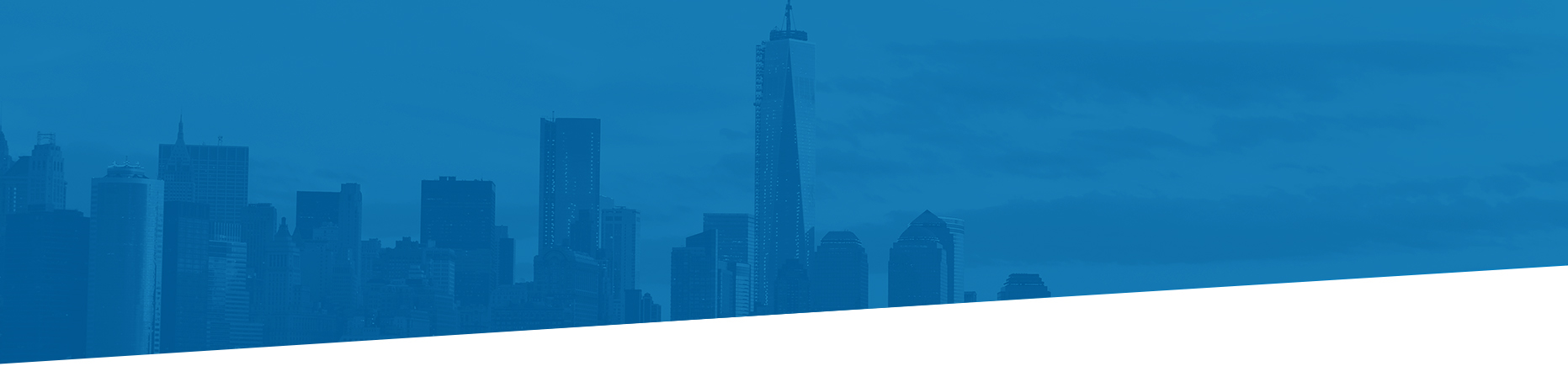
Будова КТЗ
Тема: Механічні муфти
Більшість машин компонується з механізмів, кожен з яких виконаний у вигляді агрегату, що забезпечує можливість повної взаємозамінності. Крім того, при передачі руху від двигуна до виконавчого механізму виникає необхідність включати і вимикати роботу виконавчого механізму, не припиняючи роботу двигуна. Ці завдання і ряд інших вирішуються за допомогою застосування муфт.
муфта (Від німецького die Muffe) - пристрій для з'єднання валів, тяг, труб, канатів, кабелів. слід розрізняти муфти з'єднувальні и муфти приводівмашин. Саме останні розглядаються в курсі деталей машин. Тому далі поняттям муфтаоб'єднуються пристрої, призначені для передачі обертального руху між валами або між валом і вільно сидить на ньому деталлю (шківом, зірочкою, зубчастим колесом і т. п.) без зміни параметрів руху. Сучасне машинобудування в своєму розпорядженні великим арсеналом муфт, що розрізняються за функціональним призначенням, принципом дії і конструктивним виконанням.
Призначення муфт:
компенсація неточності сполучення з'єднуються кінців валів;
пом'якшення крутильних ударів і гасіння коливань;
запобігання механізмів від руйнування при дії позаштатних навантажень;
періодичне зчеплення і розчеплення валів в процесі руху або під час зупинки;
передача односпрямованого руху або запобігання передачі зворотного руху від веденого вала до ведучого;
обмеження параметрів переданого руху - Швидкості (частоти обертання веденого вала) або крутного моменту.
Класифікація муфт:
по виду енергії, яка бере участь в передачі руху - механічні, гідравлічні, електромагнітні;
по стабільності зчеплення з'єднуються валів - муфти постійного з'єднання (некеровані), муфти зчіпні, керовані (з'єднання і роз'єднання валів по команді оператора), і автоматичні (або з'єднання, або роз'єднання автоматичне після досягнення керуючим параметром заданого значення);
за здатністю демпфірування динамічних навантажень - жорсткі, не здатні знижувати динамічні навантаження і гасити крутильні коливання, і пружні, згладжують вібрації, поштовхи і удари завдяки наявності пружних елементів і елементів, що поглинають енергію коливань;
за ступенем зв'язку валів - нерухома (глуха), рухома (що компенсує), сцепная, вільного ходу, запобіжна;
за принципом дії - Втулкові, поздовжньо-роз'ємна, поперечно-роз'ємна, що компенсує, шарнірна, пружна, фрикційна, кулачкова, зубчаста, з руйнуються елементом (зрізна), з зачепленням (кулачкові і кулькові);
за конструктивними ознаками - Поперечно-компенсує, поздовжньо-компенсує, універсально-компенсує, шарнірна, пружна (постійної і змінної жорсткості), конусна, циліндрична, дискова, фрикційна вільного ходу, Храпова вільного ходу.
Муфти постійного з'єднання дозволяють роз'єднати провідний і ведений вали тільки після розбирання з'єднання. Найбільш простими з муфт постійного з'єднання є глухі муфти. Глухий називають таку муфту, яка забезпечує при з'єднанні валів повний збіг їх геометричних осей. глухими є втулкові, поздовжньо-роз'ємні і поперечно-роз'ємні або фланцеві муфти.
втулкова муфта найбільш проста по конструкції Момент, що обертає від ведучого вала до веденого передається втулкою через штифти, встановлені в отвори, просвердлені діаметрально крізь втулку і кінці валів, через шпонки, або через шліци.
Недоліком цієї муфти є неможливість роз'єднання валів без зміщення хоча б одного з них.
Поздовжньо-роз'ємна муфта ) складається з двох напівмуфт, які стягуються при складанні гвинтами або болтами з гайкою. Роз'єм між напівмуфтами розташований в площині, що проходить через загальну геометричну вісь обох з'єднуються валів. Зусилля затягування гвинтів вибирається таким, щоб забезпечити передачу крутного моменту силами тертя, що діють між контактуючими поверхнями валів і напівмуфт. Така муфта дозволяє роз'єднувати кінці валів, що не зміщуючи останні зі свого місця, і полегшує центрування валів при установці агрегатів на загальну раму або фундамент.
Недоліком поздовжньо-рознімної муфти є можливість зміщення її центру мас з осі обертання валів при неоднаковою затягуванні гвинтів на протилежних сторонах, що може викликати вібрацію валів, особливо небезпечну при великих швидкостях обертання.
Поперечно-роз'ємнаіфланцевая муфта також складається з двох напівмуфт, але кожна з її полумуфт насаджується на сполучається кінець свого з валів - одна на провідний вал, інша на ведений. Кожна з них забезпечена фланцем. При складанні з'єднання напівмуфти встановлюються так, щоб фланці встали один проти одного з мінімальним зазором. В отвори фланців вставляються болти, що стягують напівмуфти. При точному виготовленні болтових отворів (наприклад, з-під розгортки) застосовують болти Поперечний переріз яких під час передачі крутного моменту працює на зріз. При отворах малої точності болти встановлюються з зазором , І в цьому випадку тіло болтів працює на розтяг, а крутний момент передається за рахунок сил тертя між торцевими поверхнями фланців. Муфти, призначені для відкритої установки, забезпечуються з метою забезпечення безпеки обслуговуючого персоналу виступами, які закривають головки болтів і гайки
Глухі муфти, жорстко з'єднуючи кінці валів, не дозволяють їм деформуватися під дією робочих зусиль, що виникають на елементах механізмів, що передають обертальний рух, таких, як шестерні, зірочки, шківи. Це обмеження деформації валів сприяє підвищенню згинальних напружень в них і, в кінцевому підсумку, скорочує термін їх служби.
Винятки цієї неприємності домагаються за допомогою застосування рухомих муфт - муфт, конструкція яких дозволяє окремим елементам переміщатися в невеликих межах один щодо одного разом з кінцями з'єднуються валів. Такі муфти називають інакше компенсують. Компенсуючі муфти допускають деяке неспівпадіння геометричних осей з'єднувальних валів. Величину такого неспівпадання прийнято називати величиною зміщення (рис. 16.4). Взаємне зміщення валів щодо номінального положення може відбуватися в процесі роботи механізмів внаслідок найрізноманітніших причин: деформації валів під робочим навантаженням, температурної деформації, зношування підшипників, опади фундаменту і т. П.
Всі рухомі компенсуючі муфти можна розділити на дві групи: 1) жорсткі муфти та 2) пружні муфти.
У жорстких муфтах рухливість частин забезпечується конструктивними особливостями їх елементів (розташування частин, величини зазорів, форма поверхонь і т. П.). Тому жорсткі муфти практично не здатні гасити крутильні коливання, що виникають в механізмах.
В пружних муфтах рухливість частин досягається за рахунок деформації пружного елемента муфти (різного роду пружини, деталі з еластомеру, наприклад гуми). Деформація такого пружного елемента відбувається, як правило, з досить великим поглинанням енергії, останнім сприяє інтенсивному гасіння крутильних коливань і більш спокійній роботі приводу в цілому.
Для компенсації радіального зміщення валів широко застосовується хрестово-кулісні (кулачково-дискова) муфта (Рис. 16.6), що містить три головних частини: встановлюються на сполучаються вали дві напівмуфти 1 и 2, Кожна з яких може бути як провідної, так і відомою, і між ними куліса (диск) 3, Забезпечена прямокутними гребенями на торцевих поверхнях, що йдуть уздовж взаємно перпендикулярних діаметрів. Гребені куліси при складанні муфти вводяться в пази, виконані на звернених один до одного торцевих поверхнях напівмуфт. Часто з метою полегшення куліси у неї видаляють центральну частину.
Деталі хрестово-кулісною муфти виготовляються, як правило, з вуглецевих або легованих сталей (стали 45, 50, 40Х, 15Х, 20Х та ін.). Контактні поверхні гребенів куліси і пазів напівмуфт піддають хіміко - терміческой або термічній обробці з метою досягнення високої твердості і контактної міцності.
Для з'єднання швидкохідних валів застосовується інший різновид хрестово-кулісною муфти У цій муфті дискова куліса замінена сухарём, які мають квадратне поперечний переріз, а пази на торцях полумуфт розширені до поперечних розмірів сухаря. Сам сухар виготовляється зазвичай з неметалічних матеріалів (текстоліт, фенольно-формальдегідні пластики, капролон і т. П.). В силу малої щільності матеріалу сухаря, а також менших його розмірів в порівнянні з дисковою кулісою, відцентрові сили в цьому різновиді муфти значно менше в порівнянні з муфтою, що має дискову кулісу.
Для гасіння крутильних коливань (коливань кутової швидкості), викликаних силами інерції в механічних приводах широке застосування знаходятьпружні муфти. Головною особливістю цих муфт є наявність пружного елемента (гумові втулки, Торообразная оболонка, еластична хрестовина, різного роду пружини і т. П.), Який при різкому зростанні навантаження (моменту опору) здатний деформуватися, повертаючись в початковий стан при зменшенні навантаження до нормальної робочої величини. Пружні муфти, крім того, допускають радіальний зсув валів до 0,4 ... 0,6 мм і кутове зміщення осей валів до 1,5 °. Крім пружного елемента муфти ще забезпечуються, як правило, що поглинає пристроєм, призначеним для диссипации коливальної енергії та запобігання резонансних коливань в елементах приводу при нерівномірному обертанні його валів. Досить часто пружний і поглинає елементи поєднуються в одній деталі.
Демпфуюча здатність муфти характеризується величиною механічної енергії, що поглинається муфтою необоротно при деформації її пружного елемента. Поглинання енергії в муфті відбувається або за рахунок тертя її деталей одна об одну (пружинні муфти різної конструкції), або за рахунок внутрішнього тертя в неметалічному пружному елементі. Так, наприклад, багато гумові пружні вироби здатні перетворити на тепло до 25% енергії витраченої на їх деформацію.
Як приклад з великого числа відомих конструкцій розглянемо дві найбільш поширені і прості по пристрою пружні муфти.
Муфта пружна втулочно-пальцева(МУВП; складається з двох напівмуфт, кожна з яких виконана у вигляді маточини з фланцем на одному кінці. На фланці однієї з напівмуфт (зазвичай провідною) кріпляться пальці з надітими на їх вільні кінці гумовими кільцями трапецеидального перетину або гофрованими гумовими втулками. При монтажі на сполучаються кінці валів напівмуфти встановлюються фланцями один до одного, а кінці пальців з натягнутими на них пружними елементами входять в отвори другий (зазвичай відомою напівмуфти).
Напівмуфти можуть бути виготовлені з чавуну марки не нижче СЧ 21-40 або стали Ст. 3. Для виготовлення пальців використовується сталь 45 або більше міцна. Кільця і втулки виготовляються з гуми, що має міцність на розтяг не нижче 6 МПа і твердість 55 ... 75 одиниць по Шору.
Муфти даного типу мають великий радіальної і кутовий жорсткістю, тому і механізми, вали яких з'єднують за допомогою такої муфти, повинні встановлюватися на плитах або рамах великий жорсткості якомога точніше центрування сполучених валів.
Втулочно-пальцева муфта вимагає досить точного центрування
Конструкція муфт з нерозрізний оболонкою представлена на рис. 16.11. Муфта складається з двох напівмуфт, забезпечених фланцями, і торообразной оболонки, прикріпленою своєю периферичної частиною до фланців за допомогою притискних дисків і гвинтів, що стягають ці диски з фланцями полумуфт. Притискні диски для нерозрізний торообразной оболонки розрізні (виконуються з двох або більшої кількості деталей, що з'єднуються за допомогою гвинтів), для розрізний - нерозрізні.
Муфти з опуклою торообразной оболонкою в порівнянні з муфтами, що мають увігнуту оболонку, мають дещо меншу масу, здатні передавати приблизно на 20% менший момент і витримують приблизно в 1,5 рази менші обороти, але при цьому мають істотно більшу піддатливість.
При обертанні з досить великими кутовими швидкостями на напівмуфтах з'являються постійно діючі осьові зусилля, що вимагає жорсткого осьового закріплення полумуфт на кінцях з'єднуються валів.
зчіпними називають муфти, основним назначением яких є з'єднання або роз'єднання валів при русі або під час зупинки.
Основні вимоги до зчіпних муфт:
1. швидкість і легкість включення (з'єднання валів) і виключення (роз'єднання валів);
2. плавність включення;
3. надійність зчеплення валів після включення муфти;
4. високий ККД, малий знос і нагрівання муфти;
5. простота регулювання і настройки;
6. незначні зусилля на органах управління при ручному управлінні;
7. мінімальні габарити при заданих несучої здатності, і терміні експлуатації.
Як зчіпних в машинобудуванні найбільш широкого поширення набули кулачкові, зубчасті и фрикційні муфти.
Кулачкові та зубчастімуфти Мають подібну конструктивну схему. Обидва види муфт складаються з двох напівмуфт, кожна з яких оснащена фланцевої частиною. Одна з напівмуфт кріпиться на одному з з'єднуються валів нерухомо, інша, закріплена на другому з цих валів, має можливість осьового переміщення або забезпечується рухомий в осьовому напрямку втулкою.
Різниця цих муфт полягає в тому, що в напівмуфтах кулачковою муфти зуби, які прийнято називати кулачками, виконані на торцевій поверхні фланців , А в напівмуфтах зубчастої муфти зуби розташовані на циліндричній поверхні, причому на одній з напівмуфт робляться зовнішні зуби (права полумуфта На інший - внутрішні (ліва полумуфта
Обидва різновиди муфт знаходять широке застосування в коробках передач колісних і гусеничних машин, а також металорізального обладнання.
При зближенні полумуфт допомогою осьового переміщення рухомий напівмуфти кулачки або зуби однієї напівмуфти входять у западини інший, і крутний момент передається за рахунок силового контактного взаємодії кулачків або зубів бічними сторонами.
При включенні таких муфт на ходу, коли або вали обертаються з різними швидкостями, або один з них обертається, а інший взагалі нерухомий, процес включення відбудеться з ударом між бічними поверхнями зубів, що дуже небажано через вплив на зуби надмірних ударних навантажень, що призводять до швидкого зносу робочих поверхонь і в деяких випадках навіть здатних викликати поломку зубів. З цієї причини кулачкові та зубчасті муфти часто застосовуються спільно з додатковими пристроями, що забезпечують синхронізацію швидкості обертання з'єднуються валів перед включенням муфти.
Кулачкові та зубчасті муфти виготовляються зазвичай з вуглецевих або легованих сталей (сталь 45, 50, 40ХН, 38ХМЮА і ін.). Робочі поверхні кулачків піддаються хімічній або хіміко-термічній обробці для досягнення високої твердості контактної поверхні (HRC 56 ... 62).
фрикційні муфтипередають крутний момент за допомогою сил тертя, що виникають на поверхнях зчіпних елементів (рис. 16.13).
Фрикційні муфти знайшли широке застосування в рухливих машинах, як колісних, так і гусеничних (в автомобілях це муфта зчеплення, в танках, БМП і інших гусеничних машинах - головний фрикціон).
Широке поширення фрикційних муфт обумовлено їх безсумнівними перевагами
1. допускають включення при будь-якому відмінності кутових швидкостей з'єднуються валів (не потрібно їх попередньо синхронізувати);
2. забезпечують плавний розгін веденого вала;
3. дозволяють плавно регулювати швидкість обертання веденого вала і час його розгону;
4. виконують запобіжну функцію, обмежуючи величину моменту навантаження, що передається від веденого вала ведучому.
основним недоліком фрикційних муфт є нездатність забезпечити повну синхронність обертання ведучого і веденого валів внаслідок проковзування.
Класифікація фрикційних муфт:
1. у напрямку дії замикає зусилля - осьові и радіальні;
2. за формою і конструкції елементів тертя -
осьові: а) конусні;
б) дискові;
радіальні: в) колодкові;
г) стрічкові;
д) з розтискним кільцем;
3. за наявністю мастила на поверхнях тертя - сухі и масляні.
У сухих муфтах поверхні тертя працюють без змащення, в масляних тіла тертя занурені в масляну ванну.
Якість фрикційних муфт (жорсткість і стабільність зчеплення, термін служби, частота включень-виключень) визначаються головним чином якістю використаних для їх виготовлення фрикційних матеріалів. Ці матеріали повинні відповідати наступним вимогам:
1. забезпечувати високий і постійний в часі коефіцієнт тертя;
2. володіти високою зносостійкістю;
3. мати достатню міцність
4. мати високу теплопровідність для відводу тепла від поверхні
тертя;
5. мати високу теплостійкість і хімічну стійкість проти продуктів розкладання і окислення мастильних матеріалів при високій температурі;
6. мати хорошу оброблюваність
Тема: Загальні відомості з деталей машин
Основне призначення машин - часткова або повна заміна виробничих функцій людини з метою підвищення продуктивності, полегшення людської праці або заміни людини в неприпустимих для нього умовах роботи.
Залежно від виконуваних функцій машини діляться на енергетичні, робочі (транспортні, технологічні, транспортують), інформаційні (обчислювальні, шифрувальні, телеграфні і т. П.), Машини-автомати, що поєднують в собі функції декількох видів машин, включаючи інформаційні.
агрегат (Від латинського aggrego - приєдную) - укрупнений уніфікований елемент машини (наприклад, в автомобілі: двигун, , що володіє повною взаємозамінністю і виконує певні функції в процесі роботи машини.
механізм - Штучно створена система матеріальних тіл, призначена для перетворення руху одного або декількох тіл в потрібне (необхідне) рух інших тіл.
прилад - Пристрій, призначений для вимірювань, виробничого контролю, управління, регулювання та інших функцій, пов'язаних з отриманням, перетворенням і передачею інформації.
складальна одиниця (Вузол) - виріб або частину його (частина машини), складові частини якого підлягають з'єднанню між собою (збираються) на підприємстві виробнику (суміжному підприємстві). Складальна одиниця має, як правило, певне функціональне призначення.
деталь - Найменша неподільна (не розбирався) частину машини, агрегату, механізму, приладу, вузла.
Складальні одиниці (вузли) і деталі діляться на вузли та деталі загального і спеціального призначення.
Вузли та деталі загального призначення застосовуються в більшості сучасних машин і приладів (кріпильні деталі: болти, гвинти, гайки, шайби; зубчасті колеса, підшипники кочення і т. П.). Саме такі деталі вивчаються в курсі деталей машин.
До вузлів і деталей спеціального призначення відносяться такі вузли та деталі, які входять до складу одного або декількох типів машин і приладів (наприклад, поршні і шатуни ДВС, лопатки турбін газотурбінних двигунів, траки гусениць тракторів, танків і БМП) і вивчаються у відповідних спеціальних курсах (наприклад, таких як "Теорія і конструкція ДВС", "конструкція і розрахунок гусеничних машин" та ін.).
Залежно від складності виготовлення деталі, в свою чергу, діляться на простіискладні.Прості деталі для свого виготовлення вимагають невеликого числа вже відомих і добре освоєних технологічних операцій і виготовляються при масовому виробництві на верстатах-автоматах (наприклад, кріпильні вироби - болти, гвинти, гайки, шайби, шплінти; зубчасті колеса невеликих розмірів і т. П.) . Складні деталі мають найчастіше досить складну конфігурацію, а при їх виготовленні застосовуються досить складні технологічні операції і використовується значний обсяг ручної праці, для виконання якого в останні роки все частіше застосовуються роботи (наприклад, при складанні-зварюванні кузовів легкових автомобілів).
За функціональним призначенням вузли та деталі діляться на:
1. Корпусні деталі,призначені для розміщення і фіксації рухомих деталей механізму, для їх захисту від дії несприятливих факторів зовнішнього середовища, а також для кріплення механізмів у складі машин і агрегатів. Часто, крім того, корпусні деталі використовуються для зберігання експлуатаційного запасу мастильних матеріалів.
2. сполучні для роз'ємного і нероз'ємного з'єднання (наприклад, муфти - пристрої для з'єднання валів; болти гвинти шпильки гайки - деталі для рознімних з'єднань; заклепки - деталі для нероз'ємного з'єднання).
3. Передавальні механізми і деталі, Призначені для передачі енергії і руху від джерела (двигуна) до споживача (виконавчого механізму), що виконує необхідну корисну роботу.
В курсі деталей машин розглядаються в основному передачі обертального руху: фрикційні, зубчасті, пасові ланцюгові і т. П. Ці передачі містять велику кількість деталей обертання: вали, шківи, зубчасті колеса і т. П.
Іноді виникає необхідність передавати енергію і рух з перетворенням останнього. У цьому випадку використовуються кулачкові та важільні механізми.
4. пружні елементи призначені для ослаблення ударів і вібрації або для накопичення енергії з метою подальшого здійснення механічної роботи (ресори колісних машин, противідкатні пристрої гармат, бойова пружина стрілецької зброї).
5. Інерційні деталі і елементи призначені для запобігання або ослаблення коливань (в лінійному або обертальному рухах) за рахунок накопичення та подальшої віддачі кінетичної енергії (маховики, противаги, маятники,), .
6. Захисні деталі і ущільнення призначені для захисту внутрішніх порожнин вузлів і агрегатів від дії несприятливих факторів зовнішнього середовища і від витікання мастильних матеріалів з цих порожнин (пилевікі, сальники, кришки, сорочки і т. п.).
7. Деталі й вузли регулювання і управлінняпризначені для впливу на агрегати і механізми з метою зміни їх режиму
роботи або його підтримки на оптимальному рівні (тяги, важелі, троси і т. п.).
Тема:: Передачі руху
Пасові передачі
Пасова передача - це механічний пристрій для передавання механічної енергії (механічна передача) між валами за допомогою гнучкого елементу (приводного паса) за рахунок сил тертя або сил зачеплення (зубчасті приводні паси).
Пасові передачі не забезпечують жорсткого зв'язку між шківами через можливість проковзування паса на шківах. Тому у кінематично точних приводних механізмах пасові передачі застосовують дуже рідко.
Пасові передачі переважно використовують для передавання потужностей у діапазоні 0,2-50 кВт. Зустрічаються також передачі для потужностей 500 і навіть 1500 кВт, проте застосування їх має унікальний характер.
Передавальні числа пасових передач допускаються до 5-6, рідше до 10.
Швидкість руху пасів у передачах загального призначення не перевищує 30 м/с. Спеціальні швидкохідні паси допускають при пониженій довговічності швидкості до 50 і навіть до 100 м/с.
ККД пасових передач різних типів становить близько 0,90-0,97.
У порівнянні із зубчастою передачею пасові передачі мають низку переваг і недоліків.
Основні переваги пасової передачі:
можливість передавання руху між валами, що знаходяться на значній відстані;
плавність та безшумність роботи, які обумовлені еластичністю паса;
запобігання різкому перевантаженню елементів машини внаслідок пружності паса та можливості його проковзування на шківах;
простота конструкції, обслуговування та догляду в експлуатації;
відносно високий ККД.
До недоліків пасової передачі належать:
неможливість виконання малогабаритних передач (для однакових умов навантаження діаметри шківів майже у 5 разів більші, ніж діаметри зубчастих коліс);
несталість передавального числа через можливе проковзування паса;
підвищене навантаження валів та їхніх опор, що пов'язане із потребою достатньо високого попереднього натягнення паса;
низька довговічність приводних пасів (у межах 1000-5000 год).
Класифікація
За формою поперечного перерізу приводного паса:
плоскопасова; клинопасова; круглопасова; з поліклиновим пасом.
За розміщенням валів:
відкрита; перехресна; напівперехресна: багатошківна з натяжним роликом.
Пасова передача може мати як постійне, так і змінне передавальне число (варіатор).
Окремо слід розглядати зубчасто-пасові передачі у яких плоский пас на внутрішньому боці має зубці трапецієвидної форми, а шківи - відповідні їм зубці на ободі. Така передача працює за принципом зачеплення, а не тертя. До пасових передач вона належить умовно тільки за назвою та формою тягового органу. Р Рис. 2.1 Види пасових передач
А- відкрита б- перехресна в- напівперехресна г – багатошківна напвперехресна д- з натяжним роликом е – з ступіньчатими шківами
Ланцюгова передача
Ланцюго́ва переда́ча (рос. цепная передача, англ. chaingear, chaintransmission, chaindrive; нім. Kettenantrieb m) - механізм (передача) у вигляді нескінченного ланцюга, що рухається по зубчастих колесах (зірочках), закріплених на паралельних валах, передаючи обертовий рух між цими валами.
Основні характеристики
Швидкість руху ланцюга у передачах загального призначення досягає 15 м/с при передаванні потужності до 100 кВт, а у спеціальних приводах - до 35 м/с при потужності до 2000 кВт. За допомогою ланцюгової передачі можна забезпечити передавальне число u ≤ 10, а найраціональніше мати u ≤ 4 при високому ККД (до 0,97).
Конструкція втулково-роликового ланцюга
Зовнішні пластини Внутрішні пластини Валик Втулка Ролик (сепаратор)
Валик ) запресований у зовнішні пластини ланцюга і утворює з ними одне ціле. На валик вільно посажена втулка яка запресована у внутрішні пластини (Якщо на втулку ( встановити вільно ролики то ланцюг буде втулково-роликовим. Такий ланцюг замінює тертя ковзання на тертя кочення при набіганні ланцюга на зірочку, але погіршує динамічні властивості (ланцюг стає важчим)
Класифікація
Ланцюгові передачі поділяють за такими ознаками: За типом ланцюга, яким оснащена передача, розрізняють ланцюгові передачі з
роликовими ланцюгами; втулковими ланцюгами; зубчастими ланцюгами.
За можливістю зміни відстані між осями зірочок ланцюгові передачі бувають із регульованою та постійною міжосьовою відстанню. За способом регулювання натягу ланцюга розрізняють ланцюгові передачі з періодичним і неперервним регулюванням натягу. За кількістю зірочок, що охоплені одним ланцюгом, ланцюгові передачі можуть бути двозірочкові, тризірочкові і т.д. За конструктивним виконанням та умовами експлуатації розрізняють відкриті ланцюгові передачі і закриті. Останні працюють у спеціальному корпусі в умовах неперервного змащування.
Переваги та недоліки
Ланцюгові передачі порівняно з іншими механічними передачами мають такі основні переваги:
можливість використання при значних відстанях між валами;
достатньо високий ККД;
можливість передавання обертового руху одним ланцюгом декільком валам, у тому числі і з протилежним напрямом обертання.
До недоліків ланцюгових передач належать такі:
збільшення довжини ланцюга через зношення шарнірних з'єднань і відповідне ослаблення натягу;
нерівномірність руху ланцюга і пов'язані з цим динамічні явища у передачі та підвищений шум;
низька кінематична точність при реверсуванні;
потреба застосування додаткових пристроїв для регулювання натягу ланцюга.
Приклади використання
Ланцюгові передачі застосовують у сільськогосподарських та транспортних машинах, підйомних пристроях, у приводах конвейєрів механізмів газорозподілу двигунів внутрішнього згорання. Ланцюгова передача дозволяє надавати обертовий рух валам, що знаходяться на порівняно великій відстані, а її габаритні розміри значно менші від габаритних розмірів пасової передачі. Неможливість проковзування ланцюга на зірочках забезпечує сталість середнього передавального числа передачі. Рис. 2.2 Ланцюгова передача
А – загальний вид б,в,г –види і конструкція ланцюгів
Зубчасті передачі
Зу́бчаста переда́ча - механізм, що має два зубчасті колеса, які можуть повертатися навколо осей, їх відносні положення зафіксовано й одне зубчасте колесо повертає інше за допомогою послідовної дії зубців, які перебувають у контакті.
Зубчаста передача складається з приводного зубчастого колеса (зубчасте колесо із зубчастої передачі, яке обертає інше) і веденого зубчастого колеса (зубчасте колесо із зубчастої передачі, що обертається під дією іншого).
Зубчасте колесо із зубчастої передачі, яке має менше число зубців носить назву шестерня (англ. pinion). Зубчасте колесо із зубчастої передачі, яке має більше число зубців - колесо (спрощене «спряжене зубчасте колесо шестерні», коли термін явно використано на протилежність до «шестерні»; англ. roue) .
Основні переваги
Постійність передавального числа, яке залежить лише від числа зубів зубчастих коліс (u=z2/z1 , де u - передавальне число передачі; z1, z2 - число зубів відповідно ведучого та веденого зубчастих коліс).
Можливість передачі великих потужностей (до 50000 кВт).
Високий ККД (η = 0,97...0,985).
Малі габаритні розміри в порівнянні з іншими видами передач (фрикційними, пасовими та ін.).
Висока надійність та довговічність роботи.
Основні недоліки
Необхідність використання складного обладнання для виготовлення зубів передач.
Неможливість здійснення безступінчастого регулювання швидкості.
Робота зубчастого передавача супроводжується шумом, особливо на високих швидкостях. Зубчасті передавачі можуть бути джерелом вібрації.
Класифікація
За передавальним відношенням:
з постійним передавальним відношенням;
зі змінним передавальним відношенням.
За формою профілю зубців:
евольвентні; колові (передача Новікова); циклоїдні
За типом зубців:
прямозубі; косозубі; шевронні; криволінійні.
За орієнтацією осей валів:
з паралельними осями (циліндричні передачі з прямими, косими і шевронними зубцями);
з осями, що перетинаються (конічні передачі);
з мимобіжними осями.
За формою початкових поверхонь:
циліндричні; конічні; гіперболоїдні;
За коловою швидкістю коліс:
тихохідні; середньошвидкісні; швидкохідні.
За ступенем безпеки :
відкриті; закриті.
За відносним обертанням коліс і розміщенням зубців:
внутрішнє зачеплення (обертання коліс в одному напрямку);
зовнішнє зачеплення (обертання коліс в протилежних напрямках).
Рейкова передача - один із видів циліндричної зубчастої передачі, де радіус ділильного кола рейки рівний нескінченності. Застосовується для перетворення обертового руху в поступний і навпаки.
Гвинтові, черв'ячні і гіпоїдні відносяться до зубчасто-гвинтових передач. Елементи цих передач ковзають відносно один одного.
Рис. 2.3 Види зубчастих передач
А – циліндрична прямозуба б – циліндрична косозуба в – циліндрична шевронна г – конічна д - рейкова е- червячна є – конічна гіпоїдна
Тема : Кривошипно - шатунний механізм .
Кривошипно-шатунний механізм є основою конструкції поршневих двигунів внутрішнього згоряння. Він призначений для сприймання тиску газів, що виникають у циліндрах під час згоряння палива, і перетворення зворотно-поступального руху поршнів в обертальний рух колінчастого вала.
У поршневих двигунах застосовують два типи кривошипно-шатунних механізмів: тронкові й крейцкопфні.
У сучасних поршневих автотракторних двигунах застосовуються в основному тронкові кривошипно-шатунні механізми з однорядним вертикальним і дворядним V-подібним розміщенням циліндрів
Кривошипно-шатунний механізм складається з нерухомих і рухомих деталей. До нерухомих деталей відносяться: циліндри, головка циліндрів і картер (блок-картер). До рухомих: поршні з поршневими кільцями, поршневими пальцями, шатуни, колінчастий вал і маховик. До обох груп відносять деталі кріплення, а також підшипники ковзання (вкладиші) колінвала.
Деталі КШМ між собою надійно з'єднуються і становлять остов (кістяк) двигуна. Вони навантажуються силами тиску газів, силами інерції мас, що здійснюють зворотно-поступальний та обертальний рух, моментами від цих сил, а також сприймають великі теплові навантаження. Внаслідок цього корпусні деталі повинні мати високу міцність і жорсткість.
При згоранні робочої суміші в циліндрах двигуна утворюються гази . Тиск газів передається на поршні азпоршнів на шатуни , які зєднані з колінвалом. Колінвал починає обертатися і приводить в дію механізми трансмісії . Рух передається на ведучі колеса транспортного засобу.
Газорозподільний механізм
Двигун з двома розподільними валами у головці блоку циліндрів з вирізами для демонстрування будови
Газорозподі́льний механі́зм (ГРМ) або механі́зм газорозпо́ділу - механізм керування фазами газорозподілу двигуна внутрішнього згоряння (ДВЗ), що забезпечує своєчасне подавання в циліндри двигуна повітря або паливо-повітряної суміші (залежно від типу двигуна) і випускання з циліндрів відпрацьованих газів.
