїзди й територію не можна захаращувати. Кількість автомобілів на стоянці має не перевищувати допустимої.
На території стоянки автомобілів забороняється: виконувати будь-які роботи із застосуванням відкритого вогню; заряджати акумуляторні батареї; палити; зберігати використаний обтирний матеріал.
Розлите паливо або оливу треба негайно прибрати.
Водій повинен стежити за справністю електрообладнання й пересвідчуватися, що не підтікає паливо.
У разі спалахування автомобіля треба негайно видалити його із зони стоянки й вжити заходів для гасіння пожежі.
Якщо виникла пожежа, слід викликати пожежну команду.
Тема: Технічна характеристика двигуна
У технічній характеристиці двигуна вказують такі параметри:
1. Число цилндрів
2. Робочий обєм , л
3. Діаметр циліндрів , мм
4. Хід поршня ,мм
5. Ступінь стиску
6. Номінальна потужність, квт
7. Число обертів колінвала при номінальній потужності
8. Найбільший крутний момент , н * м
9.Порядок роботи циліндрів
10. Габаритні розміри,мм
11.Суха маса двигуна,кг
На вантажних автомобілях великої вантажопідйомності застосовують дизельні 6 ,8 циліндрові двигуни. На карєрних самоскидах - дизель - генераторна установка, яка живить електродвигуни, які приводять в рух ведучі колеса.
Тема: Переваги і недоліки дизельних двигунів
Суперечки між прихильниками бензинових та дизельних двигунів потроху вщухають. Навіть не зважаючи на гучну справу Volkswagen, яка наробила галасу у 2015 році, коли німецький концерн зізнався в заниженні рівня викидів своїх автівок із дизельними двигунами, прихильників «дизеля» не поменшало. Адже з кожним роком дизельні автомобілі поступово й упевнено позбуваються своїх непривабливих особливостей. Вони стали тихішими, економнішими та екологічнішими, тому цілком відповідають усім сучасним стандартам.
Головним аргументом проти дизельних двигунів була недостатня швидкість та високий рівень шуму. Навіть за умови хорошого крутного моменту на низьких обертах автомобіль не міг досягти високої швидкості. Такий варіант був прийнятним для комерційних автівок, але не для звичайних легкових авто, які пересуваються в межах міста чи трасами. Та сучасні технології, за якими розробляють унікальні системи вприскування, турбіни тощо, допомогли дизелям покращити свої швидкісні характеристики й позмагатися на рівних зі своїми бензиновими побратимами. Тож розглянемо детальніше основні переваги та недоліки сучасних дизельних двигунів.
Переваги сучасних дизельних двигунів
- Низький рівень витрати палива. У порівнянні з бензиновим двигуном, дизельний споживає утричі менше пального, що дозволяє суттєво зекономити.
- Впевнений розгін. Високий крутний момент забезпечує автомобілю впевнений старт, рівномірний розгін і стабільну тягу.
- Довший робочий ресурс. Дизельний мотор зазвичай працює удвічі довше, аніж бензиновий. За умови регулярного обслуговування транспортного засобу його пробіг становитиме близько 400 тисяч кілометрів.
- Високий коефіцієнт корисної дії. Потужність і віддача дизельного двигуна вища за аналогічні характеристики бензинового. Конструктивні особливості камери згоряння та спосіб займання дозволяють виробляти більше енергії й економніше витрачати паливо - під час згоряння палива менше енергії витрачається даремно.
- Невисокий рівень токсичних викидів. Новітні системи перероблювання палива дозволили «дизелю» позбутися звання брудного транспортного засобу. Нижчий рівень витрати палива й ефективність його перероблювання роблять автомобільні вихлопи менш токсичними.
Недоліки сучасних дизельних двигунів
- Висока вартість на первинному автомобільному ринку. Вартість нового дизельного автомобіля приблизно на третину вища за вартість бензинового. Звичайно ж, можна окупити цю різницю під час подальшої експлуатації транспортного засобу, наприклад, завдяки нижчій витраті палива. Але якщо автомобіль використовують не часто, то процес окупності буде досить тривалим.
- Низька вартість на вторинному автомобільному ринку. Продати уживаний дизельний автомобіль за вигідною ціною набагато складніше, ніж бензиновий. Особливо, якщо в автомобіля великий пробіг.
- Дорогий ремонт. Це ще один недолік, на який звертають увагу покупці під час придбання транспортного засобу як на первинному, так і на вторинному ринку. Придбання запчастин для бензинових автівок також недешеве задоволення, але ремонт «дизелів» ще дорожчий.
- Довготривалий прогрів двигуна взимку. Економічна витрата пального й високий коефіцієнт корисної дії роблять дизельний двигун холоднішим. А тому тривалість прогріву двигуна в холодну пору року довша, ніж в автомобілів на бензині. Салон автомобіля також вимагатиме довшого прогріву. Зазвичай власники дизельних автівок використовують додаткове кліматичне оснащення, але це також зайві кошти.
- Тема: Вимірювання компресії в циліндрах двигуна
Одна з причин зниження потужності автомобіля - зменшення компресії двигуна. Розповімо як перевірити компресію в циліндрах двигуна за допомогою компресометра і без нього.
Як перевірити компресію без компресометра
Є два способи для вимірювання компресії, якими ви можете скористатися: точне вимірювання - компресометром і приблизне - вручну. Для останнього способу вимірювання потрібні певний навик, але в той же час немає нічого складного в ньому.
Виверніть всі свічки, окрім свічки першого циліндра, і повертайте колінчастий вал двигуна до тих пір, поки в першому циліндрі не закінчиться такт стиснення (визначити це можна за збігом міток). Потім по черзі викручуйте свічки в інші циліндри і також повертайте колінчастий вал. Зрозуміти, в якому циліндрі компресія знижена, можна, порівнюючи зусилля, прикладені для прокручування коленвала.
Згоден, що це вимірювання досить умовне, оскільки воно пов'язано з суб'єктивними особливостями людської фізіології. Тому краще скористатися компрессометром. Необхідне значення компресії для свого автомобіля ви можете дізнатися з техпаспорта.Як виміряти компресію за допомогою компресометра?
- Заведіть автомобіль і прогрійте до робочої температури.
- Виверніть свічки запалювання.
- Попросіть допомогти, оскільки обов'язковою умовою вимірювання є повне відкриття дросельної заслінки, а помічник буде включати стартер, до кінця вичавивши педаль газу.
- Наконечник компрессометра щільно вставити в отвір свічки запалювання, переконайтеся, що з'єднання надійно.
- Увімкніть стартер і "крутить" двигун, поки показання манометра не припинять зростати (зазвичай 2-3 секунди). Перевірка компресії в циліндрах виконується тільки при повністю зарядженому акумуляторі.
- Вимкніть стартер, вважайте показання приладу. Вимірювання проводиться у всіх циліндрах.
- Не забувайте видаляти повітря з компрессометра після кожного виміру. Якщо у вас вийшли дані, які відрізняються від норми, повторіть вимірювання на даному циліндрі.
Різниця показників компрессометра між циліндрами не повинна перевищувати 1 атм для бензинових двигунів , 2 атм для дизельних двигунів.
Перевірка компресії і знос поршневих кілець
Втрата компресії в циліндрах двигуна залежить від стану деталей мотора і зокрема від зносу поршневих кілець. Є один спосіб перевірити технічний стан кілець. Назвемо цей варіант "масляна перевірка". Для даного виду визначення несправностей нам і потрібно раніше згадані в інструментах шприц і машинне масло.
Введіть в ті циліндри, де знижена компресія, 10-30 мл моторного масла. Закрийте свічковий отвір, зробіть кілька оборотів коленвала, щоб масло поширилося по циліндру, а потім знову виміряйте компресію.
Тепер необхідно порівнювати свідчення компрессометра до і після.
- Якщо компресія значно підвищилася або дуже близька до норми, значить, негерметичні внаслідок зносу як правило поршневі кільця циліндри.
- Якщо компресія підвищиться незначно - негерметичні клапани і поршневі кільця або пошкоджена прокладка головки блоку циліндрів.
- Якщо компресія залишилася незмінною, значить, негерметичні клапани і потрібно притирання клапанів.
- Тема: Система охолодження
-
1. Призначення і класифікація систем охолодження.
2. Схеми роботи систем охолодження.
3. Будова механізмів систем охолодження.
4. Охолоджувальні рідини.
1. Призначення. Система охолодження служить для примусового автоматичного регулювання відведення зайвої теплоти від деталей двигуна в навколишнє середовище.
. На сучасних автотракторних не адіабатних двигунах застосовується закрита система охолодження з примусовою циркуляцією рідини і повітряна система охолодження. На сьогодні термосифонною циркуляцією рідини обладнані тільки пускові двигуни тракторів.
В охолоджувальній сорочці і радіаторі закритої системи тиск дещо вищий від атмосферного, відповідно вища і температура кипіння рідини. Закрита система є більш досконалою і застосовується на всіх сучасних автомобільних двигунах.
На сучасних автотранспортних двигунах в основному застосовується закрита система охолодження з примусовою циркуляцією рідини.
У двигунах сучасних автомобілів і тракторів застосовують як рідинну, так і повітряну системи охолодження.
Залежно від типу двигуна температура газів у середині циліндрів в період згоряння робочої суміші досягає 2000...2500 °С.
Гази, які мають таку високу температуру, сильно нагрівають деталі двигуна, у результаті чого нормальна робота його може порушитись.
Сильне нагрівання двигуна може викликати зниження потужності внаслідок погіршення наповнення циліндрів, самозапалення суміші і детонацію, посилення спрацювання, заїдання і поломку деталей внаслідок порушення нормальних проміжків і зниження механічних властивостей матеріалів.