Класифікація
За принципом здійснення своїх функцій ГРМ може бути реалізований наступними типами механізмів:
- клапанним, коли впуск і випуск визначається моментом і тривалістю відкриття клапанів;
- гільзовим (система Найта), коли гільза циліндра у результаті свого ковзного поздовжнього або повертального руху відкриває-закриває впускні-випускні канали;
- поршневим (щілинним), у якому сам поршень відкриває і закриває вікна (щілини) до каналів впуску та випуску;
- комбінованим (поршнево-клапанним), коли суміш подається вікнами у циліндрі, а випуск робиться через клапани.
Клапанні механізми газорозподілу
Загальні принципи будови
Клапанний механізм газорозподілу складається з розподільного (кулачкового) вала (одного або декількох) з механізмом урухомлення, тарілчастих клапанів для закривання-відкривання впускних і випускних отворів у камерах згоряння та передавальних ланок (штовхачів, штанг, коромисел, елементів регулювання, клапанних пружин, засобів провертання клапанів тощо).
Система урухомлення розподільного вала забезпечує його синхронне обертання з кутовою швидкістю удвічі меншою за швидкість обертання колінчастого вала. Для приведення у рух розподільного вала можуть використовуватись наступні механічні передачі: зубчаста, ланцюгова або зубчасто-пасова.
Класифікація клапанних ГРМ
Схематичний розріз нижньоклапанного двигунаДвигун з Т-подібною головкою (тип англ. T-head)Двигун зі змішаним розташуванням клапанів. Inlet - впускний клапан, Exhaust - випускний клапан
Класифікаційними ознаками для конструкцій клапанних газорозподільних механізмів є розташування та кількість клапанів і розподільних валів.
За розташуванням розподільного вала виділяють конструкції двигунів внутрішнього згоряння (зазвичай чотиритактних):
- з розташуванням розподільного вала у блоці циліндрів (англ. Cam-in-Block);
- з розташуванням розподільного вала у головці блоку циліндрів (англ. Cam-in-Head);
- без розподільного вала.
За розташуванням клапанів двигуни бувають: верхньоклапанні, нижньоклапанні та конструкції зі змішаним розташуванням клапанів.
З врахуванням цих ознак клапанні механізми чотиритактних двигунів внутрішнього згоряння поділяються на низку підтипів.
Двигуни з розподільним валом у блоці циліндрів
Нижньоклапанні (тип SV)
Нижньоклапанний двигун (англ. L-Head; Flathead, Side-Valve, SV) - двигун, у якого розподільний вал і клапани тарілками вгору розташовані у блоці циліндрів збоку від циліндрів. Приведення у рух клапанів відбувається безпосередньо від розподільного вала, розташованого одразу під клапанами.
Переваги схеми - малий шум при роботі, простота виготовлення та обслуговування, відсутність небезпеки контакту клапанів і поршня при порушенні фаз газорозподілу. Усі деталі ГРМ розташовані всередині блоку циліндрів, що дозволяє отримати компактне компонування двигуна. Головка блоку нижньоклапанного мотора має вигляд простої металевої плити з камерою згоряння та каналами для охолоджувальної рідини, вона легко демонтується.
Головний недолік схеми - через складний шлях паливно-повітряної суміші суттєво погіршується наповнення циліндрів, як наслідок - досягається менша потужність у порівнянні з іншими конфігураціями, двигун розвиває невеликі оберти і має низький ККД. Довгі випускні канали сприяють перегріванню двигуна, а особливості конструкцій його камер згоряння не дозволяють збільшити (понад 1:8) ступінь стиску, що до появи систем турбонаддування було найефективнішим методом підвищення потужності. З цієї ж причини ця конструкція не може застосовуватись для дизельних двигунів.
Аж до 1950-х років завдяки своїй простоті і дешевизні двигуни з таким ГРМ були найпопулярнішими на легкових (за винятком спортивних) і вантажних автомобілях. Перші масові моделі з двигуном верхньоклапанного компонування з'явилися в Європі ще у 1930-х, а до 1950-х років, після появи в широкому доступі палива з вищим октановим числом, стало очевидно, що нижньоклапанна схема стримує розвиток автомобілебудування, заважаючи створенню досконаліших, динамічних і швидкісних автомобілів. У результаті в першій половині п'ятдесятих років на легкових автомобілях почалося масове впровадження верхньоклапаннх двигунів, позбавлених властивих ніжньоклапанним схемам недоліків.
Різновидом нижньоклапанної схеми були двигуни з Т-подібною головкою (англ. T-head), що набули певного поширення у роки Другої світової війни. У них впускні клапани знаходились з одного боку блоку циліндрів, а випускні - з іншого. Розподільних валів було два. Мета конструкції - усунути перегрівання впускних клапанів. Це знижувало температуру паливно-повітряної суміші, що підвищувало її октанове число і зменшувало схильність до детонації. Ця ж ідея була покладена при використанні системи впорскування води у циліндри, яка охолоджувала суміш і знайшла використання у ті ж роки.
Двигуни зі змішаним розташуванням клапанів
У двигуна зі змішаним розташуванням клапанів зазвичай впускні клапани розташовані у головці блока, як у верхньоклапанного мотора, і приводяться у дію за допомогою штанг-штовхачів, а випускні - в блоці, як у нижньоклапанного двигуна. Розподільний вал розташовується в блоці циліндрів як у звичайного нижньоклапанного двигуна.
Така схема має ту перевагу, що вона забезпечує потужність відчутно вищу ніж у класичного нижньоклапанного і розглядалась у відповідний період як варіант модернізації останніх. Виграш у потужності був значним - до 20...40 к. с. для двигунів з вихідною потужністю 35...90 к. с.
Такі двигуни широко використовувались фірмами «Rolls-Royce» та «Rover» завдяки їх високій надійності, як у порівнянні з нижньоклапанними так і у порівнянні з ранніми конструкціями верхньоклапанних двигунів (через меншу кількість штанг-штовхачів).
З появою надійних конструкцій верхньоклапанних двигунів, ця схема вийшла з ужитку (останній двигун випускався фірмою «Willys» у 1970-х роках.
Верхньоклапанні ГРМ з приводом клапанів штовхачами (тип OHV)
Двигун з ГРМ типу OHV фірми Chrysler
Дана конструкція ГРМ була винайдена Девідом Данбаром Б'юїком (англ. David Dunbar Buick) на початку XX ст. У ній клапани розташовані у головці блока циліндрів, а розподільний вал - у блоці циліндрів (OHV - англ. OverHead Valve; або англ. I-Head, чи англ. Pushrod). Привод клапанів здійснювався штангами-штовхачами через коромисла.
Перевага такої схеми - відносно проста конструкція і конструктивна надійність. Для урухомлення механізму, як правило, використовувався простий і надійний привід розподільного вала шестернями, що виключає саму можливість таких несправностей, як розрив ременя ГРМ чи «перескакування» ланцюга в механізмі з ланцюговим приводом.
Двигуни з ГРМ типу OHV відчутно компактніші в порівнянні з верхньовальними, через відсутність у головці блоку розподільного вала.
Механізм приводу клапанів за схемою OHV є найдовшим у порівнянні з іншими варіантами
Істотним недоліком ГРМ типу OHV - велика інерційність такого механізму газорозподілу, що дещо обмежує безпечні максимальні оберти колінчастого вала двигуна і, отже, і літрову потужність (ступінь форсування). Спортивні двигуни з ГРМ типу OHV, наприклад - у машин, що беруть участь в гоночній серії NASCAR, можуть працювати і на 11000 об/хв, але для забезпечення цього потрібні спеціальні, досить дорогі конструктивні й технологічні рішення.
Крім того, така схема ускладнює використання більше двох клапанів на циліндр (двигуни з таким ГРМ при 4-х клапанах на циліндр, мають великі габарити і масу, що робить їх малопридатними для використання в легкових автомобілях, але вони є цілком прийнятними для вантажівок і важкої техніки - приклади тому двигуни КамАЗ, ЯМЗ, ТМЗ, дизельний двигун тепловоза ЧМЕ3 тощо) і ускладнює проектування впускних і випускних вікон в головці блока циліндрів з точки зору пропускної спроможності та опору потокові.
Двигуни цієї схеми зазвичай є тихохідними але мають гнучку моментну характеристику.
У світовій практиці легкового автомобілебудування такі двигуни були поширені з 1930-х (у США - з 1950-х) і до 1970-х років. Іноді такі двигуни використовувались до 1990-х років на недорогих автомобілях через свою дешевизну і компактність. Наприклад, Ford Ka першого покоління (1996-2002) використовував інжектовану версію чотирициліндрового двигуна Кент розробки кінця п'ятдесятих років з ГРМ типу OHV, який мав досить компактні за сучасними стандартами розміри, що дозволило вмістити двигун в невеликому моторному відсіку авто.
Схема OHV є популярною і на тихохідних чотиритактних двигунах для газонокосарок , бензинових електростанцій, мотоблоків. Сучасні тракторні двигуни також використовують дану схему.
Двигуни з розподільним валом в головці блока циліндрів (тип OHC)
Головка блока циліндрів двигуна D15A1 автомобіля Honda Integra 1987 року з приводом клапанів через коромислаГРМ с приводом клапанів штовхачамиСхема типу DOHC
Розподільні вали двигунів, виконані за схемами SOHC або DOHC, приводяться в рух зубчастим пасом або ланцюговою передачею. Найпоширенішим на легкових автомобілях є зубчастий пас. Перевага приводу зубчастим ременем - дешевизна та безшумність. Недоліки: у більшості двигунів обрив ременя викличе удар тарілок клапанів у днища поршнів. Щоб уникнути цього рекомендується строго дотримуватися встановленої періодичність заміни зубчастого ременя. Ресурс паса зазвичай становить від 50 до 150 тис. км. Пробігу авто.
Ланцюговий привод ГРМ є поширеним у верхньому ціновому сегменті легкових автомобілів, використовується в двигунах вантажних автомобілів. Ланцюг, зазвичай здвоєний, знаходиться в об'ємі двигуна, що омивається моторною оливою. Переваги: відсутність небезпеки раптового обриву, зношений ланцюг починає стукати, особливо на холодному двигуні, попереджаючи про необхідність заміни; більший ресурс - у 2-3 рази більший, ніж у зубчастого ременя; довговічність. Недоліки: велика вартість, шумність. Сильно зношений ланцюг може розтягуватися і перескакувати через декілька зубців зірочки - до катастрофічних для мотора наслідків це не приводить, але викликає зсув фаз газорозподілу і, відповідно, істотне порушення його роботи, яке не завжди відразу вірно діагностується при ремонті через схожість симптомів з іншими несправностями .
Тип SOHC
Докладніше: SOHC
Двигун з одним розподільним валом і клапанами в головці блока циліндрів (SOHC скор. від англ. Single OverHead Camshaft; також, англ. Overhead Camshaft) у залежності від конфігурації механізму урухомлення клапанів поділяються на двигуни з:
- приводом клапанів коромислами (Москвич-412, старі моделі BMW, Honda) - клапани розташовані з боків від розподільного вала (V-подібно), приводяться в рух насадженими на спільну вісь коромислами, одні кінці яких штовхаються кулачками вала, а інші приводять в рух стержні клапанів;
- приводом клапанів важелями (моделі від ВАЗ-2101 до ВАЗ-2107) - розподільний вал встановлюється над розташованими в ряд клапанами, урухомлює їх через важелі, що спираються на сферичні шарніри, штовхаючи їх кулачками у середній частині важелів. Недолік: підвищена шумність, високі навантаження у зоні контакту кулачка з важелем;
- приводом клапанів штовхачами (ВАЗ-2108) - простий механізм з мінімальною інерцією деталей, у якому розподільний вал розташований безпосередньо над клапанами, які спрямовані тарілками донизу, і переміщає їх через циліндричні штовхачі. Недолік: менша еластичність характеристик двигуна, складне регулювання клапанного проміжку.
Схема SOHC найбільше була поширена із середини 1960-х до 1980-х років. Окремі види двигунів («Renault Logan») випускались і пізніше.
Тип DOHC
Докладніше: DOHC
DOHC (від англ. Double OverHead Camshaft) - двигун з двома розподільними валами в головці блоку циліндрів.
При цьому існує два принципові різновиди цього механізму, що відрізняються кількістю клапанів.
DOHC з двома клапанами на циліндр. Ця схема є ускладненим різновидом звичайної схеми SOHC. В головці блока циліндрів розташовані два розподільних вали, один з яких урухомлює впускні клапани, другий - випускні. Ця схема мала застосування у 1960-х - 1970-х роках на високопотенційних двигунах таких автомобілів, як «Fiat 125», «Jaguar», «Alfa Romeo» тощо. Схема дозволяє значно збільшити частоту обертання колінчастого вала за рахунок зменшення його інерції і як наслідок, збільшити потужність двигуна.
ГРМ типу DOHC з 4-ма клапанами на циліндр
DOHC з чотирма і більше клапанами на циліндр. У схемі передбачається два розподільних вали, кожен з яких приводить свій ряд клапанів. Зазвичай, один розподільний вал штовхає два впускних клапани, другий - два випускних одного циліндра. Фактично, це дворядний варіант схеми SOHC з удвічі більшою кількість розподільних валів і клапанів, однак можуть бути реалізовані схеми із загальною кількістю клапанів на циліндр від 3-х до 6-ти. Привод клапанів, зазвичай здійснюється штовхачами.
Навіть якщо двигун має більше однієї головки блока циліндрів, а значить, більше двох розподільних валів, він все рівно належить до схеми DOHC.
Десмодромний газорозподільний механізм
Десмодромний ГРМ.
У десмодромному (англ. desmodromic) газорозподільному механізмі використовуються два розподільних вали (або один з кулачками складної форми): один відкриває клапани, а другий - закриває. Клапанні пружини відсутні.
Двигуни з десмодромним газорозподілом можуть працювати на частотах обертання, що не доступні для клапанних механізмів з пружинами, у яких при певних обертах колінчастого вала швидкості спрацьовування клапанних пружин не вистачатиме для того, щоб відвести клапани з-під удару поршня до досягнення ним верхньої мертвої точки («зависання» клапанів), що призводить до виходу двигуна з ладу.
Десмодромний механізм містить багато прецизійних деталей, є трудомістким і дорогим у виготовленні, вимагає якісного змащення. Цей механізм застосовувався на низці спортивних авто, наприклад, «Mercedes-Benz W196», «O.S.C.A. Barchetta» та «Mercedes-Benz 300 SLR», а також - на мотоциклах «Ducati».
Клапанні ГРМ без розподільного вала
У таких технічних рішеннях використовують електричний (соленоїди) або гідравлічний приводи клапанів. Перебувають на стадії дослідно-конструкторських розробок.
Клапанні ГРМ зі змінними фазами газорозподілу
Докладніше: Система зміни фаз газорозподілу
Більшість виробників автомобілів світового рівня пропонують на своїх двигунах систему зміни фаз газорозподілу, яка забезпечує регулювання параметрів відкриття клапанів відповідно до частоти обертання двигуна та навантаження на нього. Завдяки цьому досягається ефективніше використання потужності двигуна, зменшуються витрати пального та забрудненість вихлопу.
Зокрема, існують варіанти такої системи розробки фірм Honda (VTEC), Toyota (VVT-i), Mitsubishi (MIVEC), Nissan (VVL), BMW (VANOS), Ford (Ti-VCT) тощо.
Гільзова систем газорозподілу
Гільзовий газорозподіл на Bristol PerseusБудова ГРМ з ковзними гільзами
Гільзова система газорозподілу вперше розроблена американським інженером Чарльзом Найтом (англ. Charles Yale Knight), ще часто називається «системою Найта», хоча Найт розробив лише один з типів гільзового газорозподілу - з поздовжньо ковзними гільзами.
Система застосовувалась у першій половині XX ст. на дорогих легкових автомобілях - у першу чергу слід відзначити цілу серію SS (фр. «San-Soupape» - «без клапанів») французької фірми Panhard et Levassor і автомобілі фірми Avions Voisin з двигунами Найта (1919-1938), а також такі моделі, як Willys-Knight (1915-1933), Mercedes-Knight тощо.
Також, гільзовоий газорозподіл знаходив застосування в 1930-х роках в авіадвигунах, зокрема, британських таких, як Bristol Perseus, Bristol Pegasus, Bristol Hercules. Аналогічні конструкції механізмів широко застосовувалися і на парових машинах.
Принцип дії ґрунтується на відкритті/закритті вікон у стінках циліндра ковзними гільзами (англ. sleeve valves). На британських авіадвигунах застосовувалася не система Найта, а система Маккаллума, в якій гільзи ковзали не вздовж циліндра, а оберталися відносно нього, що було простішим у реалізації. Також існувало невелике число двигунів, що мали вікна не збоку циліндра, а в самій головці блока.
Головна перевага такої конструкції - повна безшумність. Крім того, зростала довговічність і покращувалось наповнення циліндрів паливно-повітряною сумішшю за рахунок великого розміру та меншого опору вікон в гільзах в порівнянні з каналами клапанів, особливо у порівнянні з нижньоклапанними двигунами.
Основні недоліки - складність конструкції та висока витрата моторної оливи.
Переваги цієї системи були особливо помітні в порівнянні з нижньоклапанними автомобільними двигунами першої половини XX століття, але після появи гідрокомпенсаторів клапанного зазору і верхнього розташування клапанів, вони практично зникли.
Поршнева система газорозподілу
Принцип роботи двотактного двигуна з поршневою системою газорозподілу
У двотактному двигуні роль ГРМ виконує сам поршень, а також, вихлопна система, а точніше - резонатор. Система досить проста: у стінках циліндра є впускні і випускні отвори, звані вікнами. Причому пальна суміш спочатку попадає в простір під поршнем, а потім через продувний канал спрямовується в камеру згоряння. Це пов'язано з тим, що простір під поршнем (називається кривошипною камерою) виконує роль своєрідного насоса. Так як ця камера герметично закрита згори поршнем, то при його русі тиск в ній змінюється (при русі поршня вгору об'єм камери збільшується, а тиск, відповідно, стає нижчим за атмосферний, при русі поршня вниз - навпаки). Саме завдяки цьому ефекту, суміш всмоктується в кривошипну камеру з впускного тракту, і далі переходить в камеру згоряння. Потім відбувається запалювання суміші і вихід відпрацьованих газів у випускну систему. Розміри і форма резонатора вихлопної системи розраховані таким чином, щоб хвилі високого тиску, які створюються при русі вихлопу «на вихід», відбивалися від стінок резонатора і перешкоджали виходу «свіжої» суміші з робочого простору циліндра
Тема Система мащення двигуна
Учбові питання
1. Призначення системи мащення.
2. Загальна будова системи мащення.
3.Принцип дії системи мащення.
1. Система мащення двигуна внутрішнього згорання виконує такі фунції:
а) мащення тертьових поверхонь
б) охолодження тертьових поверхонь
в) винос продуктів абразивного спрацювання у піддон картера
2. Система мащення двигуна включає в себе такі компоненти:а) піддон картера б) головна масляна магістраль в)масляний фільтр г) масляний насос д)щуп ж) масляний радіатор з) датчик тиску масла.
Піддон картера служить для зберігання і транспортування масла. Головна масляна магістраль призначена для подачі масла під тиском до тертьових поверхонь. Масляний фільтр очищає масло від бруду. Масляний фільтр відцентрової очистки називають ценрифугою. Масляний насос здійснює циркуляцію масла в системі. Для вимірювання рівня масла в піддоні картера служить щуп. Масляний радіатор призначений для охолодження масла. Датчик тиску масла вимірює тиск масла в системі і передає дані на контрольно - вимірювальні прилади.
3. На автомобільних двигунах застосовують комбіновану систему мащення при якій масло під тиском подається до найбільш навантажених поверхонь ( корінні і шатунні підшипники колінвала, підшипники компресора тощо) , а менш навантажені поверхні змащуються розбризкуванням.
Завдання для самостійної роботи: накреслити схему циркуляції масла в системі мащення.
Література: В.Ф. Кисликов, В. В. Лущик " Будова й експлуатація автомобілів" стр. 65 - 68
Тема; Система охолодження двигуна
Систе́ма рідинного охоло́дження - система в автомобілях призначена для підтримання оптимального теплового стану двигуна у межах 80-95°. При збільшенні температури в'язкість оливи зменшується, тому вона погано утримується в парах тертя, підвищується зношення деталей і зменшується потужність двигуна. При зниженні температури олива густішає: олива гірше подається в пари тертя, збільшується витрата палива - і зменшується потужність.
Основними недоліками системи рідинного охолодження є: більша складність конструкції і технічне обслуговування взимку і менша надійність в роботі (близько 20% усіх відмов двигуна припадає на рідинну систему охолодження).
Є три види рідинного охолодження: термосифонне, змішане, примусове.
Рідинна система охолодження складається з оболонки блока і головки блока, рідинної помпи, вентилятора, радіатора, термостата, жалюзі й різних патрубків, шлангів і краників.
Основна перевага термосифонної системи охолодження простота пристрою, а недолік - порівняно повільна циркуляція води в ній, що приводить до посиленого випарування води із системи, а отже, до необхідності частої перевірки рівня води і поповнення нею системи.
Зараз термосифонною системою охолодження обладнані тільки пускові двигуни П-1ОУД і П-350.
Різниця температур нагрітої й охолодженої води для системи з примусовою циркуляцією води не перевищує 100.
Термостат прискорює прогрів води при запуску двигуна й автоматично підтримує її температуру у визначених межах. Вони можуть бути з рідким чи твердим наповнювачем.
Недолік рідинних термостатів - велика чутливість до зміни тиску в системі, що робить роботу їх нечіткою. У двигунів ЗіЛ-130 і СМД-60 встановлені термостати з твердим наповнювачем, що позбавляє цього недоліку.
Температура води в системі охолодження контролюється за допомогою дистанційного чи електричного покажчика. У деяких двигунів (3М3-53, СМД-60) для контролю за температурою води в системі охолодження застосований електричний сигналізатор з контрольною лампою.
Види рідинного охолодження
- Термосифонне
- Змішане
- Примусове
Деталі та пристрої системи
- головка блоку циліндрів
- рідинний насос
- вентилятор
- радіатор
- термостат
- жалюзі
Принцип дії
Відцентровий насос, який дістає обертання за допомогою паса від шківа колінчастого вала, засмоктує охолодну рідину з нижньої частини радіатора через патрубок і нагнітає її в сорочку охолодження циліндрів. Охолоджувальна рідина омиває насамперед найбільш нагріті деталі двигуна, відбирає частину тепла, а потім через верхній патрубок подається у верхній бачок радіатора. Проходячи крізь серцевину радіатора в нижній бачок, нагріта рідина охолоджується й знову спрямовується до відцентрового насоса. Водночас частина нагрітої рідини надходить у сорочку впускного трубопроводу для підігрівання пальної суміші, а також у разі потреби відводиться через спеціальний кран в опалювач салону кузова.
,
Тема; Трансмісія
ПРИЗНАЧЕННЯ АВТОМОБІЛЬНОЇ ТРАНСМІСІЇ
Призначення даного механізму нескладне - передавати крутний момент, що надходить від мотора, на провідні колеса і змінювати швидкість обертання другорядних валів. При запуску двигуна маховик обертається відповідно до оборотами коленвала. Якби він мав жорстке зчеплення з провідними колесами, то на машині неможливо було б плавно починати рух, а кожна зупинка транспортного засобу вимагала б від водія глушити мотор.
Всім відомо, що для запуску двигуна використовується збільшують споживання електроенергії. Без трансмісії автомобіль відразу ж починав би свій рух, задіюючи цю енергію, що призведе до дуже швидкого розряду джерела живлення.
Трансмісія влаштована так, що водій має можливість від'єднати провідні колеса машини від мотора, щоб:
- Запускати двигун без перевитрати заряду АКБ;
- Прискорювати транспортний засіб, не підвищуючи обороти мотора до критичного значення;
- Використовувати рух накатом, наприклад, в разі буксирування;
- Вибирати такий режим, який не шкодив би мотору і забезпечував безпеку руху транспорту;
- Зупиняти машину без необхідності глушити ДВС (наприклад, на світлофорі або щоб пропустити пішоходів, що йдуть по зебрі).
Також трансмісія автомобіля дозволяє змінювати напрямок крутного моменту. Це потрібно для руху заднім ходом.
І ще одна особливість трансмісії в тому, щоб перетворювати швидкість обертання коленвала двигуна в прийнятну швидкість обертання коліс. Якби вони крутилися зі швидкістю в межах 7 тисяч, то або їх діаметр повинен був бути дуже маленьким, або всі машини були б спортивними, і на них не можна б було безпечно їздити по людних містах.
Трансмісія рівномірно розподіляє вивільняється потужність двигуна так, щоб момент трансформації робив можливим м'який і плавний старт, рух в гору, але разом з тим і дозволяв використовувати потужність ДВС для розгону транспортного засобу.
ТИПИ ТРАНСМІСІЙ
Хоча виробники розробили і продовжують створювати різні модифікації коробок передач, всіх їх можна розділити на чотири типи. Далі - коротко про особливості роботи кожної з них.
МЕХАНІЧНА КОРОБКА ПЕРЕДАЧ
Це найперший і найпопулярніший тип трансмісії. Навіть багато сучасних автомобілісти вибирають саме цю коробку передач. Причиною тому - більш просту будову, можливість використовувати ходову частину машини замість стартера, щоб завести мотор, якщо акумулятор розрядився (про те, як це зробити правильно, читайте тут).
Особливість цієї коробки полягає в тому, що водій сам визначає, коли і яку швидкість включити. Звичайно, це вимагає доброго розуміння, на якій швидкості можна переходити на підвищену або знижену передачу.
Завдяки своїй надійності і відносній простоті в обслуговуванні та ремонті даний тип трансмісії залишається на лідируючих позиціях в рейтингу КПП. Для виготовлення механіки виробник витрачає не так багато коштів і ресурсів, як для виробництва автоматів або роботів.
Перемикання передач відбувається наступним чином. У пристрій коробки входить диск зчеплення, який при натисканні на відповідну педаль роз'єднує маховик мотора від провідного механізму коробки. Поки зчеплення роз'єднане, водій переводить агрегат на іншу передачу. Так і автомобіль розганяється (або сповільнюється), і двигун не страждає.
У пристрій механічних коробок входить набір шестерень і валів, які з'єднані між собою таким чином, щоб водій зміг швидко переключити потрібну передачу. Для зниження шумності в механізмі використовуються шестерінки з косим розташуванням зубів. А для стабільності і швидкості зачеплення елементів в сучасних МКПП використовуються синхронізатори. Вони синхронізують швидкість обертання двох валів.
Інформація про пристрій механіки читайте в окремій статті.
РОБОТИЗОВАНА ТРАНСМІСІЯ
По пристрою і принципу дії роботи дуже схожі на механічні аналоги. Тільки в них вибір і перемикання передачі здійснює електроніка автомобіля. Більшість роботизованих коробок мають опцію ручного режиму, коли водій використовує важіль перемикання, розташований на селекторі режимів. Деякі моделі автомобілів замість цього важеля мають підрульові пелюстки, за допомогою яких водій підвищує або знижує передачу.
Для підвищення стабільності і надійності роботи сучасні роботи оснащуються системою подвійного зчеплення. Таку модифікацію називають селективної. Її особливість в тому, що один диск зчеплення забезпечує нормальний режим роботи коробки, а другий перед перемиканням наступної передачі готує механізми до активації швидкості.
Про інші особливості роботизованої системи перемикання передач читайте тут.
АВТОМАТИЧНА КОРОБКА ПЕРЕДАЧ
Така коробка в рейтингу подібних механізмів стоїть на другому місці після механіки. Така трансмісія при цьому має найскладніше будова. У ній є безліч додаткових елементів, в тому числі і датчиків. Однак на відміну від роботизованого і механічного аналога автомат позбавлений диска зчеплення. Замість нього використовується гідротрансформатор.
Гідротрансформатор - механізм, який працює на основі руху масла. Робоча рідина насосом подається на крильчатку муфти, яка приводить в рух провідний вал трансмісії. Відмінною особливістю даної коробки є відсутність жорсткого зчеплення механізму трансмісії з маховиком двигуна.
Автоматична трансмісія працює за схожим принципом, що і робот. Електроніка сама визначає момент переходу на потрібний режим. Крім цього багато автоматів оснащуються напівавтоматичним режимом, коли водій, використовуючи важіль перемикання, дає команду системі переходити на потрібну передачу.
Більш ранні модифікації оснащувалися тільки гидротрансформатором, але на сьогоднішній день існують і електронні модифікації. У другому випадку електронне управління може перемикатися в кілька режимів, кожному з яких відповідає своя система перемикання швидкостей.
,
ВАРІАТОР
Даний тип трансмісії також називається варіатором. Єдина коробка, в якій немає ступеневої перемикання швидкостей. Управління розподілом крутного моменту здійснюється за рахунок переміщення стінок шківа ведучого вала.
З'єднуються провідний і ведені вали за допомогою ременя або ланцюга. Вибір передавального числа визначає електроніка трансмісії на підставі інформації, що надходить з датчиків різних систем автомобіля.
Ось невелика таблиця плюсів і мінусів кожного типу коробок:
Тип коробки: Переваги: Недоліки:
МКПП (механіка) Високий ККД; Дозволяє економити паливо; Простий пристрій; Недорога в ремонті; Висока надійність. Новачкові потрібно багато тренуватися, щоб ефективно використовувати потенціал коробки; Порівняно з іншими КПП ця не забезпечує стільки комфорту.
"Робот" Комфорт при перемиканні (немає необхідності тягнутися до важеля кожен раз, коли потрібно переключитися); Електроніка визначать найоптимальніший момент переходу на потрібну передачу (особливо корисним це буде для тих, кому складно звикнути до цього параметру). Під час перемикання швидкості спостерігається затримка; Перехід на підвищену / знижену передачу часто супроводжується ривками; Не дає можливість водієві заощадити паливо.
автоматична Комфортне перемикання передач (плавне і практично невідчутне); При різкому натисканні на педаль газу переходить на знижену передачу, щоб максимально швидко прискорити автомобіль (наприклад, при обгоні). Дороге обслуговування та ремонт; Чи не економить паливо; Чи не економічна і по витраті масла; Складність в ремонті, через що потрібно шукати дорогий сервіс, не кожен механік здатний правильно налаштувати або відремонтувати механізм; Не можна завести мотор з буксира.
варіатор Саме плавне перемикання передавальних чисел без виведення мотора на підвищені обороти (що запобігає його перегрів); Підвищений комфорт при їзді; Дбайливе використання ресурсу мотора; Простота в управлінні автомобілем. Дороге обслуговування; Млявий розгін (в порівнянні з попередніми аналогами); Не дає можливості використовувати мотор в економічному режимі по галузі витрати палива; Не можна завести мотор з буксира.
,
МЕХАНІЧНА ТРАНСМІСІЯ
Особливість механічної трансмісії у тому, що весь процес переходу між передачами відбувається виключно з допомогою механічного втручання водія. Тільки він вичавлює зчеплення, перериваючи передачу моменту, що крутить, від маховика на диск зчеплення. Виключно завдяки діям водія відбувається перемикання передач і відновлення подачі моменту, що крутить, на шестірні коробки передач.
Але поняття механічної трансмісії не варто плутати із МКПП. Коробка - це агрегат, з допомогою якого відбувається розподіл тягових зусиль. У механічній трансмісії передача моменту, що крутить, відбувається за рахунок механічної передачі. Тобто всі елементи системи мають безпосереднє зчеплення один з одним.
Переваг у механічної передачі крутного моменту (в основному за рахунок шестерної з'єднання) кілька:
- Максимальний ККД, тому що не відбувається втрата потужності на роботу попутних механізмів, як, наприклад, гідротрансформаторі;
- Вартість механічної трансмісії найнижча серед ідентичних аналогів з іншим типом передачі моменту, що крутить, за рахунок більш простої конструкції;
- Все та ж проста конструкція дозволяє виробникам створювати агрегати з невеликими габаритами.
ГІДРОМЕХАНІЧНА ТРАНСМІСІЯ
У пристрій такого агрегату входить:
- Гідродинамічний перетворювач;
- Редуктор.
Переваги такої трансмісії в тому, що вона полегшує керування перемиканням швидкостей завдяки автоматизованому переходу між передачами. Також дана коробка забезпечує додаткове гасіння крутильних коливань. Завдяки цьому знижуються навантаження на деталі агрегату при максимальних навантаженнях.
До недоліків гідромеханічної трансмісії відноситься невеликий ККД через роботу гідротрансформатора. Так як в агрегаті використовується гідроблок з гидротрансформатором, йому потрібно більше масла. Для нього потрібна додаткова система охолодження. Через це коробка має збільшені розміри і більше ваги в порівнянні з аналогічною механікою або роботом.
ГІДРАВЛІЧНА ТРАНСМІСІЯ
Особливість такої коробки полягає в тому, що перемикання швидкостей виконується за допомогою гідравлічних вузлів. У конструкції агрегату може встановлюватися гідротрансформатор або гидромуфта. Цей механізм підключає потрібну пару валів і шестерень.
Перевагою гідравлічної трансмісії є плавне включення швидкостей. Крутний момент передається максимально м'яко, а крутильні коливання в такій коробці зведені до мінімуму завдяки ефективному гасінню цих зусиль.
До мінусів даної КПП відноситься необхідність у використанні індивідуальних гідромуфт для всіх передач. Через великих розмірів і ваги гідравлічна трансмісія використовується в залізничному транспорті.
ГИДРОСТАТИЧЕСКАЯ ТРАНСМІСІЯ
В основі такої коробки лежать аксіально-плунжерні гідроагрегати. Плюсами трансмісії є невеликі габарити і вага. Також в такій конструкції немає механічного зв'язку між ланками, завдяки чому вони можуть розлучатися на великі відстані. Завдяки цьому КПП має велике передавальне число.