Для забезпечення нормальної роботи не адіабатного двигуна необхідно охолоджувати деталі, відводячи від них зайву теплоту в навколишнє середовище або безпосередньо, або за допомогою проміжного тіла, наприклад низькозамерзаючої рідини (антифризу). На охолодження двигуна витрачається близько 30% теплової енергії палива, тому охолодження повинно бути обмеженим.
Під час збільшення охолодження (при переохолодженні) деталей двигуна, які обмежують внутрішньоциліндровий простір, збільшуються витрати теплоти в навколишнє середовище, погіршується випаровування палива, внаслідок згущення мастила збільшуються втрати на тертя. Все це призводить до зниження потужності і погіршення економічності двигуна, а в дизельних двигунах, крім цього, до засмолення поршнів, поршневих кілець і випускних клапанів.
Таким чином, як перегрівання, так і переохолодження порушують нормальну роботу двигуна.
2. Теплота від деталей відводиться в атмосферу. Це втрати теплової енергії, значення яких залежить від типу двигуна, його конструкції і способу охолодження. У поршневих двигунах застосовують два способи охолодження. В першому випадку тепло від стінок передається рідині, а від неї повітрю. У другому випадку - від стінок циліндрів прямо повітрю.
Система охолодження працює наступним чином: водяна сорочка-радіатор-водяна сорочка. Температура охолоджуючої води працюючого двигуна повинна бути в межах 80...95°С. Для забезпечення необхідного температурного стану двигун має ряд пристроїв, деталей і приладів, об'єднаних в систему охолодження.
Сукупність пристроїв, які забезпечують підведення охолодженого середовища до нагрітих деталей двигуна і відведення від них у навколишнє середовище зайвої теплоти, являють собою систему охолодження.
Надійним є рідинне охолодження, при якому рідина циркулює в сорочці блока і омиває циліндри. Залежно від способу циркуляції охолоджуючої води, розрізняють дві системи охолодження (рис. 33): термосифонну і примусову.
Термосифонна - це така система охолодження двигуна, коли циркуляція води відбувається внаслідок різниці щільності холодної і гарячої води. Як недолік, необхідно збільшувати місткість для рідини, забезпечувати точність її рівня.
У примусовій системі охолодження циркуляція води створюється центробіжним насосом. Тоді, крім радіатора, в систему входить водяний центробіжний насос, термостат, дистанційний покажчик температури, розширювачі об'єму рідини. Різниця температур холодної і гарячої води не перевищує 10°С. Заслуговує на увагу такий елемент, як термостат. Він призначений для перекриття руху рідини за малим чи великим колами, в залежності від температури двигуна.
3. У загальному випадку у закриту рідинну систему охолодження з примусовою циркуляцією рідини входять такі основні елементи: рідинний насос 17 із розподільною трубою 18; охолоджувальні сорочки головки 8 і блока циліндрів 9; нижній 10 і верхній 7 з'єднувальні патрубки з шлангами; радіатор з пароповітряними клапанами і розширювальним бачком; жалюзі радіатора; вентилятор; автоматична муфта виключення лопатей вентилятора; термостат; зливні краники; прилади для контролю температури води. Навколо циліндрів двигуна та їхніх головок є простір (охолоджувальні сорочки), який заповнюється охолодженою рідиною. Охолоджувальна сорочка з'єднана патрубками 7, 10 з радіатором 1 - пристроєм для охолодження нагрітої рідини. Радіатор і сорочка заповнюється рідиною через заливну горловину, яка закривається кришкою 5. Кришка має клапани, через які внутрішня порожнина системи охолодження контактує з атмосферою.
У закритих системах охолодження підтримується надлишковий тиск (до 0,02 МПа), в результаті чого температура кипіння охолоджувальної рідини підвищується до 120°С. Пара або рідина при надлишковому тиску відводиться по трубці 6 в розширювальний бачок. Закриті системи охолодження більш компактні, ніж відкриті, тобто такі, які безпосередньо контактують з атмосферою і рідше потребують дозаправки рідиною.
Примусова циркуляція рідини в системі утворюється насосом який приводиться в роботу від колінчастого вала двигуна шківом. Рідина стикається з нагрітими стінками циліндрів і головки, нагрівається і через верхній патрубок надходить у верхній бачок радіатора . По трубках радіатора , які обдуваються потоком повітря, рідина проходить у нижній бачок радіатора і охолоджується. Рух повітря через радіатор забезпечується вентилятором 2 і зустрічним потоком повітря під час руху автомобіля. Охолоджена рідина через нижній патрубок надходить в насос і від нього по водорозподільній трубі (каналу) знову підводиться до найбільш нагрітих ділянок кожного циліндра. Водорозподільна труба (канал) дозволяє рівномірно охолоджувати всі деталі незалежно від їхньої віддаленості від насоса. Таким чином, в системі охолодження відбувається безперервна циркуляція охолоджувальної рідини.
Температура охолоджувальної рідини контролюється термометром. Оптимальним температурним режимом двигуна є такий, при якому температура охолоджувальної рідини в головці блока циліндрів дорівнює 80...100°С. Для швидкого прогріву двигуна, особливо після його пуску, в системі охолодження встановлюють термостат 16. Коли двигун не прогрітий, клапан термостата закритий і рідина із сорочки охолодження не може попасти в радіатор (у велике коло циркуляції).
При закритому клапані термостата рідина поступає до насоса через трубку (мале коло циркуляції). Оскільки двигун в такому випадку охолоджується лише частиною рідини, яка заповнює систему, то ця рідина швидко нагрівається. Потім клапан термостата відкривається і двигун охолоджується всією рідиною, яка циркулює по великому колу. Прохідний переріз клапана термостата і кількість рідини, яка надходить у радіатор, збільшуються з підвищенням температури, чим у визначених межах автоматично регулюється температурний режим двигуна.
Оптимальний температурний режим двигуна підтримується, в основному, зміною інтенсивності повітряного потоку, який проходить через радіатор.
За допомогою жалюзі змінюється кількість повітря, яке проходить через радіатор, а тим самим і інтенсивність охолодження. Інтенсивність повітряного потоку може бути змінена також за допомогою вентилятора з автоматично змінюваним кроком лопаті вентилятора. На деяких двигунах за допомогою гідравлічних, електричних муфт або електродвигуна вентилятор включається в роботу тільки після прогріву двигуна. Рідина із системи охолодження зливається через крани, встановлені в нижній точці системи охолодження (радіаторі і в блоці циліндрів). Однією з особливостей системи охолодження сучасного двигуна автомобіля є наявність розширювального бачка, розміщеного у вищій точці системи.
Розширювальний бачок, який сполучається з атмосферою, заповнений охолоджувальною рідиною і з'єднаний трубкою з наливною горловиною радіатора 1. При відкриванні випускного (парового) клапана, який є в пробці заливної горловини, зайва рідина чи пара відводиться в розширювальний бачок. При зменшенні об'єму охолоджувальної рідини (наприклад, при її охолодженні) у пробці відкривається впускний клапан і рідина із розширювального бачка повертається в радіатор. Таким чином, в системі підтримується постійний об'єм циркулюючої рідини.
Друга особливість системи охолодження сучасного двигуна полягає у способі підтримки оптимального температурного режиму, який забезпечується двоклапанним термостатом 14. Коли двигун не прогрітий, нижній клапан термостата закритий і охолоджувальна рідина не проходить через радіатор . Внаслідок циркуляції частини рідини двигун швидко прогрівається. Коли двигун прогрітий, верхній клапан термостата закритий, а нижній відкритий. У такому випадку більша частина рідини із сорочки головки блока попадає в радіатор 1, охолоджується в ньому, а потім по трубопроводу і через відкритий нижній клапан термостата надходить в насос.
Менша частина рідини, як і на непрогрітому двигуні, циркулює через впускний трубопровід, і опалювач салону. В деякому інтервалі температур обидва клапани термостата відкриті і рідина циркулює одночасно по двох колах. Кількість рухомої рідини в кожному колі циркуляції залежить від ступеня відкриття того чи іншого клапана, чим забезпечується автоматичне підтримування оптимального температурного режиму двигуна.
Радіатор є теплообмінником, в якому теплота від води передається потокові повітря. У верхньому бачку радіатора є горловина , через яку система заповнюється охолоджувальною рідиною. Горловина герметично закрита пробкою яка забезпечена двома клапанами. У нижньому бачку радіатора встановлений кран для зливу рідини із системи. Верхній і нижній бачки сполучаються рядами плоских трубок з припаяними до них пластинами, які створюють необхідну охолоджувальну поверхню. Жалюзі радіатора повертаються за допомогою рукоятки, внаслідок чого змінюється витрата повітря через радіатор, чим підтримується тепловий режим двигуна. На деяких двигунах управління жалюзями радіатора відбувається автоматично. Охолоджувальна рідина із охолоджувальної сорочки поступає в радіатор через трубу , а відводиться з нього через трубку . Радіатор закріплений на рамі автомобіля спереду двигуна на резинових подушках.
Рідинний насос відцентрового типу забезпечує циркуляцію рідини в системі охолодження. Вал насоса обертається у двох кулькових підшипниках, які забезпечені сальниками для збереження змащувального матеріалу. На одному кінці вала закріплена пластмасова крильчатка з металевою втулкою. У крильчатці встановлено саморухомий сальник, текстолітова шайба якого, обертаючись, притискається пружиною до торця корпуса підшипників. Саморухомий сальник перешкоджає витіканню рідини із насоса. На другому кінці вала розміщена маточина приводу рідинного насоса і вентилятора. До маточини болтами прикріплений шків вентилятора.