Недоліки гідростатичної трансмісії в тому, що вона вимоглива до якості робочої рідини. Також вона чутлива до тиску в гідролінії, яка забезпечує перемикання передач. Через особливості КПП її використовують в основному в дорожньо-будівельній техніці.
ЕЛЕКТРОМЕХАНІЧНА ТРАНСМІСІЯ
У конструкції електромеханічної коробки використовується як мінімум один тяговий електродвигун. У ній встановлюється електрогенератор, а також контролер, керуючий виробленням потрібної для роботи КПП енергії.
Завдяки використанню електромотора (ів) забезпечується управління силою тяги. Крутний момент передається в більш широкому діапазоні, а між механічними вузлами відсутня жорстка зчіпка.
Мінусами такої трансмісії є великі розміри (використовується потужний генератор і один або кілька електродвигунів), а разом з тим і вага. Якщо порівнювати такі коробки з механічним аналогом, то у них значно менший ККД.
ВИДИ ТРАНСМІСІЙ АВТОМОБІЛЯ
Що стосується класифікацій автомобільних трансмісій, то всі ці агрегати діляться всього на три типи:
- передньо;
- Задній-;
- Повнопривідні.
Залежно від типу коробки ведучими будуть різні колеса (з назви трансмісії зрозуміло, куди надходить крутний момент). Розглянемо, чим відрізняються ці три типи автомобільних трансмісій.
ПЕРЕДНЬОПРИВІДНА ТРАНСМІСІЯ
Конструкція передньопривідною трансмісії складається з:
- Зчеплення (якщо це механіка або робот);
- Коробки передач;
- Головною передачі;
- диференціала;
- Валів, що призводять в обертання передні колеса.
Всі елементи такої трансмісії укладені в один блок, розташований поперек моторного відсіку. Зв'язка коробки і двигуна часом називається модель з поперечним розташуванням двигуна. Це означає, що машина з переднім або повним приводом.
ЗАДНЕПРИВОДНАЯ ТРАНСМІСІЯ
Конструкція задньопривідної трансмісії складається з:
- Зчеплення (якщо це механіка або робот);
- Коробки передач;
- Головною передачі;
- диференціала;
- Карданної передачі;
- Напіввісі.
Більшість класичних автомобілів оснащувалися саме такою трансмісією. Що стосується реалізації передачі крутного моменту, то заднеприводная трансмісія максимально проста для цього завдання. Карданний вал з'єднує задній міст з коробкою передач. Для зниження вібрацій використовуються опори, трохи м'якше тих, що встановлюються в передньопривідних машинах.
ПОВНОПРИВОДНА ТРАНСМІСІЯ
Такий тип трансмісії відрізняється більш складним пристроєм (детально про те, що таке повний привід, і як в ньому реалізується передача крутного моменту, читайте окремо). Причина в тому, що агрегат повинен одночасно розподіляти крутний момент на всі колеса. Існує три різновиди такої трансмісії:
- Постійний повний привід. У такому виконанні агрегат оснащується межосних диференціалом, який розподіляє крутний момент на обидві осі, і в залежності від якості зчеплення коліс з дорожнім покриттям міняти зусилля між ними.
- Ручне підключення повного приводу. У цьому випадку конструкція оснащується роздавальної коробкою (докладно про цей механізм читайте в іншій статті). Водій самостійно визначає, в який момент потрібно включити другу вісь. За замовчуванням автомобіль може бути як передньо-, так і задньопривідним. Замість міжосьового диференціала, як правило, використовуються міжколісні.
- Автоматично підключається повний привід. У таких модифікаціях замість міжосьового диференціала встановлюється вязкостная муфта або аналог фрикційного типу. Приклад того, як працює така муфта, розглядається DMесь.
АГРЕГАТИ ТРАНСМІСІЇ АВТОМОБІЛЯ
Незалежно від типу трансмісії, цей механізм складається з декількох вузлів, які забезпечують ефективність і високий ККД пристрою. І з яких агрегатів складається коробка передач.Тема: Зчеплення
Зчеплення є важливим конструктивним елементом трансмісії автомобіля. Головне завдання зчеплення автомобіля - передати крутний момент від двигуна. При роботі зчеплення короткочасно від'єднує двигун від трансмісії і потім плавно їх з'єднує. Крім усього іншого зчеплення охороняє деталі трансмісії від перевантажень. Про це ми і розповімо у статті «Ремонт і технічне обслуговування зчеплення».
Зчеплення складається з приводу, що включає в себе педаль, тягу, вилку і муфту з вижимним підшипником. Як тільки водій відпустить педаль зчеплення буде включено. Включення відбувається у момент, коли ведений диск притиснутий до маховика натискним диском за допомогою пружини. Шляхом тертя поверхні веденого диска з маховиком і натискним диском відбувається процес зчеплення. Як тільки водій натисне на педаль зчеплення, він вимкнеться. Вимикання відбувається через переміщення до маховика муфти з вижимним підшипником, при цьому відсувається натискний диск від веденого диска. То є ведучі і ведені деталі зчеплення між собою роз'єднуються.
Зчеплення здійснюється за допомогою силової муфти, в якості якої можуть виступати фрикційні, гідравлічні та електромагнітні муфти. Залежно від того, яка муфта встановлена, і передача обертального моменту здійснюється силами тертя, гідродинамічними силами або за допомогою електромагнітного поля. Зчеплення призначене для з'єднання або тимчасового роз'єднання двигуна і трансмісії. Тимчасово роз'єднати двигун і трансмісію потрібно під час перемикання передач, при зупинці або гальмуванні. А після того, як автомобіль рушить з місця і після перемикання передач необхідно їх плавно з'єднати.
Трансмісія з подвійним зчепленням
Трансмі́сія з подві́йним зче́пленням (англ. dual-clutch transmisstion, DCT) - автомобільна трансмісія у якій муфта зчеплення складається з двох фрикційних муфт, які працюють почергово при перемиканні передач. Така конструкція найчастіше використовується для оснащення роботизованих коробок передач, що забезпечує парні і непарні передачі фактично окремими муфтами зчеплення. Тому часто, коли мова йде про подвійне зчеплення використовують поняття «коробка передач з подвійним зчепленням» або «трансмісія з подвійним зчепленням» (англ. dual-clutch transmission, DCT), так як муфта подвійного зчеплення тісно пов'язана з особливою конфігурацією коробки перемикання передач. Така конструкція створює можливість попереднього вибору чергової передачі чим скорочує час на перемикання передач, яке відбувається практично без розриву потоку потужності від двигуна на колеса автомобіля. Тому іншою назвою роботизованої коробки передач з подвійним зчепленням ще є - преселективна коробка передач (від англ. preselect - попередньо обрати)
Ідея створення трансмісії, що має два зчеплення, належить французькому інженеру-механіку і винахіднику Адольфу Кегрессу[fr][1]. У другій половині 1930-х він висунув ідею та спроектував автоматичну коробку перемикання передач з подвійним зчепленням, яку сподівався встановити на легендарний Citroën Traction. Але складне фінансове становище компанії на той час не дозволило планам здійснитися.
Реальне застосування подвійного зчеплення у конструкції коробок передач розпочалось з 1980 року завдяки розробкам компаній Porsche та Audi для своїх спортивних автомобілів. У 1986 році Porsche 962, оснащений саме цією коробкою, переміг у 1000-кілометровій гонці на автодромі у Монці. У подальшому подвійне зчеплення стало використовуватись у таких конструкціях коробок перемикання передач серійних автомобілів:
- DSG (нім. Direkt Schalt Getrieb) від Volkswagen[2];
- M DCT (англ. M double-clutch transmission) від BMW[3];
- «Powershift» від Ford[4];
- «Speedshift» від Mercedes-Benz;
- DDCT (англ. Dual Dry Cutch Trasmission) від Fiat Powertrain Technologies[en];
- EDC (англ. Efficient Dual Clutch) від Renault;
- DCS (англ. Dual Clutch System) від Groupe PSA;
- DCT (англ. Dual-Clutch Transmission) від Kia Motors;
- «S-tronic» від Audi;
- «Twin Clutch SST» від Mitsubishi;
- 7DT від Porsche.
Через високу технічну складність конструкції виробників подвійного зчеплення є небагато і серед них такі компанії як:
- BorgWarner («мокре» зчеплення для Volkswagen);
- Getrag з 2018 Magna PT[en] (коробки передач з як із «сухим», так і «мокрим» подвійним зчепленням для BMW, Chrysler, Dodge, Ferrari, Ford, Mercedes-Benz, Mitsubishi, Renault, Volvo);
- Schaeffler Group[en] під брендом «LuK» («сухе» зчеплення для Volkswagen);
- Ricardo plc[en] (коробка передач для Bugatti Veyron);
- ZF Friedrichshafen AG (коробка передач для Porsche);
- Fiat Powertrain Technologies[en] (коробки передач для Alfa Romeo, Fiat, Jeep, Suzuki).
Низка автомобільних компаній у конструкції трансмісій можуть використовувати компоненти від різних виробників, наприклад, в M DCT (BMW) використовується коробка передач від «Getrag», а подвійне зчеплення від «BorgWarner».
Розрізняють два основні типи конструкцій подвійного зчеплення: «сухе» (фрикційні диски у повітрі) і «мокре» (багатодискове зчеплення знаходится зануреним в оливі).
«Мокре» подвійне зчеплення
Конструктивно подвійне зчеплення мокрого типу об'єднує два пакети фрикційних дисків, поміщених у корпус. Частина дисків обох пакетів жорстко пов'язана з корпусом зчеплення. Корпус, у свою чергу, через маточини з'єднаний з двигуном. Інша частина дисків закріплена на своїх маточинах, які посаджені на первинні вали відповідних рядів передач.
Нормальне положення зчеплення - розімкнене. Замикання зчеплення (стискання пакетів дисків) здійснюється за допомогою гідроциліндрів під керуванням електрогідравлічного модуля. У вихідне положення диски повертаються за допомогою пружин.
Залежно від конструкції зчеплення пакети фрикційних дисків можуть мати концентричне (муфти розташовані в одній площині, перпендикулярно до первинного вала) або паралельне розташування (муфти розташовуються одна за одною паралельно).
Концентричне розташування муфт є компактнішим, тому застосовується в трансмісіях передньоприводних автомобілів (при поперечному розташуванні двигуна). При концентричному розташуванні зовнішня муфта обслуговує непарні передачі, внутрішня - парні передачі. В силу своєї конструкції (велика площа дисків) зовнішня муфта розрахована на передачу більшого крутного моменту. Подвійне зчеплення з паралельним розташуванням дисків застосовується, в основному, на задньоприводних автомобілях.
«Сухе» подвійне зчеплення
Подвійне зчеплення сухого типу включає ведучий диск, з'єднаний з двохмасовим маховиком, два сухих диски зчеплення, розташованих на первинних валах коробки передач, два натискних диски, дві діафрагмових пружини, два витискні підшипники і два важелі включення зчеплення. Нормальне положення сухого зчеплення - розімкнуте.
Принцип роботи зчеплення полягає у передаванні крутного моменту від ведучого диска на відповідний диск зчеплення і далі на свій первинний вал коробки передач. Кожне із сухих зчеплень працює незалежно одне від одного.
При замиканні зчеплення важіль увімкнення притискає витискний підшипник до діафрагмової пружини, яка у свою чергу передає зусилля на натискний диск і далі на диск зчеплення. Диск зчеплення притискається до ведучого диска і крутний момент передається на первинний вал коробки передач.
Порівняння двох типів подвійного зчеплення
«Мокре» зчеплення має краще охолодження, тому може застосовуватись для передавання більшого крутного моменту (до 350 Нм і більше). Наприклад, «мокре» зчеплення у коробці передач «Bugatti Veyron» забезпечує передачу крутного моменту до 1250 Нм. Межа «сухого» зчеплення - 250 Нм. Разом з тим, «сухе» зчеплення є ефективнішим в експлуатації, оскільки в ньому відсутні витрати потужності двигуна на урухомлення масляного насоса
Переваги
- Конструкція з двома поперемінно працюючими валами дозволяє добитися максимальної плавності у їзді.
- Переключення передач здійснюється за максимально короткий проміжок часу (до 0,12 с).
- Підтримання й передавання крутного моменту без відчутних втрат при перемиканні.
- Менша (до 10 %) витрата пального (навіть у порівнянні з механічними коробками перемикання передач).
- Висока динамічність при розгоні.
Недоліки
- Малий ресурс пробігу, при поміркованій експлуатаці пробіг до ремонту становить 60...80 тис. кілометрів.
- Конструкція коробок перемикання передач є складнішою у порівнянні з автоматичною чи механчною коробкою перемикання передач, що обумовлює відповідно вищу ціну.
- Не всі автомобільні майстерні можуть надати кваліфіковані послуги з ремонту і обслуговування таких трансмісій.
- Через складність і дороговизну матеріалів обслуговування трансмісій з подвійним зчепленням є зна дорожч
- Тема: Коробка передач
Щоб автомобіль пересувався по дорозі, мало мати під капотом потужний і ефективний мотор. Крутний момент від колінчастого вала повинен якось передаватися на провідні колеса транспортного засобу.
З цією метою було створено спеціальний механізм - коробка передач. Розглянемо її пристрій і призначення, а також чим відрізняються різні модифікації КП.
ПРИЗНАЧЕННЯ КОРОБКИ ПЕРЕДАЧ
Якщо сказати коротко, то коробка передач призначена для передачі крутного моменту від силового агрегату на провідні колеса. Трансмісія також перетворює швидкість обертання колінвала так, щоб водій міг розігнати машину, не розкручуючи мотор до максимальних обертів.
Даний механізм підбирається під параметри ДВС, щоб максимально використовувати весь ресурс двигуна без шкоди для його деталей. Завдяки трансмісії машина може виконувати рух як вперед, так і назад.
Всі сучасні автомобілі мають таку трансмісію, яка дозволяє тимчасово відключити жорстку зчеплення клонували з провідними колесами. Це дає можливість машині рухатися на холостому ходу, наприклад, плавно наближаючись до світлофора. Даний механізм також дозволяє не глушити двигун, коли авто зупиняється. Це необхідно для підзарядки акумулятора і роботи додаткового обладнання, наприклад, кондиціонера.
Кожна КП повинна відповідати таким вимогам:
- Забезпечувати тягу автомобіля і економічна витрата палива в залежності від потужності і обєму мотора;
- Простота у використанні (водій не повинен відволікатися від дороги при зміні швидкості ТЗ);
- Не видавати шум під час роботи;
- Високу надійність і ККД;
- Мінімальні габарити (наскільки це можливо у випадку з потужними транспортними засобами).
ПРИСТРІЙ КОРОБКИ ПЕРЕДАЧ
У пристрій будь-коробки передач входить:
- Корпус. У ньому знаходяться всі необхідні деталі, що забезпечують зчеплення мотора з приводним валом, від якого обертання надходить на колеса.
- Резервуар з маслом. Так як в даному механізмі деталі стикаються один з одним під великим навантаженням, мастило забезпечує їх охолодження і створює масляну плівку, яка захищає від передчасної вироблення на шестернях.
- Механізм передачі швидкості. Залежно від типу коробки до складу механізму можуть входити вали, набір шестерень, планетарний редуктор, гідротрансформатор, фрикційні диски, ремені і шківи.
КЛАСИФІКАЦІЯ КП
ЗА СПОСОБОМ ПЕРЕДАЧІ ПОТОКУ ПОТУЖНОСТІ
У цю категорію ввійшли такі КП:
- Механічна КП. У такій модифікації відбір потужностей проводиться зубчастої передачею.
- КП з співісними валами. Обертання передається теж через зубчасту передачу, тільки її елементи виконані в конічної або циліндричної форми.
- Планетарна. Передача обертання виробляється через планетарний ряд, шестерні якого розташовані в одній площині.
- Гідромеханічна. У такій трансмісії механічна передача (в основному планетарний тип) використовується спільно з гидротрансформатором або гідромуфтою.
- Варіаторная. Це різновид КП, в яких не використовується ступіньчаста передача. Найчастіше такий механізм працює разом з гідромуфтою і ремінним з'єднанням.
ЗА КІЛЬКІСТЮ ОСНОВНИХ ВАЛІВ З ШЕСТЕРНЯМИ
При класифікації КП за кількістю валів розрізняють:
- З двома валами і одноступіньчастим зачепленням осі. У таких трансмісіях немає прямої передачі. Найчастіше такі модифікації можна зустріти в машинах з переднім приводом. У деяких моделях із заднім розташуванням моторів також встановлена подібна коробка.
- З трьома валами і двоступіньчастим зачепленням осі. У цій категорії є модифікації з співісними і Неспіввісність валами. У першому випадку мається пряма передача. У поперечному розрізі вона має менші габарити, а в довжину трохи більші. Такі коробки використовуються в задньопривідних авто. Друга категорія не має прямої передачі. В основному така модифікація використовується в машинах з повним приводом і в тракторах.
- З кількома валами. У цій категорії КП вали можуть мати послідовне або непослідовне число зачеплень. Такі коробки передач використовуються в основному в тракторах і верстатах. Це дозволяє збільшити кількість передач.
КЛАСИФІКАЦІЯ ПЛАНЕТАРНИХ КП
Планетарні коробки передач діляться за такими параметрами:
- Дві, три, чотири і більше ступеня свободи, коли всі фрикційні елементи від'єднані;
- Тип планетарного ряду, який використовується в механізмі - епіциклічних (основний вінець має внутрішнє або зовнішнє розташування зубів).
ЗА СПОСОБОМ УПРАВЛІННЯ
У даній категорії є такі коробки:
- Ручна. У таких моделях вибір потрібної передачі здійснює водій. Існує два види ручних трансмісій: перемикання проводиться зусиллями водія або через сервопривід. В обох випадках управління здійснює людина, тільки друга категорія КП має сервопристрій Воно отримує сигнал від водія, після чого встановлює обрану передачу. В машинах найчастіше використовується гідравлічний сервопривід.
- Автоматична. Електронний блок управління визначає кілька чинників (ступінь натискання акселератора, навантаження, що надходить від коліс, обороти колінвала і ін.) І на підставі цього сам визначає, коли включити підвищену або знижену передачу.
- Робот. Це електромеханічна коробка. У ній передачі включаються в автоматичному режимі, тільки її пристрій - як у звичайній механіки. При роботі роботизованої трансмісії водій не бере участі в перемиканні передач. Блок управління сам визначає, коли яку передачу включити. При цьому перемикання відбувається практично непомітно.
ЗА КІЛЬКІСТЮ ПЕРЕДАЧ
Дана класифікація найпростіша. У ній все коробки поділяються за кількістю передач, наприклад, чотири, п'ять шість і так далі. У цю категорію входять не тільки ручні, а й автоматичні моделі.
ТИПИ КОРОБОК ПЕРЕДАЧ
Найпоширеніша класифікація - за типом самої коробки:
- Механіка. У таких моделях вибір і перемикання передач виконується повністю зусиллями водія. В основному це редуктор з декількома валами, робота якого здійснюється через шестерну передачу.
- Автомат. Така трансмісія працює в автоматичному режимі. Вибір необхідної передачі здійснюється на підставі параметрів, які заміряє система управління коробкою.
- Робот є різновидом механічної КП. Конструкція цієї модифікації практично нічим не відрізняється від звичайної механіки: в ній є зчеплення, а передачі включаються через під'єднання відповідної шестерні на відомому валу. Тільки управління вибором передач керує комп'ютер, а не водій. Гідність такої трансмісії - максимально плавне перемикання.
НЕСИНХРОНІЗОВАНИХ КП
До ще одного різновиду специфічних коробок відноситься несинхронізованих або та, в конструкції якої не передбачено наявність синхронізаторів. Це може бути тип з постійним зачепленням шестерень або зі легкими шестернями.
Щоб переключити передачу в такій коробці, водій повинен мати певний навичкою. Він повинен вміти самостійно синхронізувати обертання шестерень і муфт, визначаючи час переходу від передачі до передачі, а також вирівнюючи швидкість обертання коленвала акселератором. Професіонали називають цю процедуру перегазовкой або подвійним вижимом зчеплення.
Для виконання плавного перемикання водій повинен мати досвід в управлінні такими механізмами. Подібний тип трансмісії встановлюється в американських тягачах, мотоциклах, іноді в тракторах і спортивних автомобілях. В сучасних несинхронізованих трансмісіях можна не використовувати зчеплення.
КУЛАЧКОВА КП
Кулачкові коробки це різновид несинхронізованою моделі. Відмінністю є форма зачіпляються зубів. Для підвищення ККД коробки передач використовується прямокутна форма або кулачковий профіль зубів.
Такі коробки дуже галасливі, тому в легковому транспорті використовуються в основному на гоночних авто. Під час змагань на цей фактор не звертається увага, але в звичайному автомобілі така трансмісія не дасть можливості отримати насолоду від поїздки.
ПОСЛІДОВНА КП
Під секвентальною коробкою мається на увазі тип трансмісії, в якому перехід на знижену або підвищену передачу здійснюється виключно на один щабель. Для цього використовується ручка або ножний перемикач (на мотоциклах), який дозволяє перемістити шестерню в кошику виключно на одну позицію за одне натискання.
Схожий принцип роботи має автоматична коробка типу Привід, але вона лише імітує дію даної трансмісії. Класична секвентальная коробка встановлюється в болідах F-1. Перемикання швидкості в них здійснюється за допомогою підрульових пелюсток.
ПРЕСЕЛЕКТИВНА CP
У класичному виконанні преселективна КП вимагала попереднього вибору наступної передачі до того, як коробка на неї переключиться. Часто це виглядало так. Під час руху авто водій виставляв на селекторі наступну передачу. Механізм готувався до перемикання, але виконував це по команді, наприклад, після натискання на зчеплення.
Раніше такі КП використовувалися у військовій техніці з несинхронізованою, безвальной або планетарної трансмісією. Такі модифікації коробок полегшували управління складними механізмами, поки не були розроблені синхронізовані механічні та автоматичні коробки.
В даний час преселективна коробка використовується, але вона частіше називається трансмісією з подвійним зчепленням. У цьому випадку комп'ютер сам готує перехід на потрібну швидкість, заздалегідь під'єднуючи до незафіксованим диску відповідний вал з включеною передачею. Інша назва цього типу в сучасному виконанні - робот.
ВИБІР КОРОБКИ ПЕРЕДАЧ. ЩО КРАЩЕ?
Багато хто з перерахованих коробок передач використовуються тільки на спецтехніці або в верстатах. Основними КП, які мають широке застосування в легковому транспорті, є:
- Механічна коробка передач. Це найпростіший тип трансмісії. Щоб обертальний рух передавалося з силового агрегату на вал КП, використовується кошик зчеплення. Натисканням педалі водій від'єднує провідний вал коробки від мотора, що дозволяє йому без шкоди для механізму вибрати відповідну для даної швидкості передачу.
- Автоматична коробка передач. Крутний момент від мотора подається через гідропередачу (гідротрансформатор або гидромуфта). Робоча рідина грає роль зчеплення в механізмі. Вона приводить в рух, як правило, планетарний редуктор. Вся система управляється електронним блоком управління, який аналізує дані з багатьох датчиків і відповідно до цього вибирає передавальне число. Серед автоматичних коробок є багато модифікацій, в яких використовуються різні схеми роботи (залежить від виробника). Існують навіть автоматичні моделі з можливістю ручного управління.
- Роботизована коробка передач. Серед таких КП також є свої різновиди. Існують електричні, гідравлічні і комбіновані типи. За конструкцією робот в основному схожий на механічну коробку, тільки з подвійним зчепленням. Перше подає крутний момент від мотора до провідних колесам, а друге автоматично готує механізм до включення наступної передачі.
- Варіаторная коробка передач. У поширеному виконанні варіатор представляє собою два шківа, які з'єднані між собою ременем (одним або декількома). Принцип дії наступний. Шків розсується або зсувається, в результаті чого ремінь переміщається на елемент з більшим чи меншим діаметром. Від цього і змінюється передавальне число.
- Тема: Складові гальмівної системи
Будь-яка гальмівна система складається з привода і гальмівного механізму.
Привод може бути механічним, гідравлічним, пневматичним, електричним і комбінованим. Електричний привод на сьогодні в чистому вигляді не застосовується.
Гальмівні механізми також бувають барабанні, дискові та стрічкові. Останні, до слова сказати, можна зустріти хіба що на гусеничній техніці.
7.2.2 Привод гальмівних механізмів
На вантажних автомобілях середньої та великої вантажопідйомності використовується пневматичний привод (на догоду довжині всіх приводів), але ми зупинимося на розгляді гідравлічного привода гальм - найпопулярнішого для легкових автомобілів.
Примітка
Привод - це набір механізмів і деталей, покликаних передавати зусилля, тягу або переміщення.Ця система базується на властивості рідин не стискатися.
Складається гідропривод гальм з таких елементів
- педалі гальма;
- головного гальмівного циліндра;
- вакуумного підсилювача;
- патрубків гідропривода і гальмівних шлангів;
- передніх і задніх робочих гальмівних циліндрів, які розташовані в гальмівних механізмах.
7.2.3 Принцип роботи гальмівних механізмів
Принцип роботи полягає в наступному: педаль гальма через шток зв'язується з поршнем, який переміщується в головному гальмівному циліндрі заповненому гальмівною рідиною, як, утім, і всі патрубки та шланги гальмівної системи.
При натисканні на педаль гальма поршень у циліндрі переміщується, тисне на рідину, яка передає зусилля на робочі гальмівні циліндри гальмівних механізмів. Все просто. Якщо не зрозуміло, не варто відразу бентежитися, оскільки далі в розділі буде описано роботу кожного елемента гальмівної системи.
Окрім того, що за допомогою головного гальмівного циліндра зусилля передається від педалі до гальмівних механізмів, також головний циліндр забезпечує розділення контурів (див. далі).
Над головним гальмівним циліндром встановлено розширювальний бачок, необхідний для компенсації розширення гальмівної рідини при її нагріві та для запобігання потраплянню повітря в систему гідропривода гальм (для цього необхідно завжди стежити за рівнем гальмівної рідини в бачку і не допускати його падіння нижче позначки «MIN»).
Розширювальний бачок розділений на два резервуари (або має один резервуар, але з розділовою перегородкою), які сполучаються з головним гальмівним циліндром системи через два отвори. На поршнях є кільцеві ущільнювальні манжети, які притискаються пружинами.
Примітка
Крім проточки, поршні мають кільцеві порожнини і пласкі кутоподібні пази, які з'єднуються з резервуаром при будь-якому положенні поршнів. Це перешкоджає потраплянню повітря в гідравлічну магістраль.Увага
Одним із найнебезпечніших, з точки зору потрапляння повітря в головний гальмівний циліндр, є момент режиму розгальмовування, який часто виконується різко, кидком педалі. У такому разі рідина внаслідок її певної в'язкості повертається в головний гальмівний циліндр відносно повільно і поршні під дією пружин прагнуть начебто відірватися від рідини, внаслідок чого в магістралі створюється розрідження. При цьому запобігти потраплянню повітря в магістраль одними тільки ущільненнями майже неможливо, тому з тильного боку поршнів або в них самих розташовують порожнини, заповнені рідиною.Технології розвиваються, і, щоб не обтяжувати водія постійними перевірками рівня гальмівної рідини, в розширювальному бачку встановлюють поплавець і приєднують до нього датчик рівня гальмівної рідини. Щойно цей рівень впаде нижче заданого, на приладовому щитку в салоні автомобіля загориться відповідний сигналізатор, а може ще й спрацює звукова сигналізація.
Примітка
Запобігти потраплянню повітря в гідропривод гальмівної системи практично неможливо. Так, при заміні будь-яких елементів гальмівної системи доведеться зливати частину гальмівної рідини. А залити свіжу гальмівну рідину без потрапляння повітря неможливо.
Також при перегріванні гальмівних механізмів ця рідина може почати кипіти, утворюючи бульбашки повітря.Для видалення повітря з гідропривода гальм у найвищих точках кожного елемента гальмівної системи передбачено так звані сапуни. Сапун - це порожнистий болт, який виступає в ролі клапана, але з «ручним приводом». При відкручуванні сапуна «клапан» відчиняється, при закручуванні - зачиняється.
Примітка
Як виконуються операції з видалення повітря («прокачування», простіше) з гідропривода гальмівної системи, можна знайти в будь-якій книжці щодо ремонту та обслуговування автомобілів.Кінцевим елементом гідропривода є робочий циліндр. Якщо гальмівні механізми барабанні, то робочий циліндр є окремою деталлю, якщо гальма дискові, то він інтегрований у гальмівний супорт гальмівних механізмів
7.2.4 Регулятор тиску
У систему гідропривода гальм встановлюють регулятор тиску гальмівної рідини. Для чого він потрібен?
Задні колеса мають починати гальмування на мить раніше передніх. Це зроблено для того, щоб запобігти занесенню автомобіля, якщо його колеса потраплять на слизьку поверхню. Але процес руху досить складний, і автомобіль може бути завантажений поклажею чи пасажирами, внаслідок чого навантаження на задню вісь підвищиться. А якщо задня вісь стане важчою, для її гальмування доведеться докласти більше зусилля. От саме для того, щоб водій не був обтяжений думками про розподіл гальмівних зусиль між передньою і задньою віссю, в гідропривод гальм «врізали» регулятор.
Регулятор тиску коригує тиск гальмівної рідини в системі задніх гальмівних механізмів залежно від зміни навантаження на задні колеса.
7.2.5 Гальмівні рідини, що застосовуються
До гальмівної рідини пред'являють жорсткі вимоги, оскільки вона працює в украй агресивних умовах: під впливом високих і низьких температур. Тому основним показником, що характеризує гальмівну рідину, є температура її кипіння: що вона вища, то краще. Взагалі, кипіння для гальмівної рідини - це шлях до зниження ефективності гальмування практично до нуля: рідина закипіла, з'явилися пухирці повітря, педаль провалилася, а гальмування так і не почалося. Також не варто забувати про те, що низькі температури можуть призвести до замерзання гальмівної рідини, результатом чого також буде втрата ефективності гальмування.
Увага
Гальмівна рідина украй гігроскопічна. Це означає, що вона має властивість поглинати вологу, що міститься в повітрі. Попадання вологи в гальмівну рідину призведе до зниження температури її кипіння і появи кристалів льоду при замерзанні, внаслідок чого миттєво знизиться ефективність гальмівної системи в цілому.Разом з автомобілем поставляється й інструкція з експлуатації. Якщо в автомобілі її немає, відповідний посібник можна придбати окремо. У такій інструкції обов'язково буде вказано тип гальмівної рідини за класифікацією Департаменту транспорту США - DOT.
На сьогодні найпоширеніші гальмівні рідини мають позначення DOT3, DOT4, DOT4+ і DOT5.1. Причому доливати в розширювальний бачок головного гальмівного циліндра рідину вищого класу допускається (наприклад, DOT4 долити в бачок із рідиною DOT3), звичайно, за умови, що обидві рідини випущені одним і тим же виробником. І навпаки, доливати в бачок з DOT4 рідину класу DOT3 не слід.
7.2.6 Барабанні гальмівні механізми
Свого часу це був дуже поширений тип гальмівних механізмів. Улаштування найпростіше (малюнок 7.3): гальмівний щиток, що не обертається і жорстко закріплений на поворотному кулаку* (якщо це керовані передні колеса) або на цапфі (якщо це задня вісь), на гальмівний щиток встановлено робочий гальмівний циліндр, також гальмівні колодки, які одним кінцем спираються на опори, а іншим - упираються в поршні робочого гальмівного циліндра. На гальмівні колодки наклеєні або приклепані фрикційні накладки, зверху усі ці деталі накриваються гальмівним барабаном, який обертається разом із колесом.
Якщо раптом знадобилося знизити швидкість або зупинитися, водій, натискаючи на педаль гальма, через гідропривод впливає на поршні робочого гальмівного циліндра, які, переміщуючись, розсовують гальмівні колодки, притискаючи їх до поверхні гальмівного барабана.
Існує кілька схем розташування гальмівних колодок.
Цікаво
У барабанному гальмівному механізмі,одна з найпоширеніших схем розташування колодок), дві колодки встановлені послідовно одна за одною. Одна колодка - передня, інша - задня (по ходу руху). Причому обидві колодки знизу встановлені на осях, а зверху впираються в поршні робочого циліндра. При гальмуванні сили діятимуть так, що передня колодка буде нібито підклинювати, а задню колодку створювані зусилля намагатимуться відсунути від барабана. Цим може бути викликаний нерівномірний знос фрикційних накладок. Так само цей ефект призводить до того, що робочі поверхні фрикційних накладок використовуються не повною мірою.Для того щоб після гальмування гальмівні колодки повернулися у вихідне положення, встановлено відвідні пружини.
Зазор між колодками і барабаном часто регулюється автоматично. Реалізовано це просто: поршні робочих циліндрів, переміщуючись назовні під дією тиску рідини, виберуть наявний між ними і пружними кільцями осьовий зазор, після чого потягнуть кільця за собою. Рух поршнів триватиме доти, доки колодки не упруться в барабан. При відпусканні педалі відвідні пружини зможуть перемістити поршні назад тільки на величину, відповідну осьовому зазору між поршнем і кільцем, оскільки зрушити кільце вони не в змозі.
Величина зазора, як було сказано вище, відповідає необхідному зазору між колодкою і барабаном. Таким чином, у міру зношування накладок кільце переміщатиметься уздовж циліндра, підтримуючи постійну величину зазора в механізмі.
Барабанні гальмівні механізми мають низку переваг, порівняно з дисковими гальмами, однак і вад чимало.
Переваги:
- велика робоча поверхня гальмівних колодок і можливість її збільшення як за рахунок діаметра гальмівного барабана, так і його ширини (корисна властивість для вантажних автомобілів);
- відносна захищеність гальмівного механізму від пилу і бруду;
- стійкість елементів гальмівного механізму до перепаду температур.
Вади:
- мала, порівняно з дисковими гальмами, потужність, що розвивається;
- велика інерційність елементів гальмівного механізму;
- чутливість до перегріву.