Привод рідинного насоса і вентилятора здійснюється клиноподібним пасом. При обертанні вала насоса рідина захоплюється лопатями крильчатки і направляється до вихідного патрубка. При частоті обертання колінчастого вала двигуна 3000 хв-1 подача насоса складає 240 л/хв.
Термостат є автоматичним клапаном, здатним прискорювати прогрів двигуна і регулювати в означених межах кількість рідини, яка проходить через радіатор. Термостати бувають рідинними і з твердими наповнювачами. Термостат із твердим наповнювачем ( має товстостінний балон заповнений сумішшю церезину (нафтового воску) з мідним порошком. Над балоном розміщена напрямляюча втулка з отвором для штока . Втулка відділена від балона резиновою діафрагмою . Шток зв'язаний коромислом із клапаном . Коли двигун не прогрітий, заслінка закрита і охолодна рідина не надходить в радіатор. При нагріванні церезин плавиться, об'єм його збільшується, внаслідок чого діафрагма буфер і шток пересуваються вверх, пружина розтягується і клапан 1 відкривається. Рідина починає циркулювати через радіатор (велике коло циркуляції). Клапан термостата починає відкриватися при температурі охолоджувальної рідини 70±2°С, повністю заслінка відкривається при температурі 83±2 °С. В інтервалі вказаних температур площа прохідного отвору термостата збільшується з підвищенням температури, внаслідок чого автоматично збільшується кількість рідини, яка надходить в радіатор.
У термостатах із рідинним наповнювачем чутливий елемент (гофрований циліндр із тонкої латуні) - заповнений рідиною, яка легко випаровується, сумішшю дистильованої води і етилового спирту. Коли система охолодження не прогріта, тиск у циліндрі знижується і він знаходиться в стиснутому стані, закриваючи клапан термостата. При нагріванні рідини в циліндрі термостата до певної температури її тиск підвищується настільки, що циліндр розширюється і клапан термостата відкривається.
Термостати з твердим наповнювачем мають більшу механічну міцність порівняно з термостатами з рідинним наповнювачем, що дозволяє застосовувати їх у закритих системах охолодження з великим надлишковим тиском.
Вентилятор служить для підвищення швидкості і кількості повітря, яке проходить через радіатор. Вентилятор встановлюється, як правило, за радіатором. Лопаті вентилятора ) кріпляться заклепками до хрестовини. Продуктивність вентилятора залежить від діаметра, кількості і кута нахилу лопатей, а також частоти обертання вала. На вітчизняних автомобільних двигунах вентилятори мають чотири, шість або вісім лопатей. Лопаті виготовляються з листової сталі або з пластмаси. Кут нахилу лопатей до площини обертання складає 35...40°С. Для підвищення ефективності роботи вентилятора його інколи розміщають в направляючому кожусі, закріпленому на радіаторі.
4. Охолоджувальні рідини. До недавнього часу як охолоджувальну рідину часто застосовували воду, яка має високу теплоємність. Однак використання води в системі охолодження зв'язані з накипанням і корозією стінок охолоджувальної сорочки і небезпекою замерзання в зимових умовах роботи. З цієї точки зору мають переваги низькозамерзаючі рідини-антифризи, які є етиленгліколевими сумішами.
У системах охолодження сучасних двигунів застосовуються низькозамерзаючі рідини типу "Тосол А", "Тосол А-40" і "Тосол А-60". Основою низькозамерзаючих рідин є етиленгліколь. Антифризи "А-40" і "А-60" крім концентрованого етиленгліколя мають у своєму складі різні присадки, наприклад такі, як протипінні, протикорозійні та інші.
Тема : Система живлення дизельного двигуна
На відміну від карбюраторних двигунів, у циліндри яких надходить з карбюратора готова пальна суміш, у дизелів пальна суміш утворюється безпосередньо в циліндрах, куди паливо і повітря подаються окремо. Ця відмінність визначає особливості будови системи живлення дизелів
Внаслідок особливостей робочого процесу і головним чином застосування високого ступеня стиску дизелі вигідно відрізняються від карбюраторних двигунів меншою (на 30-35 %) витратою палива. Цим пояснюється широке застосування дизелів на важких вантажних автомобілях.
На дизельні автомобілі МАЗ, КраЗ встановлюють чотиритактні V-подібні дизелі Ярославського моторного заводу (ЯМЗ) - 6-циліндрові ЯМЗ-236, 8- циліндрові ЯМЗ-238 і 12-циліндрові ЯМЗ-240, потужність яких відповідно 103,176 і 220 кВт (180, 240 і 300 к. с). Усі ці дизелі уніфіковані, тобто багато деталей кривошипио-шатунного і газорозподільного механізмів (гільзи циліндрів, поршні, шатуни, вкладиші, клапани), а також окремі прилади системи живлення в них однакові.
На автомобілях КамАЗ встановлюють також чотиритактні 8-циліндрові дизелі ЯМЗ-740, потужність яких 154 кВт (210 к. с).
За будовою системи живлення усі ці дизелі майже однакові
Дизельне паливо.
Як і бензин, дизельне паливо являє собою суміш, яку дістають внаслідок переробки нафти, рідких вуглеводнів з різними температурами кипіння. Дизельне паливо повинне відповідати таким основним вимогам: мати певний фракційний склад і в'язкість, дуже низькі температури застигання й самозаймання, по можливості менший період затримки займання, малий вміст органічних кислот і сірки, не мати механічних домішок і води.
Для забезпечення якісного утворення суміші дизельне паливо повинне мати певний фракційний склад. Дизельне паливо повинне мати повну в'язкість, щоб забезпечити мащення паливної апаратури. Якщо в'язкість недостатня, погіршуються умови мащення тертьових деталей. Дуже висока в'язкість утруднює подачу і вприскування палива в циліндри дизеля.
Низька температура застигання забезпечує надійну роб автомобіля взимку, а низька температура самозаймання - легкий запуск холодного двигуна.
Для забезпечення м'якої роботи дизеля треба, щоб під час згоряння палива тиск у циліндрах наростав плавно, а це можливо лише тоді, коли паливо займається відразу після надходження в циліндри перших його частинок. Запізнення загоряння призводить до одночасного згоряння значної кількості палива, що спричиняє різке збільшення тиску і жорстку роботу двигуна.
Період затримки загоряння палива характеризується цетановим числом, яке визначається процентним вмістом (за об'ємом) цетану в такій суміші його з альфаметилнафталіном, яка рівноцінна випробуваній суміші стосовно жорсткості роботи двигуна. Цетан - вуглеводень з найменшою, а альфаметилнафталін - вуглеводень з найбільшою межами затримки загоряння палива, які приймаються за еталон. Чим більше цетанове число, тим м'якша робота двигуна»
Корозійні властивості палива залежать від кількості органічних кислот і сірки, процентний вміст яких суворо обмежений
Вміст механічних домішок і води в дизельному паливі недопустимий, оскільки перші спричиняють посилене спрацюєш тертьових деталей паливної апаратури і забруднення а друга призводить до утворення льоду в паливо-проводах у холодну пору року
Марки дизельного палива
Основні марки автомобільного дизельного палива- ДА (арктичне), ДЗ (зимове) і ДЛ (літне)» Вони відрізняються одне від одного в основному фракційним складом і температурою застигання: чим нижча навколишня температура, тим більше в паливі легких фракцій і нижча температура його застигання.
Будова системи живлення
Система живлення дизеля ЯМЗ-236 призначена для очищення палива і повітря створення високого тиску палива його дозування, та подачі палива в циліндри двигуна.
Вона складається з паливного бака , підкачувального насоса , фільтрів грубої і тонкої очистки палива, паливного насоса високого тиску (ПНВТ), форсунки , паливопроводів низького і високого тиску.
Працює: Під дією паливо підкачувального насоса паливо с паливного бака через фільтра грубої та тонкої очистки палива надходить до ПНВТ в якому тиск палива збільшується і через паливо проводи високого тиску паливо потрапляє до форсунок, через які воно впорскується в циліндри двигуна в дрібно розпиленому вигляді в кінці такту стиску і змішавшись з нагрітим до 500-600 0С повітрям (за рахунок стискання повітря) утворює пальну суміш яка самозаймається і в наслідок збільшення тиску виконується робота. В такті випуску відпрацьовані гази виводяться в атмосферу через випускний колектор і глушник
Паливні баки дизельних автомобілів
мають таку саму будову, що й баки автомобілів з карбюраторними двигунами,
Паливні фільтри.
Паливо, яке надходить до насоса високого тиску і форсунок, не повинно містити механічних домішок, що спричиняють пошкодження або підвищене спрацювання паливної апаратури, виготовленої з дуже високою точністю. Тому в системі живлення дизелів паливо багато разів фільтрують. У дизеля ЯМЗ-236 є такі паливні фільтри: сітчастий, на кінці паливної забірної трубки в баці; грубої очистки, встановлений між баком і підкачувальним насосом; тонкої очистки, розміщений між підкачувальним насосом і насосом високого тиску у вхідному отворі форсунок.
У фільтрі грубої очистки встановлено фільтруючий елемент, який має сітчастий каркас з намотаним на нього в кілька шарів ворсистим бавовняно-паперовим шнуром.