7.2.7 Дискові гальмівні механізми
Єдиною перспективною альтернативою барабанних механізмів для легкових автомобілів стали дискові гальмівні механізми. У таких механізмах гальмівний диск кріпиться до маточини колеса і обертається разом із колесом. Щоб зупинити автомобіль, необхідно підвести під тиском гальмівну рідину до поршня в гальмівному супорті. Поршень, впливаючи на гальмівні колодки, передасть на них зусилля від гальмівної рідини, притисне до диска і почне уповільнювати колесо. Чимось принцип дії дискового гальма схожий на велосипедне гальмо, де роль диска відіграє поверхня обода колеса, а зупинка здійснюється притисканням колодок гальма до обода
Примітка
Існує два типи гальмівних супортів: фіксований і плаваючий. У першому випадку в гальмівному супорті є два поршні, розташовані по обидва боки від гальмівного диска. Сам супорт жорстко закріплений на поворотному кулаку. Поршні впливають на внутрішню і зовнішню гальмівні колодки. До кожного з них підводиться гальмівна рідина.
У другому випадку гальмівний супорт має поршень або поршні тільки з одного боку, при цьому він має змогу переміщатися уздовж осі обертання диска. Так, при гальмуванні поршень переміщується і тисне на внутрішню колодку, після того як колодка упреться в диск, а тиск в гідроприводі продовжить зростати, вже супорт почне переміщатися і притискати зовнішню колодку до диска.
Перший варіант міцніший, але дорожчий. Другий варіант дешевший, але не такий надійний.Ефективність дискових гальм набагато вища за ефективність барабанних. Вони простіші в обслуговуванні та ліпше відводять тепло, що виділяється при гальмуванні.
Оскільки перегрів гальмівних механізмів вважається одним із найнебезпечніших моментів, вирішили збільшити ефективність відведення тепла від гальмівного механізму. Шлях вирішення проблеми простий з точки зору ідеї та не такий простий з точки зору технологічності. У диску зробили багато отворів і каналів, через які повітря може проходити з метою охолодження диска зсередини Ефективність підвищили багаторазово. Але у всього є своя ціна, і в цьому випадку за покращене охолодження довелося заплатити низькою стійкістю до перепаду температур. Виникла ймовірність появи тріщин на диску при потраплянні на нього, наприклад, води при дуже активному гальмуванні. Причина в тому, що отвори - це концентратори напружень. Виходить, що працює принцип «Де тонко, там і рветься».
Часто на гальмівних дисках можна побачити канавки . Причина, по якій диск виготовляють з такими конструктивними особливостями, криється в тому, що при виконанні гальмування на фрикційних накладках гальмівних колодок утворюється шар відпрацьованого матеріалу (пилу), який погіршує ефективність гальмування. Шар відпрацьованого пилу зрізається канавками, оновлюючи тим самим робочу поверхню фрикційної накладки.
Проте час іде, деякі автомобілі стають більш потужними і важкими, мають високі динамічні показники і украй високу енергоозброєність*, і, щоб зупинити всю цю масу, що рухається на величезній швидкості, потрібне застосування надефективних гальмівних механізмів. Основний показник, що впливає на ефективність роботи гальм, як було сказано вище, - температура.
Існує два шляхи вирішення проблеми перегріву гальм. Перший із них - виготовити гальмівні механізми зі своєю системою охолодження, однак це занадто ускладнює конструкцію і подальше обслуговування. Другий - встановити композитні гальмівні диски, наприклад металокерамічні. Таким дискам взагалі не страшний перегрів. Але плата за металокераміку - крихкість і висока собівартість.
Примітка
* Енергоозброєність - це питомий показник, що характеризує, скільки кіловат або кінських сил потужності припадає на одиницю маси автомобіля (на кілограм або тонну). Наприклад, якщо автомобіль важить 2 т, а потужність його двигуна становить 300 к. с., то енергоозброєність цього авто становить 150 к. с./т. Але автомобіль масою 1 т і потужністю 150 к. с. матиме таку ж енергоозброєність, а значить не поступатиметься в динамічних характеристиках більш потужному, але й більш важкому «супернику».Примітка
Дискові гальмівні механізми часто обладнують датчиком зносу фрикційних накладок. У найпростішому вигляді він має вигляд підпружиненої пластини, яка при досягненні граничної товщини фрикційної накладки досягає диска і починає скрипіти.
У більш ускладненому варіанті встановлено датчик у прямому сенсі цього слова. Його показники виводяться на відповідний покажчик на щитку приладів.7.2.8 Вакуумний підсилювач гальм
Що більшою ставала маса автомобіля, то більше зусилля потрібно було прикладати до педалі гальма, щоб досить ефективно знизити швидкість або зупинити автомобіль. Було б великою помилкою не використовувати ті фізичні процеси, які відбуваються під час роботи двигуна. Помилку не зробили - встановили вакуумний підсилювач. Чому вакуумний? Він використовує розрідження, створюване у впускному колекторі двигуна. Будова такого підсилювача нескладна (малюнок 7.7): корпус, розділений діафрагмою на дві камери - вакуумну й атмосферну. На штоку педалі гальма, всередині підсилювача, встановлено стежачий клапан*, що відкриває або перекриває доступ атмосферного тиску в атмосферну камеру. Крім того, встановлено поворотну пружину діафрагми підсилювача. Після підсилювача послідовно встановлено головний гальмівний циліндр.
Примітка
З огляду на різні конструктивні особливості двигунів, розрідження може підводитися не тільки від впускного колектора, а й від спеціального вакуумного насоса.
Наприклад, для всіх дизельних двигунів використовується вакуумний насос, оскільки у них розрідження у впускному колекторі незначне.Як це працює? Досить просто: в початковому положенні (коли гальмувати ніхто не збирається) тиск в обох камерах однаковий і дорівнює тиску, створюваному у впускному колекторі. Тільки-но виникне необхідність загальмувати, необхідно буде натиснути на педаль гальма - переміщення педалі передасться через штовхач до стежачого клапана. Клапан перекриє канал, який з'єднує атмосферну камеру з вакуумною. Подальше переміщення з'єднає атмосферну камеру з атмосферою. Виникне перепад тиску, який почне впливати на діафрагму і переміщати її, долаючи зусилля поворотної пружини, а діафрагма і собі переміщатиме шток поршня головного гальмівного циліндра.
Примітка
Така конструкція вакуумного підсилювача забезпечує значне доповнення зусилля (воно може досягати п'ятикратного збільшення) на штоку поршня головного гальмівного циліндра, яке пропорційне зусиллю на педалі гальма. Якщо простіше: що дужче ви тиснутимете на педаль, то потужніше й ефективніше працюватиме вакуумний підсилювач.Тільки-но водій відпустить педаль гальма, атмосферний клапан перекриється, тиск в обох камерах підсилювача вирівняється, а діафрагма повернеться в початкове положення під дією поворотної пружини.
7.2.9 Перевірки вакуумного підсилювача
Важливо знати, що, сідаючи за робоче місце водія, слід завжди перевіряти технічний стан вакуумного підсилювача. Як це зробити? Елементарно...
Для перевірки роботи вакуумного підсилювача гальм необхідно виконати такі процедури:
1. Запустити двигун на 1-2 хвилини, а потім заглушити його. Якщо при першому натисканні на педаль гальма вона натиснута повністю, але при наступних натисканнях хід педалі стає більшим із кожним натисканням, значить, підсилювач працює правильно. Якщо висота ходу педалі залишається незмінною, значить підсилювач працює неправильно.
2. При непрацюючому двигуні натиснути на педаль гальма кілька разів. Потім натиснути на педаль гальма і запустити двигун. Якщо вона рухається вниз незначно, це є нормальною роботою підсилювача. Якщо рух педалі не змінюється, підсилювач несправний.
3. При працюючому двигуні, натиснути на педаль гальма і потім зупинити двигун. Утримувати педаль натиснутою близько 30 секунд. Якщо висота педалі не змінюється, підсилювач працює нормально, якщо педаль піднімається - підсилювач несправний.
Виконати три тести, описані вище. Якщо хоча б один із них не відповідає нормальній роботі, треба перевірити зворотний клапан, вакуумний шланг і підсилювач щодо пошкоджень.
7.2.10 Стоянкове гальмо
Стоянкове гальмо (у побуті - «ручник») призначене для утримання автомобіля під час стоянки як на рівній, так і на похилій поверхні. На легкових автомобілях стоянкова гальмівна система може виконувати роль запасної гальмівної системи.
Стоянкові гальмівні системи відрізняються за типом привода, а також за типом гальмівного механізму.
За типом привода стоянкові гальмівні системи можуть бути:
- з механічним приводом;
- з гідравлічним приводом;
- з електромеханічним приводом.
7.2.11 Стоянкова гальмівна система з механічним приводом
Проста і дешева схема впливу на гальмівні механізми задніх коліс передбачає використання тросів і важеля (або педалі), який знаходиться в салоні. Принцип дії такий: при переміщенні важеля стоянкового гальма переміщуються троси привода, які впливають на гальмівні механізми, запобігаючи у такий спосіб провертанню коліс (елементи гальмівної системи зображені на малюнку 7.1). Важіль у салоні встановлено на храповик, що дозволяє фіксувати його в робочому положенні.
Для інформування водія про те, що стоянкове гальмо в цей момент задіяне, під важелем встановлено вимикач сигналізатора на щитку приладів.
Примітка
Від важеля в салоні зусилля до гальмівних механізмів передається за допомогою тросів. У конструкції гальмівного привода стоянкового гальма використовуються один, два або три троси. Найпоширеніша схема з трьома тросами: один передній (центральний) і два задні. Передній трос з'єднаний із важелем у салоні, задні троси - з гальмівними механізмами відповідно до правого і лівого коліс. Для з'єднання переднього троса із задніми і рівномірної передачі зусилля використовується зрівнювач або балансир.Як і будь-який механізм, стоянкове гальмо необхідно регулювати, для цього передбачено регулювання довжини тросів за допомогою регулювальної гайки, встановленої часто на зрівнювачі. Повернення системи в початкове положення (зняття з гальма) проводиться при переведенні ручного важеля у відповідне положення за допомогою поворотної пружини. Пружина може розташовуватися на передньому тросі, зрівнювачі або безпосередньо на гальмівному механізмі.
Гальмівні механізми стоянкової системи можуть бути різних типів. Так, якщо ззаду застосовуються барабанні гальма, то гальмівна система використовує гальмівні механізми робочої гальмівної системи, лише в цьому випадку колодки притискаються не через робочий гальмівний циліндр, а через вплив троса системи на приводний важіль колодок. Якщо гальма дискові, то варіантів два: або передавати зусилля через приводний важіль на гальмівний супорт робочої гальмівної системи і фіксувати у такий спосіб колесо, або виготовляти диск заднього гальмівного механізму складовим (мається на увазі, що гальмівний диск буде виготовлено так, що внутрішня його поверхня виконуватиме роль гальмівного барабана).
Цікаво
Бажано завжди використовувати стоянкове гальмо, щоб запобігти закисанню тросів. Оскільки, якщо раптом трапиться екстрена та непередбачена ситуація в дорозі, скористатися гальмівною системою, як запасною, при приводних тросах, що закисли, буде неможливо.7.2.12 Стоянкова гальмівна система з гідравлічним приводом
Така стоянкова система часто використовується на спортивних автомобілях, коли стоянкове гальмо застосовується короткочасно і потрібне воно для того, щоб домогтися від автомобіля необхідної траєкторії при проходженні повороту.
По суті, використовується такий самий важіль у салоні, ті самі задні гальмівні механізми, що і в механічному приводі, але замість тросів - шланги і патрубки, заповнені гальмівною рідиною. До важеля в салоні приєднано один або два головні гальмівні циліндри. Принцип роботи той самий, що і в звичайній робочій гальмівній системі, він був розглянутий вище.
7.2.13 Стоянкова гальмівна система з електромеханічним приводом
У часи автоматизації та комп'ютеризації тяжкий тягар вмикання стоянкового гальма переклали на електромеханічний сервопривод. У салоні від важеля залишилася лише клавіша або кнопка. Троси замінили на електропроводку, а виконавчі механізми помістили на елементи робочої гальмівної системи.
З такою системою водієві не потрібно рахувати кількість клацань храповика при затягуванні «ручника», не потрібно перейматися регулюванням тросів стоянкового гальма - варто лише натиснути на кнопку або потягнути клавішу, і електроніка виконає свою справу.
На додачу до цього спрощення з'явилася система допомоги при рушанні з місця під гору, яка використовує стоянкове гальмо, і, зрештою, водій позбувся ще одного головного болю - відкочення автомобіля на початку руху.
Тема: Кузов та додаткове обладнання
У кабіні розміщені сидіння для водія і пасажирів та всі органи керування. Кабіна обладнана протисонячними козирками, склоочисниками, пристроями для обмивання вітрового скла, опалювачем. Двері кабіни мають замки, поворотні кватирки і стекла, що опускаються.
Кабіни автомобілів ГАЗ-53А, ЗИЛ-130, КрАЗ, «Урал» кріплять до рами на гумових подушках за двигуном. У автомобілях ГАЗ-66, КамАЗ, МАЗ-500А та інших кабіна розміщена над двигуном. При такому розміщенні кабіни зменшується колісна база, що підвищує маневреність, поліпшує оглядовість для водія. В таких автомобілях кабіна відкидна, що робить вільним доступ до двигуна.Кузов і оперення вантажних автомобілів.
Кузови вантажних автомобілів бувають універсальними і спеціалізованими. їх установлюють на рамі за кабіною.
Універсальний кузов призначений для перевезення різних вантажів. Він має дерев\'яну з металевим окуттям вантажну платформу, передній, задній і бокові борти. Задній та обидва бокові борти відкидаються на петлях, а в піднятому положенні утримуються запорними гаками.
Спеціалізовані кузови використовують для перевезення будь-якого одного вантажу (кузови -самоскиди, кузови-цистерни та інші)
До оперення належать капот, крила, підніжки, облицювання радіатора.
Кузови легкових автомобілів можуть бути несучими, тобто такії, що сприймає силові навантаження, і рамної конструкцій. Автомобілі дуже малого (4 особи) і малого (4-5 осіб) класу обладнані кузовами несучої конструкції. Автомобілі середнього (5-6 осіб) і вищого (5-7 осіб) мають рамний кузов. Кузов легкового автомобіля чотиридверний, несучої конструкції. Він складається з основи, передньої частини, задньої стінки, боковини і криші. До передньої частини кузова прикріплена коротка рама, до якої знизу кріпиться поперечина передньої підвіски.
До корпусу кузова на петлях навішено четверо дверей. У задній частині кузова розміщено багажник з кришкою, що закривається.
У кузові встановлено передні і задні сидіння із спинками. Для вентиляції кузова передбачено люк для приливу повітря, який установлено перед вітровим склом. У кузові є пристрій для обігрівання. Оперення кузова складають передні і задні крила, капот, бризговики, передній і задній буфери та облицювання радіатора.Додаткове обладнання кузова (кабіни).
Система опалення призначена для обігрівання кузова легкового чи кабіни вантажного автомобілів.
Система опалення, яка встановлена у кабіні вантажних автомобілів і в кузові легкового автомобіля , використовує тепло системи охолодження двигуна.
На автомобілі ГАЗ-53А опалювач кабіни встановлюють під щитком приладів. Він складається з радіатора, зовнішнього люка припливу повітря, рукоятки керування кришкою люка, кришки зовнішнього люка, повітропроводу подачі теплого повітря для обдування вітрового скла і з\'єднувальних шлангів.
Радіатор опалення з\'єднується шлангами із сорочкою охолодження головки блока циліндрів і водяним насосом двигуна.
Під час руху автомобіля, коли відкрита кришка зовнішнього люка припливу повітря, зустрічний потік повітря надходить у люк і через решітку і кожух до радіатора . Проходячи через радіатор, повітря нагрівається і через розподільник надходить до кабіни.
Система вентиляції призначена для обміну повітря в кабіні або кузові (легкового) автомобіля. Конструктивно система опалення об\'єднана із системою вентиляції.
Пристрої для обдування, очищення і обмивання вітрового скла кабіни (кузова). Щоб запобігти обмерзанню чи запотіванню вітрового скла, передбачено його обдування за допомогою вентилятора системи опалення автомобіля. Повітря через вентилятор подається до радіатора 7 опалення, там нагрівається і надходить по повітропроводах до двох щілин, які містяться на панелі кузова (кабіни) з внутрішнього боку вітрового скла. Вентилятор вмикається перемикачем .
Для очищення вітрового скла від води і снігу застосовують склоочисники. На автомобілі ГАЗ-53А встановлюють двошвидкісний склоочисник, що складається з двох щіток та електричного привода . Електродвигун через черв\'ячний механізм приводить у дію щітки склоочисника. За допомогою перемикача вмикають електродвигун і регулюють частоту обертання його вала. . Автомобіль ЗИЛ-130 обладнаний склоочисником з пневматичним приводом від системи гальм. Для вмикання склоочисника і регулювання швидкості руху його щіток користуються краном, головка якого встановлена на панелі щитка приладів.
Для обмивання вітрового скла на автомобілях установлюють спеціальний пристрій . Він складається з електричного насоса розміщенного в бачку омивника який знаходиться під капотом, жиклерів встановлених зовні перед вітровим склом, жиклери з\'єднують шлангами кнопки для вмикання омивача як правило кнопка включення омивача об\'єднана з перемекачем щиток склоочисника. Щоб обмити скло, натискують на кнопку омивача прицьому запускаеться електронасос, завдяки чому вода з бачка подається до жиклерів і оприскує вітрове скло. Одночасно вмикають і склоочисник.
На кабіні вантажних автомобілів зовні встановлюють два дзеркала заднього вигляду; на легкових автомобілях дзеркало встановлюють всередині кузова, а також на лівих передніх дверях кузова або передньому лівому крилі.
Буксирний пристрій.
Вантажні автомобілі часто використовують як тягачі для буксирування причепів або інших автомобілів. Для цього автомобілі обладнують буксирним пристроєм , який має вигляд стержня з гаком 7, установленим у задній частині рами автомобіля. У цьому місці рама підсилена додатковими поперечками і розкосами.
Гак буксирного пристрою запирають защіпкою 6 і стопорною защіпкою 4у яка утримує пристрій від передчасного саморозкриття. При закритому положенні гак фіксують шплінтом 5, який вводять в отвір защіпки.
Стержень гака встановлено в корпус З, у якому між двома упорними шайбами 10 розміщено гумовий буфер 2, затиснутий гайкою 1, накрученою на стержень гака. Така будова пристрою оберігає раму автомобіля і з\'єднувальні елементи причепа від різких ударів і струсів, які виникають під час рушання автомобіля з місця чи при гальмуванні.Види кузова легкового автомобіля
Седан
Основними елементами є: моторний відсік, пасажирський салон, багажне відділення. При цьому пасажирський салон може мати два ряди сидінь передні і задні, але при цьому салон відповідно буває 4-х або 5-ти місцевим. Такий тип автомобілів буває 4-х дверними.
Купе
Даний тип кузова купе по зовнішньому вигляду аналогічний седану. Різниця полягає лише в тому, що кузов має дві бічних дверей.
Фургон бувають пасажирські вантажні та вантажно-пасажирські
Комбі (хетчбек) Так називають кузов, який є двохоб\'ємний конструкцією із задніми дверима. Даний кузов використовується для перевезення пасажирів і вантажів. Причому габаритні розміри автомобіля мають порівнянні з легковими авто значення.
Як правило, автомобілі, виконані в кузові комбі, мають задні сидіння, що збільшує їх вантажопідйомність і об\'єм багажного відділення. У сучасному обході даний тип кузова називають не інакше як хетчбек. Нова назва перекладається як «двері ззаду».Автомобільне скло
За своїми експлуатаційними характеристиками автомобільні скла діляться на три типи:
• триплекс
• сталініт
• пластикові
Сталініт (загартоване скло) проходять термічну обробку, яка забезпечує їх руйнування на дрібні осколки з негострими краями, знижуючи ризик поранення людей. Автомобільне скло триплекс формується з трьох окремих шарів. Два «несучих» шару, які мають скла триплекс, виготовлені із стандартного листового флоат-скла. Між цими шарами, завдяки спеціальній технології, розміщується так звана проміжна плівка.
Триплекс (багатошарове ламіноване скло) - це два листа скла, з\'єднані між собою прошарком з поливинилбутиральной плівки. Завдяки цій еластичною прошарку триплекс володіє підвищеною стійкістю до зовнішніх впливів. Вироби з багатошарового скла безпечні, оскільки при їх руйнуванні (в результаті сильного удару)
Пластикове скло - це скло, яке містить в якості одного з основних компонентів полімерні органічні речовини. Такі скла, залежно від результатів випробувань на вигин, поділяються на жорсткі і гнучкі. мічної навантаження та ін) осколки скла залишаються приклеєними до плівці.
Тема: Ходова частина
Учбові питання
1. Види підвісок
2. Кути встановлення керованих коліс
3. Важільна підвіска
4. Ресори
5. Амортизатори
6. Маркування шин
Література: В. Ф. Кисликов , В. В. Лущик " Будова й експлуатація автомобілів" стр.272 - 287
1. За характером взаємодії коліс однієї осі транспортного засобу підвіски діляться на два види ; залежна і незалежна. Залежна підвіска забеспечує жорсткий звязок між колесами тобто при зміні положення одного колеса міняється положення іншого. При незалежній підвісці жорсткий звязок між колесами відсутній .
2.Передні керовані колеса незалежно від конструкції підвіски встановлюються під певним кутом як в горизонтальній так і вертикальній площині. Це дає можливість зменшити опір рухові ТЗ і зменшити спрацювання протектора шин. Розвал коліс - кут між площиною колеса і вертикальною площиною паралельною повждовжній осі ТЗ. Сходження коліс - це різниця відстаней між внутрішніми поверхнями боковин шин яка вимірюється спереду і ззаду. Розвал і сходження коліс залежать від марки ТЗ.
3. Важільна підвіска ТЗ включає в себе такі елементи : Верхні і нижні важелі, амортизатори, пружини, шарові опори , буфери стискання, осі важелів, саленблоки, стабілізатор поперечної стійкості, поворотні цапфи.
4. Ресора - пружний елемент підвіски. Ресора складається з окремих листів ,які в центральній частині скріплені між собою болтовим зєднанням. Щоб пакет листів тримався разом на листи ресори одівають хомути. Найдовший лист ресори називають корінним листом. Листи ресори виготовляють з легованої сталі. Для усунення металевого скрипу листів ресори їх змащують графітною змазкою або ставлять між листами протискрипні шайби.
5. Амортизатори служать для гасіння коливань кузова ТЗ. За конструкцією вони бувають однотрубні і двохтрубні . Однотрубні амортизатори всередині мають один циліндр поділений на дві частини. Одна частина зоповнюється газом а інша амортизаторною рідиною. Такі амортизатори ще називають газомасляними. Двохтрубні амортизатори крім циліндра мають компенсаційну камеру. Двохтрубні амортизатори заповнюються амортизаційною рідиною кількість якої залежить від марки ТЗ, мають чотири клапани (клапан стискання, клапан віддачі , перепускний і випускний клапани). Амортизатор змінної довжини називається телескопічним.
6. У маркуванні шин вказують такі показники:
а) тип шини
б) ширина профілю шини
в) висота профілю шини
г) посадочний діаметр в дюймах
Наприклад 165/70 R 13
де 165 - ширина профілю шини в мм, 70 - висота пофілю шини в процентах від ширини , R - радіальна шина, 13 - посадочний діаметр 13х 25,4
Тема : Рульове керування автомобіля
На повороті внутрішнє колесо, що котиться по дузі меншого радіусу, має повертатися на більший кут, ніж зовнішнє. Це забезпечується пристроєм, який називається рульовою трапецією. Вона складається з балки, поворотних важелів, поперечної рульової тяги
Конструкція рульової трапеції передбачає постановку осей шворнів поворотних цапф під деякими кутами. Розрізняють поздовжній бічний нахил осей шворнів.
Нахили осей викликають реактивні зусилля і моменти, додані до керованих колесіс, які прагнуть повернути їх у положення прямолінійного руху. Ця властивість рульового управління називається стабілізацією коліс. Вона полегшує водіння автомобіля і забезпечує йому більшу стійкість при русі.
Для стабілізації коліс рекомендується черв'ячну рульову передачу 9 конструювати оборотною (несамогальмівною), але для запобігання впливу на рульовий штурвал ударів, які сприймаються колесами від нерівностей дороги, - з підвищеним внутрішнім тертям.
Керовані колеса також встановлюють під деякими кутами до вертикальної площини.
Для зменшення зусилля, що витрачається на поворот керованих коліс, і пом'якшення поштовхів від нерівностей дороги на потужних вантажних автомобілях встановлюють підсилювачі рульового управління - пневматичні (на автомобілях типу КрАЗ) і гідравлічні (МАЗ-509, ЗІЛ-130, ЗІЛ-131, ГАЗ-66 ).
Справність рульового механізму має винятково велике значення для безпеки руху, тому необхідно регулярно перевіряти люфт (вільний хід) рульового штурвала (він не повинен перевищувати 25-36 °) і кути установки коліс. Кут сходження коліс регулюється зміною довжини поперечної рульової тяги, а кут розвалу, як правило, не регулюється
Будова рульового керування
. Система включає в себе рульовий механізм і рульовий привід.
Повертаючи кермо, водій повертає передні колеса автомобіля.
З одного кінця рульового вала закріплено кермо, а протилежний кінець вала входить в рульовий механізм. На цьому кінці закріплена або шестерня (рейковий рульовий механізм), або черв'ячний вал (черв'ячний рульовий механізм).
Рульовий механізм перетворює обертання керма в площинне переміщення рульових тяг, повертаючи керовані колеса на необхідні кути. У зв'язку з тим що рульовий механізм виконано за схемою редуктора (пристрою, що знижує оберти і, як наслідок, збільшує крутний момент), він ще й збільшує зусилля водія, прикладене до рульового колеса. Зазвичай зусилля, яке прикладається водієм, збільшується в 15...30 разів. Саме таке передавальне відношення мають кермові механізми.Цілком зрозуміло, що чим більше передавальне відношення рульового редуктора, тим легше водієві повертати передні колеса. Однак збільшення передавального числа понад зазначене обмежено погіршенням керованості автомобіля: при великих значеннях передавального числа навіть для незначного повороту коліс водієві доведеться повертати кермо на великі кути.
Ряд легкових автомобілів обладнано підсилювачем рульового механізму, що додатково знижує зусилля, необхідне для повороту керма.
Рейковий рульовий механізм
У більшості сучасних легкових автомобілів використовується система рульового керування з рейковим механізмом
У цьому випадку на кінці рульового вала 1, з в'язаного з рульовим механізмом, закріплено шестерню. Вона знаходиться в зачепленні із зубчатою рейкою . Дана зубчаста пара розташована всередині картера рульового механізму. Повертаючи кермо, ми обертаємо шестерню, а вона
змушує зубчасту рейку переміщуватися усередині картера вліво або вправо. Кінці рейки через кермові тяги з'єднані з поворотними кулаками передніх коліс, і при переміщенні рейки відбувається поворот керованих коліс.
Черв'ячний кермовий механізм
У даному механізмі один з кінців кермового вала зв'язаний з черв'яком, що знаходиться в зачепленні з роликом, який, у свою чергу, зв'язаний з рульовою сошкою
Сошка, переміщуючись вліво чи вправо, через кермові тяги і поворотні кулаки забезпечує переміщення передніх коліс на необхідні кути.
На сьогодні існують два типи підсилювачів рульового керування:
- гідравлічний;
- електромеханічний.
Система з гідравлічним посиленням рульового керування має:
- насос (з розширювальним бачком);
- контрольний клапан;
- виконавчий механізм;
- власне робочу рідину.
Насос створює надлишковий тиск робочої рідини в системі. При обертанні рульового колеса контрольний клапан зміщується і відкриває канал у виконавчий механізм для робочої рідини під тиском. У виконавчому механізмі знаходиться поршень, пов'язаний через шток (тягу) з рульовою трапецією. Під тиском робочої рідини поршень переміщується, створюючи додаткове зусилля на рульовому приводі, зменшуючи тим самим зусилля водія для обертання рульового колеса.
Залежно від того, в який бік обертається кермо, робоча рідина під тиском подається в порожнину над поршнем або під ним.
Коли рульове колесо стоїть по центру, насос перекачує робочу рідину без навантаження фактично вхолосту. Тільки-но кермо починає повертатися, тиск рідини в системі зростає і досягає максимуму при крайньому (правому або лівому) положенні рульового колеса.
Увага
В автомобілі з гідравлічним підсилювачем рульового керування забороняється тривалий час утримувати кермо в одному з крайніх положень, оскільки це може призвести до пошкодження нагнітального насоса.
Насос може приводитися ременем від двигуна або ж від окремого електродвигуна.
Електромеханічний підсилювач рульового керування
Гідравлічний привод підсилювача рульового керування «вибагливий»: необхідно регулярно стежити за всіма з'єднаннями, щоб учасно виявити й усунути витік робочої рідини. Крім того, є імовірність засмічення робочої рідини. У разі необхідності зняття рульового механізму виникає потреба в зливі робочої рідини. А при заправці гідропривода свіжою робочою рідиною необхідно виконувати операції з видалення повітря із системи. Зовсім інша річ - електромеханічний підсилювач: немає робочої рідини, патрубків, прокачування та є електродвигун і блок керування, який контролює частоту обертання рульового колеса. Блок керування також відстежує швидкість автомобіля і кути повороту керма. При певних значеннях швидкості він може посилати сигнал на електродвигун з метою «затиснення» або «відпускання» керма.
Існує кілька схем установки електродвигуна підсилювача:
- на рульовій колонці;
- на валу-шестерні рульового механізму;
- на рульовому механізмі.
Численні тести автомобілів з електромеханічним підсилювачем показали, що найліпша схема встановлення електродвигуна - на рульовому механізмі, оскільки цим досягається найліпший зворотний зв'язок рульового керування.
Примітка
Під зворотним зв'язком рульового керування розуміють зв'язок із дорогою. Адже, коли ми обертаємо кермо, колеса повертаються, впливаючи таким чином на дорогу, а під час руху на колесо діє безліч сил, пов'язаних із його коченням. Так от: передача всіх цих сил від дороги на колесо та далі на кермо і є зворотним зв'язком. Виражається цей зв'язок, переважно, в пропорційно зростаючому зусиллі на рульовому колесі, яке залежить від кута повороту керма і швидкості руху автомобіля. Термін найчастіше застосовується для автомобілів із підсилювачем рульового керування.
Якщо на машині з підсилювачем керма зворотного зв'язку немає, значить зусилля на кермовому колесі не змінюється залежно від кута повороту керма і швидкості проходження автомобілем повороту. Коли автомобіль стоїть на місці або рухається повільно, то легкість обертання керма тільки на ліпше. Однак при маневруванні на швидкості відсутність на кермі зусилля, що пропорційно підвищується, може зіграти злий жарт, оскільки за об'єктивними і суб'єктивними відчуттями важко буде обрати єдино правильне положення керма.
ДИСК ЗЧЕПЛЕННЯ
Цей елемент забезпечує жорстку зчеплення маховика двигуна з провідним валом головної передачі. Однак при необхідності даний механізм також роз'єднує мотор і коробку. Механічна трансмісія оснащується кошиком зчеплення, схожий пристрій має і робот.
В автоматичних модифікаціях цю функцію виконує гідротрансформатор. Єдина відмінність - диск зчеплення може забезпечити міцний зв'язок мотора і механізму трансмісії навіть при заглушеному моторі. Це дозволяє використовувати передачу в якості противідкатна механізму на додаток до слабкого ручнику. Зчеплення дозволяє запустити двигун з штовхача, чого не можна зробити на автоматі.
Механізм зчеплення складається з таких елементів:
- Фрикційні диски;
- Кошик (або корпус, в якому розташовані всі елементи механізму);
- Вилка (переміщує натискний диск, коли водій натискає на педаль зчеплення);
- Ведучий або первинний вал.
Серед різновидів зчеплення бувають:
- Сухі. У таких модифікаціях використовується сила тертя, завдяки чому фрикційні поверхні дисків не дозволяють їм прослизати під час передачі крутного моменту;
- Мокрі. Дорожча модифікація, в якій використовується гідротрансформаторним масло, якою продовжили термін служби механізму, а також робить його більш надійним.
ГОЛОВНА ПЕРЕДАЧА
Основне завдання головної передачі - приймати зусилля, що надходять від мотора і передавати їх на під'єднані вузли, а саме на ведучий міст. Головна передача збільшує КМ (крутний момент) і разом з тим зменшує обертів провідних коліс авто.
Машини з переднім приводом оснащуються даними механізмом біля диференціала КПП. Моделі з заднім приводом мають цей механізм в картері заднього моста. У пристрій ДП входить піввісь, ведуча і ведена шестерні, напівосьові шестерні, а також шестерні-сателіти.
ДИФЕРЕНЦІАЛ
Передає крутний момент, змінює його і розподіляє на Неспіввісність механізми. Форма і принцип роботи диференціала відрізняються в залежності від приводу машини:
- Заднеприводная модель. Диференціал встановлюється в картері моста;
- Передньопривідна модель. Він встановлений в коробці передач;
- Повнопривідна модель. Диференціал знаходиться в роздавальної коробці.
У конструкцію диференціала входить планетарний редуктор. Існує три модифікації планетарної передачі:
- Конічна - використовується в міжколісним диференціалі;
- Циліндрична - застосовується в межосних диференціалі повнопривідного авто;
- Черв'ячна - вважається універсальною модифікацією, яку можна використовувати, як в міжколісним, так і межосних диференціалах.
У пристрій диференціала входять осьові шестерні, закріплені в корпусі. Вони зв'язуються між собою планетарної передачею, яка складається з шестерень-сателітів. Детальніше про пристрій диференціала і принцип роботи читайте тут.
КАРДАННА ПЕРЕДАЧА
Карданна передача - це вал, що складається з двох або більше частин, які з'єднані між собою за допомогою шарнірного механізму. Вона використовується в різних частинах автомобіля. Основне застосування - в заднеприводном транспорті. Коробка передач в таких автомобілях часто знаходиться нижче, ніж редуктор заднього моста. Щоб ні механізм коробки, ні редуктора не відчував додаткове навантаження, вал, розташований між ними повинен поділятися на секції, з'єднання яких забезпечувало б плавне обертання при деформації вузла.
Якщо кардан несправний, то в процесі передачі крутного моменту відчуваються сильні шуми і вібрації. Коли водій помітив такий ефект, йому слід приділити увагу ремонту, щоб через підвищених вібрацій не вийшли з ладу механізми трансмісії.
Щоб трансмісія прослужила максимально ефективно і довго без ремонтів, кожну коробку необхідно обслуговувати. Виробник встановлює свій термін планового ТО, про що автовласник інформується в технічній документації. Найчастіше цей період знаходиться в районі 60 тисяч кілометрів пробігу авто. В технічне обслуговування входить заміна масла і фільтра, а також скидання помилок, якщо такі є в електронному блоці управління.
Детальніше про догляд за коробкою розказано в іншій статті.
КОРОБКА ПЕРЕДАЧ
Це найскладніша частина будь-якої трансмісії, навіть механічної. Завдяки цьому агрегату відбувається рівномірний розподіл тягових зусиль. Це відбувається завдяки безпосередньому участі водія (механічна коробка передач), або за рахунок роботи електроніки, як у випадку автоматичної або роботизованої трансмісії.
Незалежно від типу коробки передач, цей агрегат дозволяє максимально ефективно використовувати потужність і крутний момент двигуна в різних режимах його роботи. Коробка передач дозволяє рухатися машині швидше при мінімальних стрибках обертів двигуна (для цього водію або електроніці необхідно визначати відповідний показник обертів) або піддавати двигун меншому навантаженню під час руху в гірку.
Також завдяки коробці передач змінюється напрямок обертання веденого валу. Це необхідно для руху машини заднім ходом. Цей агрегат дозволяє передати весь момент, що крутить, від мотора до провідних колес. Коробка передач дозволяє повністю відключити двигун від провідних коліс. Це необхідно, коли машина повинна повністю зупинитися, але двигун повинен продовжувати працювати. Наприклад, у такому режимі має бути автомобіль при зупинці на світлофорі.
Серед коробок передач бувають такі різновиди:
- Механічна. Це найпростіший тип коробки, де розподіл тягових зусиль здійснює безпосередньо водій. Всі інші типи коробок можна віднести до автоматичних типів.
- Автоматична. В основі такої коробки лежить гідротрансформатор, а зміна передавальних чисел відбувається в автоматичному режимі.
- Робот. Це автоматичний аналог механічної коробки. Особливістю роботизованої КПП є наявність подвійного зчеплення, що забезпечує максимально швидке перемикання швидкостей.
- варіатор. Це також автоматична коробка передач. Тільки тягові зусилля розподіляються з допомогою зміни діаметра ременя чи ланцюга привода.
Завдяки наявності коробки можна використовувати колишні обороти мотора, але змінювати швидкість обертання коліс. Це, наприклад, стане в нагоді, коли машина долає бездоріжжя.
ВЕДУЧИЙ МІСТ
Під мостом трансмісії мається на увазі опорна частина, яка кріпиться до рами автомобіля, а всередині неї розташовується механізм передачі моменту, що крутить, на колеса. У легковому транспорті мости використовуються у задньопривідних або повнопривідних моделях. Щоб момент, що крутить, надходив від коробки передач на міст, використовується карданна передача. Про особливості цього елемента розповідається в іншій статті.
В автомобілі може бути ведучий та ведений мости. У провідному мосту встановлюється редуктор, що перетворює поперечне обертання валу (напрямок упоперек кузова авто) у поздовжнє обертання (напрямок вздовж кузова) провідних коліс. У вантажному транспорті може бути більше одного провідного мосту.
РОЗДАВАЛЬНА КОРОБКА
Роздатка використовується лише у повнопривідних трансмісіях (крутний момент передається на всі колеса). У ній, так само як і в основній коробці передач, є набір шестерень, які дозволяють змінити передавальні числа (демультиплікатор) на різні пари коліс для збільшення моменту, що крутить. Це необхідно у всюдиходах або в тягачах великої вантажопідйомності.
ШАРНІР РІВНИХ КУТОВИХ ШВИДКОСТЕЙ
Цей елемент трансмісії використовується в автомобілях, де провідними є передні колеса. Цей шарнір безпосередньо з'єднується з провідними колесами і є останньою ланкою у трансмісії.
Наявність даного механізму обумовлено тим, що при повороті передніх коліс на них має тією ж мірою надходити момент, що крутить. Цей механізм працює за принципом карданної передачі. У машині на одному колесі використовується два ШРУСи - внутрішній та зовнішній. Вони забезпечують постійний зв'язок із диференціалом.
ПРИНЦИП РОБОТИ
Трансмісія автомобіля працює у такій послідовності:
- Запускається мотор завдяки злагодженій роботі системи запалення та подачі палива.
- У процесі послідовного згоряння повітряно-паливної суміші в циліндрах двигуна провертається колінчастий вал.
- Крутний момент передається від колінчастого валу через маховик, до якого з'єднаний кошик зчеплення, на провідний вал коробки передач.
- Залежно від типу коробки передач момент, що крутить, розподіляється або по підключених шестернях, або через ремінь/ланцюг (наприклад, у варіаторі) і надходить на провідні колеса.
- У механічній коробці передач водій самостійно роз'єднує зв'язок між маховиком та провідним валом коробки. Для цього натискається педаль зчеплення. В автоматичних трансмісія цей процес відбувається автоматично.
- У коробці передач механічного типу зміна передавальних чисел забезпечується за рахунок з'єднання шестерень з різною кількістю зубів та різним діаметром. Коли вибирається конкретна передача, з'єднуються між собою лише одна пара шестерень.
- При надходженні моменту на диференціал тяга надходить на колеса різною мірою. Цей механізм необхідний, тому що машина рухається не завжди прямою ділянкою дороги. На повороті одне колесо обертатиметься швидше, ніж інше, тому що проходить більший радіус. Щоб гума на колесах не зазнавала передчасного зношування, встановлюється диференціал між півосями. Якщо машина повнопривідна, таких диференціалів буде мінімум два, а в деяких моделях встановлюється і проміжний (міжосьовий) диференціал.
- Крутний момент у задньопривідному автомобілі передається на колеса від коробки через карданний вал.
- Якщо машина повнопривідна, у трансмісії такого типу буде встановлена роздавальна коробка, за допомогою якої всі колеса впадуть ведучими.
- У деяких моделях використовується система з повним приводом, що підключається. Це може бути система з блокуванням міжосьового диференціала або між осями встановлюватися багатодискова фрикційна або в'язкова муфта. Коли основна пара коліс починає буксувати, міжосьовий механізм блокується, і момент, що крутить, починає надходити на другу пару коліс.
НАЙБІЛЬШ ЧАСТІ ПОЛОМКИ ТРАНСМІСІЇ
До найбільш поширених несправностей трансмісії відносяться:
- Складнощі з перемиканням однієї або декількох швидкостей. У цьому випадку важливо відремонтувати зчеплення, налаштувати тросик або відрегулювати кулісу.
- При переході на нейтральну передачу в коробці з'являється шум. Якщо цей звук зникає при натисканні на педаль зчеплення, то це може бути симптомом вийшов з ладу вичавного підшипника, знос підшипників первинного вала, при неправильно підібраному трансмісивному маслі або недостатньому його обсязі.
- Знос кошика зчеплення.
- Підтікання масла.
- Поломка карданного валу.
- Вихід з ладу диференціала або головної передачі.
- Поломка ШРУСів.
- Несправності в електроніці (якщо в машині повне або часткове управління здійснюється електронним блоком управління). У цьому випадку на приладовій панелі буде світитися значок несправності мотора.
- У процесі перемикання швидкостей відчуваються сильні ривки, стуки або скрегіт. Причину цього здатний визначити кваліфікований фахівець.
- Швидкості довільно вимикаються (стосується механічних КПП).
- Повна відмова агрегату працювати. Точну причину потрібно встановлювати на станції техобслуговування.
- Сильне нагрівання коробки.
ЗАЛЕЖНІСТЬ ТРАНСМІСІЇ ВІД ТИПУ ПРИВОДУ
Отже, як ми розібралися, в залежності від типу приводу трансмісії будуть конструктивно відрізнятися. В описі технічних характеристик різних моделей авто часто згадується поняття «колісна формула». Вона може бути AWD, 4х4, 2WD. Постійний повний привід позначається 4х4.
Якщо в трансмісії здійснюється розподіл крутного моменту на кожне колесо в залежності від навантаження на нього, то така формула буде позначатися AWD. Що стосується переднього або заднього приводу, то така колісна формула може позначатися 4х2 або 2WD.
Конструкція трансмісії в залежності від типу приводу буде відрізнятися наявністю додаткових елементів, які будуть забезпечувати постійну передачу крутного моменту на осі або тимчасове підключення другої осі.
Тема: Рами автомобілів
Рама автомобіля - балочна конструкція, яка виступає як основа для кріплення всіх вузлів і агрегатів, таких як силова установка, елементи трансмісії, ходової частини і так далі. Кузов при такій конструкції несучої системи забезпечує простір для розміщення пасажирів і багажу, а також виконує декоративну функцію.
Застосування рами дає можливість дати несучої частини високу міцність. Тому її використовують у вантажівках і позашляховиках. Також вона дає можливість максимальної уніфікації вузлів і механізмів між моделями різних класів.
Рама в автомобілі виступає як «скелет». Вона сприймає все зовнішні і внутрішні навантаження при русі машини і навіть при її стоянці. Зважаючи на це до автомобільної рамі пред'являється ряд вимог:
- достатня міцність і жорсткість;
- невелика маса;
- правильна форма, яка буде сприяти раціональної роботи всіх елементів автомобіля.
Рамна несуча частина має низку переваг. Так, завдяки їй збирати машину і ремонтувати її в подальшому стає значно простіше. Основна відмінність рамної конструкції від кузовний в тому, що будь-яку поломку можна легко усунути завдяки гарному фахівцеві і матеріалами. Ще одна важлива перевага: їзда на поганих дорогах не буде чревата перекосами кузова (прорізів дверей, стійок і т.д.).
Поряд з цим, є і недоліки. Перший - істотне збільшення ваги автомобіля через наявність окремих рами і кузова. Відповідно, витрата палива також буде більше. Інший мінус в тому, що для розміщення лонжеронів під кузовом потрібно додаткове місце, що ускладнює посадку в машину і забирає значну частину салону.
Також відзначається зниження пасивної безпеки, оскільки є ймовірність зсуву рами щодо кузова в разі удару. Тому несучий кузов - невід'ємний елемент легкового автомобіля. У той же час рамна конструкція добре справляється з важкими умовами, в яких їздять вантажні авто і позашляховики.
ВИДИ РАМ
Рами поділяються на кілька видів, що відрізняються за конструктивними особливостями:
- лонжерон;
- хребтові;
- просторові.
У деяких видів є підвиди. Виділяються також комбіновані типи, що поєднують в конструкції складові різних типів рам.
ЛОНЖЕРОННА РАМА
Це найпоширеніший вид. У конструкцію рами входять дві силові поздовжні балки, які називаються лонжеронами. Вони тягнуться вздовж кузова і з'єднуються за допомогою поперечок. Балки виконуються зі сталі. З метою підвищення показників скручування можуть застосовуватися різні види профілю перетину.
Лонжерони необов'язково рівні - іноді вони мають і вертикальні, і горизонтальні вигини. Вони можуть розташовуватися як паралельно горизонтальній площині, так і під певним кутом, що притаманне для позашляховиків. Також можливо різне розташування поперечок, за рахунок яких з'єднуються лонжерони. На сьогодні це найбільш популярна рамна конструкція, що застосовується в більшості вантажівок і позашляховиків.
Така рама відмінно підходить для експлуатації машини в умовах поганих доріг. Також вона спрощує ремонт і складання автомобіля. Мінуси ж в тому, що лонжерони віднімають чималу частину салону і кілька ускладнюють процес посадки.
ЛОНЖЕРОННА Х-ПОДІБНА
Х-подібна рама - один з видів лонжеронної. Особливість її конструкції в тому, що лонжерони спереду і ззаду розведені, а в центрі - максимально зведені. Даний тип на вигляд схожий на буку «Х», що і послужило причиною його назви.
ПЕРИФЕРІЙНА
Є видом Лонжерон рам. Цей вид почав активно використовуватися на великих легкових машинах європейського виробництва і «дредноутах» з США в 60-х роках. У таких рамах лонжерони розташовані настільки широко, що в процесі установки кузова вони розташовуються біля порогів. Це дозволяє істотно знизити рівень підлоги, одночасно з цим зменшивши безпосередню висоту машини.
Важливе значення подібної машини в її максимальної пристосованості до бічних ударів. Однак є істотний мінус - рама не може витримати значні навантаження, тому кузов авто повинен мати необхідну міцність і твердість.
ХРЕБТОВА РАМА
Даний вид рам розробили представники компанії «Татра» і переважно він застосовувався для машин її виробництва. Головний несучий елемент - труба, що з'єднує двигун спереду з елементами трансмісії, які розташовані всередині неї. По суті, труба виступає єдиним картером для коробки передач, роздавальної коробки і приводних валів. Крутний момент від двигуна до трансмісії надходить за допомогою поміщеного в трубу вала. Причому даний вал не є карданним, що забезпечує більшу надійність.
Перевага хребтової рами також полягає в тому, що вона має дуже високу жорсткість на кручення, а елементи трансмісії надійно захищені від зовнішнього впливу. Але з огляду на те, що певні механізми розташовані всередині конструкції рами, ремонтні роботи помітно ускладнюються.
ВИЛЬЧАТО-ХРЕБТОВА
Вильчато-хребтовий тип рам теж є розробкою «Татра». У такому варіанті двигун кріпиться не до трансмісійної трубі, а на спеціальній лонжеронной вилці. Це зроблено для того, щоб скоротити рівень передаються вібрацій від працюючого ДВС на раму і, отже, на кузов автомобіля. Однак, на сьогоднішній день вильчато-хребтові рами вже не застосовуються в автомобілебудуванні.
ПРОСТОРОВА РАМА
Найскладніший тип рамної конструкції, що застосовується для спортивних машин. Це конструкція являє собою каркас на основі тонких легованих труб і має дуже високі показники по жорсткості і міцності. В автомобілебудуванні дані рами були витіснені монокок, однак, схожі конструкції використовуються при створенні автобусів.
НЕСУЧА ПІДСТАВА
Несуча підстава - це щось середнє між кузовом і рамною конструкцією. Тут також використовуються лонжерони, але вони об'єднані днищем, а не поперечиною. Найбільш масовий і популярний володар несучого днища - «Фольксваген Жук», у якого кузов кріпиться до плоскої панелі підлоги за допомогою болтів. Аналогічну конструкцію має і інша машина масового виробництва - Renault 4СV.
Несуча днище відрізняється високою технологічністю і застосовується у великосерійному виробництві. Дана конструкція дозволяє зробити підлогу і центр ваги автомобіля досить низькими.
У рамної несучої частини автомобіля є ряд достоїнств і особливостей, які роблять її незамінною для вантажних машин і позашляховиків. І хоча рама використовується суто для конкретних видів автомобілів, деякі елементи її конструкції застосовуються вкрай широко, так як дозволяють зробити несучі кузова більш жорсткими. Майже будь-яка легкова машина оснащена підсилюють лонжеронами або підрамниками.
Тема: Передня неведуча вісь автомобіля
Передня вісь буває двох типів: цільна і розрізна. Цільну передню вісь застосовують на всіх вантажних автомобілях. Розрізну передню вісь застосовують при незалежній підвісці коліс на легкових автомобілях.
Цілісна передня вісь складається з балки, поворотних кулаків з цапфами і шворнів.
Сталева балка двотаврового перетину за допомогою ресор з'єднана з рамою. На кінцях передньої осі встановлені вильчаті поворотні кулаки з цапфами, з'єднані з віссю шарнірно за допомогою сталевих пальців - шворнів. Кожен шкворень закріплений в отворі осі наглухо, а в поворотному кулаці встановлений вільно на втулках. Внаслідок цього поворотний кулак з цапфою може повертатися навколо шворня в горизонтальній площині, ніж забезпечується поворот передніх керованих коліс і всього автомобіля.
Для полегшення повороту цапф з колесами між віссю і нижньою частиною вилки поворотного кулака на шворні встановлений наполегливий підшипник
На цапфі на двох конічних роликопідшипників встановлено втулка. До фланця маточини прикріплено колесо, на ободі якого монтується пневматична шина. Підшипники регулюють і закріплюють на цапфі гайкою, яку надійно стопорять. Зовні гайка закрита ковпаком. У маточину закладають мастило. Щоб мастило не витікала, в ступиці поставлений сальник.
У автомобілів високої прохідності передньою віссю є балка переднього ведучого моста, до напівосьові пукавам которого на шкворнях приєднуються корпуси з поворотними цапфами. На цапфах встановлюються на підшипниках передні колеса, що є провідними і керованим
Передня вісь, що має тип несучого моста, може бути цілісною і складовою.
Передня цільна вісь складається з балки, пружно пов'язаної з рамою через ресори, і двох поворотних цапф, шарнірно з'єднаних з кінцями балки за допомогою шворнів
Балка штампується із сталі і для підвищення міцності і жорсткості має в перерізі двотавровий профіль. На її верхній площині розташовані майданчики для установки і кріплення ресор. Балка вигнута так, що її середня частина дозволяє встановити двигун нижче, тим самим знизити центр ваги автомобіля і поліпшити огляд з місця водія. Кінці балки мають циліндричну форму з наскрізним отвором для шворнів.
Поворотна цапфа, штампована зі сталі, має вісь з фланцем і вилку. На дві циліндричні шийки осі встановлюються підшипники маточини переднього колеса, до фланця прикручується гальмівний щит колеса. У співвісні отвори верхньої та нижньої частин вилки запресовуються бронзові втулки, на яких цапфа повертається близько шворня. Поворот цапф і коліс здійснюється за допомогою важелів, закріплених в бічних отворах вилки. Ліва цапфа отримує зусилля повороту від рульового механізму через поздовжню рульову тягу і важіль. Це зусилля передається важелем через поперечну рульову тягу правої цапфе.
Шкворень виготовляється з сталевого прута і після установки в отвори вилки і кінця балки стопориться від переміщення в отворі балки клиновим штифтом з гайкою, Штифт і шворінь мають лиски на циліндричній поверхні, завдяки чому шкворень заклинюється.
Балка і вісь цапфи відчувають вертикальне навантаження сили ваги автомобіля, горизонтальне навантаження сил інерції при гальмуванні і повороті, крім цього балка отримує скручується навантаження від гальмівного моменту. У зв'язку з цим балка і вісь цапфи розраховуються на міцність при згині, а балка - ще й при крученні. Матеріалом балки і цапфи служать середньовуглецеві малолегованих стали, містять невелику кількість хрому.
Шкворень піддається дії навантаження того ж характеру, що і балка осі, в ньому виникає напруга, що вимагають розрахунку на міцність при згині, смятии і зрізі. Щоб забезпечити високу міцність і зносостійкість, шворінь виготовляється з середньовуглецевих сталей з подальшою поверхневої загартуванням або з маловуглецевих низьколегованих сталей, які потребують цементації і гарту.
Передня вісь автомобіля ГАЗ-53 А Включає в себе балку, до якої шкворнями приєднані поворотні цапфи (рис. 3).
Балка двотаврового перетину має два майданчики з чотирма наскрізними отворами для драбин кріплення ресори і глухим отвором для головки центрального стяжного болта ресори. На бічній поверхні балки розташовані два отвори для стопорних штифтів шворня і два отвори для пальців телескопічних амортизаторів.
Поворотна цапфа має вісь для підшипників маточини колеса. До її фланця шістьма болтами кріпиться гальмівний щит, в отвори вилки цапфи запресовані дві бронзові втулки шворня.
Шкворень забезпечений наполегливим підшипником, який сприймає вертикальне навантаження від ваги автомобіля, що припадає на передню вісь. Підшипник складається з Металокерам мической (середньої) шайби і двох сталевих шайб, укладених в обойму.
Втулки шкворня змащуються солідолом через маслянки, вкручені в бічні отвори верхньої та нижньої частин вилки. Від нижньої втулки мастило надходить за спеціальною канавці на шворні до його наполегливій підшипника.
Після установки шкворня отвори вилки закриваються кришками, які ставляться на картонні прокладки ущільнювачів і прикручуються двома болтами.
Між верхнім торцем циліндричного кінця балки і торцем верхній частині вилки повинен бути зазор не більше 015 мм. Його величина визначається товщиною регулювальної шайби.
Поворотні важелі встановлюються на шпонках в конусних бічних отворах вилки і кріпляться гайками, які зупиняються шплинтами. Важелі мають регулювальні болти, які при повороті коліс в обидві сторони впираються в спеціальні бобишки балки, обмежуючи кут повороту.
На циліндричні шийки цапфи встановлюються конічні роликопідшипники, запресовані в маточину колеса. Підшипники закріплені через наполегливу шайбу гайкою, яка дозволяє регулювати затяжку підшипників і стопориться шплінтом. Для підшипників в маточину закладається мастило, і, щоб запобігти її витікання, з внутрішньої сторони ступи-ди ставиться сальник, а із зовнішнього - ковпак.
Гальмівний барабан ставиться на болти маточини і кріпляться до неї трьома гвинтами. Диск колеса надівається на ці ж болти і кріпиться разом з гальмівним барабаном до маточини гайками.
Підшипники маточини закріплюються і регулюються упорною гайкою, яка стопориться замковим кільцем, замкової шайбою і контргайкою. Порожнина підшипників із зовнішнього боку закрита через прокладку кришкою, прикрутити гвинтами.
Гальмівний барабан з'єднаний з маточиною запресованими болтами, обробляються вони в зборі, тому роз'єднувати їх треба тільки при заміні болтів.
Тема: Колеса і шини
Колесо і шина утворюють разом колісний рушій, який призначено для здійснення зв'язку автомобіля з дорогою, забезпечення руху автомобіля, зміни напрямку руху і передачі вертикальних навантажень від автомобіля до дороги і навпаки. Простіше кажучи, саме завдяки рушію ми можемо рухатися і керувати автомобілем, тому від правильного вибору коліс і шин безпосередньо залежить поведінка автомобіля на дорозі
Вирізняють такі види рушіїв:
- ведучі;
- керовані;
- комбіновані (ведучі та керовані);
- холості (неведучі і некеровані, наприклад причіпні або опорні в багатовісних вантажних автомобілях).
Ведучі рушії мають таку назву саме тому, що вони перетворюють тягу двигуна в поступальний рух автомобіля, передаючи всі моменти і сили на дорогу. Керовані рушії відповідають виключно за контроль за напрямком руху автомобіля. А якщо рушій отримує тягу від двигуна та ще й відповідає за напрямок руху, то він є комбінованим. Холості рушії служать для рівномірного розподілу ваги транспортного засобу на поверхні дороги.
Рушій складається з пневматичної шини, маточини і колеса (яке складається з диска і обода).
Пневматична шина є найважливішим елементом в конструкції рушія. Якщо уявити собі колісний рушій без пневматичної шини - жорстким, наприклад дерев'яним, то неважко припустити, що при його коченні по твердій дорозі траєкторія руху осі копіюватиме профіль дороги. Удари рушія об нерівності дороги в цьому випадку будуть повністю передаватися на підвіску. Все виглядає зовсім інакше, коли колісний рушій має пневматичну шину. У місці контакту еластична шина (зазвичай виконана на основі каучуку і різних добавок - від сажі до оксиду кремнію) деформується. При цьому невеликі нерівності, деформуючи шину, не впливають на положення осі обертання колеса.
Якщо ж колісний рушій наїжджає на більш значні перешкоди, то сильні поштовхи викликають підвищену деформацію шини і плавне переміщення осі обертання колеса. Здатність пневматичної шини плавно змінювати негативний вплив дефектів дорожнього покриття на вісь обертання колеса називається згладжувальною.
Ефект згладжування забезпечується пружними властивостями стисненого повітря, що міститься в шині.
Тиск повітря в шині колеса є найважливішим експлуатаційним показником і кожним виробником встановлюється відповідно до конструкції та прямого призначення шини.
Усі ми звикли говорити про диски, про те, які вони - литі чи ковані, яке в них маркування. Насправді, говорячи про них, ми завжди, навіть того не відаючи, мали на увазі саме колесо, яке включає у свою конструкцію обід і диск.
Колесо зазвичай прилаштовують на маточину, яка в свою чергу встановлена в поворотний кулак і вільно обертається на роликових підшипниках. Виготовляють колесо з листового металу способом штампування і наступного зварювання елементів. Колеса можуть бути відлиті з легкосплавних матеріалів (наприклад, алюмінієвого і магнієвого сплаву), а можуть бути і кованими, які поєднують у собі легкосплавний матеріал і штампування. Також колеса бувають дискові й бездискові (згадайте «унікальне» рішення такого колеса на всім відомій «Таврії»)
Варто відзначити, що нині шини діляться на два типи: камерні й безкамерні. У шинах першого типу є спеціальна камера, в яку закачується повітря. У безкамерній шині такої камери немає, і покришка встановлюється на обід, ущільнюється та накачується повітрям
Гума, що використовується для виробництва шин (в побуті - «покришок»), складається з каучуку (натурального або синтетичного), до якого додаються сірка, сажа, смола, крейда, перероблена стара гума та інші домішки і наповнювачі. Шина складається з протектора, подушкового шару (з брекером), каркаса, боковин і посадкових бортів із сердечниками (силове кільце)
Каркас служить основою шини: він з'єднує всі її частини в єдине ціле і надає їй необхідної жорсткості, при цьому має високу еластичність і міцність. Каркас виконують із декількох шарів корду товщиною 1-1,5 мм. Кількість шарів корду є парним для рівномірного розподілу міцності конструкції і становить зазвичай 4 або 6 для шин легкових автомобілів і 6-14 для шин вантажних автомобілів і автобусів.
Зі збільшенням кількості шарів корду підвищується міцність шини, але водночас збільшується її маса і зростає опір коченню, що неприйнятно.
Корд - це спеціальна тканина, що складається переважно з поздовжніх ниток діаметром 0,6-0,8 мм подекуди з поперечними нитками. Залежно від типу і призначення шини корд може бути бавовняним, віскозним, капроновим, перлоновим, нейлоновим і металевим. Найдешевшим з усіх є бавовняний корд, але він має найменшу міцність, яка до того ж істотно зменшується при нагріванні шини. Міцність капронового корду приблизно в 2 рази вища, ніж бавовняного, а перлонового і нейлонового корду - ще вища. Найбільш міцним є металевий корд, нитки якого скручені з високоякісного сталевого дроту діаметром 0,15 мм. Міцність металевого корду вище бавовняного більш ніж у 10 разів, і вона не знижується при нагріванні шини. Шини з такого корду мають невелику кількість шарів (1-4), меншу масу і втрати на кочення*, вони більш довговічні. Нитки корду розташовують під деяким кутом до площини, проведеної через вісь колеса. Кут нахилу ниток залежить від типу і призначення шин. Він становить 50-52° для звичайних шин
Подушковий шар (і брекер) зв'язує протектор із каркасом та оберігає каркас від поштовхів і ударів, які сприймаються протектором від нерівностей дороги. Подушковий шар зазвичай складається з декількох шарів розрідженого прогумованого корду, товщина гумового шару якого значно більша, ніж у каркасного корду. Товщина подушкового шару дорівнює 3-7 мм, а число шарів корду залежить від типу і призначення шини
Боковини захищають каркас від ушкодження і впливу вологи. Їх зазвичай виготовляють із протекторної гуми товщиною 1,5-3,5 мм.
Борти надійно утримують покришку на ободі. Зовні борту є один-два шари прогумованої стрічки, яка захищає їх від стирання об обід і від ушкоджень при монтажі і демонтажі шини.
Усередині бортів є сталеві дротяні сердечники. Вони збільшують міцність бортів, оберігають їх від розтягування і запобігають зіскакуванню шини з обода колеса
Камера утримує стиснене повітря всередині шини. Це еластична гумова оболонка у вигляді замкнутої труби. Для щільної посадки (без складок) усередині шини розміри камери трохи менші, ніж внутрішня порожнина шини. Тому заповнена повітрям камера знаходиться в шині у розтягнутому стані. Товщина стінки камери зазвичай становить 1,5-2,5 мм для шин легкових і 2,5-5 мм для шин вантажних автомобілів і автобусів. На зовнішній поверхні камери робляться радіальні риски, які сприяють відведенню назовні повітря, що залишається між камерою і шиною після монтажу шини. Камери виготовляють з високоміцної гуми.
Безкамерна шина не має камери і обідної стрічки і виконує одночасно функції шини та камери. За будовою вона дуже близька до камерної шини і за зовнішнім виглядом майже не відрізняється від неї.
Особливістю безкамерної шини є наявність на її внутрішній поверхні герметизуючого повітронепроникного гумового шару завтовшки 1,5-3,5 мм.
Примітка
Матеріал каркаса безкамерної шини також характеризується високою повітронепроникністю, оскільки для нього використовують віскозний, капроновий або нейлоновий корд, повітронепроникність якого в 5-6 разів вища, ніж у бавовняного корду.
Примітка
Посадковий діаметр безкамерної шини зменшений, вона монтується на герметичний обід.
В ідеальних умовах малюнка протектора не має бути в принципі (подивіться на сліки формульних болідів), щоб площина контакту шини з поверхнею дороги була максимальною. Однак ідеальні умови - це коли дорога покрита асфальтобетоном, причому сухим.
Тільки-но на поверхні з'явиться хоча б незначний шар води або дорога стане просто вологою, зчеплення* шини різко впаде, контакт зникне і водій втратить контроль над автомобілем. Для того щоб при наїзді на поверхню, вкриту шаром води було куди відводити рідину (можна сказати, в примусовому порядку), шина рясніє «ялинкою» протектора. Якщо ж шина призначена для руху в зимовий період, значить і форма протектора буде відповідною - збільшена кількість ламелей і брудовідводів.
Примітка
* Сила, з якою колеса «чіпляються» за дорогу, характеризується коефіцієнтом зчеплення шин із дорогою. Коефіцієнт зчеплення - відношення сили зчеплення коліс із дорогою до ваги, яка припадає на колесо. Коефіцієнт зчеплення з дорогою має вирішальне значення при гальмуванні і розгоні автомобіля. Що вищий коефіцієнт зчеплення колеса, то вищою буде інтенсивність розгону і гальмування автомобіля.
Є два поняття щодо кожної моделі шини: типорозмір та індекси.
Наприклад, зазначений типорозмір - 255/55 R16, де
255 - ширина профілю шини в міліметрах;
55 - відношення висоти профілю шини (від посадкового обода до зовнішнього краю колеса) до ширини профілю в процентах;
R - радіальна конструкція корду, складові нитки корду в шарах каркаса мають радіальне розташування (спрямовані від борта до борта);
16 - посадковий діаметр обода в дюймах (1 дюйм = 2,54 см).
В індексах вказуються параметри максимального навантаження на одну шину в кілограмах та індекс швидкості - максимальна допустима швидкість руху в кілометрах на годину, а також додаткові індекси, що характеризують властивості конкретної шини.
Індекс швидкості Максимальна швидкість, км/год
L 120
M 130
N 140
P 150
Q 160
R 170
S 180
T 190
U 200
H 210
V 240
W 270
Y 300
Z Понад 240
Існує два типи маркування: для шин внутрішнього ринку і для зарубіжних шин
Відповідно до ДЕСТу на шину наносяться такі обов'язкові написи:
- товарний знак і (або) найменування виробника;
- найменування країни-виробника англійською мовою: «Made in ...»;
- позначення шини;
- торгова марка (модель шини);
- індекс несучої здатності (вантажопідйомності);
- індекс категорії швидкості;
- «Tubeless» - для безкамерних шин;
- «Reinforced» - для посилених шин;
- «M + S» або «M.S» - для зимових шин;
- «All seasons» - для всесезонних шин;
- дата виготовлення, що складається з трьох цифр: перші дві позначають тиждень виготовлення, остання - рік;
- «PSI» - індекс тиску від 20 до 85 (тільки для шин з індексом «С»);
- «Regroovable» - у разі можливості поглиблення малюнка протектора методом нарізки;
- знак офіційного затвердження «E» із зазначенням номерів офіційного затвердження і країни, яка видала сертифікат;
- номер ДЕСТу;
- національний знак відповідності Держстандарту (допускається нанесення тільки в супровідній документації);
- порядковий номер шини;
- знак напрямку обертання (в разі спрямованого малюнка протектора);
- «TWI» - місце розташування індикаторів зносу;
- балансувальна мітка (крім шин 6,50-16С і 215/90-15С, що поставляються в експлуатацію);
- Тема; Рульове керування
1.Призначення.
Слугує для забезпечення заданого напряму руху автомобіля шляхом роздільного, узгодженого та пропорційного повороту керованих коліс на задані кути. Крім того рульове керування повинно забезпечувати безпеку руху та комфорт керування.
2. Вимоги:
1. Відповідність конструкції вимогам безпеки руху та можливість керування
з використанням автоматичних електронних, локаційних, телематичних
та інших систем керування.
2. Забезпечення високої маневреності шляхом зменшення радіуса повороту
та правильної кінематики повороту автомобіля.
3. Узгодженість, пропорційність та точність дії між кутом повороту рульового колеса та кутами повороту керованих коліс, між зусиллям на рульовому колесі та моментами опору повороту.
4. Забезпечення комфортного керування.
5. Зменшення ( усунення ) зворотної сили при передачі ударів від коліс на рульове колесо та постійна стабілізація керованих коліс.