У фільтрі тонкої очистки встановлений фільтруючий елемент з набивкою мінеральної вати, просоченої клейкою речовиною. Фільтр тонкої очистки має перепускний клапан, пружина якого розрахована на 0,6...0,7 МПа (6...7 кгс/см2). Якщо тиск у фільтрі вищий від вказаного, клапан відкринасться і перепускає частину палива з фільтра через трубку, приєднану до нього, у паливний бак. Завдяки цьому у фільтрі і паливопроводі, який з'єднує фільтр з насосом високого тиску, підтримується постійний тиск.
Повітряний фільтр за будовою і принципом дії аналогічний до інерцйно-масляних повітряних фільтрів карбюраторних двигунів.
. На таких автомобілях як КаМАЗ, КрАЗ встановлені сухі паперові фільтра
Паливний насос високого тиску
Паливний насос високого тиску
Паливний насос високого тиску подає в циліндри дизеля потрібну кількість палива в строго визначені моменти. У двигуні ЯМЗ-236 насос установлено між правим і лівим рядами циліндрів. Вал насоса приводиться в дію валом привода, шестірні якого з'єднані з шестірнями розподільного вала дизеля. Частота обертання вала насоса вдвічі менша від частоти обертання колінчастого вала дизеля. За два оберти колінчастого вала, протягом яких у циліндрах дизеля відбувається один повний цикл, вал насоса прокручується на один оберт, і насос впорскує паливо у всі циліндри.
У корпусі насоса високого тиску кулачковий вал встановлено на кулькових (у насосах останніх випусків - на роликових) підшипниках.
Кожний з кулачків вала приводить у дію секцію насоса, яка являє собою одноплунжерний насос високого тиску, що обслуговує один циліндр дизеля. [b]Секція [/b]складасться з гільзи, усередині якої вміщено плунжер , нагнітального клапана і роликового штовхача . Плунжер може переміщатися в гільзі вгору і вниз. На проточці нижнього кінця плунжера встановлено опорну шайбу пружини яка верхнім кінцем через шайбу упирається в головку насоса. Під тиском пружини опорна шайба притиснута до регулювального болта штовхача а ролик штовхача - до кулачка вала насоса.
Коли виступ кулачка підходить під ролик штовхач піднімається, стискуючи пружину , і переміщує плунжер насоса вгору. У міру того як виступ кулачка, повертаючись, виходить з-під ролика штовхача, пружина повертає плунжер і штовхач у вихідне положення.
Отже, під час роботи дизеля плунжер рухається зворотно-поступально вгору і,вниз.
У верхній частині плунжер має осьову і радіальну просвердлини. Коли плунжер знаходиться в гільзі, ці просвердлили з'єднують надплунжерний простір з двома спіральними канавками , профрезерованими на боковій поверхні плунжера.
Під час опускання плунжера надплунжерний простір гільзи, а також просвердлини і канавки плунжера заповнюються паливом, яке надходить у гільзу з каналу у корпусі насоса через впускний отвір гільзи. Рухаючись вгору, плунжер спочатку витісняв паливо з гільзи назад в канал . Після того як плунжер перекрив отвір гільзи і паливо в гільзі буде в замкнутому просторі , дальший рух плунжера спричинить різке підвищення тиску в надплунжерному просторію Паливо відкривав нагнітальний і починає надходити через паливопровід високого тиску в циліндр дизеля.
Нагнітання палива триває доти, поки верхня кромка лівої спіральної канавки плунжера підійде до перепускного отвору гільзи. Після цього паливо з надплунжерного простору перетікатиме через просвердлини 20 і .21 у канавку 22 і перепускний отвір гільзи в канал корпусу насоса. Тиск у надплунжерному просторі різко знизиться, нагнітальний клапан закриється, і паливо в циліндр не подаватиметься.
Кількість палива, що подається в циліндр, регулюється повертанням плунжера навколо його осі, внаслідок чого змінюється момент кінця подачі палива секцією при незмінному моменті початку подачі. При повертанні плунжера за годинниковою стрілкою (якщо дивитися зверху) кромка його спіральної канавки раніше підходить до перепускного отвору гільзи, нагнітання палива до форсунки припиняється, і кількість палива, що подається в циліндр, зменшується. Якщо плунжер повернути за годинниковою стрілкою так, щоб радіальна просвердлена плунжера співпала з отвором гільзи, тоді секція припинить подачу палива (нульова подача). При повертанні плунжера проти годинникової стрілки кромка спіральної канавки пізніше досягає отвору гільзи, і кількість палива збільшується. Для прокручування плунжера призначені зубчаста рейка і надіта на гільзу поворотна втулка , зубчастий вінець в якої перебуває в зачепленні з рейкою. Через регулятор частоти обертання колінчастого вала зубчаста рейка зв'язана з педаллю керування подачею палива. Педаль розміщена в кабіні водія» Переміщення рейки вздовж її осі зумовлює повертання втулки, яка, в свою чергу, діючи через виступи , повертає плунжер» Рух рейки викликає одночасне повертання плунжерів усіх секцій насоса на однаковий кут.
Гільзи всіх шести секцій кріпляться в загальному корпусі насоса гвинтами. Зверху в корпус вкручено штуцери , які притискають сідла нагнітальних клапанів до гільз. Зовні до штуцерів кріплять паливопроводи, які з'єднують секції насоса високого тиску з форсунками.
Кулачки розміщені на валу насоса так, що секції забезпечують подачу палива відповідно до послідовності роботи циліндрів дизеля і визначених інтервалів між робочими ходами в різних циліндрах. ВЛ з'єднаний з валом привода за допомогою відцентрової муфти 39 автоматичного випередження впорскування , яка збільшує кут випередження впорскування палива в циліндри у міру зростання частоти обертання колінчастого вала дизеля. Ця муфта за принципом дії аналогічна до відцентрового регулятора випередження запалювання карбюраторних двигунів. На задньому кінці вала насоса встановлено шестірню, за допомогою якої обертається вал, розміщений у корпусі всережимного регулятора частоти обертання колінчастого вала дизеля. Регулятор підтримує постійною будь-яку частоту обертання колінчастого вала, яку встановлює водій шляхом натискування (або відпускання) педалі керування подачею палива і, крім того, обмежує максимальну частоту обертання колінчастого вала (2250...2275 об\хв).
Підшипники, кулачки вала насоса і штовхачі, а також деталі регулятора змащуються дизельним маслом, яке заливають у корпуси насоса і регулятора. Плунжерні пари насоса змащуються паливом.
Керують роботою насоса, з місця водія за допомогою педалі, яка з'єднана системою тяг і важелів з важелем регулятора. Регулятор, у свою чергу, діє на рейку паливного насоса. Щоб зупинити дизель треба натиснути на кнопку, яка з'єднана тросом із скобою зупинника. При витягуванні кнопки скоба повертається вниз і через важільну систему регулятора пересуває рейку до відказу в бік зменшення подачі палива, внаслідок чого плунжери всіх секцій насоса встановлюються в положення нульової подачі
Принцип дії паливного насоса високого тиску двигуна КамАЗ-740 такий самий, як і у вищеописаного насоса ЯМЗ-236, але насос КамАЗ має не 6, а 8 секцій, які розміщені у V-подібному корпусі в два ряди (по 4 секції в кожному) під кутом 90° один до одного.
Підкачувальний насос. У системі живлення дизеля ЯМЗ-236 установлюють поршневий підкачувальний насос. Його корпус 38 (рис. 29) кріпиться до корпусу 17 насоса високого тиску» У корпусі підкачувального насоса вміщено поршень 36 з пружиною 37, шток 35 і роликовий штовхач 33 з пружиною 34.
Підкачувальний насос працює так . Поршень 36 . поділяє внутрішній простір циліндра на порожнини А і Б. Порожнина з'єднується з впускним каналом, який перекривається впускним клапаном 44, і з випускним каналом, що перекривається випускним клапаном 43. Обидва клапани за допомогою пружин утримуються в закритому положенні. Ділянка випускного каналу після клапана сполучається перепускним каналом 46 з порожниною В, Поршень приводиться в дію за допомогою кулачкового вала 32 насоса високого тиску. Коли виступ кулачка набігає іш ролик штовхача 33, штовхач, шток 35 і поршень переміщуються бік порожнини А (рис. 29, а вгору). Після того як виступ кулачка повернеться і не діятиме на ролик штовхача, пружини 37 і 34 повертають поршень, штовхач і шток у початкове положення
Рухаючись угору, поршень витісняє паливо з порожнини А через випускний клапан 43, який відкрився під тиском палива, і перепускний клапан 46 у порожнину Б, об'єм якої внаслідок переміщення поршня вгору збільшиться. Під час руху вниз поршень витісняє паливо з порожнини Б до вихідного отвору насоса, звідки воно по паливоироводу поступає у фільтр тонкої очистки і далі до насоса високого тиску. Одночасно об'єм порожнини А збільшується, і в ній створюється розрідження, впускний клапан 41 під тиском палива з боку вхідного отвору відкривається і порожнина А заповнюється паливом, яке надходить з бака. Під час наступних ходів поршня описаний цикл роботи насоса повторюється.
Тиск, який створюється підкачувальним насосом, залежить від сили пружності пружини 37 поршня і при закритому вихідному отворі насоса може досягти 0,6 МПа (6 кгс/см2). У паливній системі за підкачувальним насосом підтримується тиск 0,16...0,17МПа (1,6.".1,7 кгс/см2).
Зверху на корпусі підкачувального насоса установлено насос ручного підкачування палива, який використовують для наповнення системи паливом і видалення повітря, що випадково туди потрапило.
Цей насос складається з корпусу , циліндра , поршня з штоком і рукоятки. Коли поршень за допомогою рукоятки переміщують угору, в порожнину А підкачувального насоса і в циліндр через клапан всмоктується паливо з бака. Під час переміщення вниз поршень витісняє паливо з циліндра через порожнину А і випускний клапан підкачувального насоса в паливопровод, який через фільтр тонкої очистки з'єднано з насосом високого тиску
Після користування насосом рукоятку накручують до відказу на різьбу циліндра ; при цьому поршень , який щільно притиснутий до прокладки , роз'єднує порожнини підкачувального насоса, і циліндра насоса ручного підкачування, що усуває можливість підсмоктування повітря в систему через насос ручного підкачування.
Форсунки
- Форсунки тонко розпилюють паливо, яке подає насос високого тиску в камери згоряння циліндрів дизеля. До корпусу форсунки за допомогою гайки кріпиться розпилювач з чотирма розпилювальними отворами , в який встановлена голка. Голка силою пружності пружини , яка передається через штангу , притискується до внутрішньої комічної поверхні розпилювача і перекриває вихід палива з порожнини до отворів розпилювача.
Під час нагнітального ходу плунжера насоса високого тиску паливо від насоса поступає через вхідний штуцер 12, фільтр і канал у кільцеву порожнину розпилювача. Під тиском палива голка піднімається і порожнина розпилювача сполучається з розпилювальними отворами, через які паливо впорскується в циліндр. У момент відсікання кінця подачі палива насосом тиск у порожнинах форсунки падає і пружина опускав голку. Вихід палива з отворів розпилювача припиняється. Тиск на початку впорскування палива в циліндри дизеля ЯМЗ-236 повинен бути 15 МПа (150 кгс/см'). Тиск регулюють, змінюючи натяг пружини обертанням гвинта , при цьому ковпак знято і контргайка послаблена.Форсунки кріплять в отворах головок циліндрів дизеля накладними скобами і болтами, штуцери форсунок проходять через отвори на стику головок і кришок циліндрів; в отворах установлено гумові ущільнювачі . До штуцерів приєднують паливопроводи високого тиску, а до отворів у торцях ковпаків - дренажні трубки для відведення з порожнин у верхній Частині корпусу форсунок палива, що просочується через зазори між голкою і розпилювачем. По трубці паливо з дренажних трубок зливається в бак автомобіля.
Несправності в систем живлення дизелів. Якщо в системі живлення виникли несправності, то утруднюється запуск, знижується потужність дизеля, підвищується витрата палива, виникають перебої в роботі циліндрів, збільшується димність. Основними причини цього, витікання на дива або підсмоктування в систему живлення повітря через негерметичність з'єднань паливопроводів і приладів; забруднення паливних фільтрів; несправність підкачувального насоса; спрацювання плунжерів і гільз насоса високого тиску; порушення моменту початку і рівномірності подачі палива секціями насоса; зменшення сили пружності пружини голки форсунки; негерметичність або зависання голки; забруднення отворів розпилювача форсунки.
ТЕХНІЧНЕ ОБСЛУГОВУВАННЯ СИСТЕМИ ЖИВЛЕННЯ
Технічне обслуговування системи живлення автомобіля включає в себе перевірку герметичності системи, надійності кріплення її окремих елементів на рамі і двигуні, промиванні і заміні фільтрів, зливі відстою.При щоденному обслуговуванні зовнішнім оглядом перевіряється відсутність підтікання палива і, по приладах, наявність палива в баці.При проведенні ТО1 зливається відстій з фільтра грубого очищення палива (ФГО), для чого відвернути пробку на дні склянки і зливати відстій до появи чистого палива. При заправленні автомобіля невідстояним паливом ізливання відстою робити щотижня.При кожному другому ТО2 (через 32 000 км пробігу) промити фільтруючий елемент фільтра грубого очищення. При цьому злити паливо зі стакана ФГО, відвернути чотири болти кріплення стакана і зняти стакан. Очистити від бруду фільтруючий елемент, промити його бензином чи чистим дизельним паливом і продути стисненим повітрям. Зборку провести в зворотному порядку.При експлуатації автомобіля в умовах підвищеної запиленості промивання фільтруючого елемента ФГО проводити через 350-400 км пробігу.При проведенні ТО2 продути стисненим повітрям фільтруючий елемент повітряного фільтра, а у випадку сильного забруднення замінити. Злити відстій з фільтра тонкого очищення палива (ФТО). Для зливу відстою відвернути пробку в нижній частині корпуса ФТО і зливати до появи чистого палива.
При кожнім другому ТО2 заміняти фільтруючий елемент фільтра тонкого очищення палива. Для заміни фільтруючого елемента потрібно злити паливо з корпуса ФТО, відвернути гайки кріплення кришки і зняти кришку. Вийняти з корпуса фільтруючий елемент, промити корпус фільтра і поставити новий фільтруючий елемент. Зібрати фільтр, відвернути на 1-2 обороту пробки 9 і 4 на кришці фільтра і на корпусі насоса високого тиску (рис. 13). Прокачати систему рукояткою 3 насоси ручного підкачування 2. З появою палива послідовно закручувати спочатку пробку 4 на корпусі насоса, а потім пробку 9 на кришці фільтра.Після пробігу 64 000 кілометрів (чотири ТО2) перевірити параметри паливного насоса і форсунок на стенді.
Тема: Турбокомпресор
Турбокомпре́сор або газотурбі́нний нагніта́ч - компресор динамічної дії (відцентровий або осьовий), у якому дія на потік стискуваного газу здійснюється обертовими ґратками лопаток ротора, що урухомлюється і працює в парі на одному валу із турбіною[1][2]. Є основним конструктивним елементом газотурбінних двигунів.[3] та важливим вузлом двигунів внутрішнього згоряння, що оснащені системою наддування
В автомобілях турбокомпресор (англ. turbocharger) використовується у системах турбонаддування з метою покращення характеристик за рахунок нагнітання повітря або паливо-повітряної суміші у двигун внутрішнього згоряння за рахунок енергії вихлопних газів.
Турбокомпресор підвищує тиск у впускній системі двигуна, в результаті чого збільшується маса повітря, яке надходить у камеру згоряння, що дозволяє забезпечити приріст потужності двигуна до 30-40%.
Турбокомпресори, що використовуються в автомобільних двигунах, найчастіше (з міркувань мінімізації масо-габаритних параметрів) виконуються за двоконсольною схемою з опорами, які розташовуються між дисками компресора і турбіни. Вал обертається у підшипниках ковзання. Використовуються підшипники плаваючого типу, тобто вони мають зазор як з боку корпусу, так і валу. Підшипники змащуються моторною оливою системи змащення двигуна. Олива подається по каналах в корпусі підшипників. Для герметизації масла на валу встановлені защільнювальні кільця. У деяких конструкціях бензинових двигунів для поліпшення охолодження додатково застосовується рідинне охолодження турбонагнітачів. Корпус підшипників турбонагнітача включений у двоконтурну систему охолодження двигуна.
Вихлопні гази надходять у корпус і спрямовуються на лопатки турбінного колеса, яке набирає високих обертів (до 250000 об/хв), обертаючи при цьому робоче колесо компресора. Відпрацьовані гази після турбінного колеса покидають турбіну через осьовий отвір і відводяться у випускну систему. Турбіна працює в умовах високих температур, тому її елементи виготовляють з жароміцних матеріалів (залізо-нікелевих сплавів та сталей).
Продуктивність турбокомпресора переважно визначається розміром і формою турбіни. У загальному випадку, чим більшою є турбіна, тим вищою буде продуктивність компресора. Але при малих обертах двигуна компресор не спроможний забезпечувати потрібну продуктивність, у результаті чого спостерігається турбозатримка або «турбояма» (англ. turbolag) при збільшенні навантаження на двигун, що обумовлює відставання зростання вихідної потужності у відповідь на зміну тиску відпрацьованих газів.
Малий за розмірами турбокомпресор розкручується до номінальної швидкості значно швидше, зате має меншу продуктивність. Найменші розміри мають турбокомпресори для двигунів легкових автомобілів - діаметр їх коліс порядку 50 мм. Найбільші розміри у суднових турбокомпресорів - діаметр коліс - до 1,2 м
Для зниження наслідків турбозатримки, підвищення продуктивності конструкції турбокомпресорів постійно вдосконалюються. Найпопулярнішими технічними рішеннями є:
- зниження маси турбіни за рахунок застосування легших і міцних матеріалів (кераміка тощо);
- застосування нових конструкцій підшипників, що забезпечують зниження втрат на тертя;
- використання двох послідовних або паралельних турбокомпресорів (англ. twin-turbo або англ. bi-turbo відповідно);
- використання турбін із змінною геометрією (англ. Variable-geometry turbochargers, VGT також відома як VNT-турбіна від англ. Variable Nozzle Turbine).
Основні параметри турбокомпресорів для автотракторних двигунів стандартизовані і дозволяють обирати їх типорозміри для конкретного двигуна за заданим ступенем підвищення тиску та припустимим значенням колової швидкості компресора. За цією швидкістю та діаметром диска робочого колеса визначається частота обертання вала. З умови міцності для дисків з нікелевих сплавів колова швидкість не повинна перевищувати 250...350 м/с при температурі газів перед турбіною 730 °C.
Тема: Система живлення повітрям дизеля
Система живлення двигуна повітрям призначена для забору повітря із атмосфери, очистки його від пилу і розподілу по циліндрам двигуна.
Складається із:
повітряного фільтра;
ущільнювача;
повітрезабірника;
патрубків і труби;
повітряного фільтра із впускними клапанами.
Повітряний фільтр сухого типу, двоступінчастий, призначений для очистки поступаючого в двигун повітря від пилу.