6. Забезпечення слідкуючої дії, мінімальний час спрацювання, уникнення коливань керованих коліс та можливість керування автомобілем при відмові посилювача чи автоматичної системи керування.
7. Підвищена надійність та довговічність.
8. Забезпечення мінімального зносу бігової доріжки та кочення коліс без бокового ковзання.
9. Простота обслуговування та збільшення пробігу між проведенням обслуговування рульового керування.
10. Уніфікація.
11. Дешевизна та технологічність виготовлення.
3. Класифікація:
1. За типом рульового механізму - рейкові, черв'ячні, гвинтові, комбіновані.
2. За наявністю та типом посилювача рульового керування - з гідравлічним
посилювачем, з електричним посилювачем, без посилювача.
3. За місцем розташування посилювача рульового керування - разом з
рульовим механізмом, окремо від рульового механізму.
4. За конструкцією привода керованих коліс - привод керування передніми колесами, привод керування передніми та задніми колесами, привод керування передніми та середніми колесами, привод керування усіма колесами, з розташуванням рульової трапеції спереду або позаду осі, суцільна або розчленована трапеція, тощо.
5. За способом рульового керування: автоматичне електронне рульове керування, механічне керування, повертанням керованих коліс, складанням ланок рами.
6. За напрямом повертання керованих коліс: в одну сторону, в різні сторони, при повертанні передніх та задніх коліс.
7. За розташуванням рульового колеса: зліва або справа. Будова рульового керування
1. Рульове колесо.
2. Вал приводу рульового механізму.
3. Рульовий механізм.
4. Рульовий привод керованих коліс.
5. Посилювач рульового керування ( насос з приводом, силовий пристрій, електродвигун з механізмом приводу ).
6. Автоматичні електронні, локаційні, телематичні системи стабілізації руху та керування.
Тема: Гальмівна система автомобіля
Гальмівна́ систе́ма автомобі́ля (- сукупність пристроїв, призначених для здійснення гальмування АТЗ, поступового сповільнення чи зупинки транспортного засобу, обмеження його швидкості на спусках або для забезпечення його нерухомого стану під час стоянки
За видами гальмівні системи поділяють на:]
- Робочу
Призначена для зниження швидкості руху, обмеження її на спуску та зупинки транспортного засобу із необхідними ефективністю та стійкістю у процесі гальмування. Застосовується у всіх режимах руху автомобіля.
- Запасну (аварійну)
Призначена для зупинки автомобіля у разі відмови робочої гальмівної системи. Сумарна гальмівна сила, що створюється системою, дещо менша, ніж у робочої. Як правило, функції запасної системи може виконувати справна частина робочої або стоянкової систем.
- Стоянкову
Призначається для утримування автомобіля у нерухомому стані відносно опорної поверхні із необхідною ефективністю навіть за відсутності водія, підтримуючи стоянкові гальма у загальмованому стані за допомогою чисто механічних пристроїв.
- Допоміжну
Призначена для зниження швидкості транспортного засобу та обмеження її на спусках. Використовується на автомобілях особливо великої вантажопідйомності (МАЗ, КрАЗ, MAN) та автобусах великої місткості для зменшення навантаження на робочу гальмівну систему в разі тривалого гальмування на затяжних спусках у гірській чи пагорбистій місцевості.
Будь-яка гальмівна система складається із гальмівних механізмів та їх приводів
Принцип дії полягає у тому, що ці деталі не дають обертатися колесам, внаслідок чого автомобіль зменшує швидкість.
Типи гальмівних механізмів За будовою гальмівні системи поділяються на дискові та барабанні. Принцип дії перших засновано на стисканні гальмового диску гальмовими колодками; другого - на притисканні гальмових колодок до внутрішньої поверхні барабану.
Принцип дії гальмівного механізму заснований на використанні сили тертя, що утворюється між гальмовим диском та колодкою. Притискання колодок до диску відбувається тоді, коли гальмові поршні під дією тиску виходять із циліндрів. Зазор між колодкою та диском у розгальмованому стані становить 0,1 - 0,15 мм. Види гальмівних приводів : гідравлічний - гальмівні механізми приводяться в дію від тиску гальмівної рідини і пневматичні - від тиску повітря
Тема: Гальмівна система з гідроприводо
Гальмівна система складається з привода , гальмівних механізмів, підсилювач гальм..
Складається гідропривод гальм з таких елементів
- педалі гальма;
- головного гальмівного циліндра;
- вакуумного підсилювача;
- патрубків гідропривода і гальмівних шлангів;
- передніх і задніх робочих гальмівних циліндрів, які розташовані в гальмівних механізмах.
Принцип роботи полягає в наступному: педаль гальма через шток зв'язується з поршнем, який переміщується в головному гальмівному циліндрі (зображений на малюнку 7.2), заповненому гальмівною рідиною, як, утім, і всі патрубки та шланги гальмівної системи. При натисканні на педаль гальма поршень у циліндрі переміщується, тисне на рідину, яка передає зусилля на робочі гальмівні циліндри гальмівних механізмів.
Окрім того, що за допомогою головного гальмівного циліндра зусилля передається від педалі до гальмівних механізмів, також головний циліндр забезпечує розділення контурів
Над головним гальмівним циліндром встановлено розширювальний бачок, необхідний для компенсації розширення гальмівної рідини при її нагріві та для запобігання потраплянню повітря в систему гідропривода гальм (для цього необхідно завжди стежити за рівнем гальмівної рідини в бачку і не допускати його падіння нижче позначки «MIN»).
Розширювальний бачок розділений на два резервуари (або має один резервуар, але з розділовою перегородкою), які сполучаються з головним гальмівним циліндром системи через два отвори. На поршнях є кільцеві ущільнювальні манжети, які притискаються пружинами
РЕГУЛЯТОР ТИСКУ
У систему гідропривода гальм встановлюють регулятор тиску гальмівної рідини. Для чого він потрібен? Задні колеса мають починати гальмування на мить раніше передніх. Це зроблено для того, щоб запобігти занесенню автомобіля, якщо його колеса потраплять на слизьку поверхню. Але процес руху досить складний, і автомобіль може бути завантажений поклажею чи пасажирами, внаслідок чого навантаження на задню вісь підвищиться. А якщо задня вісь стане важчою, для її гальмування доведеться докласти більше зусилля. От саме для того, щоб водій не був обтяжений думками про розподіл гальмівних зусиль між передньою і задньою віссю, в гідропривод гальм «врізали» регулятор.
Регулятор тиску коригує тиск гальмівної рідини в системі задніх гальмівних механізмів залежно від зміни навантаження на задні колеса.
ГАЛЬМІВНІ РІДИНИ, ЩО ЗАСТОСОВУЮТЬСЯ
До гальмівної рідини пред'являють жорсткі вимоги, оскільки вона працює в украй агресивних умовах: під впливом високих і низьких температур. Тому основним показником, що характеризує гальмівну рідину, є температура її кипіння: що вона вища, то краще. Взагалі, кипіння для гальмівної рідини - це шлях до зниження ефективності гальмування практично до нуля: рідина закипіла, з'явилися пухирці повітря, педаль провалилася, а гальмування так і не почалося. Також не варто забувати про те, що низькі температури можуть призвести до замерзання гальмівної рідини, результатом чого також буде втрата ефективності гальмування.
Увага
Гальмівна рідина украй гігроскопічна. Це означає, що вона має властивість поглинати вологу, що міститься в повітрі. Попадання вологи в гальмівну рідину призведе до зниження температури її кипіння і появи кристалів льоду при замерзанні, внаслідок чого миттєво знизиться ефективність гальмівної системи в цілому.Разом з автомобілем поставляється й інструкція з експлуатації. Якщо в автомобілі її немає, відповідний посібник можна придбати окремо. У такій інструкції обов'язково буде вказано тип гальмівної рідини за класифікацією Департаменту транспорту США - DOT. На сьогодні найпоширеніші гальмівні рідини мають позначення DOT3, DOT4, DOT4+ і DOT5.1. Причому доливати в розширювальний бачок головного гальмівного циліндра рідину вищого класу допускається (наприклад, DOT4 долити в бачок із рідиною DOT3), звичайно, за умови, що обидві рідини випущені одним і тим же виробником. І навпаки, доливати в бачок з DOT4 рідину класу DOT3 не слід.
БАРАБАННІ ГАЛЬМІВНІ МЕХАНІЗМИ
Свого часу це був дуже поширений тип гальмівних механізмів. Улаштування найпростіше гальмівний щиток, що не обертається і жорстко закріплений на поворотному кулаку (якщо це керовані передні колеса) або на цапфі (якщо це задня вісь), на гальмівний щиток встановлено робочий гальмівний циліндр, також гальмівні колодки, які одним кінцем спираються на опори, а іншим - упираються в поршні робочого гальмівного циліндра. На гальмівні колодки наклеєні або приклепані фрикційні накладки, зверху усі ці деталі накриваються гальмівним барабаном, який обертається разом із колесом.
Якщо раптом знадобилося знизити швидкість або зупинитися, водій, натискаючи на педаль гальма, через гідропривод впливає на поршні робочого гальмівного циліндра, які, переміщуючись, розсовують гальмівні колодки, притискаючи їх до поверхні гальмівного барабана
Для того щоб після гальмування гальмівні колодки повернулися у вихідне положення, встановлено відвідні пружини.
Зазор між колодками і барабаном часто регулюється автоматично. Реалізовано це просто: поршні робочих циліндрів, переміщуючись назовні під дією тиску рідини, виберуть наявний між ними і пружними кільцями осьовий зазор, після чого потягнуть кільця за собою. Рух поршнів триватиме доти, доки колодки не упруться в барабан. При відпусканні педалі відвідні пружини зможуть перемістити поршні назад тільки на величину, відповідну осьовому зазору між поршнем і кільцем, оскільки зрушити кільце вони не в змозі.
Величина зазора, як було сказано вище, відповідає необхідному зазору між колодкою і барабаном. Таким чином, у міру зношування накладок кільце переміщатиметься уздовж циліндра, підтримуючи постійну величину зазора в механізмі.
Барабанні гальмівні механізми мають низку переваг, порівняно з дисковими гальмами, однак і вад чимало.
Переваги:
- велика робоча поверхня гальмівних колодок і можливість її збільшення як за рахунок діаметра гальмівного барабана, так і його ширини (корисна властивість для вантажних автомобілів);
- відносна захищеність гальмівного механізму від пилу і бруду;
- стійкість елементів гальмівного механізму до перепаду температур.
Вади:
- мала, порівняно з дисковими гальмами, потужність, що розвивається;
- велика інерційність елементів гальмівного механізму;
- чутливість до перегріву.
ДИСКОВІ ГАЛЬМІВНІ МЕХАНІЗМИ
Єдиною перспективною альтернативою барабанних механізмів для легкових автомобілів стали дискові гальмівні механізми. У таких механізмах гальмівний диск кріпиться до маточини колеса і обертається разом із колесом. Щоб зупинити автомобіль, необхідно підвести під тиском гальмівну рідину до поршня в гальмівному супорті. Поршень, впливаючи на гальмівні колодки, передасть на них зусилля від гальмівної рідини, притисне до диска і почне уповільнювати колесо. Чимось принцип дії дискового гальма схожий на велосипедне гальмо, де роль диска відіграє поверхня обода колеса, а зупинка здійснюється притисканням колодок гальма до обода. Будову дискового гальмівного механізму можна побачити на малюнку 7.4.
Існує два типи гальмівних супортів: фіксований і плаваючий. У першому випадку в гальмівному супорті є два поршні, розташовані по обидва боки від гальмівного диска. Сам супорт жорстко закріплений на поворотному кулаку. Поршні впливають на внутрішню і зовнішню гальмівні колодки. До кожного з них підводиться гальмівна рідина. У другому випадку гальмівний супорт має поршень або поршні тільки з одного боку, при цьому він має змогу переміщатися уздовж осі обертання диска. Так, при гальмуванні поршень переміщується і тисне на внутрішню колодку, після того як колодка упреться в диск, а тиск в гідроприводі продовжить зростати, вже супорт почне переміщатися і притискати зовнішню колодку до диска.
Перший варіант міцніший, але дорожчий. Другий варіант дешевший, але не такий надійний.Ефективність дискових гальм набагато вища за ефективність барабанних. Вони простіші в обслуговуванні та ліпше відводять тепло, що виділяється при гальмуванні.
Оскільки перегрів гальмівних механізмів вважається одним із найнебезпечніших моментів, вирішили збільшити ефективність відведення тепла від гальмівного механізму. Шлях вирішення проблеми простий з точки зору ідеї та не такий простий з точки зору технологічності. У диску зробили багато отворів і каналів, через які повітря може проходити з метою охолодження диска зсередини (малюнок 7.5). Ефективність підвищили багаторазово. Але у всього є своя ціна, і в цьому випадку за покращене охолодження довелося заплатити низькою стійкістю до перепаду температур. Виникла ймовірність появи тріщин на диску при потраплянні на нього, наприклад, води при дуже активному гальмуванні. Причина в тому, що отвори - це концентратори напружень. Виходить, що працює принцип «Де тонко, там і рветься
Часто на гальмівних дисках можна побачити канавки .6). Причина, по якій диск виготовляють з такими конструктивними особливостями, криється в тому, що при виконанні гальмування на фрикційних накладках гальмівних колодок утворюється шар відпрацьованого матеріалу (пилу), який погіршує ефективність гальмування. Шар відпрацьованого пилу зрізається канавками, оновлюючи тим самим робочу поверхню фрикційної накладки.
Проте час іде, деякі автомобілі стають більш потужними і важкими, мають високі динамічні показники і украй високу енергоозброєність*, і, щоб зупинити всю цю масу, що рухається на величезній швидкості, потрібне застосування надефективних гальмівних механізмів. Основний показник, що впливає на ефективність роботи гальм, як було сказано вище, - температура.
Існує два шляхи вирішення проблеми перегріву гальм. Перший із них - виготовити гальмівні механізми зі своєю системою охолодження, однак це занадто ускладнює конструкцію і подальше обслуговування. Другий - встановити композитні гальмівні диски, наприклад металокерамічні. Таким дискам взагалі не страшний перегрів. Але плата за металокераміку - крихкість і висока собівартість.
Дискові гальмівні механізми часто обладнують датчиком зносу фрикційних накладок. У найпростішому вигляді він має вигляд підпружиненої пластини, яка при досягненні граничної товщини фрикційної накладки досягає диска і починає скрипіти.
У більш ускладненому варіанті встановлено датчик у прямому сенсі цього слова. Його показники виводяться на відповідний покажчик на щитку приладів.Вакуумний підсилювач гальм
Що більшою ставала маса автомобіля, то більше зусилля потрібно було прикладати до педалі гальма, щоб досить ефективно знизити швидкість або зупинити автомобіль. Було б великою помилкою не використовувати ті фізичні процеси, які відбуваються під час роботи двигуна. Помилку не зробили - встановили вакуумний підсилювач. Чому вакуумний? Він використовує розрідження, створюване у впускному колекторі двигуна. Будова такого підсилювача нескладна (: корпус, розділений діафрагмою на дві камери - вакуумну й атмосферну. На штоку педалі гальма, всередині підсилювача, встановлено стежачий клапан, що відкриває або перекриває доступ атмосферного тиску в атмосферну камеру. Крім того, встановлено поворотну пружину діафрагми підсилювача. Після підсилювача послідовно встановлено головний гальмівний циліндр.
З огляду на різні конструктивні особливості двигунів, розрідження може підводитися не тільки від впускного колектора, а й від спеціального вакуумного насоса. Наприклад, для всіх дизельних двигунів використовується вакуумний насос, оскільки у них розрідження у впускному колекторі незначне.
Як це працює? Досить просто: в початковому положенні (коли гальмувати ніхто не збирається) тиск в обох камерах однаковий і дорівнює тиску, створюваному у впускному колекторі. Тільки-но виникне необхідність загальмувати, необхідно буде натиснути на педаль гальма - переміщення педалі передасться через штовхач до стежачого клапана. Клапан перекриє канал, який з'єднує атмосферну камеру з вакуумною. Подальше переміщення з'єднає атмосферну камеру з атмосферою. Виникне перепад тиску, який почне впливати на діафрагму і переміщати її, долаючи зусилля поворотної пружини, а діафрагма і собі переміщатиме шток поршня головного гальмівного циліндра.
Така конструкція вакуумного підсилювача забезпечує значне доповнення зусилля (воно може досягати п'ятикратного збільшення) на штоку поршня головного гальмівного циліндра, яке пропорційне зусиллю на педалі гальма. Якщо простіше: що дужче ви тиснутимете на педаль, то потужніше й ефективніше працюватиме вакуумний підсилювач.Тільки-но водій відпустить педаль гальма, атмосферний клапан перекриється, тиск в обох камерах підсилювача вирівняється, а діафрагма повернеться в початкове положення під дією поворотної пружини.
Стоянкова гальмівна система
Стоянкове гальмо (у побуті - «ручник») призначене для утримання автомобіля під час стоянки як на рівній, так і на похилій поверхні. На легкових автомобілях стоянкова гальмівна система може виконувати роль запасної гальмівної системи.
Стоянкові гальмівні системи відрізняються за типом привода, а також за типом гальмівного механізму.
За типом привода стоянкові гальмівні системи можуть бути:
- з механічним приводом;
- з гідравлічним приводом;
- з електромеханічним приводом.
СТОЯНКОВА ГАЛЬМІВНА СИСТЕМА З МЕХАНІЧНИМ ПРИВОДОМ
Проста і дешева схема впливу на гальмівні механізми задніх коліс передбачає використання тросів і важеля (або педалі), який знаходиться в салоні. Принцип дії такий: при переміщенні важеля стоянкового гальма переміщуються троси привода, які впливають на гальмівні механізми, запобігаючи у такий спосіб провертанню коліс (елементи гальмівної системи зображені на малюнку 7.1). Важіль у салоні встановлено на храповик, що дозволяє фіксувати його в робочому положенні.
Для інформування водія про те, що стоянкове гальмо в цей момент задіяне, під важелем встановлено вимикач сигналізатора на щитку приладів.
Примітка
Від важеля в салоні зусилля до гальмівних механізмів передається за допомогою тросів. У конструкції гальмівного привода стоянкового гальма використовуються один, два або три троси. Найпоширеніша схема з трьома тросами: один передній (центральний) і два задні. Передній трос з'єднаний із важелем у салоні, задні троси - з гальмівними механізмами відповідно до правого і лівого коліс. Для з'єднання переднього троса із задніми і рівномірної передачі зусилля використовується зрівнювач або балансир.Як і будь-який механізм, стоянкове гальмо необхідно регулювати, для цього передбачено регулювання довжини тросів за допомогою регулювальної гайки, встановленої часто на зрівнювачі. Повернення системи в початкове положення (зняття з гальма) проводиться при переведенні ручного важеля у відповідне положення за допомогою поворотної пружини. Пружина може розташовуватися на передньому тросі, зрівнювачі або безпосередньо на гальмівному механізмі.
Гальмівні механізми стоянкової системи можуть бути різних типів. Так, якщо ззаду застосовуються барабанні гальма, то гальмівна система використовує гальмівні механізми робочої гальмівної системи, лише в цьому випадку колодки притискаються не через робочий гальмівний циліндр, а через вплив троса системи на приводний важіль колодок. Якщо гальма дискові, то варіантів два: або передавати зусилля через приводний важіль на гальмівний супорт робочої гальмівної системи і фіксувати у такий спосіб колесо, або виготовляти диск заднього гальмівного механізму складовим (мається на увазі, що гальмівний диск буде виготовлено так, що внутрішня його поверхня виконуватиме роль гальмівного барабана).
Цікаво
Бажано завжди використовувати стоянкове гальмо, щоб запобігти закисанню тросів. Оскільки, якщо раптом трапиться екстрена та непередбачена ситуація в дорозі, скористатися гальмівною системою, як запасною, при приводних тросах, що закисли, буде неможливо.СТОЯНКОВА ГАЛЬМІВНА СИСТЕМА З ГІДРАВЛІЧНИМ ПРИВОДОМ
Така стоянкова система часто використовується на спортивних автомобілях, коли стоянкове гальмо застосовується короткочасно і потрібне воно для того, щоб домогтися від автомобіля необхідної траєкторії при проходженні повороту.
По суті, використовується такий самий важіль у салоні, ті самі задні гальмівні механізми, що і в механічному приводі, але замість тросів - шланги і патрубки, заповнені гальмівною рідиною. До важеля в салоні приєднано один або два головні гальмівні циліндри. Принцип роботи той самий, що і в звичайній робочій гальмівній системі, він був розглянутий вище.
СТОЯНКОВЕ ГАЛЬМО З ГІДРОПРИВОДОМ
У часи автоматизації та комп'ютеризації тяжкий тягар вмикання стоянкового гальма переклали на електромеханічний сервопривод. У салоні від важеля залишилася лише клавіша або кнопка. Троси замінили на електропроводку, а виконавчі механізми помістили на елементи робочої гальмівної системи.
З такою системою водієві не потрібно рахувати кількість клацань храповика при затягуванні «ручника», не потрібно перейматися регулюванням тросів стоянкового гальма - варто лише натиснути на кнопку або потягнути клавішу, і електроніка виконає свою справу.
На додачу до цього спрощення з'явилася система допомоги при рушанні з місця під гору, яка використовує стоянкове гальмо, і, зрештою, водій позбувся ще одного головного болю - відкочення автомобіля на початку руху.
Тема: Прибирально - мийні роботи
Учбові питання:
1. Способи миття транспортних засобів
2. Способи очищення деталей від бруду
Під час технічного обслуговування і ремонту застосовують такі способи миття ТЗ: а) ручний б) механізований в)автоматизований г) комбінований
Ручний спосіб здійснюють за допомогою міні - мийок. Вода під певним тиском подається на поверхню , яка підлягає очищенню.
При механізованому способі ТЗ переміщується крізь мийну установку або мийний пристрій переміщується відносно ТЗ. Для миття зовнішніх поверхонь кузовів ТЗ може застосовуватися універсальна багатощіткова установка. В момент проходження ТЗ під першою душовою рамкою, його поверхня сильно обливається водою , потім горизонтальними щітками промивається верхня поверхня кузова. Далі вертикальними барабанами промиваються бічні поверхні.Заключною операцією є ополіскування ТЗ під душовою рамкою.
Під час капітального ремонту ТЗ застосовують комплексні мийні установки, які забезпечують зовнішнє миття ТЗ а також випаровування масел з картерів з допомогою лужного розчину.
2. Для очищення деталей від бруду і нагару застосовують як хімічний так і механічний способи. При хімічному способі очищення використовують спеціальний розчин. Різновиди механічного способу очищення деталей : а) піскоструминний б) дробоструминний в) очищення кісточковим дрібязком.
При піскоструминному способі на поверхню деталі з допомогою компресора подається сухий пісок .При дробоструминному способі - металеві дробинки діаметром 2 - 3 мм, а при очищенні кісточковим дрібязком - частинки кісточок плодових порід дерев.
Тема: Догляд за лакофарбовим покриттям кузова
При догляді за лакофарбовим покриттям кузова (ЛФП) у першу чергу перевіряється стан різних його хромованих деталей і фарбування. Виявлені глибокі подряпини можуть бути вогнищами наступної корозії. При виявленні іржі, з нею необхідно боротися негайно.Її видаляють із хромованої поверхні й захищене місце покривають лаком, що перешкоджає її подальшому поширенню. Усувають іржу спеціальним складом на основі хімічних реактивів, а також з використанням крейди або зубного порошку, нанесеними на м'яку суху тканину. Залежно від місця розташування корозії, її розмірів і форми вогнища поразки рухи ганчірки можуть бути круговими або прямолінійними з легким натиском.Будь-яке порушення ЛФП кузова веде до ослаблення захисних функцій від корозії, тому ділянку з корозією негайно зачищають наждаковою шкуркою й покривають емаллю. Більш значні поверхні ґрунтують і покривають фарбою й емаллю. Технологія відновлення ЛФП наведена нижче.Раз на місяць проводять заходи щодо відновлення блиску поверхні кузова й запобіганню ЛФП від впливу зовнішнього середовища шляхом нанесення захисного воскового шару полірувальною водою, а кожні 3-4 місяця - восковою пастою. Якщо ж ЛФП втратила первісний блиск і стала матовою, то блиск відновлюють поліруванням. Полірування полягає в згладжуванні нерівностей поверхні (заповненні мікротріщин і пор, видаленні виступів), створенні стійкого захисного шару на ЛФП.У процесі експлуатації автомобіля в холодну пору року й в умовах підвищеної вологості (морський клімат) хромовані деталі змазують технічним вазеліном або маслом і обновляють змащення кожні 2-3 місяця.Негайно видаляють із поверхні кузова паливо, що витекло, масло, консистентне змащення або гальмову рідину, які можуть змінити колір фарби й ушкодити антикорозійний захист.Чисто вимиті й сухі панелі ЛФП регулярно обробляють спеціальними засобами, щоб захистити поверхню від впливу метеорологічних умов за допомогою водовідштовхувального воску, який заповнює пори й тріщини ЛФП.Покриття кузова автомобіля залежно від стану ЛФП підрозділяється на нове, обвітрене й старе. З урахуванням цього факту промисловістю налагоджений випуск різних поліролей. Кожний продукт має паспорт-етикетку з технологією його застосування.Полірування рекомендується проводити на відкритому повітрі, у тіні, при 20 градусах по Цельсію, при цьому пил не повинен попадати на поверхню автомобіля. Поліруючий склад швидко наноситься ватяним тампоном рівномірним шаром на оброблювану поверхню. Полірувати кузов найкраще невеликими ділянками, старою (випраною) махровою тканиною або полірувальними серветками, швидкими круговими рухами, поки розчинник не випарувався, до одержання блискучої поверхні.Перед поліруванням необхідно відмити поверхню кузова, особливо ретельно миється нова поверхня ( до року експлуатації). Після нанесення поліроль розтирається м'якою тканиною, її складові (віск, абразивний матеріал, розчинник) перемішуються, і після обробки поверхні кузов стає оновленим і блискучим. Полірування рекомендується починати з полірування більш грубим матеріалом (фетр або сукно), поступово переходячи на більш м'які матеріали. Від якості розтирання поліролі залежить товщина й рівномірність блискучої плівки ЛФП кузова. Сам процес полірування дуже трудомісткий і тому рекомендується використовувати електродриль зі змінними дисками.Для оцінки якості полірування проведіть такий експеримент: нанесіть воду на відполіровану панель і, якщо вода не скачується з покриття панелі після полірування, а розтікається на великій площі, то потрібно повторити процес полірування.При русі на поверхню кузова автомобіля попадають смолисті речовини, які протягом короткого часу в'їдаються у фарбу, утворюючи плями, від яких не вдається повністю позбутися. Свіжі плями видаляють м'яким дрантям, просоченому очищеним бензином (марки «Б-70»). При відсутності такого можна скористатися бензином «А-95», гасом або скипидаром. Після чого оброблену поверхню рясно промивають проточною водою. Дуже ефективним проти плям смоли є засіб для видалення бітумних плям. При його використанні можна відмовитися від наступної мийки обробленої ділянки.При русі, особливо у весняно - літній період, о поверхню кузова розбивається велика кількість комах. Залишки мертвих комах містять речовини, які можуть ушкодити фарбування, якщо їх не вилучити протягом короткого часу. Якщо вони налипнули на поверхню кузова і їх не вдається змити губкою з водою, то вдаються до допомоги теплого мильного розчину або миючого препарату. Є також спеціальні засоби для очищення від комах.Бризи будь-яких будівельних матеріалів, що потрапили на кузов, змивають теплим розчином нейтрального мийного засобу. При цьому не можна дуже сильно терти поверхню, щоб не ушкодити ЛФП. На закінчення поверхню рясно промивають чистою водою.
Тема: Щоденне технічне обслуговування
Щоденне ( щозмінне ) технічне обслуговування проводиться через 8 - 10 годин роботи транспортного засобу водієм і включає в себе такі основні операції:
а) Перевірка комплектності транспортного засобу (наявність буксирного тросу, запаски, домкрата,аптечки, знака аварійної зупинки , ключів)
б) Перевірка наявності паливо - мастильних матеріалів, необхідних для роботи двигуна
в) Перевірка герметичності систем і механізмів двигуна ( візуальний огляд)
г) Перевірка стану деталей ходової частини ( колеса, шини,деталі підвіски) - візуальний огляд
д) Перевірка герметичності гальмівної системи - візуальний огляд
ж) Перевірка дії приладів системи освітлення і сигналізації
з) Перевірка люфту рульового колеса
к) Перевірка дії гальмівної системи
Тема: Операції ТО - 1
ТО - 1 проводиться залежно від кількості пробігу ТЗ або від кількості мотогодин роботи двигуна. Під час проведення ТО - 1 виконують операції ЩТО і додатково:
а) Перевіряють надійність кріплення основних вузлів і агрегатів
б) виконують мастильні роботи згідно карти мащення
в) перевіряють натяг приводних пасів
г) зливають бруд і відстій з паливних фільтрів
д) перевіряють і при необхідності регулюють вільний хід гальмівної педалі і педалі муфти зчеплення
ж) спускають конденсат з ресивера ( у зимовий період експлуатації дану операцію рекомендують проводити
при ЩТО)
Лабораторно - практична робота
Тема: ТО двигуна
Обладнання робочого місця: Автомобілі ГАЗ - 3307, ЗІЛ -130
Порядок виконання роботи;
1. Відкрити капот і візуальним оглядом перевірити герметичність систем і механізмів двигуна.
2. Завести двигун і перевірити герметичність систем і механізмів двигуна а також герметичність системи живлення візуальним оглядом.
3. При робочому двигуні перевірити відсутність посторонніх шумів і стуків. Шуми і стуки в районі розміщення колінвала і розподільного валу свідчать про спрацювання підшипникових вузлів. Стуки в клапанній коробці свідчать про великі теплові зазори в клапанах.
4. При працюючому двигуні проконтролювати колір вихлопних газів. Поява у відпрацьованих газах сизого диму свідчить про спрацювання деталей кривошипно - шатунного механізму.
5. При робочому двигуні перевірити покази контрольно - вимірювальних приладів. Температура охолоджувальної рідини прогрітого двигуна повинна бути 80 градусів, тиск масла в системі мащення 2 - 4 атм.
6. При працюючому двигуні перевірити відсутність вібрації. Якщо двигун працює нерівномірно ( « троїть») це свідчить про те, що одна із свічок запалювання неробоча.
7. Скласти звіт про виконану роботу.
Лабораторно - практична робота
Тема: ТО механізмів трансмісії
Обладнання робочого місця: Автомобілі ГАЗ - 3307, ЗІЛ -130, ВАЗ - 2107
Порядок виконання роботи;
1. При непрацюючому двигуні перевірити герметичність вузлів і агрегатів трансмісії.
2. Завести двигун і знову перевірити герметичність вузлів і агрегатів трансмісії.
3. При працюючому двигуні перевірити правильність регулювання приводу муфти зчеплення. Правильність регулювання приводу муфти зчеплення перевіряється ввімкненням задньої передачі.
4. При працюючому двигуні перевірити легкість перемикання передач.
5. Перевірити легкість перемикання передач під час руху автомобілем.
6. Перевірити відсутність посторонніх шумів і стуків агрегатів трансмісії під час руху автомобілем.
7. Після припинення руху автомобілем перевірити на дотик рукою температуру картерів коробки передач, ведучого мосту.
8 . Скласти звіт про виконану роботу.
Лабораторно - практична робота
Тема: ТО механізмів керування ТЗ
Обладнання робочого місця: Автомобілі ГАЗ - 3307, ЗІЛ -130, ВАЗ - 2107
Порядок виконання роботи;
1. Візуальним оглядом перевірити герметичність гальмівної системи і рульового механізму ТЗ.
2. Перевірити люфт рульового колеса, повертаючи його в одну і другу сторону до моменту,коли починають повертатися керовані колеса.
3. Натиснути на гальмівну педаль при неробочому двигуні і переконатися в тому , що вільний хід гальмівної педалі не перевищує нормативних показників.
4. Перевірити стан шарнірних зєднань рульових тяг прокручуючи тяги навколо осі обертання.
5. Перевірити шплінтування рульових пальців.
6. Завести двигун і перевірити дію підсилювача гальм, шляхом натискання на гальмівну педаль.
7. Розігнати транспортний засіб до швидкості 40 км/год і перевірити дію гальм .
8. Скласти звіт про виконану роботу.
Лабораторно - практична робота
Тема: ТО електрообладнання ТЗ
Обладнання робочого місця: Автомобілі ГАЗ - 3307, ЗІЛ -130, ВАЗ - 2107
Порядок виконання роботи;
1. Відкрити капот і очистити від пилу і бруду АКБ, генератор, стартер.
2. Перевірити надійність кріплення агрегатів електрообладнання.
3. Візуальним оглядом перевірити цілісність ізоляції проводів високої і низької напруги.
4. Ввімкнути запалення і перевірити дію контрольно - вимірювальних приладів при непрацюючому двигуні.
5. Перевірити дію звукового сигналу.
6. Перевірити дію перемикача світла фар, сигналів повороту.
7. При працюючому двигуні перевірити дію контрольно - вимірювальних приладів.
8. Натиснути на гальмівну педаль і перевірити дію сигналів гальмування.
9. Скласти звіт про виконану роботу.
Лабораторно - практична робота
Тема: ТО кузова і додаткового обладнання ТЗ
Обладнання робочого місця: Автомобілі ГАЗ - 3307, ЗІЛ -130, ВАЗ - 2107
Порядок виконання роботи
1. Очистити кузов ( кабіну і вантажну платформу) від пилу і бруду.
2. Перевірити легкість відкриття і закриття капоту,кришки багажника, дверей.
3. Перевірити дію склоомивачів, склоочисників.
4. Перевірити дію опалювача салону.
5. Перевірити дію завісів бортів вантажної платформи.
6. Скласти звіт про виконану роботу.