Складається із:
корпуса;
кришки;
фільтруючого елемента.
Очистка повітря в повітряному фільтрі двоступінчаста. Перша ступінь очистки - моноциклон, складається із заслінки, яка забезпечує обертання повітряного потоку навколо фільтруючого елемента, таким чином очищаючи повітря від пилу, який збирається в бункері.
Друга ступінь очистки - фільтруючий елемент, який складається із зовнішнього і внутрішнього кожухів.
Система випуску газів призначена для викидання в атмосферу відпрацьованих газів, а також часткового відводу тепла від двигуна.
Система складається із:
2-х випускних колекторів;
2-х прийомних труб;
гнучкого металевого рукава;
глушника.
Кожний випускний колектор обслуговує один ряд циліндрів. Колектори з'єднуються з головками циліндрів патрубками.
На автомобілі встановлений комбінований активно-реактивний глушник. Активний глушник працює за принципом перетворення звукової енергії в теплову, що здійснюється установкою на шляху газів перфорованих перегородок, в отворах яких потік газів дробиться і пульсація газів затухає. В реактивному глушнику використовується принцип акустичної фільтрації звука. Цей глушник уявляє собою ряд акустичних камер, зўєднаних послідовно.
Тема; Газобалонні установки
Основні елементи газобалонної установки(стиснений газ)
- газові трубопроводи
- вентилі
- редуктор високого тиску
- підігрівник газу
- електромагнітний клапан
- газовий редуктор низького тиску
- дозувально-економайзерний пристрій
- карбюратор-змішувач
Принцип роботи системи на стисненому газі
Блок управління - (бо) - найважливіших елемент ГБО. Залежно від серії, БО призначаються для установки на двигуни з різною кількістю циліндрів. Блоки управління бувають універсальними, які можуть монтуватися на 3-, 4-, 5-, 6- і 8-циліндрові.
Вісім балонів, згрупованих по чотири, розміщують під платформою кузов(рами) а й кожну групу обкладають вентилем, що дає змогу витрачати газ у будь-якій групі або відразу в обох. Газом балони наповнюються крізь вентиль . Із балонів газ крізь витратні вентилі надходить у підігрівник (18), що призначається для захисту системи від замерзання внаслідок великого зниження температури газу під час його розширення в редукторі високого тиску . Між підігрівником газу, що обігрівається теплотою відпрацьованих газів, і балонами встановлено основний витратний вентиль. На редукторі високого тиску установлено датчик контрольної лампи, яка засвічується в разі заниження тиску газу в редукторі до значення менше ніж 0,45 мПа. Це сигналізує водієві про те, що газу в балонах залишилося на 10...12 км. Із редуктора ) газ надходить в електромагнітний клапан із фільтром. Цей клапан відкривається під час пуску двигуна, і газ трубкою надходить у редуктор низького тиску Редуктор ) має два ступені й знижує тиск газу, що надходить у карбюратор - змішувач, майже до атмосферного, дозує газ для приготування суміші потрібного складу й вимикає газову лінію в разі зупинки двигуна. Під час роботи двигуна газ надходить у карбюратор - змішувач, а в режимі холостого ходу - шлангом безпосередньо в за дросельний простір. Робота двигуна на бензині забезпечується стандартною системою живлення бензином, яку підключено до карбюратора - змішувача
Газобалонна установка для роботи на зрідженому газі
З балона крізь витратний вентиль(19), магістральний вентиль) і газопровід стиснений газ надходить у випарник що обігрівається рідиною з системи охолодження двигуна. Потім крізь фільтр( газ надходить у редуктор), де його тиск зменшується майже до атмосферного. Контролюють робочу системи за допомогою манометрів.Пуск і прогрівання двигуна здійснюють на паровій фазі газу. Для цього відкривають паровий і магістральний() вентилі. На короткий час двигун зупиняють вимиканням запалювання, а в разі зупинки на 1 .2 год. перекривають магістральний вентиль.
На днищі() балона є запобіжний клапан(), наповнювальний вентиль із зворотнім клапаном, вентиль максимального заповнення бальна й датчик рівня зрідженого газу.
Для заповнення балона використовують вентиль(4). Заповнюють тільки 90%, що у разі розширеного газу під час нагрівання балон не зруйнувався. Рівень різкого газу в процесі заповнення контролюється за допомогою трубки-рівня вентиля-показчика. Водій контролює наявність газу за допомогою показчика
Технічне обслуговування
ЩТО
Оглядом перевіряється:
- кріплення газових балонів і герметичність з'єднань усієї газової системи.
- геометричність арматури балонів і витрачених вертикалів.
- з'єднання бензопроводів і електромагнітного клапана-фільтра.
ТО-1
Крім робіт, передбачених ЩТО, перевіряється:
- робота запобіжного клапана газового редуктора високого тиску
- Змащується різьба штоків магістрального, наповнювального та витратного вентилів
- герметичність газової системи
- пуск і робота двигуна на холостому ходу як на газі, так і на бензині
Обов'язкове проведення очищення й встановлення на місце фільтрувальних елементів магістрального фільтра та фільтра редуктора високого тиску.
ТО-2
Крім робіт, виконуваних під час ЩТО та ТО-1, перевіряється:
- герметичність редукторів високого й низького тисків
- тиск у першому й другому ступенях редуктора низького тиску
- робота запобіжного клапана газового балона
- робота манометрів високого й низького тисків
- кріплення карбюратора й перехідника змішувача до карбюратора.
- перевірка герметичності підігрівника
- робота заслінки та її привода
Зняття та промивка (заміна) повітряного фільтра, залити в його ванну свіжу оливу. Якщо потрібно, відрегулювати змішувач на мінімальний вміст оксиду вуглецю у відпрацьованих газах двигуна.
СО
Передбачається розбирання, очищення й регулювання:
- карбюратора-змішувача,
- редукторів, фільтрів,
- електромагнітних запірних клапанів.
Перевіряється тиск спрацювання запобіжного клапана редуктора високого тиску. Один раз у три роки проводиться огляд газових балонів. Готуючись до зимової експлуатації, зливається відстій і промивається бензобак автомобіля.
Переваги
- Газоповітряні суміші порівняно з бензоповітряними мають вищі антидетонаційні властивості, що дає змогу підвищити ступінь стискання й поліпшити економічні показники двигуна.
- Газові двигуни характеризуються повнішим згорянням суміші й набагато нижчою токсичністю (шкідливістю) відпрацьованих газів, завдяки чому зменшується забруднення довкілля.
- У разі застосування газу не зсувається плівка оливи зі стінок гільз і поршнів, зменшується нагароутворення в камерах згоряння; через відсутність конденсації пари бензину на стінки гільз циліндрів не розрізняють[Що?] олива, завдяки чому 1.5..2 рази збільшується термін служби двигуна й період зміни оливи.
Недоліки
- у газобалонних автомобілів складніша система живлення
- підвищуються вимоги щодо пожежо та вибухонебезпечності
- потужність газових двигунів на 10-20 % менша порівняно з бензиновими
Заходи безпеки
- До водіння й обслуговування газобалонних автомобілів, допускаються особи, які мають відповідну підготовку і склали іспити з техмінімуму та техніки безпеки. Виконувати технічне обслуговування газобалонних установок можуть тільки кваліфіковані слюсарі, які пройшли відповідну підготовку й мають посвідчення.
- Регулярні роботи з двигуном, що працює слід виконувати на спеціальному посту з місцевою вентиляцією для видалення відпрацьованих газів.
- Пускати газовий двигун, якщо є витікання газу, не допускається.
- Заправляти газобалонні установки можна тільки на газонаповнювальних станціях, коли двигун не працює. Під час заправляння балонів зрідженим газом треба берегтися обмороження.
- Експлуатація газобалонних автомобілів з несправним газовим обладнанням і витіканням газу забороняється. Коли не вдається усунути витікання газу, його випускають в атмосферу (якомога далі від людей і джерел вогню).
Тема: Особливості будови електрообладнання автомобілів та основи його ТО.
Учбові питання
1. Акумуляторні батареї.
2.Генераторні установки.
3. Несправності джерел електричного струму.
4. Стартер.
5.Контрольно- вимірювальні прилади.
6. Прилади освітлення і сигналізації.
Домашнє завдання: О. П. Строков, М. Г. Макаренко, В. Ф. Орлов, В. О. Павленко " Основи будови та експлуатації автопоїздів" стр.127 - 175
1. На вантажних автомобілях застосовують стартерні кислотні акумуляторні батареї. Акумуляторні батареї мають єдиний моноблок у який заливають електроліт і встановлюють блоки позмтивно і негативно заряджених пластин. При номінальній напрузі бортової мережі 24 В використовують дві 12- вольтові акумуляторні батареї зєднані послідовно.
2.Генераторна установка складається з генератора,випрямний блок і інтегральний регулятор напруги.Генератор складається з корпусу, кришок, статора, ротора ,шківа приводу ротора. Випрямний блок складається з шести діодів. Регулятор напруги служить для підтримки в заданих межах напруги, яку вмробляє генератор.Являє собою електронний пристрій закритий кришкою і залитий герметиком.
3.Несправності джерел електричного струму:
а) Окислення вивідних штирів АКБ
б) Випадання активної маси пластин АКБ
в) Підвищений саморозряд АКБ
г) Тріщини в корпусі АКБ
д) спрацювання і зависання щіток генератора
ж) Обрив або коротке замикання обмоток ротора і статора генератора
з)забруднення контактних кілець генератора
4. Стартер служить для електричного запуску двигуна. Стартер складається з таких основних частин: а) корпуса б) сталеві полюси в) обмотка збудження г) щіткотримачі із мідно - графітовими щітками д)якір ( вал, осердя,обмотка, колектор ж)муфта вільного ходу з)тягове реле к) реле вмикання. Під час пуску стартер споживає великий струм тому тривалість його вмикання не повинна перевищувати 10 - 15 с.
5. Контрольно - вимірювальні прилади діляться на дві групи : вказуючі і сигналізуючі. Вказуючі прилади мають шкалу і стрілку.До вказуючих пристроїв відносяться манометри, які показують тиск масла або повітря ,показчик температурм охолоджувальної рідини, показчик рівня палива, амперметри, спідометри з механічним приводом. Сигналізуючі прилади попереджують водія про виникнення несправностей втому чи іншому вузлі. До сигналізуючих приладів відносяться сигналізатори аварійного тиску масла або повітря, сигналізатор аварійної температури.
6. Прилади освітлення і сигналізації діляться на дві групи: прилади зовнішнього освітлення і світлової сигналізації і прилади внутрішнього освітлення і світлової сигналізації. До приладів зовнішнього освітлення і світлової сигналізації відносяться фари головного освітлення, протитуманні фари, підфарники, задні ліхтарі, ліхтарі освітлення номерного знаку,світлові показчики повороту, стоп- сигнали. До приладів внутрішнього освітлення і світлової сигналізації відносяться лампи освітлення приладів , плафони для освітлення кабіни водія, підкапотна лампа, переносна лампа , сигнальні лампи на шкалі приладів.
Тема Трансмісія автомобіля
Трансмісія автомобіля-тягача — це низка взаємодіючих між собою агрегатів і механізмів, які передають крутний момент від двигуна до ведучих коліс. При передачі крутний момент змінюється за величиною і за напрямком, розподіляючись одночасно між ведучими колесами автомобіля.
За характером зв'язку між двигуном і ведучими колесами, а також за способом перетворення крутного моменту трансмісії поділяються на механічні, комбіновані (гідромеханічні), електричні та гідрооб'ємні. Найбільшого поширення на автомобілях-тягачах на-були механічні трансмісії, виконані за різними схемами (див. Схема трансмісії) залежно від загальної компоновки агрегатів автомобіля, включаючи розташування двигуна і ведучих коліс.
1 — зчеплення; 2 — коробка передач; 3 — карданна передача; 4 — головна передача; 5 — диференціал; 6 — піввісь; 7 — роздавальна коробка
Механічна трансмісія яка використовується па більшості вантажних автомобілі» і автомобілів-тягачів складається із зчеплення 1, коробки передач 2, карданної 3 і головної 4 передач, диференціала 5 і двох піввісей (і. Трансмісії автомобілів-тягачів підвищеної прохідності з двома і більше ведучими мостами (див. Схема трансмісії в) обладнані роздавальною коробкою 7 і додатковими карданними валами (передачами 3), а кожна пара ведучих коліс мас свою головну передачу,піввісі і диференціал.
Вищеописані схеми трансмісій часто називають мостовими, оскільки крупині момент, підводиться до кожного ведучого моста, а потім розподіляється між правилі і лівим ведучими колесами моста.
. Зчеплення служить для короткочасного від'єднання двигуна від трансмісії і плавного їх з'єднання у момент початку руху з місця стоянки автомобіля, а також після перемикання передач у процесі руху Крім того, зчеплення оберігає деталі двигуна і агрегатів трансмісії від перевантаження, які виникають під час різкого гальмування автомобіля з працюючим двигуном.
Принцип роботи зчеплення З маховиком і жорстко сполучений кожух, зв'язаний шарнірами 5 з натискним диском 2.
Шарніри дозволяють натискному диску переміщатися в осьовому напрямку і сприймати момент від кожуха. Між натискним диском і маховиком встановлений ведений диск 4. Натискний і ведений диски притискаються до маховика натискними пружинами в і в результаті сил тертя крутний момент від маховика передається веденому диску, встановленому на шліцах веденого вала 7, який є одночасно ведучим валом коробки передач.' У цьому випадку зчеплення ввімкнено і крутний момент від ведучого вала передасться до агрегатів трансмісії.
. Зчеплення дозволяє на нетривалий час від'єднати трансмісію від двигуна і забезпечує плавне включення трансмісії при рушанні автомобіля з місця або при перемиканні передач. Коробка передач служить для отримання різних тягових зусиль на провідних колесах шляхом зміни крутного моменту, що передається від двигуна до карданного валу, а також для зміни напрямку обертання провідних коліс при русі заднім ходом і для відключення трансмісії від двигуна на тривалий час.
Карданна передача дозволяє передавати крутний момент від вихідного валу коробки передач до заднього моста при змінюваному (при русі автомобіля) вугіллі між осями валу коробки передач і провідного валу головної передачі.
Головна передача служить для того, щоб передати крутний момент під кутом 90 градусів від карданного вала до піввісь, а також для зменшення числа оборотів провідних коліс по відношенню до числа оборотів карданного валу. Зменшення частоти обертання механізмів трансмісії після головної передачі призводить до збільшення крутного моменту і, відповідно, збільшує силу тяги на колесах.
Диференціал забезпечує можливість обертання правого і лівого провідних коліс з різними швидкостями на поворотах і нерівній дорозі. Дві півосі, пов'язані з диференціалом через напівосьові шестерні, передають крутний момент від диференціала до правого і лівого провідним колесам. Диференціали, встановлювані між приводами коліс провідної осі, називають міжколісними, між різними осями - міжосьовими (в повнопривідних трансмісіях).
Тема: Ходова частина автомобіля
Учбові питання:
1. Рама автомобіля
2. Підвіска автомобіля
3. Колеса і шини
4. Можливі несправності ходової частини та способи їх усунення
Домашнє завдання: О. П. Строков, М. Г. Макаренко, В. Ф. Орлов, В. О. Павленко " Основи будови та експлуатації автопоїздів" стр.229 - 252
1. На вантажних автомобілях застосовують два види рам: лонжеронна і хребтова. Хребтова рама застосовуються на автомобілях тягачах і являється різновидом лонжеронної рами (лонжерони максимально наближені друг до друга). Будова лонжеронної рами: лонжерони, перемички, кронштейни, передній бампер, буксирні гаки, тягово - зчіпний пристрій.
2.Складовими елементами підвіски вантажних автомобілів є: ресори ( основні і додаткові), амортизатори, штанги, пневмоподушки. Штанги являються елементами балансирної підвіски , яка застосовується як првило в тривісних автомобілях.
3.За призначенням колеса вантажних автомобілів діляться на: ведучі, ведені, комбіновані , підтримувальні. За конструкцією вони бувають дискові і бездискові. бездискові колеса застосовують на вантажних автомобілях великої вантажопідйомності. Пневматичні шини за конструкцією бувають камерні і безкамерні. За будовою шини бувають: діагональні і радіаальні. На автомобілях застосовують радіаьні шини так як вони мають більшу довговічність.
4.Основні несправності ходової частини: биття коліс , відведення автомобіля в бік від прямолінійного руху , підвищене або нерівномірне спрацювання протектора, сильні удари кузова об буфер під час руху по нерівній дорозі , скрипіння або осідання ресор ( пружин).
Биття коліс може бути викликане порушенням їх балансування, великим люфтом підшипників коліс або кульових зєднань. Відведення автомобіля в бік може бути наслідком різниці тисків повітря в шинах, неправильного встановлення керованих коліс ( кути розвалу і сходження), дисбаланс коліс, неоднакової пружності ресор підвіски. Підвищене або нерівномірне спрацювання протектора викликане підвищеним або зниженим тиском повітря у шинах, порушення балансування коліс. Сильні удари кузова свідчать про несправності деталей підвіски.
ЕМА: Рульове керування вантажних автомобілів.
Питання вивчення матеріалу теми:
1. Призначення і загальна будова рульового керування.
2. Рульовий механізм.
3. Рульовий привід.
4. Рульове керування автомобілів ГАЗ, ЗИЛ і КАМАЗ.
Конспект.
Рульове керування вантажного автомобіля складається з двох основних частин:
1. Рульовий механізм.
2. Рульовий привід.
Рульовий механізм забезпечує повертання керованих коліс з невеликим зусиллям
на рульовому колесі.
Типи рульових механізмів:
1. Черв'ячні. (передача черв'як – ролик).
2. Гвинтові (передача гвинт – гайка – зубчастий сектор).
3. Шестеренчасті (передача утворена циліндричними або кінічними шестернями,
а також шестерня-рейка).
Рульовий привід передає керуюче зусилля від рульового механізму до керованих коліс (система тяг і важелів).
Рульова трапеція – це з'єднання тяг і важелів приводу у вигляді трапеції.
Рульова трапеція забезпечує поворот передніх коліс на різні кути (щоб поворот здійснювався без бічного ковзання коліс).
Керовані колеса повертаються на обмежений кут (28-35градусів) для того , щоб під час повороту виключити зачіпання колесами деталей кузова автомобіля.
Гідропідсилювач рульового керування зменшує зусилля,яке необхідно прикласти до рульового колеса для повороту передніх коліс.
На автомобілях ЗИЛ і КАМАЗ насос гідропідсилювача рульового керування лопатевого типу з бачком для масла.Насос приводиться в дію від шківа колінвала двигуна клинопасовою передачею на автомобілях ЗИЛ і шестеренчастою передачею на автомобілях КАМАЗ.