Тема: Класифікація автомобілів
Учбові питання
1. Види автомобільного рухомого складу
2. Загальна будова автомобіля
Література: В. Ф. Кисликов, В. В. Лущик " Будова й експлуатація автомобілів" стр.5 - 9
1. Автомобільний рухомий склад за призначенням поділяють на: вантажний , пасажирський , легковий.
До вантажного автомобільного рухомого складу відносяться: вантажні автомобілі, автомобілі - тягачі, причепи, напівпричепи. До пасажирського рухомого складу відносяться: легкові автомобілі, мікроавтобуси, автобуси. Легкові автомобілі призначені для перевезення від 2 до 8 пасажирів, мікроавтобуси - від 9 до 17 пасажирів, автобуси - більше 17 пасажирів. До спеціального автомобільного рухомого складу відносяться автомобілі комунальних служб, міністерства надзвичайних ситуацій, міністерства охорони здоровя.
2. Автомобіль складається з таких частин: двигун, кузов, шасі. Шасі включає в себе трансмісію, ходову частину, механізми керування. Трансмісія призначена для передачі руху від двигуна на ведучі колеса. трансмісія включає в себе такі вузли і агрегати: зчеплення, коробка передач,карданні передачі, головна передача, диференціал,півосі,кінцеві передачі. до ходової частини відносяться: рама, колеса, підвіска. До механізмів керування відносяться рульове керування і гальмівна система. Кузов вантажного автомобіля складається з кабіни і вантажної платформи. Кузов легкового автомобіля суцільнометалевий.
Тема: Колеса і шини
Учбові питання
1. Класифікація коліс
2. Будова коліс
3. Класифікація шин
4. Будова шин
Література: В. Ф. Кисликов, В. В. Лущик " Будова й експлуатація автомобілів" стр 280 - 287
1.Колеса забезпечують безпосередній звязок автомобіля з дорогою. За призначенням вони діляться на ведучі,ведені, керовані, підтримувальні. За конструкцією вони діляться на дискові і бездискові. дискові колеса діляться на дискові з глибоким ободом і дискові колеса з плоским ободом.
2.Дискове колесо складається з диску і обода.Дані деталі виготовляють з спеціальної сталі і зєднують між собою з допомогою зварювання.За внутрішньою формою обода колеса бувають з глибоким і плоским ободом. Дискові колеса з глибоким ободом застосовують на легкових автомобілях а плоским - вантажних. На великотонажних вантажних автомобілях застосовують бездискові колеса які складаються з секторів, ступиці, притискачів.
3. Шина забезпечує пружний звязок колеса з поверхнею дороги. За конструкцією шини бувають камерні і безкамерні. За призначенням вони бувають загального і спеціального призначення. Шини спеціального призначення це пневмокотки і аркові шини які застосовують на вантажних автомобілях підвищеної прохідності.
4. Камерна шина складається з покришки і камери а безкамерна з самої покришки. За внутрішньою будовою покришки шини бувають радіальні і діагональні. У радіальних покришок нитки корду каркасу не перетинаються між собою і тому вони мають більший термін служби. Покришка шини має таку будову: борти, дротяне кільце,каркас, брекер, боковини, протектор.
Тема: Рульове керування транспортних засобів
Учбові питання:
- Призначення рульового керування
- Загальна будова рульового керування
- Принцип дії рульового керування
Література: В. Ф. Кисликов, В. В. Лущик " Будова й експлуатація автомобілів" стр 297 - 300
- Рульове керування призначене для зміни напрямку руху транспортного засобу шляхом повертання керованих коліс.
- Рульове керування складається з таких основних частин: рульовий привід, рульовий механізм, підсилювач рульового керування. Рульовий привід призначений для передачі руху від рульового колеса до керованих коліс. Він включає в себе такі елементи: рульове колесо, рульовий вал, сошка, повздовжня рульова тяга,поперечна рульова тяга, поворотні важелі. При незалежній підвісці керованих коліс до рульового приводу відноситься і маятниковий важіль. Рульовий механізм призначений для збільшення зусилля ,яке передається від рльвого колеса до керованих коліс. За конструкцією рульові механізми бувають червячні, гвинтові, рейкові або шестеренчасті. Як правило перші два види рульових механізмів застосовують на вантажних автомобілях а третій - на легкових.
Підсилювачі рульового керування призначені для зменшення зусилля на рульовому колесі під час повороту. За видом приводу вони бувають гідравлічні, електричні, гідроелектричні.
- При повертанні рульового колеса приводиться в дію рульовий вал який передає зусилля на рульовий механізм. З рульового механізму зусилля з допомогою рульових тяг передається до поворотних важелів з допомогою яких змінюється положення керованих коліс. У корпусі рульового механізму вмонтований підсилювач рульового керування , який полегшує поворот транспортного засобу.
Тема: Рульове керування транспортних засобів
Учбові питання:
- Призначення рульового керування
- Загальна будова рульового керування
- Принцип дії рульового керування
Література: В. Ф. Кисликов, В. В. Лущик " Будова й експлуатація автомобілів" стр 297 - 300
- Рульове керування призначене для зміни напрямку руху транспортного засобу шляхом повертання керованих коліс.
- Рульове керування складається з таких основних частин: рульовий привід, рульовий механізм, підсилювач рульового керування. Рульовий привід призначений для передачі руху від рульового колеса до керованих коліс. Він включає в себе такі елементи: рульове колесо, рульовий вал, сошка, повздовжня рульова тяга,поперечна рульова тяга, поворотні важелі. При незалежній підвісці керованих коліс до рульового приводу відноситься і маятниковий важіль. Рульовий механізм призначений для збільшення зусилля ,яке передається від рльвого колеса до керованих коліс. За конструкцією рульові механізми бувають червячні, гвинтові, рейкові або шестеренчасті. Як правило перші два види рульових механізмів застосовують на вантажних автомобілях а третій - на легкових.
Підсилювачі рульового керування призначені для зменшення зусилля на рульовому колесі під час повороту. За видом приводу вони бувають гідравлічні, електричні, гідроелектричні.
- При повертанні рульового колеса приводиться в дію рульовий вал який передає зусилля на рульовий механізм. З рульового механізму зусилля з допомогою рульових тяг передається до поворотних важелів з допомогою яких змінюється положення керованих коліс. У корпусі рульового механізму вмонтований підсилювач рульового керування , який полегшує поворот транспортного засобу.
Тема: Типи кузовів
Будь-який автомобіль, що випускається в світі - це набір механізмів і систем, що виконують певну функцію і які закріплені на остов. Цей остов називається несучою частиною.
Спочатку на автомобілях роль несучої частини виконувала рама, але з часом при виробництві легкових автомобілів від використання рами відмовилися, віддавши перевагу несучому кузову . Але рами використовуються досі на вантажних автомобілях.
Якщо брати до уваги легкові автомобілі, що випускаються на даний момент, то типів їх кузовів безліч.
Які бувають типи кузова
Кожен тип кузова автомобіля розрахований на свій сегмент покупців. У даній статті буде розглянуто, які бувають типи кузова авто.
типи кузовів
Відрізняються типи автомобільних кузовів між собою своєю конструкцією, і кожен з них має свою назву.
Випускаються автомобілі в кузовах купе, седан, хетчбек, універсал, лімузин, пікап, кросовер, фургон, мінівен, позашляховик. Дані типи кузовів застосовуються як на легкових автомобілях, так і на пасажирських, вантажопасажирських, і вантажних автомобілях, а також на авто підвищеної прохідності.
купе
Такий тип кузова як купе в більшості випадків використовується виробниками, які займаються випуском спортивних автомобілів. Представляє він собою трьохоб'ємний кузов, тобто конструкцією передбачено відведення окремої обсягу кузова для двигуна, окремого обсягу для пасажирів і обсягу для багажного відсіку.
Всі кузова типу купе обладнані двома дверима для пасажирів. Конструктивною особливістю купе є, то, що кузов розрахований на двох, рідше чотирьох, людина. Причому простір пасажирів сидячих позаду сильно обмежена. Яскравим представником автомобілів, в яких використовується кузов типу купе - Porsche 911 2.1.2 Види кузовів
Кузови автомобілів за видом можна розділити на одно-, двох- і трьохоб'ємні. Під об'ємом в даному випадку розуміють простір / ємність для розміщення чогось, відокремлені перегородкою від іншої частини кузова.
2.1.2.a Двохоб'ємні
Простіше кажучи, в двохоб'ємному кузові є відведений об'єм (простір) під двигун (моторний відсік з повноцінною кришкою капота). Він відділений поперечною перегородкою від другого об'єму - салону разом із багажним відділенням.
2.1.2.b Трьохоб'ємні
У трьохоб'ємному кузові є об'єм для двигуна, пасажирів із водієм і об'єм для багажного відділення.
2.1.2.c Однооб'ємні
Цікава ситуація з однооб'ємним кузовом. Тут немає як такого об'єму під моторний відсік. Двигун фактично знаходиться в салоні автомобіля під панеллю приладів.
2.1.3 Типи кузовів
Отже, з кількістю об'ємів автомобільних кузовів розібралися, тепер перейдемо до класифікації за типом.
Тип кузова частково визначає функціонал автомобіля: чи то він призначений для отримання задоволення від водіння, чи то для перевезення великої кількості людей, чи то для комфортного переміщення з точки А в точку Б і таке інше - форма і зміст кузова відповідатимуть його призначенню навіть в епоху уніфікації, універсалізації й усіляких прагнень маркетологів задовольнити якомога більшу кількість потенційних клієнтів, які у своїх побажаннях вельми вимогливі.
2.1.3.a Седан
Стисло: трьохоб'ємний, чотиридверний, п'ятимісний.
Почнемо з одного з найбільш поширених і популярних, принаймні в країнах СНД, типу кузова - седан. Це трьохоб'ємний кузов з чотирма дверима (дуже рідко - з двома) і, найчастіше, з п'ятьма повноцінними сидіннями для середньостатистичних дорослих.
З огляду на те, що майже кожна автомобільна марка виявляє мало не еталонну відданість своєму бренду, то назва типу кузова всередині компанії і в різних країнах може відрізнятися від, так би мовити, стандартизованої. Тому, наприклад, у Німеччині седани називають Limousine, а на туманному Альбіоні - не інакше як Saloon.
2.1.3.b Купе
Стисло: трьохоб'ємний, дво- / чотиридверний; дво- / чотиримісний або з компонуванням місць «2 + 2» (два повноцінні і два дитячі).
Слідом за седаном розглянемо його більш динамічну версію - купе - таку ж трьохоб'ємну, але з двома дверима. Узагалі, в колишні часи, щоб називатися «купе», автомобіль повинен був мати тільки два передні місця (виняток - плюс ще два, але неповноцінні місця позаду), двоє дверей і вкорочену колісну базу. Але з наданням більш широких повноважень усе тим же маркетологам назву «купе» почали приписувати для красного слівця повноцінним седанам, відмінною рисою яких стала чітко виражена похила, завалена задня стійка кузова. Яскравими представниками цього типажу стали Mercedes- Benz CLS, Audi A5 Sportback і VW CC.
2.1.3.c Лімузин
Стисло: трьохоб'ємний, чотиридверний, чотири-/восьмимісний.
Якщо вже почали говорити про трьохоб'ємник, варто згадати такий тип кузова, як лімузин (не плутати з лімузином в Німеччині, там він називається Pullman-Limousine або просто Pullman). Це знову ж таки седан, але часто з подовженою колісною базою, іноді з трьома рядами сидінь і з жорсткою перегородкою, що відокремлює водія від пасажирів. У більшості випадків перегородка має підйомне скло.
2.1.3.d Рідкісні варіації кузова седан
Не хочеться залишити без уваги досить ефектні перетворення кузова седан, які нині зустрічаються вже украй рідко.
Наприклад, фастбек (представник цього типу - Bentley Continental) - кузов фактично трьохоб'ємний, але з настільки похилою задньою частиною, що в профіль складається враження, що багажник відсутній як такий.
Є також хардтоп-седан - седан із відсутньою центральною стійкою кузова і часом із безрамними дверима. Такий типаж колись був популярний у Сполучених Штатах Америки.
2.1.3.e Універсал
Стисло: двохоб'ємний, трьох-/п'ятидверний, п'яти-/семимісний.
Тепер перейдімо до автомобілів двохоб'ємного сімейства, які широко представлені на ринку автомобільної техніки. Першим з-поміж них слід згадати тип кузова універсал. Це п'ятимісний, п'ятидверний (рідше трьохдверний) автомобіль із задньою частиною кузова вагонного типу й зазвичай майже вертикально встановленими дверима багажного відділення. Назва типу кузова говорить сама за себе. Універсальність полягає в тому, що, отримуючи задоволення від їзди, можна перевезти досить-таки великий об'єм поклажі. Більшість універсалів мають функцію збільшення об'єму багажного відділення за рахунок складаних задніх сидінь.
Після своєї появи універсал зазнавав різних метаморфоз: він то подовжувався, то ставав вищим, а то й зовсім розширювався в усіх напрямках.
2.1.3.f SUV (Універсал підвищеної прохідності)
Стисло: двохоб'ємний, трьох-/п'ятидверний, п'яти-/семимісний.
Збільшивши дорожній просвіт, трохи витягнувши кузов по висоті, в окремих випадках установивши всілякі пластикові захисні накладки, з універсала отримали тип кузова з нехитрою назвою «універсал підвищеної прохідності». Автомобілі з таким типом кузова належать до класу SUV (Sport Utility Vehicles, у простолюдді - «паркетник»). За прохідністю, у буквальному розумінні цього слова, автомобіль не пішов далеко від свого прабатька, але за рівнем комфорту багатьом може дати фору.
2.1.3.g Хетчбек
Стисло: двохоб'ємний, трьох-/п'ятидверний, п'ятимісний.
Хетчбек є одним з найпопулярніших в Європі типів кузова. Цей двохоб'ємний кузов є вкороченою версією універсала. Дослівно «хетчбек» перекладається як «поза спиною». У цій автівці уже не вдасться перевезти з однаковим комфортом, як в універсалі, і 4-5 пасажирів і об'ємний вантаж, але пару великих сумок вмістити можна. Проте хетчбеки, як і їхній подовжений родич, мають функцію складання задніх сидінь. Тому, якщо немає потреби в одночасному транспортуванні бригади будівельників з робочим інвентарем, то, склавши спинку другого ряду сидінь, можна отримати куб, а то й більше додаткового простору.
2.1.3.h Мінівен, мікровен і компактвен
Стисло: одно-/двохоб'ємний, чотири-/п'ятидверний, чотири-/семимісний.
Згадуючи про метаморфози кузова універсал, ми плавно підійшли до автомобілів, які уособлюють практичність і сімейність. Серед усіх типів кузовів лідер за кількістю можливих варіантів трансформації салону - мінівен. Це здебільшого двохоб'ємний, украй рідко однооб'ємний автомобіль, кузов з п'ятьма, шістьма або сімома посадковими місцями, з чотирма дверима (одні задні зсувні) або з п'ятьма дверима (усі двері розпашні або двоє задніх зсувних).
Принада будь-якого мінівена в тому, що задні сидіння можна скласти повністю або окремо, їх також можна відрегулювати, підлаштувавши таким чином салон автомобіля під конкретні потреби.
Трохи зменшивши в розмірах, урізавши функціонал салону, але не на шкоду комфорту пасажирів, отримали тип кузова мікровен, та зрештою це все той самий мінівен.
Компактвен успадкував від родичів зі спільною частиною «-вен» лише висоту стелі й посадку водія і пасажирів, що наближається до вертикальної, зберігши при цьому на належному рівні комфорт, але максимум для п'ятьох чоловік. Багажне відділення, на жаль, постраждало від перетворень найбільше.
2.1.3.i Кабріолет
Стисло: трьохоб'ємний, дво-/чотиридверний, чотири-/п'ятимісний, зі складаним дахом.
Слово про найефектніші типи кузовів. Кабріолет - типовий седан - чотири-, а то й дводверний, із дахом із будь-якого м'якого тканинного матеріалу, з чотирма повноцінними місцями для пасажирів, включно з водієм (назвати окремі версії п'ятимісними язик не повертається). Буває й таке, що дах металевий, але складаний, у такому випадку кузов називають «купе-кабріолет». Ефектність цього типу кузова - саме в його відкритості. Однак весь захват володаря кабріолета може миттєво зникнути за відсутності функції автоматизованого складання верху (так-так, є й такі в нашу епоху), бо дощ, сльота, мокрий салон і дах, що відмовляється зафіксуватися на рамці вітрового скла, залишать незабутні враження.
2.1.3.j Родстер
Стисло: трьохоб'ємний, дводверний, двомісний, зі складаним або знімним дахом.
Двоюрідним братом кабріолета є родстер. Останній - безкомпромісний: тільки двоє дверей і два посадкові місця. Чому двоюрідний брат? Тому що зроблений він на базі купе, яке плоть від плоті седана. На родстері також може бути як м'який, так і жорсткий верх. Одне об'єднує, як рідних, родстер і кабріолет - об'єм багажного відділення, що безжально з'їдається приводними механізмами й самим дахом, якщо він складаний.
Porsche 911
седан
Одним з найпопулярніших типів кузовів легкових автомобілів є седан.
Даний тип кузова також як і купе є трьохоб'ємним. Але відрізняється він тим, що кузов типу седан конструктивно довше і володіє двома рядами сидінь і дозволяє розміщуватися комфортабельно пасажирам і на передніх і на задніх сидіннях.
У більшості випадків седан має четверо дверей, але випускалися моделі і з двома дверима. У вітчизняному виробництві представниками чотирьохдверних седанів є ВАЗ-2101, 2103, 2105, 2106, 2107, «Волга», а представником дводверного седана - «Запорожець». У модельних рядах зарубіжних виробників, таких як Volkswagen BMW Audi Toyota Ford і інших, також є як двох, так і чотири-седани.
хетчбек
Останнім часом поряд з седанами популярними стали кузова типу хетчбек.
Конструктивною особливістю хетчбеків є двохоб'ємний кузов. Конструкцією кузова не передбачено окремий простір для багажного відсіку. роль багажника в хетчбек грає спеціальна ніша в пасажирському відсіку, доступ до якої здійснюється через встановлену ззаду двері.
Chevrolet Cruze
Конструкція хетчбека передбачає наявність двох або чотирьох дверей для пасажирів і додаткової задніми дверима для завантаження вантажу. До представників трьохдверних хетчбеків відноситься ВАЗ-2108, Volkswagen Polo, Hyundai i30 і ін. П'ятидверний хетчбек є ВАЗ-2109, Volkswagen Golf, Hyundai Getz і ін.
Універсал
Для людей, яким потрібна легковий автомобіль, але з можливістю перевезення вантажів випускаються автомобілі з кузовом типу універсал. Автомобілі з таким кузовом є Двохоб'ємний, як і хетчбеки, але довжина кузова у універсала значно більше.
Універсал
Розраховані вони на перевезення як пасажирів, так і вантажів, але після невеликої трансформації салону, при якій сидіння для пасажирів складаються, тим самим збільшуючи обсяг для вантажу. В основному випускаються п'ятидверний універсали (ВАЗ-2104, Opel Astra, Volkswagen Passat) але зустрічаються і тридверні (Opel Record, Ford Sierra).
лімузин
У наш час проводяться також автомобілі, кузов яких схожий на седан, але носить назву цей тип кузова - лімузин. Також як і у седана, конструкція кузова лімузина є трьохоб'ємна. Але розрахований цей кузов на комфортабельне розміщення пасажирів на задніх сидіннях, для чого довжина кузова значно збільшена, в порівнянні з седанами.
лімузин
Також у лімузинів можливо відділення впередисидящих пасажирів від тих хто знаходиться ззаду за допомогою спеціальної перегородки. До автомобілів з кузовом лімузин відноситься «Чайка», Imperial Crown, Lincoln Town Car.
пікап
Для перевезення вантажів також використовуються автомобілі з типом кузова пікап. Цікаві пікапи тим, що кузов має кабіну для розміщення пасажирів і відкриту платформу для вантажів, причому конструктивно дана платформа з'єднана з кабіною.
Кабіни у пікапів можуть бути снащени двома дверима і одним або двома рядами сидінь для пасажирів або ж чотирма дверима. До пікапам відноситься ВАЗ-ВІС, Dacia Logan Pickup, Mitsubishi L200 (фото нижче).
Mitsubishi L200
кросовер
З недавнього часу стали популярні автомобілі, в конструкції якого використовується такий тип кузова як кросовер.
По суті, даний кузов являє собою симбіоз кузовів універсал та позашляховик, про який мова піде нижче. Також як і у універсала в кроссоверах використовується Двохоб'ємний компоновка з використанням трьох або п'яти дверей. Від позашляховика кроссоверам дістався збільшений кліренс і повний привід .
паркетник
Але на відміну від повноцінних позашляховиків, кросовери не володіють високою прохідністю, за що в народі отримали прізвисько «Паркетник». Представниками кросоверів є Toyota RAV 4, Land Rover Freelander, Nissan Juke .
фургон
Ще одним автомобілем, призначеним для перевезення вантажів, є фургон.
Кузов типу фургон є Однооб'ємний, полутораоб'емную або ж Двохоб'ємний суцільнометалеву конструкцію, в якій кабіна для пасажирів об'єднана з вантажним відсіком, єдине, можливо їх відділення перегородкою. До фургонам відносяться Lada Largus, Volkswagen Caddy, Fiat Doblo (фото нижче).
Fiat Doblo
Мінівен
Дуже схожі за зовнішнім виглядом з фургонами автомобілі з типом кузова мінівен, оскільки при їх виробництві використовується одна і та ж платформа. Відрізняються авто з такими кузовами тим, що розраховані вони на перевезення пасажирів, для чого салон автомобіля обладнаний декількома рядами сидінь.
Особливостями мінівена є використання однооб'ємний і полутораоб'емной конструкції. Мінівенами є ВАЗ «Надія», Volkswagen Sharan, Opel Zafira.
позашляховик
Також, автовиробники випускають автомобілі високої прохідності - позашляховики.
джип
У позашляховиків тип кузова можна віднести до універсального, ще він збільшений по висоті. Відмінною особливістю позашляховика є високий кліренс, повний привід і колеса великого діаметру. УАЗ «Патріот» , Jeep Wrangler, Ford Maverick.
Тема; Кузов вантажного автомобіля
Бортова платформа вантажного автомобіля складається з дерев'яних і металевих деталей. Основу платформи становить підлога, зроблена з дощок, яка спирається на поздовжні й поперечні бруси. До основи прикріплено передній борт (нерухомо), відкидні бічні і задній борти. Відкидні борти з'єднані з основою завісами удержуються в піднятому положенні спеціальними запорами у кутах бортів. До рами автомобіля бортова платформа кріпиться стрем'янками
Кабіна вантажного автомобіля) капотної конструкції складається з каркаса , кришки , верхньої , задньої і бічних панелей, між якими зроблено дверні прорізи. В прорізах на завісах навішуються двері. В зачиненому положенні двері удержуються за допомогою спеціальних замків. Двері кабіни обладнано опускним склом із склопідйомниками та кватирками. У віконні прорізи кабіни вставлено гнуте скло, яке не відкривається. Всередині кабіни розміщено сидіння водія та органи керування.
Сидіння водія може бути двомісним або тримісним, спільним для водія й пасажирів або окремим. У разі роздільної конструкції сидіння виконують регульованим за висотою й довжиною, а також за нахилом спинки. В кабінах безкапотної конструкції передбачають одне спальне місце, розташоване впоперек кабіни за спиною водія. Щоб забезпечити доступ до двигуна, в таких кабінах роблять пристрій для перекидання кабіни відносно передніх шарнірних опор (автомобілі МАЗ, КамАЗ).
Оперення вантажного автомобіля в разі капотного компонування складається з капота крил , підніжок, коли двигун розташовано під кабіною, до оперення входять тільки крила, підніжки та облицювання радіатора..Класифікація вантажних автомобілів за типом вантажної платформи включає наступні види:
Напівпричіп тентований (євротент, єврофури) - поширений варіант кузова, який використовується для більшості перевезень. Має спеціальні розпірки і брезентовий тент зі шнурівкою. Така конструкція захищає вантаж від погодних умов і забезпечує безпеку перевезення. При повному розтентуванні можна виконати бічне і верхнє завантаження. Такий тип кузова часто використовується для вантажоперевезення з Європи,
Автосцепка - автомобіль, з'єднаний з причепом. Цей тип дозволяє перевозити значний обсяг вантажу до 120 м3 і в короткий термін виконувати його завантаження розвантаження. Недолік - не призначений для довгомірних вантажів.
Рефрижератор - металевий фургон, захищений теплоізоляцією і укомплектований кліматичним устаткуванням. Холодильний відсік підтримує постійну температуру в заданих межах від + 25º до -25º C. Його призначення - перевезення швидкопсувних вантажів або вантажів, що потребують спеціальних умов. Залежно від діапазону температур розрізняють 6 класів рефрижераторів.
Ізотермічний кузов - суцільнометалева конструкція зберігає температуру за рахунок укладання теплоізоляційних матеріалів. Умови всередині фургона сприятливі для товару, чутливого до коливань температури.
«Jumbo» - напівпричіп збільшеної місткості, що має особливу «Г» -образну форму підлоги і зменшений розмір коліс. Ці особливості дозволяють виділити додатковий простір для вантажу.
Контейнеровоз - причіп з майданчиком, на яку встановлюються контейнери, що мають уніфіковані розміри. Даний тип причепа незамінний для мультимодального перевезення, наприклад при реалізації доставки вантажу з Китаю в контейнерах через Європейські порти.
Автоцистерни - використовуються для перевезення наливних вантажів. Виготовляються зі сталі або алюмінію, останній матеріал має кращу стійкість до корозії і не вимагає нанесення спеціального покриття. Цистерни бувають з однією або декількома секціями, можуть бути обладнані насосами або парової камерою для обігріву вантажу.
Самоскид - відкритий бортовий кузов, який має гідравлічний пристрій, що дозволяє здійснити автоматичне вивантаження сипучого вантажу. Його борт кріпиться на шарнірах і відкривається при нахилі.
Відкрита платформа - призначена для транспортування вантажу, на який не впливають погодні умови. Відсутність обмежувачів дозволяє використовувати її для негабаритних вантажів.
Бортовий кузов - платформа, обмежена бортами, яка використовується для вантажу нечутливого до зовнішніх умов.
Платформа для негабаритних і великовагових вантажів до 200 т. Низькорамні трали перевозять автомобілі та іншу техніку.
Тема Буксирний пристрійБуксирний пристрій встановлюють на рамі автомобіля і він складається з таких деталей
1 - корпус; 2 - опорні пластини; 3 - стержень гака; 4 - напрямна; 5 - вісь;
6 - заскочка; 7 - замок; 8 - гумовий пружний елемент
Сідельно-зчіпний пристрій застосовують на автомобілі-тягачі, коли він працює з напівпричепом, на якому в цьому разі встановлюють зчіпний шворінь. Номінальний діаметр шворня для напівпричепа повною масою до 40 т становить 50,8 мм, а для напівпричепів з масою від 40 до 100 т - 89 мм. Відповідний діаметр отвору захватів дорівнює діаметрові шворня плюс 0,3...0,5 мм. Зчіпний пристрій забезпечує автоматичне зчеплення напівпричепа з автомобілем-тягачем при плавному в'їжджанні його під загальмований напівпричіп.
Тема: Система технічного обслуговування
Учбові питання
1. Види ТО
2.Організація робіт із ТО автомобілів
Література:Б. С. Бабіч, В. В. Лушик « Технічне обслуговування і ремонт металевих кузовів автомобілів стр. 80 -84
1. Технічне обслуговування - комплекс операцій для підтримання автомобіля в працездатному або справному стані. Згідно з положенням про технічне обслуговуванням та ремонт рухомого складу автомобільного транспорту передбачено такі види ТО:
А) Щоденне або щозмінне ( ЩТО)
Б) Перше ( ТО - 1)
В) Друге ( ТО - 2)
Г) Сезонне ( СТО)
Д) ТО за талонами сервісної книжки
Періодичність проведення ТО крім сезонного залежить від умов експлуатації. Сезонне ТО проводиться два рази на рік (весною і восени).
2. Організація робіт із ТО автомобілів залежить від належності їх юридичним або фізичним особам. ТО за автомобілями які належать юридичним особам проводиться на автотраспортних підприємствах а за автомобілями які належать фізичним особам - на станціях технічного обслуговування. Форма організації робіт з ТО може бути бригадна і агрегатно - дільнична. За бригадної форми організації ТО передбачається створення спеціалізованих бригад , які виконують весь комплекс робіт з ТО. При агрегатно - дільничній формі створюються окремі виробничі дільниці для виконання всіх видів робіт з ТО.
Тема: Технічне обслуговування кривошипно - шатунного механізму
Учбові питання:
1. Основні несправності кшм
2. Причини виникнення несправностей кшм
Література: В. Ф. Кисликов ,В. В. Лущик « Будова й експлуатація автомобілів» стр 78 - 79
1. Основні несправності кшм:
А) Стуки і шуми
Б) Зниження потужності
В) Підвищена витрата палива і масла
Г) Поява диму у відпрацьованих газах
2. Причини виникнення шумів і стуків:
А) Спрацювання деталей тертьових зєднань
Б) Збільшення зазорів між спряженими деталями
Причини зниження потужності:
А) Порушення ущільнення між деталями кшм (головка циліндрів - блок - картер)
Б) Спрацювання або руйнування деталей кшм
Причини підвищеної витрати палива , масла, димного вихлопу:
А) Залягання поршневих кілець
Б) Руйнування поршневих кілець
Тема: Технічне обслуговування механізму газорозподілу
Учбові питання:
1. Основні несправності механізму газорозподілу
2. Причини виникнення несправностей
Література: В. Ф. Кисликов ,В. В. Лущик « Будова й експлуатація автомобілів» стр 80 - 81
1.Механізм газорозподілу може мати такі несправності:
А) Спрацювання деталей механізму газорозподілу
Б) Нещільне прилягання клапанів
В) Неповне відкриття клапанів
2. Причини нещільного прилягання клапанів:
А) Відкладення нагару на клапанах і гніздах
Б) Руйнування клапанних пружин
В)Заїдання клапанів у напрямних втулках
Г) Відсутність теплових зазорів у клапанах
Причиною неповного відкриття клапанів є великий тепловий зазор. Ця несправність характеризується підвищеними стуками , які виникають у клапанному механізмі.
Тема: Технічне обслуговування системи охолодження
Учбові питання:
1. Основні несправності системи охолодження
2. Причини виникнення несправностей
Література: В. Ф. Кисликов ,В. В. Лущик « Будова й експлуатація автомобілів» стр 82 - 84
1. Основні несправності системи охолодження:
А) Перегрівання двигуна
Б) Переохолодження двигуна
2. Причини перегрівання двигуна:
А) Негерметична система охолодження
Б) Несправний клапан - термостат
В) Недостатній рівень охолоджувальної рідини
Г) Недостатній натяг пасу приводу вентилятора
Д) Забруднення системи охолодження накипом
Причини переохолодження двигуна:
А) Несправний клапан - термостат
Б) Заїдання жалюзів радіатора у відкритому положенні
Тема: Технічне обслуговування системи мащення
Учбові питання:
1. Основні несправності системи мащення
2. Причини виникнення несправностей
Література: В. Ф. Кисликов ,В. В. Лущик « Будова й експлуатація автомобілів» стр 85- 86
1. Основні несправності системи мащення:
А) Низький тиск масла
Б) Високий тиск масла
2. Причини низького тиску масла в системі мащення:
А) Негерметична система
Б) Низький рівень масла в піддоні картера
В) Низька вязкість масла
Г) Несправний редукційний клапан масляного насосу
Д) Спрацювання шестерень масляного насосу
Ж) Спрацювання підшипників колінвала
Причини високого тиску масла в системі мащення:
А) Висока вязкість масла
Б) Несправний редукційний клапан масляного насосу
В) Засмічення маслопроводів
Тема; Буксирний пристрій
Вантажні автомобілі загального призначення мають кузови у вигляді дерев'яної бортової платформи. На спеціалізованих автомобілях кузови пристосовані для перевезення певного вантажу (самоскидні, фургони, цистерни тощо).
.Тема; Кузов вантажного автомобіля
Тема: Пасові передачі
Пасова передача - це механічний пристрій для передавання механічної енергії (механічна передача) між валами за допомогою гнучкого елементу (приводного паса) за рахунок сил тертя або сил зачеплення (зубчасті приводні паси).
Загальні відомості
У найпоширенішій конструкції пасова передача складається з ведучого (a) і веденого (b) шківів та замкнутої форми приводного паса (c,d), що розміщується на шківах із деяким попереднім натягом. Вільна ділянка (c) паса, що набігає на ведучий шків (a), називається ведучою віткою паса, а вільна ділянка (d), що набігає на ведений шків, називається веденою віткою. Попередній натяг паса створюється за рахунок його пружного розтягу при закладенні на шківи або застосуванням спеціального натяжного пристрою (ролика) (e). Під час роботи передачі пас передає енергію від ведучого шківа до веденого за рахунок сил тертя, які виникають між пасом та шківами.
Пасові передачі не забезпечують жорсткого зв'язку між шківами через можливість проковзування паса на шківах. Тому у кінематично точних приводних механізмах пасові передачі застосовують дуже рідко.
Пасові передачі переважно використовують для передавання потужностей у діапазоні 0,2-50 кВт. Зустрічаються також передачі для потужностей 500 і навіть 1500 кВт, проте застосування їх має унікальний характер.
Передавальні числа пасових передач допускаються до 5-6, рідше до 10.
Швидкість руху пасів у передачах загального призначення не перевищує 30 м/с. Спеціальні швидкохідні паси допускають при пониженій довговічності швидкості до 50 і навіть до 100 м/с.
ККД пасових передач різних типів становить близько 0,90-0,97.