Запобіжний клапан насоса регулюється на тиск 8,5 – 9МПа. (85-90 кгс/см квадратний)
Тема: Система живлення стисненим повітрям гальм
Учбові питання:
1. Загальна будова
2. Характеристика основних вузлів
Література: О. П. Строков ,М. Г. Макаренко , В. Ф. Орлов , В. О. Павленко « Основи будови та експлуатації автопоїздів» стр.284 - 288
1. Система живлення стисненим повітрям включає в себе такі елементи:
А) Компресор б)Регулятор тиску в)Запобіжник від замерзання г) конденсаційний ресивер
2. Компресор призначений для створення тиску повітря в гальмівній системі. Компресор поршневого типу, двохциліндровий ,одноступеневого стиску. Привід компресора бензинового двигуна - пасовий, дизельного - шестеренчастий від розподільних шестерень. Регулятор тиску підтримує тиск в системі в межах 6,2 - 7,5 атм і захищає систему від забруднення. Складається з корпусу, фільтра, клапанів (розвантажувального, випускного, впускного, зворотнього), поршнів (слідкуючого і розвантажувального). Запобіжник від замерзання призначений для запобігання замерзання конденсату в трубопроводах. Запобіжник від замерзання складається з корпусів (нижнього і верхнього), пробок( одна з яких зливна), тяга з рукояткою, гніт з пружиною. У нижній корпус заливається спирт, який просочує гніт. Запобіжник від замерзання приводиться в дію з допомогою тяги з рукояткою, яка розтягує гніт.
Тема: Пневмопривід робочого гальма автомобіля
Учбові питання:
1.Пневмопривід гальм переднього візка
2. Пневмопривід гальм заднього візка
Література: О. П. Строков ,М. Г. Макаренко , В. Ф. Орлов , В. О. Павленко « Основи будови та експлуатації автопоїздів» стр.288 - 298
1. В пневмопривід переднього візка входять такі елементи: а) ресивер б) частина потрійного захисного клапана в) верхня частина двострілкового манометра г) нижня секція двосекційного гальмівного крана д) клапан обмеження тиску ж) гальмові камери з) гальмові механізми к) датчик зниження тиску л) трубопроводи. При зниженні тиску в ресивері нижче 4,5 атм. в кабіні водія вмикається звуковий сигнал і загоряється сигнальна лампочка. Потрійний захисний клапан призначений для розподілу стисненого повітря на два основних і один додатковий контури, автоматичного вимкнення одного з пошкоджених контурів. Двосекційний гальмовий кран призначений для керування виконавчими механізмами двоконтурного приводу робочого гальма. Клапан обмеження тиску призначений для зменшення тиску в гальмових камерах передньої осі при гальмуванні з малою інтенсивністю і швидкого випуску повітря з гальмових камер під час пригальмовування. Гальмівні камери призначені для приведення в дію гальмівних механізмів.
2. Пневмопривід заднього візка складається з частинини потрійного захисного клапана, ресиверів, частини двострілкового манометра , верхньої секції гальмівного крана, автоматичного регулятора гальмових сил, гальмівні камери, гальмівні механізми, трубопроводи і шланги .
Тема: Стоянкове і допоміжне гальмо
Учбові питання:
1. Стоянкове гальмо
2. Допоміжне гальмо
Література: О. П. Строков ,М. Г. Макаренко , В. Ф. Орлов , В. О. Павленко « Основи будови та експлуатації автопоїздів» стр.299 - 309
1. Контур приводу стоянкового гальма складається з частини подвійного захисного клапана , двох ресиверів, річного крана стоянкового гальма, прискорювального клапана, частини двомагістрального перепускного клапана, чотирьох пружинних енергоакумуляторів, гальмових камер , трубопроводів і шлангів. Кран керування стоянковим гальмом призначений для керування пружинним енергоакумуляторами приводу гальм стоянкової і запасної гальмівних систем. Прискорювальний клапан подає стиснене повітря в енергоакумулятори і призначений для зменшення часу спрацьовування приводу гальм. Двомагістральний перепускний клапан призначений для керування одним виконавчим механізмом (пружинним енергоакумулятором). Гальмова камера з пружинним енергоакумулятором призначена для приведення в дію гальмівних механізмів коліс заднього візка при ввімкненні робочого, запасного, стоянкового гальм. Вмикання стоянкового гальма проводиться повним випуском повітря в атмосферу з порожнини циліндра енергоакумулятора через прискорювальний клапан ,керований ручним гальмовим краном.
2. Допоміжне гальмо служить для зменшення навантаження на механізми робочого гальма. При вмиканні допоміжного гальма ( мотор - сповільнювач) перекриваються випускні трубопроводи і вимикається подача палива. Контур приводу допоміжного гальма складається з частини подвійного захисного клапана, двох пневмоциліндрів, пневмоциліндра приводу важеля зупинки, пневматичного крана, пневмоелектричного датчика, трубопроводів і шлангів. Пневматичний кран з кнопковим керуванням призначений для ввімкнення і вимкнення подачі стисненого повітря до споживачів. Два крани: один - керування пневмоциліндрами допоміжного гальма, інший - для керування системою аварійного розгальмовування пружинних енергоакумуляторів. Тема: Карданна передача
Ведучі мости автомобіля встановлюються на рамі або на кузові автомобіля за допомогою пружних елементів підвіски й під час руху змінюють своє положення відносно місць кріплення. Для передавання крутного моменту від коробки передач до ведучого моста застосовують карданні передачі, їх використовують також у приводі до передніх керованих і ведучих коліс.
Карданна передача до ведучого моста складається з карданного вала, шарнірів і проміжної опори. Карданні шарніри забезпечують передавання крутного моменту між валами, осі яких перетинаються під змінними кутами. В трансмісії автомобілів застосовують жорсткі карданні шарніри неоднакових і однакових кутових швидкостей.
Карданний шарнір неоднакових кутових швидкостей складається з жорстких деталей (рис. 4.16, а): ведучої і веденої 4 вилок, хрестовини 2, на шипи якої насаджено голчасті підшипники 3. Крутний момент передається від вилки 1 до вилки 4 через хрестовину 2. За такої конструкції й рівномірного обертання вилки ведучого вала кутова швидкість веденої вилки змінюватиметься двічі за кожен оберт: збільшуючись і зменшуючись. Тому такий шарнір називають шарніром неоднакових кутових швидкостей.
Щоб усунути нерівномірність обертання веденого вала в карданній передачі, як правило, застосовують два шарніри неоднакових кутових швидкостей, розташованих на кінцях карданного вала. Тоді нерівномірність обертання, що виникає в першому ведучому шарнірі, компенсується нерівномірністю обертання другого шарніра, й ведений вал передачі обертається рівномірно, з кутовою швидкістю ведучого вала. Така карданна передача називається подвійною. Одинарні передачі з одним жорстким карданним шарніром практично не застосовуються.
У приводі передніх керованих і ведучих коліс автомобілів підвищеної прохідності застосовують шарніри однакових кутових швидкостей двох типів: кулькові й кулачкові.
Кульковий карданний шарнір ( складається з двох фасонних кулаків з овальними канавками, куди закладаються ведучі кульки . Для центрування вилок використовують сферичні западини на їхніх внутрішніх торцях, в яких установлюється центрувальна кулька
Під час передавання крутного моменту ведучі кульки розташовуються незалежно від кутових переміщень вилок у їхніх овальних канавках у площині, яка поділяє кут між осями навпіл. У результаті обидві вилки обертаються з однаковими кутовими швидкостями.
Кулачковий карданний шарнір однакових кутових швидкостей застосовують у приводі переднього колеса автомобіля
«Урал-375». До конструкції шарніра включено зовнішню піввісь колеса, яка входить шліцьовим кінцем у вилку шарніра. Внутрішню піввісь виконано як одне ціле з вилкою шарніра, а її зовнішній кінець стикується з шестірнею диференціала шліцьовим з'єднанням. У вилки установлено кулаки у пази яких закладено сталевий диск Під час роботи шарніра півосі обертаються разом із вилками навколо кулаків у горизонтальній площині, а разом із кулаками — навколо диска у вертикальній площині. Таким чином забезпечується передавання крутного моменту на ведучі й керовані передні колеса.
Недолік розглянутого шарніра — підвищене тертя в місцях з'єднання диска й кулаків із вилками, внаслідок чого знижується коефіцієнт корисної дії й підвищуються нагрівання та спрацьовування шарніра під час роботи.
Карданна передача автомобіля ЗИЛ-130 ) складається з проміжного та основного карданних валів, з'єднаних один з одним. Проміжний вал спирається на проміжну опору, що складається з шарикопідшипника уставленого в гумове кільце із металевим кронштейном На передньому кінці проміжного вала приварено вилку карданного шарніра, а другий кінець його виконано у,^ вигляді шліцьової втулки , в яку вставлено шліцьовий кінець вилки карданного шарніра основного вала. Завдяки ковзному шліцьовому з'єднанню проміжного й основного карданних валів їхня загальна довжина може змінюватися в разі вертикальних переміщень ведучого моста на нерівностях дороги.
Карданні шарніри складаються з двох вилок у вушка яких установлено хрестовину із шипами й голчастими підшипниками
Кожен підшипник складається зі сталевого стакана з голками, закріпленого у вушку вилки кришкою, стопорною пластиною та двома болтами. Змащуються голчасті підшипники від пресоливниці /каналами у хрестовині. Витіканню мастила з підшипників запобігають торцеві ущільнювачі й гумові само підтискні сальники у вилках.
Карданні вали виготовляються з тонкостінних сталевих труб, на кінцях яких запресовано й приварено хвостовики вилок. Після складання карданні вали балансують для зменшення вібрацій, які виникають під час роботи карданної передачі.