Переваги та недоліки
У порівнянні із зубчастою передачею пасові передачі мають низку переваг і недоліків. Основні переваги пасової передачі:
- можливість передавання руху між валами, що знаходяться на значній відстані;
- плавність та безшумність роботи, які обумовлені еластичністю паса;
- запобігання різкому перевантаженню елементів машини внаслідок пружності паса та можливості його проковзування на шківах;
- простота конструкції, обслуговування та догляду в експлуатації;
- відносно високий ККД.
До недоліків пасової передачі належать:
- неможливість виконання малогабаритних передач (для однакових умов навантаження діаметри шківів майже у 5 разів більші, ніж діаметри зубчастих коліс);
- несталість передавального числа через можливе проковзування паса;
- підвищене навантаження валів та їхніх опор, що пов'язане із потребою достатньо високого попереднього натягнення паса;
- низька довговічність приводних пасів (у межах 1000-5000 год).
Класифікація
За формою поперечного перерізу приводного паса:
- плоскопасова;
- клинопасова;
- круглопасова;
- з поліклиновим пасом.
За розміщенням валів:
- відкрита;
- перехресна;
- напівперехресна:
- багатошківна з натяжним роликом.
Пасова передача може мати як постійне, так і змінне передавальне число (варіатор).
Окремо слід розглядати зубчасто-пасові передачі у яких плоский пас на внутрішньому боці має зубці трапецієвидної форми, а шківи - відповідні їм зубці на ободі. Така передача працює за принципом зачеплення, а не тертя. До пасових передач вона належить умовно тільки за назвою та формою тягового органу.
Тема; Ланцюгова передача
Ланцюгова передача
Обертальний рух зірочки з ланцюгом
Ланцюго́ва переда́ча (рос. цепная передача, англ. chaingear, chaintransmission, chaindrive; нім. Kettenantrieb m) - механізм (передача) у вигляді нескінченного ланцюга, що рухається по зубчастих колесах (зірочках), закріплених на паралельних валах, передаючи обертовий рух між цими валами.
Основні характеристики
Швидкість руху ланцюга у передачах загального призначення досягає 15 м/с при передаванні потужності до 100 кВт, а у спеціальних приводах - до 35 м/с при потужності до 2000 кВт. За допомогою ланцюгової передачі можна забезпечити передавальне число u ≤ 10, а найраціональніше мати u ≤ 4 при високому ККД (до 0,97).
Конструкція втулково-роликового ланцюга
Конструкція
- Зовнішні пластини
- Внутрішні пластини
- Валик
- Втулка
- Ролик (сепаратор)
Валик ) запресований у зовнішні пластини (1) ланцюга і утворює з ними одне ціле. На валик вільно посажена втулка яка запресована у внутрішні пластини (Якщо на втулку ( встановити вільно ролики то ланцюг буде втулково-роликовим. Такий ланцюг замінює тертя ковзання на тертя кочення при набіганні ланцюга на зірочку, але погіршує динамічні властивості (ланцюг стає важчим).
Найстаріше відоме зображення ланцюгової передачі, з книги Су Сонга 1092 року, де описано його годинниковий механізм в башті міста Кайфенг
Класифікація
Ланцюгові передачі поділяють за такими ознаками: За типом ланцюга, яким оснащена передача, розрізняють ланцюгові передачі з:
- роликовими ланцюгами;
- втулковими ланцюгами;
- зубчастими ланцюгами.
За можливістю зміни відстані між осями зірочок ланцюгові передачі бувають із регульованою та постійною міжосьовою відстанню. За способом регулювання натягу ланцюга розрізняють ланцюгові передачі з періодичним і неперервним регулюванням натягу. За кількістю зірочок, що охоплені одним ланцюгом, ланцюгові передачі можуть бути двозірочкові, тризірочкові і т.д. За конструктивним виконанням та умовами експлуатації розрізняють відкриті ланцюгові передачі і закриті. Останні працюють у спеціальному корпусі в умовах неперервного змащування.
Переваги та недоліки
Ланцюгові передачі порівняно з іншими механічними передачами мають такі основні переваги:
- можливість використання при значних відстанях між валами;
- достатньо високий ККД;
- можливість передавання обертового руху одним ланцюгом декільком валам, у тому числі і з протилежним напрямом обертання.
До недоліків ланцюгових передач належать такі:
- збільшення довжини ланцюга через зношення шарнірних з'єднань і відповідне ослаблення натягу;
- нерівномірність руху ланцюга і пов'язані з цим динамічні явища у передачі та підвищений шум;
- низька кінематична точність при реверсуванні;
- потреба застосування додаткових пристроїв для регулювання натягу ланцюга.
Приклади використання
Ланцюгові передачі застосовують у сільськогосподарських та транспортних машинах, підйомних пристроях, у приводах конвейєрів тощо. Ланцюгова передача дозволяє надавати обертовий рух валам, що знаходяться на порівняно великій відстані, а її габаритні розміри значно менші від габаритних розмірів пасової передачі. Неможливість проковзування ланцюга на зірочках забезпечує сталість середнього передавального числа передачі.
У гірничій справі застосовується у системах транспортування (конвеєрах), елеваторах, екскаваторах, лебідках, тельферах тощо.
Тема : Зубчасті передачі
Зу́бчаста переда́ча - механізм, що має два зубчасті колеса, які можуть повертатися навколо осей, їх відносні положення зафіксовано й одне зубчасте колесо повертає інше за допомогою послідовної дії зубців, які перебувають у контакті[1]
Зубчаста передача складається з приводного зубчастого колеса (зубчасте колесо із зубчастої передачі, яке обертає інше) і веденого зубчастого колеса (зубчасте колесо із зубчастої передачі, що обертається під дією іншого).
Зубчасте колесо із зубчастої передачі, яке має менше число зубців носить назву шестерня (англ. pinion). Зубчасте колесо із зубчастої передачі, яке має більше число зубців - колесо (спрощене «спряжене зубчасте колесо шестерні», коли термін явно використано на протилежність до «шестерні»; англ. roue)[1].
Основні переваги
- Постійність передавального числа, яке залежить лише від числа зубів зубчастих коліс (u=z2/z1 , де u - передавальне число передачі; z1, z2 - число зубів відповідно ведучого та веденого зубчастих коліс).
- Можливість передачі великих потужностей (до 50000 кВт).
- Високий ККД (η = 0,97...0,985).
- Малі габаритні розміри в порівнянні з іншими видами передач (фрикційними, пасовими та ін.).
- Висока надійність та довговічність роботи.
Основні недоліки
- Необхідність використання складного обладнання для виготовлення зубів передач.
- Неможливість здійснення безступінчастого регулювання швидкості.
- Робота зубчастого передавача супроводжується шумом, особливо на високих швидкостях. Зубчасті передавачі можуть бути джерелом вібрації.
Класифікація
- За передавальним відношенням:
- з постійним передавальним відношенням;
- зі змінним передавальним відношенням.
- За формою профілю зубців:
- евольвентні;
- колові (передача Новікова);
- циклоїдні
- За типом зубців:
- прямозубі;
- косозубі;
- шевронні;
- криволінійні.
- За орієнтацією осей валів:
- з паралельними осями (циліндричні передачі з прямими, косими і шевронними зубцями);
- з осями, що перетинаються (конічні передачі);
- з мимобіжними осями.
- За формою початкових поверхонь:
- циліндричні;
- конічні;
- гіперболоїдні;
- За коловою швидкістю коліс:
- тихохідні;
- середньошвидкісні;
- швидкохідні.
- За ступенем безпеки :
- відкриті;
- закриті.
- За відносним обертанням коліс і розміщенням зубців:
- внутрішнє зачеплення (обертання коліс в одному напрямку);
- зовнішнє зачеплення (обертання коліс в протилежних напрямках).
Рейкова передача - один із видів циліндричної зубчастої передачі, де радіус ділильного кола рейки рівний нескінченності. Застосовується для перетворення обертового руху в поступний і навпаки.
Гвинтові, черв'ячні і гіпоїдні відносяться до зубчасто-гвинтових передач. Елементи цих передач ковзають відносно один одного.
Тема: Карданні передачі
Карданна передача (універсальний шарнір, шарнір Гука, універсальна муфта, механізм Кардана) - просторовий шарнірний механізм, що складається з центральної хрестовини і двох посаджених на кінці валів-вилок, що шарнірно сполучені з кінцями хрестовини. Служить для передачі крутного моменту між валами, що мають велике кутове зміщення осей (до 40-45°), яке у процесі обертання валів може змінюватись
Основна концепція універсального шарніра була відома з античних часів. Ймовірно універсальний шарнір використовували у Стародавній Греції в конструкції балісти. Перша відома особа, що запропонувала використовувати такий шарнір для передачі рушійної сили, був Джироламо Кардано, італійський математик у 1545 році, хоча неясно, чи він виготовив робочу модель. У Європі пристрій часто називають «Кардан», або «карданний вал». Швед Крістофер Польхем пізніше заново його винайшов, що шведською мовою дало назву Polhemsknut.
Механізм пізніше був описаний у праці Technica Curiosa SIVE Артіс Mirabilia (1664) Гаспаром Шоттом (Gaspar Schott), який назвав його paradoxum, де зробив помилкове твердження про сталість передачі кутової швидкості.[1] Незабаром після цього, між 1667 і 1675, Робертом Гуком було проаналізовано роботу шарніра й виявлено, що його швидкість обертання не є сталою. Перша згадка терміна «універсальний шарнір» для цього пристрою була зроблена Гуком у 1676 році, в його книзі Helioscopes[2]. Він опублікував свій опис у 1678 році,[3] в результаті чого механізм отримав нову назву «шарнір Гука». У 1683 році Гук запропонував вирішення проблеми нерівномірної швидкості обертання універсального шарніра: механізм, який зараз відомий як шарнір рівних кутових швидкостей.
Термін «універсальний шарнір» був поширений у 18 і 19 століттях і використовувався у механізмах привода млинів та ткацьких фабрик. У 19 столітті використання універсального шарніра поширилося на широкий спектр технічних рішень. Значна кількість універсальних шарнірів була використана у системі керування телескопа Нортумберленд Інституту астрономії в Кембріджському університеті в 1843 році[4]. Ефріам Шей (Ephriam Shay) в 1881 р. отримав патент на локомотив, де використовувався подвійний універсальний шарнір у приводі локомотива[5]. Чарльз Амідон (Charles Amidon) використав універсальний шарнір малих розмірів у коловороті, запатентованому у 1884 році[6].
Карданні шарніри використовуються для:
- компенсації неточності взаємного розміщення валів, що виникає при складанні, при деформаціях рами і ресор (транспортні та ін. машини);
- передачі обертання переставним валам (шпинделі багатошпиндельних свердлильних верстатів, валки вальцювального обладнання та ін.);
- передачі обертання валам, розміщення яких змінюється під час роботи (консолі фрезерних верстатів та ін.).
Часто використовуються конструкції, у яких дві шарнірні муфти сполучаються проміжним валом: такий пристрій називається карданним валом і є звичайною конструкцією багатьох приводних валів.
За габаритами й крутними моментами карданні шарніри (шарнірні муфти) поділяються на:
- малогабаритні, призначені для передавання малих моментів (від 12,5 до 1280 Н·м). У них шарніри розміщені в габаритах ступиць півмуфт;
- великогабаритні, що призначені для передавання середніх і великих моментів (від 1000 до 800000 Н·м). У них шарніри винесені за габарити півмуфт.
Карданний вал служить для передачі обертального моменту від коробки передач (роздавальної коробки) до ведучих мостів у випадку класичного або повноприводного компонування. Також використовується в травмобезпечній рульовій колонці для з'єднання рульового вала й рульового виконавчого механізму (рульового редуктора або рульової рейки).. Будова карданної передачі : карданний вал , проміжна опора, шарніри.
Карданна передача має істотний недолік - несинхронність обертання валів, що збільшується при збільшенні кута між валами, що виключає можливість застосування карданної передачі в багатьох пристроях, наприклад, у трансмісії передньоприводних автомобілів. Шарнір рівних кутових швидкостей (ШРКШ або синхронний шарнір) - досконаліша конструкція того ж призначення, з назви якої випливає, що вона забезпечує синхронність обертання валів.
Тема: Гідропривід транспортних засобів
Гідропри́вод (гідравлі́чний при́вод) (рос. гидропривод, англ. hydraulic power drive, нім. hydraulischer Antrieb m, Hydraulikanlage f) - привод, до складу якого входить гідравлічний механізм з одним чи більше об'ємними гідродвигунами, призначений для передавання, керування та розподіляння енергії робочою рідиною під тиском[1]. Гідропривод, що складається з гідравлічної апаратури та гідроліній, використовується для приведення в дію робочих органів машин та механізмів за допомогою потенціальної енергії рідини, що перебуває під тиском. При цьому енергія передається за допомогою переміщення окремих об'ємів рідини.
Гідропривод є свого роду «гідравлічною вставкою» між приводним двигуном і навантаженням (машиною або механізмом) та виконує ті ж функції, що і механічні передачі (редуктор, пасова передача, кривошипний механізм тощо).
Базовими елементами гідроприводу є гідромашини (енергоперетворювачі): насос і гідравлічний двигун. Насос є джерелом гідравлічної енергії, а гідродвигун - її споживачем, тобто перетворює гідравлічну енергію в механічну.
Для підтримання роботи гідроприводу у переважній більшості гідросистем встановлюється допоміжна апаратура: масляні фільтри, системи охолодження, гідроакумулятори, гідробаки та ін.
Для контролю за роботою гідроприводу використовують контрольно-вимірювальні прилади: манометри, витратоміри, термометри тощо.
Робоча рідина в гідроприводі є одночасно носієм енергії і змащенням. При цьому вона зазнає впливу високих тисків, швидкостей і температур. Крім того, рідина повинна бути нейтральною до матеріалів, пожежобезпечною і нетоксичною. Значною мірою ці вимоги задовольняють мінеральні оливи і синтетичні рідини на кремнійорганічній основі. На сьогодні як робочі рідини об'ємних гідроприводів, що використовуються в загальному машинобудуванні, застосовуються мінеральні оливи: індустріальні (И-20, И-30, И-50)[2], турбінні, веретенні тощо.
Принципова гідравлічна схема гідроприводу обертального руху з розімкненою (вгорі) і замкнутою циркуляцією (внизу) рідини
За принципом роботи гідроприводи бувають об'ємними (гідростатичними), гідродинамічними і змішаними:
- у гідродинамічних приводах використовується в основному кінетична енергія потоку рідини;
- у об'ємних гідроприводах використовується потенційна енергія тиску робочої рідини;
- у змішаних гідроприводах поєднуються властивості перших двох видів.
За характером руху вихідної ланки гідродвигуна гідравлічні приводи поділяються на:
- гідроприводи обертального руху (гідродвигуном служить гідромотор);
- гідроприводи поступального руху (гідродвигуном служить у переважній більшості гідроциліндр);
- гідроприводи поворотного руху (гідродвигуном служить поворотний гідродвигун).
За схемою циркуляції рідини у приводі:
- гідропривод із замкнутою схемою циркуляції, у якому робоча рідина від гідродвигуна одразу повертається у всмоктуючу гідролінію насоса;
- гідропривод з розімкненою системою циркуляції, у якому робоча рідина знаходиться у гідробаку і постійно контактує з атмосферою.
Гідропривод із замкнутою циркуляцією робочої рідини компактний, має невелику масу і допускає велику частоту обертання ротора насоса без небезпеки виникнення кавітації, оскільки в такій системі у всмоктуючій лінії тиск завжди вищий за атмосферний. До недоліків слід віднести погані умови для охолодження робочої рідини, а також необхідність зливу робочої рідини та заповнення гідросистеми при заміні або ремонті гідроапаратури.
Переваги розімкненої схеми - хороші умови для охолодження і очищення робочої рідини. Проте такі гідроприводи громіздкі і мають велику масу, а частота обертання ротора насоса обмежується швидкостями руху робочої рідини, що допускаються (з умов безкавітаційної роботи насоса), у всмоктуючому трубопроводі.
За можливостями і видом регулювання гідропривод може бути нерегульованим і регульованим, останній у свою чергу буває:
- об'ємного регулювання;
- дросельного регулювання.
За задачами регулювання, гідроприводи бувають:
- стабілізаційні;
- слідкувальної дії;
- програмного керування.
Переваги гідроприводів
Значне поширення гідроприводів у різних галузях зумовлюється низкою істотних переваг, до яких у першу чергу належать:
- можливість одержання великих сил та обертальних моментів при порівняно малих розмірах та масі гідродвигунів;
- передача великих потужностей при малій масі гідроприводу;
- плавність рухів вихідних ланок;
- можливість безступінчастого регулювання швидкості у широкому діапазоні;
- мала інерційність;
- простота керування та автоматизації;
- висока експлуатаційна надійність та стійкість до перевантажень;
- простота реалізації основних видів рухів: обертального, зворотно-поступального і зворотно-поворотного.
Недоліки гідроприводів
При незаперечних високих якостях гідравлічного приводу слід відзначити і властиві йому недоліки:
- гідроприводи поступаються електричним у відстані транспортування енергії від джерела до споживача та швидкості передачі командних сигналів;
- у гідроприводах актуальним є питанням забезпечення герметичності порожнин, що знаходяться під тиском;
- чутливість до в'язкості робочої рідини, котра у свою чергу залежить від температури;
- нижчий к.к.д. у порівнянні з механічними передачами у приводах.
Гідропривід застосовують у гальмівних системах транспортних засобів, проводі муфти зчеплення, підсилювачі рульового керування, автоматичних коробках передач.
Тема : Пневмопривід
Пневмопривід - це сукупність пневмомашин і пневмоапаратури, що перетворює енергію стисненого повітря в механічну.Пневмопривід
Пневмопривід - перетворює енергію стисненого повітря в механічну. Робочим тілом у пневмоприводах є стиснутий газ або повітря, і діє він або тиском на тверді поверхні (циліндри з рухомими поршнями, мембрани), або у вигляді аеродинамічного ефекту (струменеві елементи).
Стиснене повітря або газ, одержаний за допомогою компресійної установки, в яку входять: компресор, нагнітаючий повітря в систему; ресивер для створення запасу стисненого повітря; пристрій для очистки повітря від водяних парів, пороху; трубопроводи, по яких стиснене повітря чи газ від компресора поступає до пневмодвигунів; пристрої контролю і автоматики.
Внаслідок значних коливань тиску повітря в пневмосистемах виникають досить різкі зміни швидкості руху деталей робочих органів, не завжди допустимі в роботі технологічного обладнання. Для виключення цього недоліку використовують у пневмоприводі повітря з незначним надлишком тиску, але при цьому необхідне відповідне збільшення площі поверхонь, сприймаючих тиск повітря.
Пневмопривід може бути раціонально використаний в установках з епізодичною роботою, пересувних, за необхідності різко ударної дії. Пневмопривід широко використовують в установках автоматизації теплових виробничих процесів. Пневмопривід доцільно використовувати також у випадках швидкого обертання деталей з невеликим силовим навантаженням; ротаційні пневмодвигуни можуть надати їм швидкість до 60...80 тис. об/хв.
Для таких установок потрібне чисте і сухе повітря (точка роси повинна бути нижча кінцевої температури повітря), так як при охолодженні до мінусових температур водяна пара легко переохолоджується і перетворюється в лід, що осідає на робочі поверхні приводу.
Пневмопривід відрізняється від гідроприводу більш низьким ККД, не перевищуючим 0,15...0,2; використовують їх у тих випадках, коли інші приводи не забезпечують надійної роботи всієї технологічної установки. Існують пневмоприводи поршневі і ротаційні. Пневмоприводи поршневого типу використовують найбільше. В транспортних засобах пневмрпривід застосовують у гальмівних системах, приводах муфт зчеплення великотонажних автомобілів
Тема: Класифікація автомобільного транспорту
Автомобільний рухомий склад за призначенням поділяють на:- Вантажний
- Пасажирський
- Спеціальний
Класифікація легкових автомобілів
Тип транспорту призначений для перевезення не більше 8 чоловік.
За класом автомобіля (розміром)
- A-клас (особливо малий)
- B-клас (малий)
- C-клас (малий середній, компактний, гольф-клас)
- D-клас (середній)
- E-клас (верхній середній, бізнес-клас)
- F-клас (верхній, представницький клас)
- За типом кузова
- Седани
- Універсали
- Хетчбеки
- Лімузини
- Пікапи
- Мінівени
- Мікровени
- Мультивени
- Купе
- Кабріолети
- Фаетон[en]
- Ландо
- За робочим обємом двигуна
- Особливо малий (до 1,2 л)
- Малий (1,2 - 1,8 л)
- Середній (1,8 - 3,5 л)
- Великий (понад 3,5 л)
- Верхній (не регламентується)
Класифікація вантажних автомобілів
До вантажного автомобільного рухомого складу належать:
- Вантажні автомобілі
- Автомобілі-тягачі
- Причепи
- Напівпричепи
За характером використання
- Загального призначення, кузови яких мають форму бортової платформи.
- Спеціалізовані, кузови яких пристосовані для перевезення певних вантажів.
- За конструктивною схемою
- Одиночні вантажні автомобілі
- Автопоїзди
- За типом кузова
- Самоскиди
- Бортові
- Криті (Кунги)
- Криті (Тентові)
- Автоцистерни
- Автоміксери
- Авторефрижератори
- Автовози
- Контейнеровози
- Тягачі
- За вантажопідйомністю
- Особливо малої (до 1 т)
- Малої (1-3,5 т)
- Середньої (3,5-15 т)
- Великої (понад 15 т)
- Особливо великої (понад 40т, - позадорожній автомобіль)
- За повною масою
- 1 клас (до 1,2 т)
- 2 клас (1,3-3 т)
- 3 клас (3-5 т)
- 4 клас (5-8 т)
- 5 клас (8-16 т)
- 6 клас (16-40 т)
- 7 клас (понад 40 т)
Класифікація пасажирських автомобілів
Транспорт, що призначається для перевезення 9 і більше чоловік, враховуючи водія.
За габаритною довжиною
- Особливо малий (до 5м)
- Малий (6м - 7,5м)
- Середній (8м - 9,5м)
- Великий (10,5м - 12,0м)
- Особливо великий (спарований) (16,5 м і більше)
- За призначенням[1]
- Міські
- Приміські
- Місцевого сполучення
- Міжміські
- Туристичні
- Екскурсійні
- Мікроавтобуси
- Тролейбуси
Класифікація спеціальних автомобілів
- Автокрани
- Спортивні авто
- Перегонові авто
- Боліди
- Карети швидкої допомоги
- Пожежні авто
- Катафалки
- Автокрамниці
- Прибиральні авто
- Снігоочисники
- Трактори
- Багі
- Грейдери
- Екскаватори
- Бульдозери
- Бронеавтомобілі
- Амфібії
- Вантажні тролейбуси
- Авто, що мають ліцензію ADR для перевезення легкозаймистих вантажів
- Коток
За ступенем пристосованості до роботи в різних дорожніх умовах
- Дорожні (звичної прохідності) - призначені для їзди по шляхах загальної мережі автодоріг
- Підвищеної прохідності - для їзди по дорогах з невідповідними нормами, а також по бездоріжжю
- Всюдиходи
За загальною кількістю коліс і тягових коліс
(умовно позначають формулою, де перша цифра - число коліс авто, а друга - число тягових коліс (кожна пара здвоєних тягових коліс рахується за одне колесо)
- 4×2 - двохосьовий автомобільний транспорт з однією ведучою віссю
- 4×4 - двохосьовий автомобільний транспорт з обидвома тяговими осями (повноприводний)
- 6×6 - трьохосьовий автомобільний транспорт з трьома тяговими осями (повноприводний)
- 6×4 - трьохосьовий автомобільний транспорт з двома тяговими осями
- 8×4
- 8×6
- 8×8
- 10×4
- 10×6
- 10×8
- 10×10
За кількістю осей
- 2-x осьові
- 3-x осьові
- 4-x осьові
- 5-x осьові
- 6-x осьові
- 7-x осьові
- 8-x осьові
- 10-x осьові
За типом двигуна
- з дизельним
- з бензиновим
- з роторним двигуном
- з електродвигуном (Електромобіль)
- з газовим
- Паровий газотурбінний двигун
- Гібридне авто
- Водневе авто
- Тема: Двигуни внутрішнього згорання
Поршневи́й двигу́н вну́трішнього згоря́ння або просто поршневи́й двигу́н - двигун внутрішнього згоряння, у якому теплова енергія газів, що розширюються і які утворились в результаті згоряння паливо-повітряної суміші у замкненому об'ємі, перетворюється у механічну роботу поступального руху поршня у циліндрі.
Поступальний рух поршня поршневого двигуна зазвичай перетворюється в обертання колінчастого вала кривошипно-шатунним механізмом.
Поршневий двигун внутрішнього згоряння сьогодні є найпоширенішим тепловим двигуном. Він використовується для приводу засобів наземного, повітряного і водного транспорту, військової, сільськогосподарської та будівельної техніки, електрогенераторів, компресорів, водяних насосів, помп, моторизованого інструменту (бензорізок, газонокосарок, бензопил) та інших машин, як мобільних, так і стаціонарних, і виробляється у світі щорічно в кількості декількох десятків мільйонів одиниць.
Потужність поршневих двигунів внутрішнього згоряння може бути від декількох ват (двигуни авіа-, мото- та судномоделей) до 75 000 кВт у дизельних суднових двигунів.
За видом пального
Як пальне у поршневих двигунах внутрішнього згоряння використовуються:
- рідини - бензин, дизельне паливо, спирти, біодизель;
- гази - зріджений нафтовий газ, природний газ, водень, газоподібні продукти крекінгу нафти, біогаз;
- тверде паливо (вугілля, торф, деревина), з якого виробляється монооксид вуглецю у газогенераторі, що входить до складу паливної системи двигуна.
За кількістю тактів робочого циклу
Повний цикл роботи двигуна складається з послідовності тактів - односпрямованих поступальних ходів поршня. Розрізняють двотактні та чотиритактні двигуни.
За кількістю та розташуванням циліндрів
Кількість циліндрів у різних поршневих двигунах може становити від 1-го до 24-х. За розташуванням циліндрів поршневі двигуни бувають
- рядні;
- V-подібні;
- опозитні;
- радіальні (зіркоподібні);
- X-подібні;
- W-подібні тощо
За особливостями утворення паливо-повітряної суміші і методами її запалювання
За способом утворення паливо-повітряної суміші поділяються на:
- Двигуни із зовнішнім сумішоутворенням.
За конструктивним виконанням засобів для утворення паливо-повітряної суміші такі двигуни бувають[1]:
- карбюраторними - паливо-повітряна суміш готується у карбюраторі та надходить впускними колекторами (патрубками) у циліндри двигуна;
- інжекторними з моновпорскуванням (центральне впорскування або одноточкове впорскування) (англ. Single Point injection, Spi; нім. Ein Spritz) - одна форсунка на всі циліндри, розташована, зазвичай, на місці карбюратора (на впускному колекторі). Втратила актуальність через зростання екологічних вимог: починаючи з Євро-3 екологічний стандарт вимагає індивідуального дозування палива для кожного з циліндрів. Система моно вприскування відрізнялась простотою і високою надійністю, перш за все через те, що форсунка розташовується у порівняно комфортному місці у потоці холодного повітря;
- інжекторними з розподіленим впорскуванням (багатоточкове впорскування) (англ. multi point injection, MPi) - кожний циліндр обслуговується окремою ізольованою форсункою у впускному колекторі поблизу впускного клапана.
За способом запалювання паливо-повітряної суміші такі двигуни поділяються на:
- двигуни із запалюванням від електроіскрового розряду, який виробляється системою запалювання (наприклад, бензиновий двигун чи двигун Гессельмана).
- Компресійні карбюраторні двигуни. В них пальне подається разом з повітрям. Зазвичай в основі пального лежить діетиловий етер, рицинова олія та гас). Займання відбувається від стиснення. Ступінь стиску регулюється контрпоршнем, від якого залежить момент спалахування суміші. Компресійні двигуни використовуються головним чином в авіа- та автомоделях. Компресійні карбюраторні двигуни не є дизельними двигунами.
- Двигуни із внутрішнім сумішоутворенням.
Двигуни із внутрішнім сумішоутворенням мають (як у теорії, так і на практиці) вищі ККД та крутний момент за рахунок вищого ступеня стиску. Такі двигуни, у свою чергу, поділяються на:
- Дизельні двигуни, що працюють на дизельному пальному. У цих двигунах стисненню в циліндрах піддається лише повітря, при перебуванні поршня поблизу верхньої мертвої точки при такті стиску в камеру згоряння форсункою впорскується дизельне пальне, яке спалахує при контакті з повітрям, що нагрілося від стиснення до декількох сотень градусів Цельсія.
- Бензинові двигуни з безпосереднім (прямим) впорскуванням, у яких пальне впорскується безпосередньо в циліндр, займання паливо-повітряної суміші відбувається від свічки запалювання.
- Існують також двигуни із змішаним сумішоутворенням (газодизельні двигуни), що працюють на суміші природного газу з повітрям. Так як температура запалювання від стиску газо-повітряної суміші становить близько 700 °C (дизельне пальне займається при 320-380 °C), запалювання проводиться впорскуванням через форсунки невеликої кількості дизельного палива.
За способом охолодження
Ефективний ККД поршневого ДВЗ не перевищує 60%. Решта теплової енергії розподіляється, в основному, між теплом відпрацьованих газів і нагріванням конструктивних частин двигуна. Оскільки остання частка є суттєвою, поршневі двигуни мають потребу у системі охолодження. Розрізняють такі системи охолодження:
- повітряні, що віддають надлишкове тепло у навколишнє повітря через ребристу зовнішню поверхню циліндрів; використовуються у двигунах порівняно невеликої потужності (десятки к.с.), або у потужніших авіаційних двигунах, що працюють у швидкому повітряному потоці;
- рідинні, у яких охолоджувальна рідина (вода, олива або антифриз) пропускається через сорочку охолодження (канали у стінках блоку циліндрів), і далі надходить у радіатор охолодження, у якому теплоносій охолоджується зустрічним потоком повітря та/або потоком, що створюється вентилятором.
Механізми та системи поршневих двигунів внутрішнього згоряння
До основних механізмів і систем поршневого двигуна належать:
- кривошипно-шатунний механізм;
- газорозподільний механізм;
- система живлення;
- система запалювання;
- система охолодження;
- система мащення;
- впускна система;
- випускна система;
- система рециркуляції вихлопних газів.
Основні параметри поршневого двигуна
З роботою поршневого двигуна внутрішньго сгоряння пов'язані такі параметри.
- Верхня мертва точка (ВМТ) - положення поршня при максимальному його віддаленні від осі колінчастого вала в момент коли поршень змінює напрямок руху.
- Нижня мертва точка (НМТ) - положення поршня при мінімальному його віддаленні від осі колінчастого вала в момент коли поршень змінює напрямок руху.
- Радіус кривошипа - відстань від осі корінної шийки колінчастого вала до осі його шатунної шийки.
- Хід поршня - відстань між ВМТ та НМТ, що дорівнює подвоєному радіусу кривошипа колінчастого вала. Кожному ходу поршня відповідає повертання колінчастого вала на кут 180° (пів-оберта).
- Такт - частина робочого циклу двигуна, що відбувається при русі поршня з одного крайнього положення в інше.
- Об'єм камери згоряння - об'єм простору над поршнем, коли він перебуває у ВМТ.
- Робочий об'єм циліндра - це об'єм простору, який звільняється при переміщені поршня з ВМТ до НМТ.
- Повний об'єм циліндра - об'єм простору над поршнем при перебуванні його В НМТ. Повний об'єм циліндра дорівнює сумі робочого об'єму циліндра і об'єму камери згоряння.
- Робочий об'єм двигуна для багатоциліндрових двигунів - це добуток робочого об'єму на кількість циліндрів.
- Ступінь стиску - відношення повного об'єму циліндра до об'єму камери згоряння.
двигун з іскровим запалюванням 7,5 - 13
двигун з наддуванням 14 - 18
двигун із самозапалюванням 18 - 24- Тема: Принцип роботи двигуна
- Робота чотирьохтактного одноциліндрового двигуна
1 Такт впуск
При обертанні колінчатого вала поршень рухається від ВМТ до НМТ і над ним створюється розрідження, тобто тиск у циліндрі стає нижче атмосферного. У цей час за допомогою газорозподільного механізму відкривається впускний клапан (випускний закритий) і пальна суміш із карбюратора надходить у циліндр, наповнюючи його
2 Такт стиску
поршень рухається до ВМТ, впускний клапан закриється (випускний клапан продовжує залишатися в закритому положенні). Об'єм у циліндрі зменшується, тиск і температура підвищуються..
3 Такт розширення
Наприкінці такту стиску в циліндр через свічу запалювання подається електрична іскра і запалює пальну суміш, відбувається згоряння з наростанням тиску газів у циліндрі. Під тиском газів, що розширюються, поршень рухається від ВМТ до НМТ і передає зусилля через поршневий палець на шатун і колінчатий вал.
4 Такт випуск
Поршень рухається з НМТ до ВМТ, відкривається випускній клапан і гази, що відробили, видаляються із циліндра
При подальшому обертанні колінчатого вала такти повторюються. Отже, робочий цикл у чотиритактному бензиновому двигуні відбувається за чотири ходи поршня або два обороти колінчатого вала, що відповідає 720° його повороту.
Особливістю роботи дизельного двигуна є те , що при такті впуску в циліндр двигуна поступає повітря а в кінці такту стиску форсунка подає в циліндр паливо, яке при контакті з гарячим повітрям самозагоряється.
Порядком роботи двигуна
Чергування однойменних тактів по циліндрах двигуна в певній послідовності, установленої заводом- виготовлювачем, називається порядком роботи двигуна.
Зміна тактів у 8 циліндровому двигуні відбувається через 90° повороту колінчатого вала, але такт триває протягом 180°.
Таким чином, у двох циліндрах одночасно протягом 90° повороту колінчатого вала здійснюється той самий такт - відбувається перекриття (накладення) тактів, що сприяє більше рівномірному обертанню колінчатого вала.
Порядок роботи двигуна 1-5-4-2-6-3-7-8